Options if inspector insists on interior poly barrier?

I’m planning a small one-room addition on my home in Ottawa, Canada (zone 5-6 based on my read of the US map). This will have a simple shed-style roof with a cathedral ceiling and vertical board siding.
Having followed GBA for a while I would like to use the suggested wall assembly of exterior foam (sufficient for warm sheathing), batt or blown insulation in the stud cavities, and airtight drywall — and no interior poly barrier.
I have been warned by my designer that the building department here is not likely to approve anything that does not include the poly “VB”. If that’s truly the case, what are the options for a better-than-average insulation system? (“average” around here being stud cavity insulation only, thermal bridging be damned)
If I must have the interior poly, is it safe to have any amount of exterior foam on the walls or roof? I know some foams are vapor-permeable, but if I have say 1″ or 2″ of exterior XPS foam, is that really a wall assembly that can dry to the outside? My instincts say “no” but if I’m wrong please let me know!
Thanks,
Chris.
GBA Detail Library
A collection of one thousand construction details organized by climate and house part
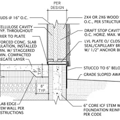
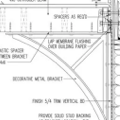
Replies
Chris,
You have two options:
1. You can try to educate your local building inspector. There are some documents published in Vancouver, BC that may help you do the necessary convincing -- I'll try to post the links when I find them, or perhaps a Canadian reader will beat me to it. A warning, however: many builders have found that it's harder to educate a building inspector than it is to train a cat.
2. You can just install MemBrain (a so-called "smart vapor retarder" with variable permeance) instead of poly. It seems that most building inspectors just want to see something that comes in a roll installed on the interior sides of the studs, so this solution often satisfies them. While the expense is unnecessary, it's often cheaper and faster than battling city hall.
OK, thanks. I guess I could also go with a double-stud wall or something like that, but I have to say it sounds a little too complicated for this project.
Chris,
I am a recent mechanical engineering graduate from Carleton University with a focus on residential building envelopes. I would be interested in following along with your project or help you "educate" our inspectors. If you wish to contact me, you can do so at [email protected].
Regards,
Chris,
The problem is that building inspectors in most Provinces of Canada are rather simple followers of the law, over which they have no influence other than asking their local municipal authority for a change in the relevant by-law. What I am saying is that your typical local inspector (who is quite often well technically qualified - i.e. as a P.Eng.) has no little or no discretion to permit a "significant" variation to the locally applicable code. What is significant? That point is indeed discussable with the inspector, and may offer a way forward in a given case!. Normally, the local code incorporates all or many parts of several national codes/standards by reference (e.g. electrical, plumbing, insulation, ventilation, structural etc.). At the local level, these are considered "safe" and thus practically sacred to individual more or less technically ignorant elected Councillors (I am one, so know how the system tends to work).
Following this reasoning, I would heartily agree with Martin's suggestion to use something like Membrain, and either find out if your inspector will permit this as a non-significant variation or instead hope that the inspector does not notice, provided that you are ready to run the risk that he has the legal right to require you to rip it out.
Good luck, Tony.
Anthony,
I disagree with your position about MemBrain. I'm in a similar situation as Christopher where I want to avoid using a poly vapour barrier in our new house. We’ve met with the city inspector before finishing the house plans to discussed of the various possibility to find out that you’re ok as long as the product you intend to use as a CCMC approval number, which is the case for MemBrain. http://www.nrc-cnrc.gc.ca/ccmc/registry/pdf/13278_e.pdf . The inspector also approved 5/8” OSB as a vapour barrier. Another option is to obtain a stamp from a certified architect. Good luck with your project Christopher.
Marc, Actually I don't think we disagree - provided you can persuade your local Inspector that what you want to do lies within the by-law as written plus his allowed discretion, you are fine. It is just that most local by-laws are pretty inflexible in their implementation.They vary quite a lot between different locations. If you don't want to use a Poly vapor barrier, and the local code requires it, that is where the problem lies and one has to find a work-around.
Regards, Tony
Chris,
I am not an expert - but from what I've read 2" (and more) of extruded polystyrene acts like a vapor barrier.
I don't know your system, but ...if I was going to install >2" rigid foam over wood sheathing (e.g., a retrofit), I would leave a 10 ml drainage plane / capillary break between the two.
Allister
Allister,
I assume you meant "10 mm," not "10 ml." It doesn't make much sense to measure a gap depth in milliliters.
The reason that you don't want a 10 mm (3/8 inch) gap at the location you propose is that you don't want any air flow between the exterior insulation and the insulation between the studs. With air flow, the exterior insulation becomes useless.
As long as the exterior foam is thick enough to keep the wall sheathing above the dew point during the winter, then the sheathing will be warm and dry all winter long. The only danger occurs when the sheathing gets cold and damp.
More information here: Calculating the Minimum Thickness of Rigid Foam Sheathing.
Martin,
Yes, I meant mm (not ml).- thanks.
My read is that there is movement away from having >2" rigid xps/eps (a vapor barrier) directly on osb/plywood without some kind of avenue for moisture drainage between the two?
An example of a system that kind of does this is EIFS - however their 10MM drainage plane is expanded foam with an integrated moisture drainage systems (e.g., vertical channels). I just saw an expanded foam which almost looks like a dimple board to allow moisture to drain. I understand expanded foam is more permeable than xps/eps.
I had a discussion with an architect who does not support (at all) putting extruded polystyrene directly on osb/plywood. I'm doing a renovation so trying to figure this out.
Thanks,
Allister
I should mention - where I live (Canadian Prairies) is extremely cold during winter ( -25C to -40C for many weeks) and the maximum amount of exterior insulation I can add is 3" ( e.g., R15). The interior walls have R12. I don't know if that combination will keep the temp above the dew point at the wood sheathing interface.
Ottawa (where Chris lives) has warmer winters than the Prairies but it's still darn cold.
Appreciate your advice...
Thanks
Allister,
There are two potential sources of moisture: rain and condensation (or accumulation) of interior moisture carried by leaking air or diffusion.
The rain is handled by good flashing and a rainscreen gap (10 mm if you like, or more) between the siding and the rigid foam.
The potential for accumulation of moisture from leakage of interior air or diffusion is handled by making the rigid foam thick enough to keep the OSB or plywood warm.
If you can't include a rainscreen gap between your siding and the foam -- for whatever reason -- some people worry about OSB, and they include wrinkled housewrap (NOT a 10 mm gap) between the foam and the OSB. A 10 mm gap would be too large, because you don't want air flow between the two insulation layers.
EIFS is a category unto itself, with its own history of moisture problems and its own solutions. You are right that EIFS manufacturers now include drainage channels between the foam and the OSB. But these drainage channels are significantly smaller than a 10 mm. gap.
More information here: Calculating the Minimum Thickness of Rigid Foam Sheathing