Our builder insulated our cathedral ceilings with dense pack insulation. Now we are having condensation and mildew problems.

We have contacted a local roofing company and it proposes to remove our shingles and sheeting and then remove all the insulation. They also propose removing siding where necessary. Cost: $140,000. Is there another solution?
GBA Detail Library
A collection of one thousand construction details organized by climate and house part
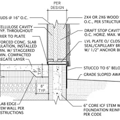
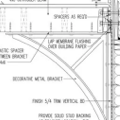
Replies
Insulation is rarely the cause of a problem, but it can suffer the results of other mistakes. Is the roof vented? Is there an interior air barrier? Recessed lights in the ceiling?
Unless you own the biggest house around, $140,000 sounds nuts. What is the planned repair?
Did the roofer explain what the problem is and the supposed cause?
Where is the house located?
Do you have details about the roof construction or what kind of insulation is there?
Pay a few hundred dollars to an actual expert, i believe Resnet and BPI have people who can determine the real cause and save you well over 100k
Where is the condensation and mildew occurring specifically?
If your builder used dense pack insulation WITHOUT installing closed cell insulation over or under de roof decking first, then this is not a surprise. Code REQUIRES IT in all climate zones! (See IRC 806.5). A typical case of people not knowing what to do.
Unless you have a very large and complicated roof, $140K seems high.
Need a lot more information, starting with the climate zone, and the materials stackup of the assembly from the interior ceiling paint/finish to the shingles.
Comments on responses: House is in south central Indiana; Insulation was installed after roof on house with netting from the inside; Insulation appears to be cellulose; Roof is not vented although there are soffit vents and ridge vents at the apex.
Would be glad to have an expert evaluate this. Will follow up with Resnet and BPI;
Condensation is at the peaks inside. Told that it's because insulation has slid down and that there is a temperature differential from inside to out causing the condensation.
Well, sounds like your contractors were idiots. What kind of morons add or retain vents where they'll allow outside air to pass through air-permeable organic insulation, not only completely compromising its operation but introducing a near-certain vector for condensation and mold growth? Sounds like gross negligence to me. I'd sue.
Are you seeing the condensation on the interior surface of the ceiling, or is it happening in the cavity?
$140k does sound high; it's also not clear how his proposal would help--is he proposing a specific plan as far as replacement insulation?
In any case, well worth getting an expert to look at it.
#9, we are seeing condensation on the inside surface of the ceiling.
I'll fix it for $135K anywhere in the world!
Old fashioned competition i see, i will add my 2 cents (minus inflation), and pitch a quote for $134,999.99
On the other hand If i were the OP i'd offer to pay Dana and Martin to come to Indiana and save upwards of 140k
James,
You still haven't provided many details. Is this a painted drywall ceiling? What were the circumstances leading up to the insulation job? Is this new construction or an insulation job at an old house?
It's unusual to get condensation on a painted drywall ceiling. Such condensation tells us two things: (a) your indoor relative humidity is probably too high (this can be confirmed or refuted by some measurements with a hygrometer), and (b) your ceiling is unusually cold.
Here is a link to an article that explains what you need to do to lower your indoor relative humidity: Preventing Water Entry Into a Home.
We don't know why your ceiling is unusually cold, but we can guess. It's possible that the air-permeable cellulose insulation wasn't dense-packed -- it was installed at a low density, allowing outdoor air to travel through the roof assembly from your soffit vents to your ridge vents. If that outdoor air is passing through poorly installed insulation, or if the insulation crew missed some of the rafter bays (leaving them empty), the moving outdoor air could be cooling your ceiling.
James, I second the recommendation for a BPI and/or RESNET certified energy auditor. I think you want someone who can perform a blower door test and infrared inspection and who will bring a hygrometer to your home (and perhaps datalogging-type hygrometers that can be left at the house to collect data for a few days or weeks).
A roofer is not likely to be the person to solve this. You want someone who can make a thorough building science investigation.
If you post some photos of the house, interior and exterior, the eaves, the ridge of the roof, and whatever else you have, that might help.
#13 response: 2 bedrooms are painted dry wall. Great room is wood (car siding); This was new construction. Our indoor humidity is not high so I think the condensation is due to temperature differential.
An inspector determined that the insulation has slipped down and that there is none near the apex of the roof. Thanks for you inquiries.
James,
There are many issues here.
