Energy Retrofit: Wrapping Exterior in ThermalTight Insulation

I live in the old farmhouse in central Vermont, climate zone 6A, that I grew up in. The house predates the town’s building records so our best guess is that the oldest sections were built in the 1840’s based on newspapers found in the walls dated 1848. At least thats when they got around to insulating. It has roughly 2×4 walls (no dimensional lumber to speak of) that had fiberglass batts and a poly air/vapor barrier added behind the sheet rock in the 70’s or 80’s. There is also an addition built in ’91 with 2×6 walls also with fiberglass batts and a layer of poly.
I’ve been slowly attempting an energy retrofit for the house. To summarize, so far we have added bathroom fans and plastic on the dirt parts of the basement to manage ventilation and moisture. Also external air for the wood stove, our sole source of heat. Then rigid spray foam to the basement walls as well as the 5-8″ between the living space and the underside of the roof. My long term goal is to be airsealed and insulated well enough to install heatpumps that could heat the house without costing a fortune.
Next up the siding needs to be replaced (currently its some junky, falling apart, press board like material). That creates the opportunity to add exterior rigid insulation. Last year I replaced a few windows and experimented with Thermal Bucks to build the windows out in preparation for rigid insulation. This summer BRINC the Thermal Buck company gave me some sheets of their new product ThermalTight to use on my covered porch. ThermalTight is neopor rigid insulation with an attached water/air/vapor barrier that overlaps for easy seam sealing. It was easy to install and if its not cost prohibitive I would like to use it on the rest of the house.
I know minimum rigid insulation in zone 6 for 2×4 walls is 7.5 and 11.25 for 2×6 walls (thank you Martin Holladay greenbuildingadvisor.com/article/calculating-the-minimum-thickness-of-rigid-foam-sheathing). The thickest ThermalTight board they make standard is R-11 (2 1/8″). Thats plenty for the 2×4 walls but what about the 2×6 walls? Martin also writes (greenbuildingadvisor.com/article/rethinking-the-rules-on-minimum-foam-thickness) that maybe there is some more flexibility especially when there is no air conditioning and the poly behind the sheetrock might actually help.
How much should I worry about being R-0.25 under the recommendations for my zone? Does the vapor permeability of Neopor help? Are there other things I need to think about?
Finally to air sealing. I’ve been considering taping over the plastic cap nails that hold in the rigid insulation. Would that help much? I will also be attaching furring strips over the rigid insulation and also I think all the nails holding the siding in place will go through the furring strips and puncture the rigid insulation’s air barrier. Would something like 3M All Weather Flashing Tape 8067 behind the furring strips maintain the air barrier in any significant way?
Thanks for reading my whole post. I hope I gave enough information. Big picture are there things I seem to be missing and need to consider?
GBA Detail Library
A collection of one thousand construction details organized by climate and house part
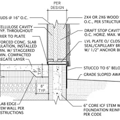
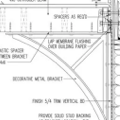
Replies
I brought up the same issue with the people at ThermoTight and they suggested they might be able to make it thicker to achieve the 11.25. We're using Rockwool though so I didn't pursue it. I would ask them. Seems like it would be better for them if their standard offering met the code.
You can add about R1 using the 1/4" thick fanfold type XPS insulation. That's a quick and easy way to get up to the minimum R value you want. A much more elegant solution is if the manufacturer can make you a custom run of their product that is slightly thicker. BTW, I think it's pretty awesome they would even offer to do something like that for you!
Bill
The minimum often referred to here is for a wall with a class III vapor barrier (ie painted drywall). In zone 5, you can go with less exterior rigid insulation provided you have at least a class II vapor barrier. Since you have the poly, you will be fine.
2x6 walls with only R5+poly is a very common assembly around me (Toronto) and it works fine. Since this limits the drying capacity of the wall, you need to pay extra attention to flashing details around windows and doors. This is especially the case for older buildings.
I have ThermalTight on my exterior which is a 2x4 framed home. I cant remember exactly but i think mine is 2.5" thick plus the strapping on top to mount my siding to it.
I'm sure John and his crew over at thermalbuck will be able to make what you need. I cant say enough about the positive experience from them as a company. From the delivery driver to sales, to John actually coming out to help installation and explain all that is needed and supplying my project with misc items to complete it.
Make sure the "junky, falling apart, press board like material" in your siding doesn't contain asbestos. It doesn't sound like it -- asbestos siding is usually more like a thin layer of concrete -- but you want to be sure. You can get it tested online for a few bucks.
Thanks everyone. I did talk to John at Thermal Buck and they can custom make an size though I worry about the cost.
Fortunately the siding was put on in 91 so I don't think it could have asbestos in it. Plus I think asbestos would perform better. If this gets wet at all it puffs up then falls apart like it was glued together cellulose.
>"Fortunately the siding was put on in 91 so I don't think it could have asbestos in it. Plus I think asbestos would perform better. If this gets wet at all it puffs up then falls apart like it was glued together cellulose."
That sounds like some kind of fiberboard siding, so probably a mostly wood product. Fiber cement also swells and comes apart if it gets wet, but it takes more severe wetting to damage fiber cement than it does to damage the wood fiber products.
Bill
For what it is worth, I found what I believe to be my optimum solution for a Climate Zone 5B DIY retrofit to be Type IX expanded polystyrene from a local "expander" who sliced it into the thicknesses I wanted. I am doing one layer at 1" and 1 layer at 2", staggering the seams. I do not need to differentiate between the 2" EPS going over my basement floor vs. the 2" EPS going on the outside of the walls. I am limited to 3" total non-nailable thickness by the circle I have painted myself into through the acquisition of Artisan plank siding. There is no polyethylene in the walls, and for this I am thankful.
The cool thing about EPS (also true for XPS, and I am using some reclaimed XPS) is its increasing R value with decreasing temperature. On a cold winter's night the foam will approach R15 and the wood sheathing will drop to about 38ºF.
Solitex Mento 3000 WRB covers the foam, and both foam and WRB are held in place by actual 1"x2.5" SYP furring secured with 7-in. broad headed screws. We are removing and reusing the 3-1/2" screws and washers used for temporarily securing the foam.
If our installation of the WRB, flashing and the balance of air sealing (most was done with along with attic insulation) is successful, I'll be bragging about the results someday, and we'll have to put in mechanical ventilation.
We did put on rake extensions on the gables in conjunction with a simple tear off and re-roofing. We are replacing the existing windows (a mix of double glazed casement, double hung and single glazed double hung and hoppers with storms) with double glazed tilt-turn assemblies purporting a whole standard window R of 5.6. Someday we'll be in Climate Zone 4B and the thermal performance will be less critical.
We pursued this retrofit in part to leave a better house to the next owner, to learn first hand the challenges of the retrofit, and avoid prepping the machine grooved 16" cedar shingles (with 14" exposure) yet one more time for painting.