Old home renovations and unique insulation
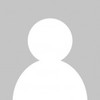
Hello all, Jake here. Zone 5, Central PA. A couple of questions.
I’m doing a bathroom and utility room renovation (second floor and first floor, separately) on a 120 or so year old farmhouse that we just purchased. As well as myriad paint, flooring etc. throughout.
As part of our improvements, we’re trying to be efficiency conscious as well as respect this old house! I intend to retrofit the original wood windows with Conservation Technology gaskets to improve air envelope, and we’re considering myriad insulation projects. Closed cell foam is coming soon for the basement rim band (I believe this should be acceptable from a vapor standpoint?), and sorting out whether the attic has appropriate ventilation after which we may put down additional blown cellulose (there is a few inches already) and batts.
As we’ve been doing demolition, I’ve stumbled across something unique and am trying to determine how to proceed. The home is traditional stick-built, but in between most of the studs in the house are solid blocks of 3-inch wood, with braided rope in between. (see image) It looks like this was an early attempt at securing the air envelope and insulating? In doing my bathroom and utility room, since the studs are exposed, I’m trying to decide how to better insulate? If I tear these out, what should I use so that I don’t have moisture problems (one space IS a bathroom).
The blocks are somewhat loose, but this must have been an incredibly time-consuming process. Before lathe and plaster, too! Beyond this (exterior of the building) is standard wood clapboard, and aluminum siding beyond that.
Photo is behind the 70s era kitchen backsplash, now gone.
GBA Detail Library
A collection of one thousand construction details organized by climate and house part
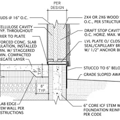
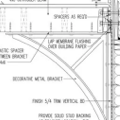
Replies
At 3" most northeastern softwood species would run about R3.5. Adding an inch of HFO blown closed cell foam would bring that to north of R10 (total) and would air seal fairly well. At about 1 perm @ 1" the closed cell foam would protect the wood from interior side moisture drives, yet still offer a reasonable rate of seasonal drying toward the interior.
If the whole house is built that way it would be easier/better to insulate from the exterior when re-siding. The inherently back-ventilated aluminum siding gives the assembly a lot of protective drying capacity toward the exterior and would probably last forever, but to upgrade the overall performance to near current code minimums would require some amount of exterior insulation.
Is there any flashing on those original windows?
Any storm windows? A low-E exterior storm window over a reasonably tight wood sash antique performs remarkably close to current code-minimum, and would also protect the antique sashes from bulk water & exterior moisture drives, all at a fraction of the cost of replacement windows.
Thanks Dana. Yes, there are pretty good storm windows! That's part of the reason I'm inclined to protect/restore what's there.
I think at this point I'm just going to pull down this blocking in the two rooms we've already gutted and have 2-3 inches of closed cell done. Vapor, draft, and quality R-value.
The rest of the house will probably remain as-is, and we'll focus on the attic after this.
>I think at this point I'm just going to pull down this blocking in the two rooms we've already gutted and have 2-3 inches of closed cell done. Vapor, draft, and quality R-value.
If you're going to all the trouble to remove the blocking, a full fill of OPEN CELL foam and "vapor barrier latex" primer or a "smart" vapor retarder is a much greener, higher performance, and less expensive approach. At 4" (the depth of a full-dimension 2x4 stuc bay) half pound open cell foam uses only as much polymer as 1" of closed cell, and center-cavity R of about R15, which is more than 2" of HFO blown closed cell foam.
See:
https://materialspalette.org/wp-content/uploads/2018/08/CSMP-Insulation_090919-01.png
But the real performance improvement is that the R-value of the thermally bridging framing has been doubled by being twice the depth, cutting the framing losses in half:
https://www.finehomebuilding.com/membership/pdf/184243/021269086NRGnerd.pdf
In zone 5 the great drying capacity of the inherently back-ventilated aluminum siding means it wouldn't really need an interior side vapor retarder tighter than standard interior latex paint on gypsum to meet the IRC code directives in chapter 7 under the "Vented cladding over wood structural panels." exception:
https://up.codes/viewer/washington/irc-2015/chapter/7/wall-covering#R702.7.1
(The very definition of "vented cladding" in the IRC refers to vinyl & aluminum siding, but would also include rainscreened siding of other types.)
But vapor barrier primer or 2-mil nylon (Certainteed MemBrain) is cheap insurance, at less than 20 cents per square foot (often less than 15 cents), which is WAY cheaper than an inch of closed cell foam.
At 4" of depth half pound open cell foam usually costs slightly less than 1" of HFO blown closed cell foam, slightly more than 1" of the climate-damaging HFC blown closed cell foam, and WAY less than 2" of any closed cell foam.