Open-Cell Spray Foam vs Fiberglass for Wall Insulation

All,
Thanks in advance for your help. Trying to finalize insulation choices w/my builder and am currently debating open-cell spray foam vs dense fiberglass (BIBS) in my walls. Attic will be conditioned (2″ closed cell + 5.25″ open cell). I’m at the very north end of Zone 3 (basically on the line between Zones 3 and 4).
My wall assembly from outside in will be Hardie->3/8″ furring strips serving as rain screen/drainage plane->1″ XPS->Zip sheathing->2×6 framing.
From an embodied energy standpoint, off-gassing potential, and flammability standpoint, I’d like to stay away from the spray foam except where needed. With proper air sealing of the exterior shell (Zip + whatever additional air sealing is provided by topping it with the foam) do I need the spray foam to achieve sufficient air sealing? What would folks here generally go with (dense pack cellulose is not an option w/our builder)?
I am looking to achieve in the neighborhood of 1.5ACH50 if that matters.
GBA Detail Library
A collection of one thousand construction details organized by climate and house part
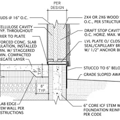
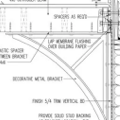
Replies
If you care about embodied energy, ditch the XPS unless it is recycled. If you don't have access to recycled foam, use eps or polyisocyanurate.
You don't need spray foam in the roof, either, in cz3: https://www.greenbuildingadvisor.com/article/vapor-diffusion-ports
Many people have had very good success with Zip.
Ok, so vapor diffusion ports is an option except for the fact that I can't get near the R-value I need b/c somehow (blame the builder, blame the lumberyard, who knows), they framed out the roof with 2x8s instead of 2x12s like the plans called for. So using fiberglass or cellulose in the attic would only get me ~R24. Closed cell + open-cell cavity fill lets me get to R35 or so in the roof (plans called for R-38). We're also not using Zip on the roof (couldn't get builder to do that), so I would also lean towards spray foam in the roof for added air-sealing there.
But, back to the walls. I could ditch the XPS, I suppose...but it's already on-site to be installed this week. I'm not a huge fan of polyiso b/c of degraded performance in cold temperatures. I tried to get the builder to use Rockwool Comfortboard, but he didn't go for that. So XPS was what he said he could get. So yeah, I care about embodied energy, but sometimes you have to take what you can get. Seems to me, though that if we do the air sealing right at the Zip/exterior foam and make sure to deal with any penetrations, the spray foam shouldn't be needed for air sealing purposes and I'd be ok going w/BIBs?
If the XPS is purchased and on-site, then I would use it. If you are using Zip as your air barrier, there isn't a good reason to use open cell in the walls unless it is less expensive.
In CZ3 the temperature effects on polyiso are not really relevant. Any loss in performance is measured in hours, maybe days, but not months.
Zip tape can also be used on plywood or osb roof sheathing to join the roof air barrier to the wall air barrier. CC spray foam is very useful for retrofits and where its low permeance is necessary for vapor control. You have a new building in a warm climate, so I don't see the utility of using it. Besides, the closed cell in the roof isn't buying you all that much r value:
https://www.greenbuildingadvisor.com/article/installing-closed-cell-spray-foam-between-studs-is-a-waste
Is the height of the ceiling underneath the roof a concern? If not, cross strap the roof with 2x4s on edge and add R13-15 of fluffy underneath the rafters. Inexpensive and a fairly substantial thermal break.
Yeah, I've considered doing things for the roof like cross-strapping, putting foam board on the bottom of the rafters, etc. All still on the table. I at least think I understand my options there. A lot of that will come down to what my builder is comfortable doing.
I'm not sure I agree with the temperature effects on polyiso being neglible where I am. Like I said, I'm at the border of CZ3/4. Average temps in Jan/Feb are lows in the upper 20s, highs around 50F. From what I've seen/read, polyiso performance peaks around 60F. It then declines sharply from 60F to about 15F (conductivity increases from 0.02 W/mK to 0.07 W/mK...at 30F, about my normal low for a couple months of the year, it's conductivity is 0.05 W/mK. Other sources don't have it quite as bad (e.g. buildingscience.com says that the mean R-value at 25F is 4.7). Maybe it's not a huge difference, but I'm not sure how I feel about my insulation losing 15-30% of it's effectiveness in the dead of winter when I'm wanting it the most. And on the coldest days where I am (teens with a few single digit readings a year), it'd be worse.
So I guess I'm kind of right on the edge climate wise where I feel like the temp dependency of polyiso makes a difference.
