One Chicago building envelope system

Thank you all GBA participants who have help educate me on the latest building science and green solutions. I’ve used quite a lot of this forums past and present posts to make informed decisions on my upcoming rehab project. I have 20 years experience in renovations but this is my first whole house design/build attempting to apply sustainable principles to one of my projects. My last project was in 2005.
For this project, I have hired an energy modeler to run scenarios and for now the design is showing a LEED Gold home with a mini-split system (renewable energy source) with a total BTUh of under 30,000 with this house system.
Chicago (Zone 5) gut rehab of an 1896 8 inch wythe masonry three story rowhome in Lincoln Park. First level is 13″ below grade and 8′ ceiling. 2nd level 11 ft and 3rd 10 ft. Flat roof. Located (abutting) the El tracks. Seeking LEED certification. Total footprint 750sf per level.
The systems:
Heat?Cool: 5 separate Mitsubishi Hyper-Heat pump units and installation of radiant heat tubing in the basement. Future PV panels.
Windows: standard tilt & turn vinyl window with 1/4″ lami over 3/16″ low-e U-value 0.25
FLOOR: slab on grade with radiant heat off dual water heater/boiler (any suggestions on this solution?) I’ve been looking at the GE Hybrid but it is not a radiant floor solution and water heater. R10 rigid insulation under 5″ slab with edge insulation. Note sure yet on final flooring (polished concrete sounds expensive). Cork?
WALLS: 3.5″ Open Cell Insulation . Lot of research and time went into this details including Roxul, Blown cellulose and an attempt not to over-insulate and have condensation and freeze issues of moisture in the wall cavity.
CEILING: 6″ OC on roof deck and none on attic deck given the energy model and ROI on blown insulation is over 40 year return on the money spent to install attic deck. One GBA article mentioned the annual savings of attic insulation would be $350 (in that home) vs roof deck insulation but I am thinking of only applying it on roof deck. Not closed cell because of cost. I do have some concern about the roof deck being OC so would appreciate your input. I think IRC recommends at least R21 to deal with condensation / moisture related issues in our climate for an unvented attic SPF insulation so that is what we will apply.
Lots of other variables of course but looking for input on the general building envelope solutions I have planned on my project.
Thanks for any and all thoughts.
GBA Detail Library
A collection of one thousand construction details organized by climate and house part
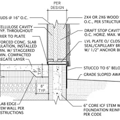
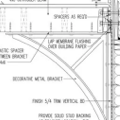
Replies
Jim,
1. Cork flooring is a poor choice over a radiant-heated slab. You don't want to install R-value above your radiant floor.
2. I'm not a fan of radiant floor heating. Your R-10 insulation under the slab is probably OK if you skip the tubing and heat your bottom floor differently, but if you insist on in-floor hydronic tubing, I suggest that you increase the R-value of your sub-slab insulation to R-20. You definitely can't use a heat-pump water heater for space heating, since the heat-pump water heater takes its heat from your room air.
3. Insulating an old multi-wythe brick building is tricky. Most experts recommend using closed-cell spray foam for this location, not open-cell spray foam. To learn more, see Insulating Old Brick Buildings.
4. I think it's crazy to do a gut-rehab in Chicago and install only R-20 or R-22 roof insulation. That doesn't even meet code. In Zone 5, the code calls for a minimum of R-38; installing more than the code minimum would be good. I'm guessing that your building has a low-slope roof; I may be wrong, of course. But if it does, you might want to read this article: Insulating Low-Slope Residential Roofs.
Thanks Martin. Appreciate the feedback. A few comments or inputs from my end.
Yes the system is designed to not require a radiant floor hydronic system however I felt it may be wise to add the tubing at this point since it would be harder later. At the moment there will be no active hydronic radiant floor. The heat pump heater wouldn't be in the same room so could draw from the room air.
1& 2. Cork on slab seemed a good solution (without radiant floors) vs wood or carpet. Still not sure there.
