Off-site construction – SIPS
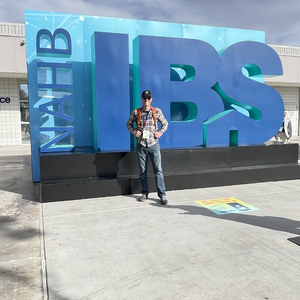
I have had a strong interest in off-site construction. Through the last 11 months I have been comparing site-built vs. off-site construction using volumetric modular and determined due to the delivery costs it made sense to shift to on-site construction which I will very likely execute in the same time frame.
Recently, I had watched a video that Matt Risinger posted regarding SIPS construction using Extreme Panel and it peaked my interest.
After looking into the costs again with SIPS the overall costs seemed to be a factor and since the house design didn’t allow the roof panels to work I again tabled the idea for this particular house.
Then in researching further I found a company that is local to my area called Eco Panels. This could align well and now I am thinking while not on this particular project maybe I am able to consider this in the future. I was able to meet the founder and he gave me a factory tour.
My question: From a green building point of view coupled with energy efficiency the difference between EPS and Spray foam…but, what Eco-Panels says is a proprietary blend of closed cell polyurethane foam created in part from a poly-alcohol derived from post process sugar-beets, what questions should I be asking or considering?
Is this marketing or is this a better version of foam?
This is from their website:
https://www.eco-panels.com/
Flame Retardant and Organic-Based Foam Core
We’ve never seen anyone else take a less than one-inch thick piece of insulation on their upturned palm and hold a 3,600° F torch on it for long periods of time like we can (please do not try this with your own insulation!). Our custom blend of closed cell polyurethane foam core is without peer for its structural and adhesive strength, thermal insulating ability and it is free of any formaldehyde, styrenes or VOCs, and rated with an ozone depleting potential (ODP) of zero and a global warming potential (GWP) of less than one. While most SIPs on the market use a urethane adhesive to bond the foam core to the siding materials, our injected foam itself is the only adhesive that bonds together all components of our building panels with a force of almost 50 lbs per square inch. That’s around 14,000 pounds of bonding force for every panel square foot! By comparison a typical stud frame wall system has only one hundred to two hundred pounds of bonding force per square foot with nails and sheathing. With our panels having a bonding force this strong, significantly fewer fasteners are needed to build a very strong home or structure.
GBA Detail Library
A collection of one thousand construction details organized by climate and house part
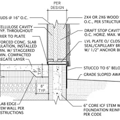
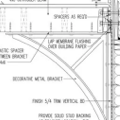
Replies
"Bio-derived" foam resin is almost entirely greenwashing. Typically a small percentage of the raw material is grown rather than extracted from petroleum, but not enough to make a significant difference.
My former employer used to take a handful of cellulose insulation, place a penny on top and melt the penny with a torch. It is impressive that they can do the same with foam; it just means that they are using a high percentage of flame retardant, and probably not the bio-friendly mineral borate that is used in good-quality cellulose and wood fiber.
"Zero ozone-depletion potential" is something foam manufacturers love to tout. It means they are following a law put into place over ten years ago.
By convention and not by fact or common sense, for some reason foam manufacturers don't include the carbon impact of anything except the blowing agent when reporting on global warming potential.
They are using hydrofluoroolefin (HFO) as a blowing agent, now industry standard for several years, which does have a low global warming potential when measured with conventional means, which among other things spreads the impact out over 100 years. We don't have 100 years to recover the damage done, and recent studies show that HFO may combine with other compounds to dwarf the impact of legacy, HFC blowing agents.
There are many advantages of using off-site construction. Using foam as the basis for offsite construction is a waste. There are many alternatives that use little to no foam or other climate-damaging materials.
