Peace of mind vapor barrier

Plans for the uninsulated 50-year old slab depict a vapor barrier beneath the slab above crushed gravel.
Is there any harm in laying down another vapor barrier atop the slab before putting in rigid foam and finished flooring? I assume it would do little, but perhaps more than nothing. But could it cause harm? Since 6 mil PE is cheap, I don’t mind putting it down even if the benefit is small.
GBA Detail Library
A collection of one thousand construction details organized by climate and house part
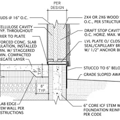
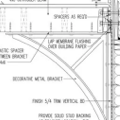
Replies
It sounds like you are basically performing what's outlined here:
https://www.greenbuildingadvisor.com/article/installing-rigid-foam-concrete-slab
I'm doing the same, although I don't have existing poly (that I know of). Do you KNOW it's there?
The short answer is, no, there's no danger, and if you're at all unsure that there is existing poly, it would be good insurance.
But to complicate matters, some folks—such as Joe Lstiburek—claim a sheet good is not the proper product for this:
https://www.buildingscience.com/documents/insights/bsi082-walking-the-plank#foot01
His argument doesn't feel very well hashed out to me, especially if one is careful placing the VB, but I can see the argument if people are going to be sloppy with the sheet VB product; any imperfection can introduce an air exchange component rather than just a vapor diffusion component. (Theoretically, though I don't see much of a driver for air communication and Joe doesn't really go into it. Joe can have strong opinions that sometimes don't feel well supported with a reasoned argument).
I would actually be interested to hear others' thoughts on this, since I'm grappling with the choice myself. One of those areas where there is conflicting advice and little consensus. (And if NOT a sheet product, which product specifically? Redgard?)
I don't know the odor threshold for mold, but say it's 1 ppm. Not much, this much might get past almost any air sealing. There is also the question "will mold always grow between concrete and a not-fully adhered impermeable interior barrier (poly or foil faced foam)?" I've seen both ways. So I agree, better quantification of this risk is needed.
I find it interesting that products like "DMX 1-Step" claim the opposite - that an air gap prevents mold.
I think those are the right questions. I'd like to see those with the prowess answer them or, better yet, provide case-studies. I don't see where Joe made that attempt.
He didn't seem to imply that mold will grow between the poly and the concrete and spit mold spores into the living space, as much as he implied that water vapor would be transported to the floor assembly via air movement and subsequently the floor assembly could grow mold. At least I think that was his implication.
Is air moving from beneath the poly into the floor assembly? What's the driver? Is there much pressure differential between the thin air film below the poly and assembly above? If there is, perhaps it's an argument for taping the foam, and/or even the subfloor, in order to neutralize those differentials. If the poly was loose and the floor system warped, I could see how air could be 'pumped' from beneath the poly. Ultimately, I have doubts that significant air exchange occurs here in most cases. The floor holds the poly down fairly tight to the concrete.
The other question is whether there is enough oxygen below a layer of sealed poly to sustain a mold colony? Food would also be limited, but not non-existent.
In any case, since air tightness and not just vapor tightness apparently matters, I might lean towards a more robust sheet product and tape it. (Something like a Tu-tuff or Stego).
[this all being most relevant when there is NOT poly existing below the slab]
I'm also curious how it would compare $-wise and PITA-wise to adhere standard poly to the slab vs what Joe recommends (expensive epoxy coatings). It would seemingly accomplish a similar thing.
I bet it'd be cheaper in materials, but perhaps high on the PITA scale. (pain in the...)
> He didn't seem to imply that mold will grow between the poly and the concrete
I think Lstiburek was pretty clear in the entire "Why is using a plastic sheet a dumb idea?" paragraph just below Fig 7 in BSI 082 - if not fully adhered, it will leak, mold will grow in the pockets and the odor is going to leak out.
Jon. I must be missing it. Can you provide the quote?
Here's the quote that speaks to my point:
"If these air pockets communicate with the interior you will grow mold and algae. And the floor will smell."
Tyler,
Glad to see I’m not alone in grappling with this. That said, it would be better to simply follow the experiences of others instead of relearning a possibly known lesson.
What finish flooring are you planning to lay atop your VB-rigid foam install? I’m hoping to go tile, with plywood ripped in 12 inch wide segments for PEX tubing to go between. Some seem to think I’m crazy. I fear they’re right. But it also sure as heck seems like I’m just creating a Roth panel setup with more labor but lower cost.
I'm planning 2 staggered layers of advantec tongue and groove, floating, but screwed to each other. Might leave a finish off for a while to serve as shop floor.
GBA itself has a handful of articles that mention using poly. Flooring industry apparently too. Others say it's either a no-no or at least not the ideal path. So 'the experience of others' in this case is diverse.
On the other hand, I've not really heard any argument AGAINST an adhered VB, so if one wants to play it safest, perhaps that's the ticket. Its likely to be more $$, and still can be screwed up if one uses the wrong product or doesn't apply it properly.
I think it’s safe to assume that a vapor barrier laid 50 years ago was not installed with the utmost attention to detail. I’d put the poly sheet on top for sure
There is a big difference between an adhered vapor barrier and a sheet vapor barrier. An adhered one will prevent water from permeating through the concrete and block it at the concrete level. Concrete doesn't mind/care about being wet so this works great.
A sheet good above the concrete can only block vapor that diffuses through the air gap between the two as such you can and will get some condensation underneath the poly. This can create issues with mold.
So the best solution is sub slab poly (even a shabbily installed one works). If this is not an option, the next best thing is a roll on vapor barrier (Redguard, Hydro Ban, AquaDefense or certain epoxy floor coatings).