3. The article you reference is the main point of reference for the design. At first I didn't want to overinsulate to avoid the freeze/thaw and I was particulary avoiding spray foam (especially closed cell). I did not want to trap moisture in a significantly temperature reduced interstitial wall cavity and have the moisture freeze in the masonry wall and push outward. The open cell solution seemed to allow moisture to move through that system while provide thermal and air control.
4. Yes it is a flat roof slow pitch. I felt the same originally about focusing on the R value and was concerned this solution (R21) may not be adequate however this model is a prescriptive approach vs performance approach. If I wanted the performance I would add at least R50 to the roof deck (or attic) to reach performance numbers. So I ran a modeling scenario looking at the air sealing and thermal performance for an R50 (loose blown attic deck insulation and R21 roof deck OC) vs on the R21 roof deck. In the end the energy cost savings for the R50 were only $45/year savings. The additional costs for the blown insulation would be around $2000 so that ROI is a 44 year return. The code will allow the lower R21 on the roof as long as the performance model shows it meets the minimums which it more than does. I found this very interesting and I am beginning to drink the kool aid on this (assuming our construction performance matches the modeling).
Yes I 've read that low slope roof article too (very good article) as well as this one
https://www.greenbuildingadvisor.com/community/forum/green-building-techniques/25180/flat-roof-insulation-question-no-2
I have a 5 year plan (since there is still 5 years left on the rubber roof) to tear off and possibly add a 2" rigid to the top of my deck (as suggesting in your flat roof insulation article 2 above) which would alleviate my concerns for condensation getting in to the OC application. Then too I hope to add PVs to the home and go more renewable primary energy source.
Jim,
If I were insulating the walls of an older brick building, I would think twice before concluding that I had a better idea than building scientist John Straube. This is risky territory, and not a good place to improvise or wing it.
Freeze/thaw damage happens during cold weather, of course, when the direction of the vapor drive is from the humid interior to the dry exterior. If you use closed-cell foam, you limit the vapor drive during the winter. If you use open-cell foam, you'll be allowing more of the interior moisture to reach the bricks.
Five mini-splits to manage 2250' of conditioned space isn't a solution to anything other than the installer's boat payments.
Unless the room/zone has an individual design heat or cooling load of at least 5000BTU/hr it shouldn't have it's own head/cassette. (Splitting the output of mini-duct casettes can often reduce the total count.) Get the room by room, zone by zone heat loads down, and be aggressive on the Manual-J parameters- undersizing is a much lesser sin than oversizing. The very smallest ductless heads are ~7KBTU cooling, and would deliver 8K heating at Chicagoland's 0-5F 99% outside design temps. The smallest one-off mini-splits are ~9KBTU/hr and deliver over ~11KBTU/hr @ +5F. Unless you sleep with the windows open there's no way you'll ever need the 65,000BTU/hr of heating, or 45,000 BTU/hr of cooling implied by five 3/4 ton mini-splits (but it may be half that.)
R10 sub-slab insulation makes sense if you're not heating the slag in a US climate zone 5 location with 50F subsoil temps. If it's a radiant slab R15 would make more sense.
Open cell foam on a brick wall is risky to the interior finish wall if you intend to air condition. Between the dew/rain absorbed moisture and the sometimes higher-than-room temp summertime outdoor dew points you will have periods of extreme exterior moisture drive intensity, especially on the sun-drenched sides. If you have big enough overhangs to limit rain-wetting of the brick you'd do better with cellulose, right up against the brick, with a "smart" vapor retarder on the interior side to limit wintertime moisture migration into the cold side of the cellulose. Unlike open cell foam, cellulose can help manage large swings in moisture drives, adsorbing & releasing it without loss of function. With open cell foam most of the summertime moisture will end up either soaking the foam, or the gypsum (or both.)
Insulating brick in zone 5 isn't nearly as risky as it can be in zones 6 or higher, but that's not to say that it's zero or very low risk any where north of the Mason-Dixon.