Michael Maines it is clear from your response that you are perhaps not well informed on this subject. Since your response impugning my company may remain on this forum for many years to come, I must respond. If you delete your response to the question then perhaps it will delete my response trying to address your misinformation. As founder of the company Eco-Panels we very much reject your accusation of "greenwashing", but I believe the lack of informed comments in your response comes from simple ignorance (so I'm not really sure why you are the one that gets to be the judge of this).
Mentioning the fact that our custom blend of foam chemistry is largely based on post processed sugar beets - or sugar cane - is not greenwashing - it is a fact - whether you care to admit it or not. We specify this because there are people marketing "soy" or "soya" foams and we wish to differentiate ourselves from them. You are apparently not aware that was our intention. We believe "soy based" foams is greenwashing - the world is increasingly familiar with "soy" as a more renewable substitute for meat so therefor that must be a good thing for insulation? The experts in the refrigeration insulation industry - where our product originates - understood many years ago that soy foams did not have the structural and adhesive, flow or insulation properties suitable for making a great insulated panels like the poly-alcohols originating from sugar beet or sugar cane foams did.
More than one building scientist has noted that people should be building their homes more like walk-in coolers. They are in a sense noting that we should not be using 200 year old stud frame technology that was never even intended to provide a well insulated or energy efficient structure. At a time when the cost of maintaining the interior climate of homes has an increasing impact on global warming we should be looking to the industry that has been practicing climate control for 100 yrs, not the home building industry who only really started to do it in a widespread manner in my lifetime.
It's odd to me that you criticize our touting that our foam contains no ozone depleting compounds. We say this because for many many years people outside our industry accused us of having ozone depleting materials - which we do not and have not for several decades. Blowing agents are a complex and large industry and people apparently like you have ascribed negative attributes of other products to our own where they do not apply. So this is why we say it.
Now we have HFO as a blowing agent and you appear to criticize us for it. I've seen at least four different blowing agents in my years and HFO is the most environmentally friendly yet, and somehow this seems to offend your sensitive nature. Note we state the blowing agents GWP of less than one because THAT IS WHAT FOR ALMOST FORTY YEARS (you should research the Montreal Protocol) what the industry has gauged us against - the ODP and GWP of blowing agents. Are you not familiar with this? That is what we have been tracked against by architects and other well meaning professionals - not the LCA or EPD of the finished product - that is a far more recent development. People keep moving the goal posts - and we will keep trying to adapt. And for a small company these (LCA and EPD) are EXPENSIVE numbers to come by - only recently have there been "free" software tools on the market to enable their analysis - but just like a Manual J calculation they have severe limitations on their accuracy. We've paid for these reports only to find out for example that the extreme air sealing capabilities or reduced jobsite construction time and waste that our product inherently brings to the table is not even accounted for in the LCA comparative analysis by the company that we hired. In fact I don't know of any company doing an analysis that really recognizes all of the attributes that we bring to the table. I think because the stud framing industry does not want the comparative tools that will actually take all of this into consideration and shows all of their downsides. For example - the insurance industry recognizes moisture damage in structures as the single greatest on-going liability/risk of multi-family housing - even above fire - and this has significant negative effects even at the residential level even affecting the life of the home. Do you know any stud framer that GUARANTEES their wall systems will NEVER have mold form inside them? Do you know any LCA that recognizes the negative effects of moisture in the building envelope including on how traditional insulations in humid environments have decreased R values? I would love to have an LCA analysis take into account finishing a home at least a full month faster than with stud framing - but I've yet to see any positive impact associated with that taken into account.
Did you know that stud frame construction is the most complicated and weakest and least energy efficient method of construction allowed by law? And that's a conjunctive statement so please don't try to nit-pick - there is not another form of construction allowed in building code that has a higher cost to construct, that is weaker in structure and less efficiently insulated because where you have wooden members required for structure you can not have insulation and you very likely have created many opportunities for air leakage. You appear to want people to keep building with these 200 year old weakest and least energy efficient methods, though let's make them more complicated so they can perform better. I agree that the production of wooden studs does not have significant carbon impact relative to our foam products - but did you know that the negative environmental impacts of the long term ownership of a stud framed home with all of its thermal bridging FAR OUTWEIGHS any negative carbon impacts of the blowing agent or the manufacturing of the panels? BTW, blowing agents are not shown to "escape" from our panels over time, though that is a trope often wrought by a competing EPS foam industry - again based on misinformation, though some does escape from site applied spray foam in the application process - but that is not the same foam product nor the world that my company whom you accuse of greenwashing operates in. This again shows your ignorance.
