Parge layer on inside block – issues

Hi,
Longtime lurker, first-time poster. We bought a house with foundation issues and will be excavating three walls (thankfully the fourth wall is exposed, like a walk out basement) and planning on insulating the exterior as recommended by the Mass Save Deep Energy Retrofit Builder Guide (https://buildingscience.com/sites/default/files/migrate/pdf/GM_DER_Guide_2013-01-18.pdf)
We intend to follow the guidance on page 63, which I attached as an image. Note the last bullet point they recommend a parge layer on the inside block as an air barrier. As you can see from my walls, some have paint and glue lines where there were previous 2x2s they used to attach drywall.
I’ve read alot and I know removing you cannot put a cement parge layer over the paint and glue marks. However, removing them is going to be tedious abd will likely require scraping the glue marks and/or using some sort of toxic adhesive remover, or an angle grinder or drill with wire brush, or both. And, afterwards, depending on the method(s) may have swirl or grind marks on the block anyway.
So my questions are:
1. Is there something I can put over the paint and/or glue lines that will serve as a parge layer with minimum effort on my part? I am looking for an easy button here
2. If not, how important is this parge layer if the outside walls follow the suggestions on the attached image from that guide?
I am not looking for perfection here. If I can get 80% of perfection I am fine. According to Deep Energy Retrofit Builder Guide, the slab would need 2″ of insulation on the inside, plus a plywood layer or two and finished flooring. I don’t want to give up my basement ceiling height so I am going to leave the slab undone, other than any improved drainage put in by the foundation company. I will run a basement dehumidifier.
I’d appreciate any thoughts.
GBA Detail Library
A collection of one thousand construction details organized by climate and house part
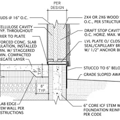
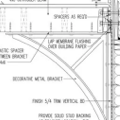
Replies
Is the concrete in good condition--i.e., not cracked? If so, it is already an air barrier. If it is somewhat cracked, you can seal the cracks with various products. Or you can cover the wall with a high-quality air barrier (and variable permeance vapor retarder) such as Siga Majrex, Pro Clima Intello or Rothoblaas ClimaControl.
Block is in good condition except for a few spots with cracks that I will patch and then fix the underlying problem with increased drainage. Michael, you say the concrete block is already an air barrier. If so, why does the DER guide implying otherwise, or are they just being overly conservative?
To install one of those air impermeable membranes in the basement is the best practice to use some sort of adhesive strips to anchor the membrane to the block wall, and then screw 2x2s or 2x4s through the membrane directly into the wall in order to attach drywall, wood paneling, etc., or anchor the 2x2s or 2x4s directly to the wall through screws (or make a free standing wall in front of the block) and attach the membrane to the framing structure, with drywall over that?
kmcdonou,
The diagram given you is a good start and I am pleased to see the drain tile beside the footing and a full fabric wrap around the washed stone bedding for the fabric wrapped drain pipe. I do understand the bituthene barrier on the outside of the block and rim level, though I would do the whole depth of the foam face to keep out termites. I did just that on my own exterior foundation XPS. If you only have the bituthene on the block the foam will likely become a home to ants and or termites. The current sealing and flashing might slow them down, but nature is very persistent. Don't use wood chips as mulch around the house or plantings as they will gladly enjoy the buffet. Ants kind of like plantings in general. Don't tie downspouts to the footing drain.
If you can get approval(?) to place the bituthene over the XPS and still use the metal coil stock to protect both you might be able to use a liquid coating on the blocks exterior. There are many choices of coatings. You could also just put bituthene over both wall and XPS. I would power wash the block before attempting any coating or membrane. There is a "glue" that can be sprayed on difficult surfaces to make the bituthene adhere better. I used it to ensure the bituthene stayed stuck to my XPS. I have a bottle somewhere, so I will see if I can provide a specific name.
Regarding the interior side of the block. The advice to parge the interior for air is more likely meant to control for moisture transport through the block. Your wall is light years ahead of the one I rescued in a prior home. I also had three side buried and one to daylight and major tuck pointing to do on the three buried sides. It is helpful to confirm whether the cores are filled, partially filled or empty. Look down along the edge of the sill plate, which in my case did not quite span the holes in the block. Do not assume the cores are filled even if someone has troweled in cement along the sill plate. That was an early form of caulking the air gap between sill and block.
The purpose of filling all cores is to strengthen the wall. Rebar sometimes dropped in too. Cost or local habit sometimes meant only do the corners and every third core or if you are unlucky like I was, nothing. In my case the damp coating on the outside was useless due to the shifting and cracking of the blocks overtime. The hollow cores had filled with water in many places making the blocks efflorescence heavily. If you don't have this problem, so much the better. If you see areas of efflorescence, I suggest drilling holes in the block cells as close to the floor as you can get to check for bulk water. Good drainage outside is the best long term cure for bulk water.
Prepping the wall is of course a royal PITA and can be achieved with wire brush, heavy scraper type blades, (not paint scraper, floor scraper) and synthetic wire wheels. The glue should chip off. The paint should be removed by the synthetic wire wheel with less loading on the brush. Some paint will survive in the block texture. You could do a test patch using the bio-safe citrus based paint removers. The risk being that the block will tend to absorb the remover and paint inward. Not helpful. Some types spread on like a thick mask coat which peels off. They also sell adhesive removers that claim to take on Liquid Nails type adhesives though chipping is often quicker.
I used a product by Thoroseal meant for sealing grain and water towers. It was a powder you mixed and brush on with one of those weird giant brushes. I found certain types of scrub brushes much easier to use and less damaging to the wrist. The scrub brush forced the coating into the block texture much more effectively. Currently, I think MasterSeal 581 is a close analog of what I used 35 years ago. Ace is one place, but check on line for further products that might be good. I do not favor UGL and the paint like ones for real water issues. If your wall seems pretty dry they might suffice. It is a tough judgement call you only get one shot at.
I have focused on parging over a membrane as a waterproofing parge will contain the water potential in the block. A membrane will allow potential moisture to gather at the surface behind the membrane and with build up, rain down between to the bottom of the wall to cause problems. With R-20 on the outside most of the wall will not be experiencing condensation from room humidity, but damp rise and the cold temps right at the floor junction can produce condensate. Others may well disagree with me.
I have also only said XPS because I am not certain mineral fiber board is able to keep bulk water out of its structure. Not too sure how you anchor it on the wall without a lot of holes nor how you would protect it against back fill. I need to get a piece and immerse it to prove otherwise, but getting a small piece locally has not been possible. At least look into the properties closely. The nattering about GWP is wildly overdone in my opinion now that the new Low GWP Foamular is available. One SUV will do more damage over its life span than your foam usage.
Your slab will be cold and a perpetual ding on your heating needs. It is also probably going to be a large contributor of moisture if no vapor barrier is under the slab. With luck the slab does have one and you can test for moisture drive with the standard plastic film square taped down on the floor. If it stays dry or presents only very slight moisture you can consider the comfort value of some insulation. I would tend to use vinyl planking as a safe flooring choice. If the basement is a rumpus room for the shorter members of your household the lower ceiling height only comes into play when jumping on the furniture.