If you insist on doing the walls in foam, the semi-open ~2lb foams from Icycene are a much better solution than anybody's half-pount foam. The MD-R-200 has a vapor permeance of about 1.2 @ 3.5", the slightly denser MD-R-210 runs about 0.8 perms @ 3.5", either of which is sufficient vapor retardency to limit both summer & wintertime drives from creating issues, and can't load up with moisture on it's own unless submerged. It's considerably more expensive than 3.5" of half-pound foam though.
Whatever you do, a studwall that penetrates the foam and contacts the masonry would be serious risk. Finger-joined 1x3s (for flatness) turned sideways on the 2x2 stud plates to that you get a full 2" of foam between the masonry on a 3.5" and would be better from both a moisture & thermal performance point of view. (In fact, 2" of the 2lb foam on it's own will has a comparable "whole-wall" R value to 3.5" of open cell foam between full depth studs at a 20% framing fraction.) If you went with the gypsum 3.5" away from the masonry on a turned-stud studwall with 2" of 2lb foam you'd be comparable to code min studwall performance even without factoring in the distributed mass effect of the 8" of brick (which will lower your peak heating/cooling loads a bit.)
Thanks Martin, you wrote "I would think twice before concluding that I had a better idea than building scientist John Straube. This is risky territory, and not a good place to improvise or wing it." Yes I agree it would be foolish not to consider Mr Straube's guidance however he admits the final solution depends on each particular property and building and detailing. I am trying to balance advice (everyone it seems has the 'correct' solution) and come to a solution that makes the most sense with the least risks based on past performance. I have read close cell can cause problems in exterior wall assemblies. I have two local industry experts who have claimed using similar OC solutions (or as Dana more accurately describes it as a semi-open cell) for over 10+ years without trouble in similar applications. I've told them both I don't want my home to be an experiment as you suggest ('wing it"). So I am taking all advice and science into consideration including of course yours.
A smart vapor would help in an OC solution, which has been suggested in terms of moisture management in winter or summer. Closed cell is still an option but I've read it can cause moisture to be trapped (on either side) not allowing winter (or summer) moisture to be managed and of course it is more expensive however that is not the main issue in the end.
Dana your thought about using blown cellulose was for a long time the front runner solution until I started modeling the air performance of blown (vs sprayed) and that is when I went back to considering spray. It is significant. Our solution is a 2# spray (not the 0.5#) but I don't have data on the perm rating right now.
We have an M series Mitsubishi Hyper model (to continue running to 15 below zero) and that model does not allow split systems off one supply. To your point we do have a few areas over 5K per area
We have the follow as some of the higher heat load areas:
Lower living space : 5716 (Btuh) + Bed 3 (lower) 2019 - hvac contractor sized on 12k unit on this level. Perhaps we revisit that one as a 9k unit
main living space; 6667 + 586 +3114 and he sized two 9K units on this level for distribution purposes. Perhaps one 12k would work there.
Upper beds we have two units in each bedroom location (one feeds two beds). Over sized (9k each) however they only use what they need so I don't think one unit on the bedroom level makes sense from a comfort standpoint.
Baths will have electric floor heat or alternate heat to offset cool spots.
Thanks too for the detailing on exterior wall design. I was thinking of using either 2x wood or metal 1 5/8" stud to avoid any thermal transfer and fill the entire stud cavity with the foam, however the flat wall approach you describe is great too.
I'm not sure how well your modeling data on air tightness jives with measured reality. Air-tight gypsum and/or detailing of smart vapor retarders as air barriers works pretty well. The air-retardency of even 2.5lb cellulose is sufficient to prevent loss of performance due to convection- we're talking a third or fourth order effect here.
Who other than Icycene has a 2lb semi-open cell, and what is it's vapor permeance (and blowing agent==???)
There are people in my neighborhood (similar outside design temps as yours, temps hit negative double digits maybe once or twice in 20 years) heating comfortably with 2 & 3 heat Mitsubishi multi-splits.
