Open cell under the roof sheathing – now what?

In 2011 we gutted/renovated a 1960s/70s era cape. We were working with an Energy Star certified builder and at the time all the exterior drywall was removed and the 2×6 walls were sprayed with icynene. The roof and slopers were also sprayed creating a conditioned space where a Fantech HRV was installed. The rafters are 8″ and the foam fills the rafter bays and covers the rafters as well. We also installed Marvin Integrity double paned low-e windows and the contractor and his crew were very diligent about taping and sealing. At the time, we were reluctant to go with closed cell due to the spraying agents and a super sensitive asthmatic son.
It wasn’t until recently while researching insulation options for my garage project that I read about issues with excessive moisture damaging roof sheathing due to spraying open cell directly on the underside of the sheathing without a vapor barrier. We’re in climate zone 6 and fortunately have not had any moisture issues.
We were considering adding more open cell foam in the attic to up the R-value from the current R-28 to R-44 (+4″) while the garage was being foamed. One quote added about $1200 to do this.
So, now what?
1. Is our roof at risk the way it is? The roof is sheathed in Advantech with 2 layers of ice and water shield along the eaves, gables and in valleys, then a layer of Triflex covering the whole roof topped with architectural shingles.
2. Is it worth it to add more insulation? It’s the only place we can really tune. And we’re trying to further tune our heating to work out some cold spots. The house is pretty tight – even needed to install make-up air for the range hood. There is no rigid foam on the exterior of the framing – just 2″ on the exterior of the foundation.
3. Should a vapor barrier be installed over the existing spray foam? Or could that bite us by trapping potential moisture in the open cell up against the roof sheathing? If we should add a vapor barrier, what should we install? Would spraying 2″ of closed cell on top of the open work?
4. Should we add some ventilation to be on the safe side ? Since the HRV is already in the attic, I could explore adding a return and/or supply register up. But then would that violate fire code? Or should we just leave it be and monitor moisture/RH in the peaks and on the floor of the attic?
many thanks in advance for your advice..
GBA Detail Library
A collection of one thousand construction details organized by climate and house part
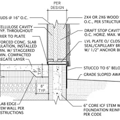
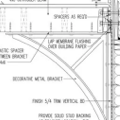
Replies
I will give your post a bump.
I think it is worthwhile to monitor indoor humidity. For peace of mind, I installed a SensorPush Wireless Thermometer/Hygrometer in my attic after foaming the roof sheathing.
If it's simply a dead-space attic and fairly air tight to the fully conditioned space below, a very modest amount of supply-only ventilation with outdoor air should take care of it. Something like this would work:
https://na.panasonic.com/us/whispersupply-walltm-supply-air-system-10-cfm
With the attic slightly pressurized relative to the outdoors the attic won't be pulling in moist conditioned space air driven by stack effect all winter, and the air that is being injected into the space is ultra-dry outdoor air during the colder weather when moisture might otherwise accumulate in the roof deck.
If doing it with an HRV it has to be supply-only to pressurize the attic, which would then un-balance the HRV, reducing it's efficiency slightly.
A vapor RETARDER could be installed over the existing (or new) foam, but not a true vapor barrier. A variable permeance "smart" vapor retarder such as Intello Plus or Certainteed MemBrain would allow the roof deck to dry over the summer (unlike 6 mil polyethylene), or even "vapor barrier latex" half-perm paint on gypsum board (not a true vapor barrier, a class-II vapor retarder). These would limit the amount of moisture uptake in winter, yet still provide a drying path. But without some active ventilation of the attic space the moisture would not be purged to the outdoors.
Doing both as a "belt and suspenders" approach wouldn't be crazy.
Q to Dana: What if OP cut out a small supply vent (HVAC) and then add a transfer grill into the space below?
>"What if OP cut out a small supply vent (HVAC) and then add a transfer grill into the space below?"
The HVAC air has the same moisture content as conditioned space air, and would increase rather than decrease the wintertime moisture burden at the roof deck. It's the opposite effect of what the goal is. Ventilating the attic with a tiny amount of OUTDOOR air which is much drier than indoor air when it's cold out lowers the moisture burden in the attic.
Only during the (much briefer and shallower) cooling season in zone 6 would an HVAC supply duct remove more moisture than it adds.
The transfer grille might also run into fire code issues unless all of the foam gets covered with a thermal barrier against ignition.
Thanks for the recommendations. I had the original foam company in to give a quote on the garage project and look at the existing house attic foam. I didn't realize it, but when they installed the foam they did spray a vapor barrier over the finish. So that's good news.
I'm reluctant to poke a hole in the house to the outside to bring supply air into the conditioned space. I'd rather work with the HRV since it's in the attic anyway. It's a fully dedicated Fantech SHR1504 and tied into a drain. I'm able to set an RH level on the central controller. If I were to extend HRV capability to the conditioned attic and keep a balanced system, would putting a supply and exhaust under these conditions be sufficient?
>"I didn't realize it, but when they installed the foam they did spray a vapor barrier over the finish. So that's good news."
That is not necessarily good news. What was the product? Was it applied to the foam, or to gypsum board in close proximity to the foam on a cathedral ceiling, or to the ceiling gypsum below the floor?
If it was "vapor barrier latex" paint, that has been proven to be ineffective, barely moving the needle on vapor permeance when applied directly to open cell foam, whereas it's quite effective when applied to paper faced gypsum board.
If it's on the ceiling under the floor it's unlikely to be doing much good, given the number of likely leak points of the ceiling. A square inch of air leak moves much more more moisture than the entire whole ceiling's worth of vapor diffusion through standard latex paint, orders of magnitude more than through vapor barrier latex. What are the odds that the HRV, ducts, and register boots are going to be air-tight for life? How about all the electrical & plumbing penetrations?