If your insulation installer doesn't understand dense-packing techniques, and the insulation slipped down the rafter bays, leaving the upper sections of the bays uninsulated, then there is no mystery to what is going on.
However, there may have been other errors committed in the design and construction of your house.
1. Did the design include a ventilation channel between the upper surface of the insulation and the underside of the roof sheathing? When installing cellulose insulation, this ventilation gap is required by code (unless you have a thick layer of rigid foam above your roof sheathing). You need a stiff ventilation baffle (made out of plywood, rigid foam, or some type of plastic) to make sure that the cellulose insulation doesn't block this channel.
2. Ideally, the cellulose insulation would have been installed at a density of at least 3 pounds per cubic foot, and the R-value of the installed insulated would meet minimum code requirements (R-49 -- that's about 13.5 inches of cellulose).
3. You need to have an air barrier behind your car siding (board) ceiling. Car siding is not an air barrier; it requires a layer of taped gypsum drywall (or a heavy air-barrier membrane) between the boards and the cellulose.
Thanks Martin. I'm guessing the builder made many mistakes. The design provided for soffit vents and ridge vents which were installed. When we had this checked by a local, he found that the ridge vents were blocked off so that there was no air flow. I have no idea whether the details to which you refer were ever incorporated, but I seriously doubt it. What I believe happened is that the roof was completely installed and then netting was tacked on the rafters. Then cellulose was crammed into the cavity all the way to the peak of the roof. Then the netting was buttoned up at the top and the dry wall and wood ceilings were installed. From what I'm reading now, it sounds like a ticking time bomb. I need an expert to make a home inspection.
Finding a good expert is tricky since this is not a mainstream issue, and most will tell you what they know, spray foam it or tear everything down and start over (which seems to be the answer you got, but 10x overpriced)
Alan,
I disagree. Improperly vented or improperly built unvented roofs are probably the most common cause of building envelope failures. Any reputable builder should be able to suggest a fix for this.
The only real benefit of getting a building scientist to write a report detailing what caused this is to assign blame for the costs of damages and remediation.
Lets just say we probably live in very different universes and agree to disagree
I dunno, Malcolm, I know a lot of builders who are only marginally up on this kind of stuff, and would do the same thing in an expensive custom home.
Yeah, I agree w/ Meiland. As I often say, any idiot can be a contractor and most do.
Don't get me wrong - just because the population density isn't as high here doesn't mean we don't have the same proportion of idiots. But we have a compensatory mechanism, which is our code, and it specifies how roofs have to be built. So builders here, smart and dumb, get used to ventilating roofs and having that ventilation inspected. When faced with more complex unvented assemblies, they have to run them by someone who knows what they are going.
If you described James' roof to any builder here they would ask where the ventilation was, or who had approved it to be installed that way.
Clearly the original question comes from someone in a region with less effective code enforcement! I am glad to hear it works well there.
In US climate zone 4A it takes 30% of the total R to be on the exterior of the fiber layer to keep the fiber dry, assuming there is a reasonable air (but not vapor) barrier on the interior side. If it's a wooden plank ceiling you could use either air-tight drywall or a "smart" vapor retarder between the wood ceiling and the insulation. If you're stripping the roof decking as part of the rehab (which might be easier and cheaper than replacing the ceiling) a 2" shot of open cell foam is a sufficient air barrier. To make replacing/repairing the ceiling wood easier, tack down a layer of kraft paper or something on the rafter bay side of the ceiling so that ceiling isn't glued to the foam.
You can then dense-pack the rafters, provided you put a layer of rigid foam above the roof deck, or make it all open cell foam. If the're 2x8 rafters the lay-up of o.c. foam + cellulose would come to about R27, so you'd need a minimum of R11.6 above the roof deck, either 3" of EPS or 2" of polyiso, for a total of about R38-R39. That would not meet current IRC code minimum for total R, but would have met IRC 2009 minimums. To bring it up to IRC 2012 or IRC 2015 code min would require a total of 5.5" of EPS or 4" of polyiso.
If it's 2 x10 rafters you'd have R35-R36 in the cavity, which would require at least R15.4 above the roof deck for ~R51-ish total. That's 3" of polyiso or 4" of EPS. That WOULD meet current IRC code for roof-R.
For a budgetary estimate, EPS & polyiso typically runs about 9-11 cents per square foot per R, installed. Open cell foam 10-13 cents per R-foot. The simpler the roof lines, the less cutting and less scrap you get with the rigid foam, pushing it to the lower end of the estimate.