Partial wall reconstruction with rigid foam and vertical vinyl siding

My contractors and I will be partially rebuilding a 40′ section of 8′ tall west-facing wall. We/I plan to use external rigid foam and vertical vinyl siding. I realize there are some risks with these types of walls, so I’d appreciate if the community would look over the planned design and point our risks.
The climate is zone 5a (or almost 6a), about 30 miles north of NYC.
The construction from inside to outside is planned to be:
– Lowes Valspar Signature “paint+primer” (unknown permeability rating) or sealed bathroom tile
– 1/2″ drywall or bathroom green board. (hopefully providing good air penetration sealing)
– 2×4 studs but with some twisted to be 4×2 and minimal cavity depth. Usually no cavity insulation.
– 3/4″ horizontal slat sheathing. (I’ll verify the thickness once exposed.) — Possibly replacing with plywood at bottom to provide improved sealing.
– 1″ polyiso (taped) — will foil tape
– 1″ polyiso offset and taped — will foil tape
– 1×4 vertical furring strips aligned on studs
– 5″ pan head roofing screws. Tips seem to be a built to cut.
– 1×4 horizontal furring strips. Spacing to be determined.
– Mastic brand vertical vinyl siding.
I’m a bit concerned about the bathroom area having essentially two vapor barriers. (See previous post.) I’m hoping that the horizontal slat sheathing will provide improved horizontal air flow between the bays of the 9′ of exterior bathroom wall.
I hope the inner layer of furring provides a good vertical air gap for drying and bulk rain. I’m hoping the outer, horizontal layer of furring will satisfy the siding manufacturer’s requirement of a good backing material while still allowing good drying. Suggestions for spacing are welcome.
There are a couple windows on this wall which I do not plan to remove/remount in the process. I’m pretty sure that this will mean things like new boxes for the window will not be possible. I’m really counting on my contractors and their years of conventional building experience to get the window flashing right.
I’m not sure I’m going to have access to the cavities after the polyiso is applied so I’ll probably not be able to insulate the points of the screws that miss the studs.
As far as I can tell, the vertical siding hangs from the top nail and all subsequent nails are only there to keep the siding from swinging. With that in mind, I might increase the spacing of the horizontal furring lower on the wall. At the same time, I’m aware that Mastic seems to prefer continuous backing material, so perhaps I’ll not space out those furring strips.
I have no plans to drill pilot holes before screws or nails are used. I’m hoping the cutting roofing screw design will prevent split furring strips.
I’ve heard people recommend diagonal furring when using vertical siding. I’m not planning to do that, and am hoping the gaps I’ll be leaving between the first level of furring strips will make it unnecessary to mount any furring strips diagonally.
There will be good flashing and bug-screen at the bottom of the wall and I am trusting my contractors to insure the window flashing is good. I haven’t finalized how we will tastefully create a gap for air exchange at the top of the siding.
My contractors are experienced, but not with this type of wall. They are dependent on me filling in gaps in their knowledge with this sort of wall. My saving grace in this particular wall is that it’s only 8′ tall and all covered by an ample (2′) overhang except in one place (1.5″ after all these layers of insulation added). There is no plan to add gutters above this, but there are tentative plans to insure that water and ice coming offer the roof splashes away from the house at the point where overhang is less ample. (There is some rot in this place possibly due to splashing off the ground or a plant that used to be here.)
That’s about it. Have I made some questionable decisions? Have I mitigated the risks sufficiently?
J.
GBA Detail Library
A collection of one thousand construction details organized by climate and house part
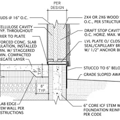
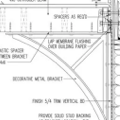
Replies
Hey Jason!
I've retrofit and rebuilt a few walls in the past 12 years w/o leaks. Just wondering where the drainage plane is (i.e. Tyvek) over the 3/4" sheathing? I don't see it on the list. You can use window frame extensions made from wood or vinyl and add those around existing frames (I use light aluminum angle flashing) as long as you cut in a lower flashing under the window to make sure any moisture heads outward if there is a window leak. You can add any fancy window frame trim to that and surrounding furring strips. Caulk and/or peel and stick above that will be fine with that sized overhang.
We're just south of Green Bay, WI and I'd worry about the interior wall being too cold. Going from 2" outer layer to 4" is a huge warming difference and allows for better drying to the outside. I don't remember ever having 1x4s split with nice screws. 1x3s YES! I'd also add some type of insulation layer inside the wall - cellulose preferred for air tightness. Easy to do from the outside with the wall apart. Remember 1/3rd insulation inside and 2/3rds outside seems to be the new model of excellence.
PK
Thanks Paul. That's a good question. I was thinking that the most exterior edge of the foil faced polyiso would be the drainage plane. Now that you reminded me, I'll make sure that my contractors understand that the window flashing would need to be respectful of that.
Jason,
Paul makes a good point about determining which layer is your water-resistive barrier (WRB). I'm not a big fan of using rigid foam as a WRB -- mainly because of the difficulties inherent with integrating window flashing and door flashing with rigid foam. For more information on this issue, see:
Using Rigid Foam As a Water-Resistive Barrier
All About Water-Resistive Barriers
The second issue to consider is the R-value of your wall. Two inches of polyiso provides only R-13. If I were you, I would double the foam thickness -- or go even thicker. However thick your foam, it's always a good idea to install the rigid foam in at least two layers, staggering the seams between layers.
Finally, some vinyl siding manufacturers insist on the use of plywood or OSB rather than furring strips under their siding. For more information on this controversy, see Can Vinyl Siding be Applied Over Furring Strips?