Is it an affront to you that many stud framers that want to eliminate the thermal bridging of stud framing apply solid foam sheathing over the outside of the framed house - adding more materials, complexity of assembly (that if installed improperly can lead to long term degradation of structure) and cost just to try and catch up stud framing to be more energy efficient? We believe that strong and energy efficient wall systems should be more simple to assemble, often offering a lower total cost of ownership. We believe that a more simple assembly offers fewer opportunities for error in assembly - and fewer components that are stronger in nature offer a more durable product over the centuries (not just a few decades like stud framed homes are rated for).
I'm sorry if I come across as upset but you've slighted our company and our products and our good intentions with your own form of misinformation - it was dealing with trolls on GBA that led me to stop engaging directly with this forum long ago.
The best Yeti or Igloo coolers on the market are not made with stud framing - they are manufactured with closed cell polyurethane foam that imparts structural properties on the assembly. And everyone knows how durable they can be. If people are looking for a better way to build a stronger home - often for less money - we encourage them to reach out to Eco-Panels. Almost every year we see our owner builder clients building very strong and highly energy efficient homes COMPLETE for around $100-$150/sqft. Or you can keep paying increasingly expensive stud frame builders to frantically try to make more energy efficient a wood-framed structure that was never originally intended to be energy efficient.
User...575,
You would do better to refute the claims than simply make a series of assertions based on your opinions that start with "Did you know..."
If your foam is "largely based on post processed sugar beets - or sugar cane" rather than them making up what Michael described as a small percentage of the raw material, why not tell us how much of the total is bio-based, how much petroleum, and what their relative carbon footprints are?
Your screed seems to mix what you see as an attack on your proprietary company product, and on anyone who persists on using wood framing. I have some sympathy for the first - maybe you do make a better panel than most - but a number of us have reservations about SIPs as a construction method, and if you are looking for us to apologize for that you are in for a long wait.
Deleted
Thank you for the response. In a world with so much information and varying opinions forums like this are helpful.
You're welcome, and I agree! To be clear, I think foam is an amazing material; it can do things that other types of insulation simply can't do. I just consider it the precious resource that it is and use it only where needed, rather than indiscriminately just because it's easy.
In the Huntsman (Canada) closed cell foam HFO blowing agent foam - it states that it "contains 22% renewable soybean oil and recycled plastic".
https://huntsmanbuildingsolutions.com/en-CA/products/closed-cell-insulation/heatlok-soya-hfo
I don't know about eco-panel, but whether or not 22% is small or makes a significant difference I'm not sure, but it is in my opinion - encouraging ...
I agree that using 22% recycled or bio-based materials is probably a good thing. But the fact that Huntsman's EPD combines Heatlok and Heatlok Soya into a single analysis shows that the soy element doesn't change the GWP by much, if at all, or else they would have separated the them.
It's also a good example of a true GWP. While they claim a GWP of less than one, if you add up the GWP100, IPCC AR5, you get about 2.5 kg/CO2e for every 10.85 board feet (12"x12"x1").
It also assumes that only 24% of the blowing agent is off-gassed over a 75-year lifespan, and that the foam remains in place without change for that 75 years. Both may vary significantly.
https://huntsmanbuildingsolutions.com/en-CA/sites/en_ca/files/2021-07/Final%20-%20Hunstman%20-%20EPD%20-%20Heatlok%20HFO%20and%20Heatlok%20Soya%20HFO%20-%20ENG.pdf