Picking windows

I’ve got some pricing on double hung windows. Is fiberglass really worth 2x the cost of vinyl? And can I do better than 8-12 weeks lead time on an economical quality double hung window?
Here’s the pricing I’m looking at for 30×52 double hung windows. (Just a sampling of my quotes) A lot of these places seems to quote their default double glazing, instead of their lower U coatings., despite my asking about them.
(1) Local no-name vinyl, double glazed, 3rd surface 7257 coating, DP40
U 0.27, SHGC .44, VT .54 (no grid)
U 0.27, SHGC .40, VT .48 (no grid)
(I have reservations about their extrusion supplier)
$260 each, 5 weeks
(2) Canadian fiberglass, double glazed, Cardinal 272 or 366, DP55
U 0.29, SHGC .24, VT .41 (grid)
U 0.28, SHGC .16, VT .37 (grid)
(They didn’t quote the glazings I asked about, so the performance is mediocre)
$680 each, 8-12weeks
(3) Well known regional vinyl, double glazed
I’ve used their windows before, they’re pretty nice
U 0.27, SHGC .31, VT .56 (no grid)
$290-300 each, 8-20 weeks, 12+ weeks probably
(4) Big American 1 All Fiberglass double glazed
$650 Each
(5) Big American 2 Composite double glazed
U 0.3, SHGC .27 (grid)
$390 Each
(6) Big American Wood/Fiberglass double glazed
U 0.3, SHGC .28 (grid)
$670 Each, 5 weeks
(7) Big American Wood/Composite double glazed
U 029., SHGC .27 (grid)
$660 Each
(8) European PVC “budget” tilt-turn triple glazed
$800 Each, 8-12 weeks
GBA Detail Library
A collection of one thousand construction details organized by climate and house part
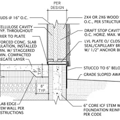
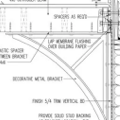
Replies
You get what you pay for. Better quality windows with better performance will cost more money. Are you planning on selling the house in 10 years? If not, then get the better performing windows.
Lead times are due to supply chain problems. This is a problem with many household construction materials. 8-12 weeks is about the norm right now.
Personally, I would get something in the < 0.20 U-Value range.
I'm definitely considering triple pane windows and lower U values, if the payoff makes sense. Is there a quick calculator that estimates the yearly fuel cost of a window based on utility rates, window size and U-value? (Including SHGC might be a stretch.)
Hi, John. I thought I’d chime in as I find myself in a similar spot. My comparisons were between triple-glazed horizontal sliding windows in vinyl, fiberglass, and Sierra Pacific’s H3 line which is a hybrid of wood, aluminum, and vinyl.
I spoke to our window supplier, and he had a couple of thoughts that may be applicable. The first is that for smaller windows, the difference isn’t as noticeable according to him. That is, the difference between a 36x46 horizontal slider in vinyl versus fiberglass may not be worth the cost difference. This changes when you move to a casement or awning style where the window is pivoting out and putting all that stress on the frame. He said he still would probably skip over fiberglass in that instance (mostly based on price, not performance) and switch to the H3, but in any case he said that the lack of rigidity in vinyl would be noticeable in that use case.
He also said that as the window gets larger that same issue of rigidity—or lack thereof—comes into play with vinyl. The expansion and contraction rates of vinyl also come into play at that size according to him. We have some 48x80 windows in our house, and he said those would be a good place to step up to a different frame material. Luckily in our case the room layout allows us to switch styles without them being noticed as different.
Finally—and I’m not sure how valid this is, but I’ll pass it along anyway—he said that the safety and disposal procedures around fiberglass make it more expensive. He said “the EPA kills manufacturers on fiberglass”(in what way that’s different than pvc I’m not sure) and that adds to the cost difference on our end.
For what it’s worth, we ended up being quoted triple-pane vinyl sliders on the back that come in at about $27 per square foot, and triple pane H3 sliders (which we’ll likely change to casement) at $73 per square foot.
1) Local no-name vinyl for $260 and 5 weeks...."Is fiberglass really worth 2x the cost of vinyl?"
Quality fiberglass (or wood or vinyl) can easily be worth twice or three times the cost of junk vinyl. Unfortunately junk vinyl is the market leader. I would pass this bye without a second thought.
