Phased insulation plan for a 1960s home

Long time reader, first time question.
I’ve got a 1960s raised ranch in Chicago (zone 5) that we have been renovating. As we renovated rooms, we would open the walls and replace the inch or two of original fiberglass insulation with XPS and/or closed cell spray foam. We did this because it was the best insulation we could cram in the stud bay and our home is cold and drafty. Eventually I’d like us to be net zero and my wife would like to be comfortable, so we thought this was a good first step.
We started doing this before I read about the REMOTE insulating method and I love the idea. However, we’ve gotten a fair amount done inside with the foam. I’m hoping I haven’t screwed things up by putting foam in the stud bays. When we are ready to replace the windows and siding, we may as well install exterior insulation.
If I understand things correctly this is my plan… Since we’ve put foam in the study bays this will act as our air and vapor barrier. Outside I thought we could put ROXUL comfortboard, rather than the usual XPS or polyiso, so that the sheathing may breathe. See attached
Is this a satisfactory design? Thanks in advance!
GBA Detail Library
A collection of one thousand construction details organized by climate and house part
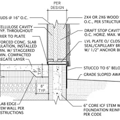
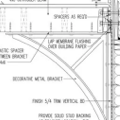
Replies
Putting high R/inch foam insulation between low R/inch studs is a waste of good foam. Using XPS or closed cell spray foam is even worse, since both are manufactured with high global warming potential blowing agents. Filling a 2x4 bay with R6.5/inch closed cell foam only adds about R1.5 better overall thermal performance than you would get with air-sealing + R15 batts, due to the thermal bridging of the ~25% framing faction.
As the HFC134a (~1400x CO2) leaks out of XPS over time, it's performance drops by about 15-20% to that of EPS of similar density. Closed cell polyurethane doesn't lose as much as the HFC245fa leaks out, but it's still not the right thing to do for cavity fill
If you do any more of this on a DIY basis, seal the stud bays to the sheathing, and install R15 rock wool instead, and install a "smart" vapor retarder such as MemBrain or Intello Plus on the interior. Save the high R/inch foam budget for the exterior, where it actually does some good.
Most 1960s houses are sheathed in plywood, but even fiber board can be dead-easy to air seal the framing bays to the sheathing with caulk. Horizontal seams in the sheathing not supported by framing can be sealed with tapes, (or if dirty, tapes + mastic.)
For the sections with 3.5" of foam in the cavities you'll have to use the more expensive rigid rock wool on the exterior, as per your proposed stackup or the fiberboard can potentially become saturated and sag. For any new sections you can safely install 4" of EPS or polyiso (both of which are blown with pentane, at ~7X CO2) on the exterior. If doing it at the same time as the cavity fill, you can even skip the the MemBrain. If the cavites were mostly empty, and the R5 fiberglass doesn't have a foil facer you don't even have to gut the walls- you can dense pack over the old stuff with 1.8lb fiberglass or 3-3.5lb cellulose, drilling from either the exterior or the interior.
There is no drain-plane specified in either stackup. I assume in the old wall asphalted fiberboard was the weather resistant barrier/drain-plane. If you are replacing the windows and window flashing you need to make some decisions as to how to re-flash the windows to match wherever the new drain-plane is going to be. If the glass is going to be roughly coplaner with the fiberboard, it's good to insert a crinkle-type housewrap between the sheathing and any exterior foam, but with rigid rock wool a flat housewrap is fine. If the glass is going to be roughly coplanar with the siding, the housewrap goes between the rigid insulation and the furring, and properly lapped with the window flashing.
If you're going to fill in between the 2x strapping, leave at least a 1/2" gap between the insulation and siding which allows both the wall assembly and siding to dry quickly. The gap is an excellent capillary break, which limits the amount of wetting of the insulation or housewrap from wind-driven rain that blows in. Most foam-overs use 1x4 furring though screwed to the studs with pancake head timber screwed sized for a minimum of 1.5" stud penetration which works just fine. That works with rigid rock wool too, but you may have to tweak the screws in/out a bit to achieve the same amount of flatness with rock wool, due to it's being more compressible than foam:
https://www.greenbuildingadvisor.com/blogs/dept/musings/installing-mineral-wool-insulation-over-exterior-wall-sheathing
Dan,
The layer that Dana Dorsett calls a "drain-plane" is usually called a "water-resistive barrier" (WRB). For more information on WRBs, see All About Water-Resistive Barriers.
I agree with Dana that if you have any more walls to insulate from the interior, you should probably switch to a vapor-permeable insulation like fiberglass, cellulose, or mineral wool. The most important step when you do this work is paying attention to air sealing.
What if you were to install rigid foam on the exterior side of the fiberboard sheathing instead of mineral wool? Dana is convinced that this approach would be risky; I'm not as sure as he is. Exterior mineral wool (which you propose to use) will certainly work fine, but I don't think that much moisture will reach the sheathing layer even if you use exterior rigid foam, which is easier to work with and usually cheaper than mineral wool.
Sandwiching sheathing between vapor-impermeable layers isn't ideal, but if there is good flashing on the exterior, and attention to airtightness on the interior, these less-than-ideal walls usually work.
The risk in a foam-sandwich approach is almost entirely in just how perfectly the flashing is installed. In construction there's good, better, and best, but perfect hasn't been done yet. If you're meticulous the risk is low, but if built per the drawing without weather resistant barrier or rainscreen it's a problem.
If you use 4" of unfaced EPS rather than XPS or foil faced good on the exterior there would still be at least SOME drying capacity toward the exterior, assuming you take the advice and build it with a "rainscreen" gap between the foam & siding.
Dana and Martin, thank you for your insights and quick replies. I will switch to ROXUL with a vapor barrier for future interior work. Should we stay here long enough to do the siding then we'll be ready for foam board outside. Thanks for the recommendation on vapor barriers and rainscreen placement. Those will of course be included.
I know putting foam on both sides of the sheathing is not ideal and I also don't like the idea of inconsistent insulation methods around the structure. This was my cause for hesitation to switch to batts in the bays and foam out where it is best. But if the sections of foamed bays will be okay then I feel better about switching since I can at least be consistent outside.
Qualitatively thinking about future exterior foam, if the foam in the existing bays is tight it would keep the warm/moist interior air away from the sheathing. If this is the case, even if the sheathing is a bit colder than it would be with batts, where would the moisture come from, especially once the exterior insulation is installed?
Dan,
Q. "Even if the sheathing is a bit colder than it would be with batts, where would the moisture come from, especially once the exterior insulation is installed?"
A. As Dana pointed out in an earlier comment, the most likely source of moisture would be wind-driven rain, which is why a rainscreen gap and excellent flashing details are important.
A less likely but possible source of moisture would be water vapor traveling with exfiltrating air along defects in your air barrier (defects in your cut-and-cobble rigid foam installation).
Workmanship is rarely perfect. However, if you include the rainscreen gap and pay attention to your flashing, I think you'll be able to sleep at night.
Defects in my workmanship, that's unpossible!... ;)
Gotcha, thanks for clarifying Martin.
Don't use a true vapor barrier (such as 6 mil polyethylene) on the interior, since that limits the drying capacity of the assembly. Using 2 mil nylon (eg Certainteed MemBrian) is roughly 2x the cost of polyethylene, but it's a "smart" vapor retarder, that will allow moisture to leave the cavity toward the interior should moisture ever get in. Think of the upcharge as cheap insurance.
Some Lowes & H.D. stores are carrying short rolls of it in my neighborhood, but you can get 8' x 100' rolls for about a Franklin at Menards. You may have to order it online, since not all Menards stores stock it.