Past experiences in upgrading wall insulation of a (solid) brick building?

I’ve learned that even with all the energy-efficient, air sealing, etc..stuff that I do in my house, that until my wall insulation is upgraded, I will be uncomfortable because of convective loops.
The walls from exterior to interior consists of:
a) two-wythe brick
b) 3/4″ – 1″ kraft faced fiberglass bat (not tightly installed)
d) drywall attached to brick with furring strips (no wall)
…which of course is the worst for a brick building.
If I did want to upgrade the insulation, I believe that means I have to tear down all drywall, tile, and spray closed cell foam on the walls to a thickness that meets Zone 5 requirements, and then reinstall interior finish. Probably some electrical & plumbing work.
Questions:
1) Can anyone share ANY previous experience with doing this in a residential setting. Just looking for real-world experience & not some text from a report or study.
2) What is a typical cost associated with this?
3) If after getting the batts of the walls & mold is found in a great capacity, what would a typical remediation job consist of? Yes humidity is typically high even with a properly-vented bathroom fan & a couple who hardly ever cooks or does ANYTHING that generates moisture except breathing.
We’re really tired of freezing our fingers & feet even though the heat is cranked & energy audits apparently say our house is doing “fine” in terms of energy usage. And the increase of health issues of both inhabitants makes me suspect wall insulation since it’s supposedly the not-recommended setup. Basement does have stud walls, but that setup is concrete->unfaced fiberglass->plastic->drywall.
GBA Detail Library
A collection of one thousand construction details organized by climate and house part
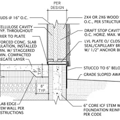
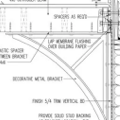
Replies
J. Pritzen,
Have you read this article yet? Insulating Old Brick Buildings
Yes, many times. I'm looking for real-world past experience on this as opposed to guidelines or the generally-accepted practices. I'm a new homeowner who just wants to know what he's really getting into if he goes through with it.
Seriously, you'll be better off leaving the interior side alone and using rigid foam on the outside. It' cheaper, and you won't end up having to live inside a construction zone. A rigid EPS wrap on the exterior costs about 10 cents per R per square foot (and doesn't take up any interior space!), compared to 17-19 cents per R-foot for sprayed closed cell polyurethane.
To hit code min performance for US climate zone 5 on a U-factor basis takes ~R15 continuous foam, if it's all on the inside of the brick. Just the insulation is going to run you at least $2.50 per square foot, could be as high as $3. Then there's the cost of the new wallboard & paint, trim, etc.
To hit code-min performance with exerior foam even without the pre-existing ~R2.5-3 fiberglass would only take about R10, but if you leave the fiberglass in place it only takes about R8. The overall lower R requirements for an exterior foam solution is due to the benefits of the thermal mass of the brick. At 2" Type-II EPS would run R8.4. That would run you a buck a square foot installed, maybe even less. The $1.50+ difference in insulation cost would probably buy you the siding and a sprayed-on WRB on the brick itself, and the detailing around the windows.
There are slick systems out there for doing foam-overs (eg, Quad-Lock R-ETRO: http://www.quadlock.com/retrofit_insulation/index.htm ) but it's also possible to just buy standard 4'x8' sheet goods and use 1x4 furring through-screwed to the masonry with masonry screws, hanging the new siding on the furring. The minimalist R10 R-ETRO is done with 2.5" of Type-II EPS, which would bring your wall performance up to better than code min for climate zone 5, close to code-min for zone 6, all without touching the interior finish.
With a foam-over you raise the average winter temperature averages of all of the structural wood, lowering it 's moisture level. With an interior foamed approach you'll have cold wet wood where ever it's in contact with the masonry. If you're in love with the look of exterior brick, there are fiber-cement panels that you'd probably find acceptable, but really just about any siding (including EIFS faux- stucco directly on the foam) will work when more than half the R value is on the exterior.
Thank you, Dana.
I had previously looked into EIFS but at $10/sqft installed, it's way too expensive & has a questionable history. $1/sqft (plus cost of siding) sounds more like it for something everyone knows (EPS). I am glad you mentioned the wood, because I am worried about that, since the floor joists sit in pockets in the brick (no rim joist).
However, I am still concerned about the possible presence of mold between existing insulation & brick & if anyone has ever gone through that.
So am I correct in thinking that the occurrence of interior insulation retrofits for regular brick houses are uncommon? I assume it happens in commercial settings or maybe multi-unit brick buildings, but for a basic, single-story, less than a thousand square-foot home, nobody really does this?