Matt,
I am looking at similar issues for a Zone 3/4 build. From past experience on a previous house, I can tell you that the extra inch of exterior foam adds quite a bit of cost and complexity to the build process (especially if you are doing two stories).
For my new house, I am considering this wall stackup: cement or composite siding, Coravent rain screen, Zip R-3 (taped), 2x6 framing, R-23 rockwool or blown cellulose, and airtight drywall. Cost is a factor, but I'm also trying to keep things simple from a construction standpoint. I know the builder and his subs are comfortable with most of these materials and shouldn't give me much grief over putting it all together. (Fingers crossed.)
On air sealing, see Martin's list of articles here: https://www.greenbuildingadvisor.com/article/how-to-do-everything.
[edit]
You can achieve a lot with tape and caulk. You should schedule a blower door test and air sealing before the drywall goes up as well.
Steve,
It sounds like we are in similar boats. You must be in north Georgia? I am in north Alabama (Huntsville metro area). I had suggested using Zip R-3 or R-6 to my builder because I thought it would be an easier install. he decided he'd rather do the foam separately. I have not really gotten him on board with something like Coravent as he thinks 3/8" thick furring strips will be sufficient to create a drainage plane behind the fiber cement (I will probably defer to him on this unless I hear something compelling otherwise....there are times when you need to save your bullets for another day).
I'd be interested to hear what you're planning on doing for airtight drywall. Caulk behind drywall? A gasket (like the Conservation Technology gaskets?). I, like you, am certainly conscience of cost, but am more concerned with keeping install simple for the builder/subs. One of my revelations in building is that even getting things installed per manufacturer's instructions is often a difficult thing to do. For example, I had the builder use the conservation technology sill gasket combined with Siga Fentrim F-6 tape to seal the Zip/foundation interface. I thought it would be a simpler install than having them doing something like a double bead of acoustical sealant between sill plate and foundation and a liquid flash product). The Fentrim tape is simple to install. I've never used it before, but had no problems installing in my experiment on some wood/cinder blocks at my current house. AFter they installed it, I went out and found numerous places that clearly weren't rolled well and thus weren't adhering...which defeats the whole purpose.
So to me, as our build goes on (framing just finishing up), the more important it is to me to go routes that are going to get installed correctly. This is the same battle we had w/choosing an HVAC. I might've preferred a ductless minisplit, but after talking to the HVAC installer, I just wasn't confident that we'd get a good install, so we ended up going with a 3-ton Carrier Infinity Greenspeed unit.
It has become apparent to me that if you want your house built to the standards that I think most of want (if we're hear posting on this forum), we have to work closely with the builder and be proactive in helping develop solutions that work for everyone.
Good luck with your build! Where are you at in the process?
Matt,
We are on the north side of Atlanta and early in process. We were ambivalent about building again (This will be our third custom home.) but ultimately concluded it was our best option for getting most of our wants.
I agree that it is easy to spec requirements and much trickier to have them fully and correctly implemented. I also agree that it's better to opt for simplicity over cost when that's possible.
The builder will are talking with seems knowledgeable and willing to accommodate some modification of his usual practices. But I guess we will see what happens when the contract is signed.
On the HVAC, proper design and installation seems to be a lot more important than system type or brand (within reason).
I used 1 inch XPS on my last home. If I had it to do over (and based on what I know now), I would use EPS or, if available, reclaimed foam. But I can understand not wanting to do a product swap. It's a PITA for the builder and an added cost to the budget.
The temperature issues with polyiso aren’t as severe as some articles imply. At some point I’ll probably write a new article with data to back it up, and I have designed the test rig but don’t have time to build it, although I do have the components! Hopefully soon. Maybe over the winter.
Anyway, if you already have the XPS I would use it. Note that if you’d used zip-R, they use polyiso with their panels. Using zip under the XPS might be a bit of overkill, but it won’t hurt and zip is a good product. For the air tight drywall, there is a really good article on GBA showing where you need to use sealant for this. I have used polyurethane caulk for the sealant, some use acoustical sealant. Acoustical sealant is messy to work with, and stays messy permanently. Polyurethane caulk is tough, stretchy, and lots less messy after it cures. You’ll need to be sure to detail all your wall penetrations/openings carefully with airtight drywall — which usually means careful detailing of electrical boxes.
You don’t need spray foam here. Sprayfoam is great for certain niche applications (unvented roofs, rim joists, a few other things), but is rarely needed in walls as walls allow other air sealing methods to achieve similar results.
Bill