Permeability of closed cell spray foam

I have a 110 year old foursquare in Michigan (zone 5). The exterior sheathing is wide board pine, typical of this vintage construction. I will be using rockwool in the wall cavities and removing two of the three layers of siding (vinyl, asbestos, a layer of tarpaper) and applying fiberglass or paper faced polyiso to the exterior (over the original lap siding and sheathing) before constructing a rainscreen and re-siding. I think I would like to spray foam the wall cavities with roughly 1/2″ of closed cell foam before installing the rockwool. I wouldn’t be doing this for the insulation value, but as more of an adhesive. In regards to drying to the interior, would I be creating a moisture trap with such a thin application of spray foam?
GBA Detail Library
A collection of one thousand construction details organized by climate and house part
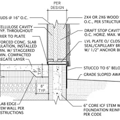
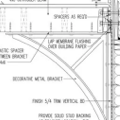
Replies
Just curious - what do you mean by "adhesive"?
Where do you think you would be creating a "moisture trap"?
How much polyiso on the exterior?
Some of the board sheathing is pretty rough. Also, there are gaps. This is mostly my OCD. My moisture trap concern would be the sheathing itself.
1/2" of closed cell foam will probably be somewhere around 2 perms, but the thickness will likely vary up to 1-1.5" with a permeance closer to 0.5 to 1 perm. In any case, if your sheathing were to get damp, that should allow enough drying to the interior for it to be a safe assembly.
I would never rely on spray foam to glue things together. A 1/2" layer isn't enough to really give you any structural benefit anyway, you'd probably need more around 2" to get any "structure" from the foam itself. Another thing that will be an issue is that it will be nearly impossible to get an even layer of closed cell spray foam that is that thin. You're going to end up with places that are way too thick, and others that you can see the sheathing through trying to do that. It's difficult to get an even layer, and it's VERY difficult to do it when the layer is especially thin.
I don't see any issue with a vapor barrier in the middle of the wall like this, since the wall can still dry towards the interior on the interior side. While bidirectional drying is a plus, it's not a requirement. I'm assuming you are using rigid foam of at least the minimum thickness for this climate zone (hellow fellow zone fiver in MI, BTW :-D), which will keep the wall assembly safe. It is my preference to use an inexpensive smart vapor retarder over the interior studs anyway though for added insurance (I use CertainTeed's MemBrain for this).
Is there any particular reason you're using the fiber faced polyiso here? I'm assuming its due to drying concerns, but my own preference would be to use foil faced polyiso here, with the exterior facing taped with foil tape (Nashua 324A). This gives you that outer foil facer as a WRB at the back of your rain screen, and allows inward drying for the sheathing. If you also use the smart vapor retarder on the interior the way I mentioned, and AT LEAST the minimum amount of rigid foam R value for the climate zone, you'll end up with a very robust wall assembly this way.
BTW, using polyiso 1" or thicker on the exterior and vertical furring for the rain screen, I think you'll find the polyiso will help keep the exterior wall assembly tight and flat. I'm not sure if that's what your concern is that has you considering using spray foam to "glue" that sheathing to the studs. Using polyiso this way can help to "squeeze the sandwich", and the thicker the polyiso, the flatter you can get things (up to around 2"-2.5" thick polyiso, beyond that doesn't really gain you anything in terms of rigidity of the panels).
Bill
I'm not really looking for a structural benefit like racking resistance. It's more due to the appearance of the sheathing. I'd like to fill the gaps, etc. I have close to 1/2" to spare due to the stud size and I will have extra spray foam after spraying the sill and above the top plate. The foam preference is due to cost. My Amish foam dealer has a lot of commercial polyiso at really good prices. I'll likely use the 2.6" he has regularly. My thought was to seal the seams with some liquid flashing. I've used both Prosoco and some 3M and I've liked both. The thought was to run a bead along the edge and push the two together, use a bondo spreader for any squeeze out. I probably won't stagger seams/tape, although if the price is right, I'll consider foil faced.
So you're going to do the spray foam work yourself by using one of the 2 component kits?
Correct. We'll see how much of a mess I make.
If you look at the use of those kits on Youtube, they are way harder to control the depth & smoothness of (per Bill's comment above) vs. a professional spray foam contractor.
I personally would shoot for an average 1-2" & then just buy a FG batt & compress it.
~ worked for a spray foam contractor
If I don't feel like I can get the coverage I'm looking for after doing the sill, I'll just skip the flash coat inside the walls. Good information though.
There's nothing wrong with the fiber faced stuff if you can get it cheaply. Staggered seams does help if you can manage it, but it's not the end of the world if you can't. What I've done in the past is run a bead of canned foam in the gap and then immediately pushed the panels tightly together. The canned foam squishes in the gap and seals the panels together. I often find that works better than caulk in that application.
The appearance of the sheathing probably isn't all that important. Air seal the perimeter, then airseal the perimeter of the polyiso and seal the gaps between panels. That will get you a pretty decent air barrier regardless of the condition of the sheathing. If the sheathing isn't structurally sound, spray foam won't really help you there anyway, you just need to replace the sheathing panels.
The two part spray foam kits are not fun to use. About the best you can hope for is about a 1" layer of relative ease of application, and it still won't end up all that even. It will take you some time to learn how to get a good layer too, because the foam doesn't expand immediatly on application, it keeps "growing" after you spray it onto a surface. It's tricky, but doable, just don't expect great results your first time. I do recommend warming the canisters up SLIGHTLY well before use. Commercially, I sit them on top of a transformer overnight, so they end up warm to the touch (but not hot) the following day. On residential projects, I've put them in a small bathroom with a space heater for several hours. The goal is to get the entire contents of the canisters up to around maybe 80ish degrees or so. The cannisters will cool off as you use them, and I find starting out with them warm helps to get both a better result and more of the material out of the cannisters.
BTW, wear a FULL tyvek suit while spraying. That means suit, hoodie, footies. Wear gloves, tape them to the sleeves of the tyvek suit with duct tape. Wear a full face mask respirator. You NEED good eye protection, and you NEED the respirator. Doing this protects you, you don't want to get the spray foam on your skin (it's hard to get off), and you really don't want to get it in your hair. You don't want to breath the stuff, either. You can get all the safety gear pretty cheaply.
One last thing: have some pieces of stiff wire on hand to poke into the cured spray foam to check depth. It can be surprisingly difficult to gauge the thickness of the spray foam layer by eye.
Bill
I saw someone recommended using a couple of heating pads, stuffed in the boxes that the canisters ship in. Seems reasonable. I'll absolutely be wearing a bunny suit.