2) What glazings did you request that would improve the performance from "mediocre"?
3) - 8) So who are they? (I am guessing 4 is Marvin or maybe Pella, 5 is Andersen, 6 is Marvin).
You have included minimal information (other than U, SHGC, so on) and many junk windows have decent to good U and SHGC numbers. What are CR , AI, DP ratings? And who are they?
There are some very good vinyl windows, some very middle of the road vinyl windows, and some very bad vinyl windows available, while fiberglass tends to average better quality overall and really hasn't seemed to have caught on with the bottom feeder companies (that I have seen so far).
While fiberglass windows do tend to be more in the not bad to very good range in quality, this is morel about the quality of the company manufacturing the product and less about the material used to build the window.
Fiberglass windows do tend to be more expensive, often equal to or even more than wood of comparable "quality level", and don't be surprised when a top quality vinyl window isn't cheap either. Top end vinyl windows can be expensive, sometimes as much as comparable quality wood or fiberglass products.
Bottom feeder vinyl windows shouldn't be compared with better quality vinyl products, because it isn't a true apples to apples comparison. But when only looking at out-of-the-box numbers, even some junk quality vinyl windows may offer energy performance numbers as good or better than either wood or fiberglass assuming glass options being the same.
2) What glazings did you request that would improve the performance from "mediocre"?
There are a couple places that make surface 2 or 3 coated double pane double hung windows that are U0.26. Some windows with surface 4 coatings get down to U0.24. There are probably others that do better. It's not triple pane performance, but I'm looking at a lot of windows, so up front costs matter.
I definitely prefer the CR ratings of the surface 3 options and shy away from surface 4. The AI ratings of the windows I like most have been .1 or less. DP varies from 30-65.
The warmest part of almost any window is center of glass. Center of glass being defined as the area inside of 2 1/2" perimeter from edge of the glass to sash interface..
Glass-only, Cardinal's 366 has a CoG of U.24 and a U.19 when using I89 surface 4 coating. Overall window performance is calculated using CoG, edge of glass, sash and frame and window U factor is almost always poorer than CoG measurement, so while you considered different glazing for improved performance, it's really about the sash/frame and whatever bells and whistles associated with those components that makes the major difference rather than glazing.
If you are looking for higher solar heat gain then look for surface 3 coating, but probably better than 90% of all LowE coatings are applied to surface 2. Surface 2 vs surface 3 does not affect U value, but it does affect SHGC, no matter the coating.
I like to see am AI of .05 or better, depending on sash/frame material, but that point is arguable. And for consideration a DP 30 is equivalent to wind velocity of about 110mph and 65 is about 165mph, but higher DP also relates to better water infiltration performance. That's probably the biggest factor assuming you don't live in a hurricane zone.
Just curious, but are the windows in the building original?
Not a single original window in the building. We're guessing they were replaced in the 1950s. They're single pane wood on metal rails with exterior lead paint.
The best bang for your buck is to design your windows so that the large ones are fixed and only the smaller ones operable.
You can than go for budget vinyl triple pane fixed units for these and some better quality windows for your operable ones. Since they are smaller, the operable windows don't need to be triple pane.
Generally there is no ROI on better windows in most climates but I can guarantee you'll regret buying low quality windows.
Unfortunately, I've got 25 essentially identically large windows going into a 200+ year old brick house that doesn't (at this point) have air conditioning. I don't have much flexibility on leaving windows inoperable.
Just a recommendation on one manufacturer to avoid: Inline Fiberglass of Ontario, Canada. Subpar hardware and sloppy frames, and terrible customer service!
OP it would be helpful for others if you included the manufacturer and model line of the windows you are referencing.
Okay, I've got a window that is looking like it might be my current winner. It's a Paradigm 8 series vinyl double hung.
Test results say:
a. Size Tested: 44 x 60 (1118 x 1524 mm).
1) Design Pressure Rating (DP): R40.
2) Structural Test Pressure: 90.0 psf (4.31 kPa); tested at 150 percent of DP.
3) Water Infiltration: 6.00 psf (0.29 kPa); 15 percent of DP rating.
4) Air Infiltration: 0.05 cfm per sq ft (0.25 Liters per sec per sq m).
