OSB + fluid applied WRB VS. Zip
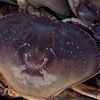
Curious about two ways to accomplish the same goals: strong air-sealing and improved resistance to wind-blown water, simpler integration of window/door flashing and penetrations.
1.) Zip System sheathing. Pros: Simple, relatively proven, and available. Cons: Costs ~50% more than OSB, and still requires labor in addition to hanging the sheathing (taping seams, window flashing tape).
2.) OSB + painted/rolled on fluid applied WRB (StoGuard, DuPonts Fluid Applied WB, etc.). Pros: Less expensive than Zip (I think?), easily done by me after the framer gets done (i.e. “free labor”), easy to treat cut edges, easy to integrate into door/window/penetration flashings. Cons: Added labor, maybe performance issues?
Your thoughts on which approach makes more sense? (FYI this is in zone 5B, on a 2 x 6 16″ O.C. building with blown-in-blanket fiberglass insulation, no exterior foam).
GBA Detail Library
A collection of one thousand construction details organized by climate and house part
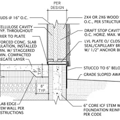
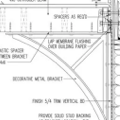
Replies
Until you compare actual costs rather than guessing you won't know.
With regards to liquid applied WRB's you still have to address the joints (see link) with sealant first.
https://www.buildingscience.com/documents/building-science-insights/bsi-103-joints-and-corners-and-penetrations
"Back to movement. Joints and inside and outside corners open up and close up all the time. The gaps get bigger and the gaps get smaller. Let me repeat the point here…they don’t just open up…they go back and forth. The water control layer we cover them with…the liquid applied membranes that are spray applied, brush applied, trowel applied, or whatever, need to be elastic. Think rubber band. There is elongation and recovery. There is cycling. There is fatigue. There is aging.
There is more. There always is. The geometry of the joint and corner matters. Both the material properties of the joint and corner treatment and the geometry of the joint and corner matter.
With a “difficult” joint and corner the material properties of the liquid applied membrane are a big deal. With an “easy” joint and corner the liquid applied membrane is stressed less. Not too many liquid applied membranes have the material properties to handle “difficult” joints. But with the field experience over the past two decades with liquid applied membranes we can turn “difficult” joints in to “easier” joints. The best combination of course is combining a high performance liquid applied membrane over a joint that has been made less stressful."
High-quality fluid-applied WRB are expensive. It's not just 'rolling it on' - you need a nearly-perfect seal - usually requires two coats, plus detailing joints and problematic areas. Many are also weather-sensitive - need right humidity/temp/clear skies. Some require commercial-quality sprayers that costs thousands (and nobody rents them out).
Definitely use a rain screen - heck, it's the most important defense - provides a pressure drop and a capillary break so that moisture can't get to your sheathing and will dramatically extend paint life. If budget is stretched, I'd use a low-cost mechanically-fastened wrap and then tape/detail seams and penetrations and install a high-quality rain screen assembly.
Hey Ryan,
I'm not sure why you think the flashing details will be easier with the fluid-applied WRB. In fact, you could use ZIPs fluid applied product with ZIP sheathing for doors and windows if you wanted and it would be just the same process. But I'm not making a case for ZIP. That just stuck out to me in your pros and cons.
You're going to get some opinions, but as you know, the decision will come down to cost and what you are comfortable with for process and details.
If I were building a house today, I'd include plywood with taped or fluid-flashed seams as the exterior air barrier, and a mechanically-fastened WRB as one of the options, at least if I was installing flanged windows. It seems that there is some benefit to plywood when it comes to vapor control and some evidence of it being more durable that OSB when things go wrong, and there is something reassuring about being able to integrate the WRB with flashings without any reverse lapping.
I'll be interested to hear other's opinions on this one.
Hi Brian,
I agree with your sentiments. I am going to be building a home next year in SE MI which is climate zone 5. We get a good amount of rain (36 in), snow, cold, hot and wind. I plan on using plywood sheathing with a mechanically fastened WRB. I will definitely seal the sheathing joints, just not sure if I will use tape or fluid flashing. I think this strategy has the best chance of being installed well enough by the contractors that it will work in practicality. I will use rock wool insulation in the wall cavities to allow for good drying and mold growth resistance.
The only part I’m struggling with is whether or not to add exterior insulation and / or furring strips for a rain gap over the WRB. I’ve read a lot on various ways to execute the window flashings and they all look to take more care and attention than any contractor would provide. I want outie windows (flange mounted) so they look like a normal window install. That will mean building up each window frame out and I haven’t seen a recommended way of integrating the WRB around a built up frame....not one article or video. Seems like more trouble then it is worth.
I'd like to second the excellent advice from John and Brian. My own preference is to rely on lapped-joints, so I'd stick with sheet WRBs - and definitely plywood over OSB.
Another option are the adhered WRBs. I have no experience with them, and will be using builders around me at as guinea-pigs to judge both the difficulty of installation and cost.
I’d say it depends on how “free” you consider your own labor to be.
The labor to joint fill seams (necessary for the liquid WRB) is, by definition, equivalent to liquid flashing the Zip seams (which is one acceptable means of handling them).
So, the question really is: is the cost of the liquid WRB plus your labor “cost” to apply it less than the material difference between OSB and Zip? I find it hard to believe that it is. Further, if it were me, I’d be comparing the all in cost of Advantech or plywood sheathing (rather than commodity OSB) plus the liquid WRB vs. Zip.
What do you think about this tidbit from GBA's article "An Intro to Control Layers of a Wall".
"Mechanically fastened WRBs like Tyvek Homewrap are more difficult to make work as part of the air control layer."
I do appreciate your comments. The CDX + house wrap is an interesting option as well. I was not aware that CDX was superior in terms of air sealing (with tape/sealant over the seams, of course).
Ryan,
Plywood has two advantages over OSB. Unlike its cousin Zip, some OSB isn't entirely air-tight, and it also degrades much quicker when repeatedly wetted.
Mechanically fastened WRBs are very hard to air-seal effectively. They are best used in combination with another air-sealing strategy, like a separate interior air-retarder or taped sheathing. What I like about them is they rely on laps (gravity), rather than sealants for their joints and at flashings.
I used 2 rolls of peel & stick WRB over plywood on my own project. Blueskin VP100 & Vycor - they had a learning curve to get used to, but move fast once figured out. I was using it for the air barrier & WRB.
They don't sell the feature that the siding nails will or may "seal" when driven thru the WRB, but it seems like they would.
They were easy to visually inspect the installation, and you didn't have to worry about film thickness like with the fluid applied.
I did not blower door test - but I have kept the ants out.
Tim,
What was the price like?
Blueskin from https://www.dhcsupplies.com/store/p/6095-Blueskin-reg-VP100-Self-Adhered-Water/Air-Barrier-Membrane-48-x-100.html
$260 for 400 sq ft
I got the Vycor from the orange big box for about the same price.