A 3/4 ton unit is about right for the Lower Living space zone- you'll have some margin, but not ridiculous oversizing. A 1-ton would do more cycling than modulating there.
The main living space could probably be handled by a single 1-ton mini-duct cassette and some short duct runs if you need the distribution, and it would run more efficiently than a pair of 3/4 ton heads, either of which could would nearly cover the whole load on their own.
Without the whole floor plan it's hard to say for sure how to break out the bedroom zones. Radiant cove heaters controlled by both thermostat and occupancy sensor work pretty well for getting some room-to-room temp balance on doored- off rooms otherwise served by a head in an adjacent common area, big enough to handle the whole load when the bedroom doors are open.
I stand corrected on the foam rating. Architect has spec'd Agribalance 0.75lb OC on the walls and Sealection 500 0.5lb on the roof deck. I believe both wall and roof deck show vapor barriers. Smart on walls and vb on ceiling. The Agribalance has a 4.95 perm rating at 5" and I only have 3.5" spec'd now. The Sealaction shows 6.33 at 3.5" with 6" shown. http://www.demilecusa.com/tech-library/building-science
So if I understand this correctly the moisture permeability would be less with a closed cell (Martin/Straube). In the winter where moisture is driving towards the outside it would be better than the more permeable OC foam so it doesn't hit the bricks and freeze. The risk of moisture coming inward is lower than outward (winter). The reverse is true in the summer where moisture trying to get inside (or out) would not permeate a closed cell as much as open and there would be a reduced risk of moisture (and mold). That is confusing since it seems more permeable may be better. Blown insulation would work well because it can manage the moisture as well (retain it and then release) and still work as a thermal barrier. OC works but not as well in summer and in winter and if moisture levels rise it could pose mold issues. This is very interesting. Are there case studies that show OC problems or articles? It contradicts what my local experts are telling me (not that I am surprised).
One thing for sure. Everyone's opinion is the correct one (even though they are all different).
Dana, interesting comments about your neighborhood using only 2 or 3 mini-split units. I would love to achieve that. I could 'test' it with only one on each level and can always add more later however I would have to convince the hvac contractor and most importantly the city inspectors that we modify the plans, however anecdotal stories or experiences won't work in Chicago (unless I go the old school route of greasing the wheels but I wont go there).
Yes denser foam is lower-permeance, and 5 perms is still pretty high- too high IMHO. HFC blown 2lb foam is on the order of 1 perm @ 1", give or take 20%. The water blown ~2lb foams from Icynene are about 2-3x higher permeance than the HFC blown foam at any given thickness.
With high-permeance foam when the outdoor dew points are in the high 70s and the room temp is in the mid-70s you can get high moisture content in the gypsum on any side of the house, and if it persists the foam will soak some up too, since the interior paint (~2-5 perms) is slowing the drying to the air-conditioned interior, and the foam isn't slowing the moisture delivery from the brick by nearly as much.
On the sunny side of the house dew or rain wetted brick heating up in the sun creates intermittent but HUGE vapor drives (independently of the outdoor air's dew point) - conceivably to the point of interior side finish paint failure if the permeance of the foam + vapor retarder is 2x that of the paint, which it could be. Smart vapor retarders switch to a highly vapor-open state as the RH of the entrained air nearest it goes over 70%, which it would be in that scenario, making the paint the lowest permeance layer in the stackup. If you get the foam down to the sub-2-perm range you'll be fine- the paint would then always have a drying rate equal to or faster than what the foam could deliver.
If you have sufficient eave & rake overhangs to limit the amount of rain-wetting of the brick you'll probably be fine with 0.7lb or 0.5lb Demilec, even with it's limited moisture buffering capacity. About a foot of overhang for every story works pretty well in my neighborhood, not sure if that would also be true in Chicago. (It's probably not enough in windy coastal areas.)