NFRC lists a few options that look okay (for double pane no grid)
U 0.22, SHGC 0.27, VT 0.51, CR 49 (LoE 270 / Argon / LoE i89, foam)
U 0.24, SHGC 0.48, VT 0.58, CR 48 (LoE 180 / Argon / LoE i89, foam)
U 0.24, SHGC 0.27, VT 0.51, CR 51 (LoE 270 / Argon / LoE i89, no foam)
U 0.25, SHGC 0.48, VT 0.58, CR 46 (LoE 180 / Argon / LoE i89, no foam)
U 0.26, SHGC 0.35, VT 0.53, CR 52 (Clear / Argon / LoE 270, foam)
U 0.27, SHGC 0.35, VT 0.52, CR 60 (Clear / Argon / LoE 270, no foam)
I'm not sure on the price adder for foam, but LoE 270 / Argon / LoE i89 with no foam in white vinyl with half screens is about $300. Going triple pane starts about $360.
The big question I have now: In the climate of Northborough, MA, what CR rating is adequate?
Which climate zone are you in? Are the walls insulated?
For an older double brick home where insulation was not an options, I went with triple pane tilt and turns. With larger windows, this actually bumps up the overall wall R value by a fair bit and made a big difference on comfort (and energy bills) over the original single panes.
Important part when replacing windows in brick homes is to go with brick to brick replacement. This way the rough opening can be properly sealed up, the original frames with pockets for counter weights tend to leak a fair bit and are very hard to seal up.
Climate zone 5. 6969 degree days. I've seen -2F to 90F and 2F to 87F as the 99% design temperatures.
What's the process for a brick-to-brick replacement? I actually have no idea what we'll find if we open up to the rough opening. How do you manage air and water with almost certainly no existing air and water barrier?
The old window frames, jambs and trim is removed. If you have a brick sill, good time to tuckpoint them especially if any bricks are loose. Stone sills generally don't need any work, wood sills should be capped or replaced with stone.
Lumber is tapconed into the brick pocket area to hold the new window. Since brick houses have thicker walls make sure to order deeper jamb extensions.
The air barrier is usually canned foam around the window and the water barrier is a bead of caulk between the brick mold and the brick. I've never done anything more than that. Sometimes when there is a large gap between the jamb and the interior plaster, I've spray foamed between them with one of the smaller two part spray foam kits.
Reusing the old trim is possible but more work than staining new trim to match. Usually brick to brick replacements will also be larger than the original windows (great as you get more light) but the original trim might be too short to reuse.
An advantage to vinyl frames is that the seams are typically welded, so they don't seperate. Fiberglass frames have a sealant at the seams. Fiberglass frames are stiffer though, so less likely to sag and bind which can be an advantage on heavier operable windows. I'm not aware of anyone making budget fiberglass windows, but with vinyl windows there is a big range between budget and high-end windows in terms of manufacturing quality.
Regarding triple pane windows, if you're going to spend the money for triple pane, get full depth (1-3/8") IGUs. The 7/8" triple pane windows just get you up to the level of performance triple pane IGUs are capable of -- the air gaps are too small. With 7/8" triple pane, it might be worth it for a Krypton fill, but I'd just go for full depth and argon.
If you only want 7/8" thick IGUs, double pane with i89 on the inside is probably a better cost/benefit than a 7/8" triple pane window. I personally don't like the 366 coating, either -- in my opionion you sacrifice too much visual transmission for the modest gain in thermal performance. 366 windows are dark, and show a noticeable tint to whatever you're looking at through them.
If you go with triple pane windows, my favorite combination is LoE-180, 1-3/8" thick IGU, and an argon fill. This is a good balance of visual and thermal performance specs. If you go with double pane windows, then the more aggressive LoE coatings make more impact, but I still don't like the darkening. If you're in a heating-dominated climate, I'd focus on the U values and VT. If you're in a cooling dominated climate that bakes in the sun, then SGC (solar gain) is more of an issue, so the more aggressive coatings like 366 might be worth the tradeoff in terms of reduced VT. Cardinal has a good summary of their coatings and relative performance metrics here: https://www.cardinalcorp.com/technology/reference/loe-performance-stats/
BTW, you can split a large window into a large fixed window with a small operable awning window on the bottom. I have a number of windows like this in my own home, and they are a nice tradeoff.
Bill