Over-roofing options?

I’ve asked a few questions on this forum recently but wanted to start a new thread to keep the topic inline.
I live in a 1920 Farmhouse in Climate zone 4. Currently have open-cell spray foam under the roof deck and an unvented attic/conditioned attic. The current R Value under the roof deck about 22. I’m planning to add rigid insulation top of the roof deck to increase the R value and sleep better at night knowing I don’t have a wet deck and to cover a few spots of quick frost melt.
I’ve done hours of research on the best approach and narrowed it down to a couple options:
Option 1. the layers on the existing roof deck would be:
– Grace ice and water shield to act as an air barrier
– 1.5″ polyiso (do the joints need taped?)
– 4″ vented/insulated T&G nail base – joints staggered from polyiso
– roof underlayment
– asphalt shingles
This would give me a total roof system R value of about 45 with half above the deck. It’s a little thicker that I want to add (5.5″) because it makes the detail at the eaves a little tricky.
Option 2
– Grace ice and water barrier
– 2″ of polyiso (again, tape the joints?
– 3.5″ unvented/insulated T&G nail base
– roof underlayment
– asphalt shingles
This would give me a total roof system R value of about 51, still a 5.5″ add to the roof and a little thicker that I’d like but probably doable.
I’ve read a lot of information regarding vented/unvented and R values and snow loads, etc. My question is, can I go with less insulation in climate zone 4 with a snow load of 15lb/ft? I know I need R15 above the deck to control condensation but do I really need to go to R45 or R50 for the total roof?
And in a low snow load area, I know the venting under the shingles wouldn’t hurt anything, but would it help? Especially if I’m close to R45 or 50 anyway. Would more R value in the same thickness be more beneficial that the air gap? Thanks
GBA Detail Library
A collection of one thousand construction details organized by climate and house part
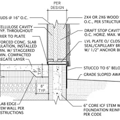
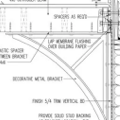
Replies
To get to code minimum only requires a U-factor less than U0.026, which is ~R38.5 whole-assembly, after factoring in thermal bridging and adding in the R-values of the roof sheathing itself, the shingles, and other layers (including interior & exterior air films).
At a typical 7% framing fraction and no interior side gypsum the R22 already installed between the rafters yields about R20 whole-assembly, and even at a 10% framing fraction (typical for full dimension rough 2 x 6 rafters rather than 1.5" x 5.5" milled 2 x 6) it would still be R19+. That means you really only need ~R18-R20 of continuous insulation (+ nailer-R) above the structural roof deck to get to code-minimum performance.
A single layer of 3.5 - 4" unvented nailbase panel would get you there, adding at most 4" to the roof thickness.
Alternatively, 2" of polyiso + a 2 - 2.5" unvented nailbase panel, seams staggered & taped works, adding at most 4.5" of thickness.
A vented nailer deck version has value in snow zones to reduce ice-dam potential, and vented nailers also protect the nailer deck itself in the event of a roof leaks, but it doesn't seem like the additional thickness is going to be worth the trouble in your case.
Thanks Dana. I'm leaning toward your second option which gets me to about R45 - which from what I understand is the high target R value for compact roofs in climate zone 4. I do like the idea of the vented deck but I think I'd rather have more R value in same thickness.
Is a single layer of nailbase a good idea? It is T&G but I didn't know if that would still cause problems. Or would applying a bead of spray foam at the joints prevent any issues?
Two layers with overlapped seams is more robust over the long term than a single layer t & g nailbase panel.
R45 "whole assembly" is approaching the financial-rationality limits for a zone 4 climate if using virgin-stock foam, according to Table 2 p10 of this document:
https://buildingscience.com/sites/default/files/migrate/pdf/BA-1005_High%20R-Value_Walls_Case_Study.pdf
If using reclaimed roofing foam at less than 1/3 the price of virgin-stock goods it moves the rational-R levels up a bit. Nailbase panels have a higher material cost than simple sheet goods, but save a bit on labor. The material cost of 6" recliamed foam + OSB nailer deck is still less than the material cost of a 3" nailbase panel at half the R.
So I've figured out a detail where I can use the 4" vented nail base over 1 1/2" of polyiso, adding a total of 5 1/2" to the existing roof and getting to R45 total with about half of the R value above the existing deck and half below. So my question is, am I just overdoing here? I want to do it right but I don't want to waste money or add additional thickness I don't need to. Thoughts?
And thanks Dana for the reclaimed rigid idea, but unfortunately I haven't found anyone local that will make that option feasible. Still looking though.
R45 at center cavity, half of which is a continuous thermal break over the rafters is definitely better than code-min performance, but not complete overkill.
BSC is suggesting in Table 2 of BA-1005 (the link in response #3) that R45 "whole assembly" would be the right range for a "compact roof" on a lifecycle economic basis, and you'd be nearly there- close enough to not really worry about it not being quite enough, and not over the line into the irrational zone.
Michael,
I am currently using the ThermaCal vented nailbase on a project. I decided to go with 2" of polyiso and then a ThermaCal panel with 2" of polyiso, 1" air gap and 5/8" CDX. I was told this would be a better stack-up then just a 4" layer of Polyiso on the nailbase, despite the fact that the panels are T&G. Having used the panels, I can now see why I was told that as the T&G ends are not very tight and leave quite a bit of air space. I suppose you could "butter" each piece with a bead of spray foam when installing, but that is more work that no one wants to do when they are on a roof. Also note that the blocks in the panel are spaced 12" OC, not 16" so the fasteners for the most part do not hit the rafters, but the roof deck. May be an issue for some depending on the roof pitch. There is a lead time with the product, 4 weeks in my case, the roof guys had a hard time cutting them with the air gap (they tell me they are roofers, not carpenters), the polyiso is glued to the underside and on a few panels they came off and there just seemed to be quite a bit of waste as my guys had never used this product before. While I like the concept of a top-vented roof, I think it would be easier to make it on site. We came up short on panels for this project and so we are going to build our own top-vented roof to finish the balance (once we get some dry weather, which seems like never this year).
Jonathan,
Thanks for the comments. Are you using vented nail base for snow load reasons or just to vent under the roof? Maybe your using shingles? I live in a low snow load area so I'm trying to decide if the top venting is just adding unneeded cost and hassle. I do plan to use an asphalt shingle roof.
You mentioned the blocking in the panel is spaced 12" o.c. - I assume you mean the blocking the air space - do you have to screw through the blocking or can you just screw anywhere on the panel?