Option to not put a heat emitter in every room can be a really tough sell, even when it's the right way to go. It's often discouraged by lending institutions, and even prohibited by code in some locations- code implemented back when balloon framing sans insulation was common, and central heating was becoming established practice as the US /Canada/northern Europe was moving away from point-source heating. But even at current code-min construction the comfort hit from going to point-source heating is often quite small, and in homes with better-than code R with low glazing fractions and higher performance windows the dictum for explicit heat sources in every room for the vanishingly small room loads makes even less sense.
Case in point- I currently live in a ~2400' 1920s 1.5 story bungalow that has been modified to a fairly open floor plan (compared to it's original incarnation), and after retrofitting the 2x 4 walls with cellulose and fixing the most egregious air leaks I can heat the place comfortably at the +5F outside design temp with just the wood stove in the living room and the radiant floor in the family-room addition that has way too much window. Convection heats the upstairs, the bathroom and other bedroom are low-load due to limited window & exterior wall area, the kitchen/pantry and dining areas have large open archways for good contiguous air with the living room where the wood stove is. I could easily heat the place with a 2.5 ton multi-split and 2 heads (or separate 3/4 ton + 1.5-2-ton mini-split) and maybe 300-500 watts of radiant cove for the master bedroom to keep it comfortable with the door closed when it was 5F or colder outside). It's way sub-code for window performance and R-values too. I've yet to use the fossil-burner for anything but the family room this season, and usually don't unless I run out of wood (which sometimes happens due to limited storage area, since I live in the city. I can't stockpile more than 1.5 months of wood at a time.) With better windows and higher-R walls it could all be scaled down too.
Thanks to all of your advice and experience I've made great progress and advances to my design. The heating contractor is revisiting the initial design outlined above. His primary concern has always been that the hyper mini-split models have no evidence of modeling at the lower numbers which have been published (so there is a study a building scientist can put on their to-do list), In this case Mitsubushi has no public data available for the varying approaching and below zero days but we are assuming based on their cut sheets and essentially 40-50% reduced output load. So, my 42k system just dropped to 21k on the coldest day but the home needs 30k and the several hundred dollars extra may be worth the protection. Although I am pushing for removing an entire unit so that will push to over $1k in savings.
The insulation contractor is agreeing with much of what you outlined above but still believes the OC does work at a significant savings over OC. He pointed to this Straube article which frankly I feel supports more of both of your positions about moisture drives and air permeability although this summary comment does contradict your previous assertions that OC is not a viable option (assuming humidity controls are in order):
"Open cell (1/2 pound per cubic foot density) foam can control diffusion in climates that are not too cold (eg less than 4500 HDD18) when the interior winter RH level is controlled by appropriate ventilation to below about 40%RH. Open cell foam does not have sufficient vapor control for use in very cold climates (4500 HDD and more) unless the interior winter- time RH is strictly controlled (to below about 30%RH)." ~ Straube
http://www.buildingscience.com/documents/reports/rr-0912-spray-polyurethane-foam-need-for-vapor-retarders-in-above-grade-walls
This article suggests and indoor Rh of 40% which my hvac contractor does not believe to be possible with the spec'd minis in our summer. He recommends a separate system for the whole house which in the end would cost more than the added cost of spraying a 2# closed cell foam (for my house only around $1300 more in cost assuming I would not have to spray closed on a demising (party) wall or on the rood deck. I may add 2" rigid above deck and just do the tearoff this season. The great thing about my home is it has a shared demising wall and the rear is a common stairwell in back so there are really only two exterior sides - the south facade (35 feet) and the east (20 feet).
Dana to your recommendations and 'ifs' on eaves and insulation options - this building has no eaves. 38 feet of vertical brick on south and east- newly tuckpointed/rebuilt and sealed with good drip edges on the new limestone sills. Demising on north and west sides. A pretty perfectly sited property (although 15 feet to the south is a 40 foot building so solar gain and massing opps are gone).