Adding Exterior Roof Insulation to Commerical Building
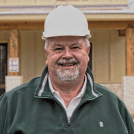
A friend has a commercial building in Scotia, NY with a full vaulted ceiling, built in the 70’s. The roof deck is 3×6 T&G Cedar planks with maybe 2” of some foam insulation and roof shingles. The T&G ceiling is exposed and would like to keep if possible.
He wants to reroof, so this is a good time to add insulation on top. In CZ5, it’s required to have R49 or R38 ci. Can 7.5” of rigid foam (or 6″ Thermax) with plywood sheathing be install safely into 3×6 deck? My gut tells me yes, since we don’t have to worry about drilling screws into rafters.
Would installing 2x4s on top of the foam to create a vented assembly be a gooder idear? Thanks, y’all.
GBA Detail Library
A collection of one thousand construction details organized by climate and house part
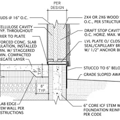
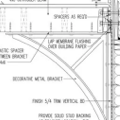
Replies
Armando,
Most rigid boards are anywhere from 1.5 to 2.0 lb/ft^3 densities, so you're talking around 1 lb/ft^2 at 8" thickness. Anything with 3x6 rafters should be able to handle the extra ~2.5 lb/ ft^2 that the foam, panel and 2x4 adds to the roof. The nice part of that is being able to screw into the deck instead of ensuring a rafter hit. That alone should make this job a fun one!
Given the snowfall, rain amounts, and temperatures I'd add the 2x4 channel myself.
If the overall depth isn't an issue, I would recommend using an insulation with lower environmental impact than rigid foam. On a similar project I designed a system of 2xs on edge and mineral wool to go above the roof deck. Cellulose would have been lower-impact but with the likelihood of rain on a given day here in the northeast it wasn't a safe option.
If you want to stick with rigid insulation, wood fiber board (Gutex or Steico) are easy to work with.
Assuming I can't talk you out of rigid foam, Thermax is a premium product with a premium price tag. It is apparently better than other polyiso at retaining its R-value when the temperature drops, but in most cases it would only be the outer portion of the foam that is cold so it might not have as large an effect as it would if there was only a thin layer of exterior foam.
To save money, you might be able to find recycled/reclaimed or factory second foam.
As for the vent channels, either way I'd use 5/4 or 2x furring to hold the foam in place and to attach the sheathing. On some projects I have left the gap between furring members open so the sheathing stays cold, with less risk of ice damming, and on other projects I have filled the gap to create a "hot" roof to keep the assembly as thin as possible. In snow country I think it's usually safer to provide ventilation.
I can tell you from experience that trying to hit every rafter perfectly is challenging, and when the interior framing will remain exposed I don't know that it would be possible unless the rafters are at least a nominal 4X in width. Generally speaking, fasteners should penetrate framing by at least 1 1/4", but with the screws used for this situation I would want at least 2" of penetration to provide adequate pullout resistance. With 3x roof sheathing you should be able to get 2" fastener penetration without any worries about shiners.
I agree with Kyle that the added weight shouldn't be a problem. Snow loads in Scotia (near Albany) are in the 40-60 psf range so an extra 1-2 psf shouldn't matter.
Michael,
With the coming of NGX, aren't all rigid foams now more or less OK in terms of GWP? I know there's still a lot of the old formulation of the Foamular XPS, but in a year or less it'll probably be drying up, or shipped to the states where it's not as restricted.
Kyle, no, as I post here every time I see someone promoting NGX--while the blowing agent in NGX is low-GWP, the overall climate impact of NGX is still one of the worst of any construction material we use. And no foam is off the hook--as part of the Pretty Good House approach, we say that it should never be necessary to use foam above grade, and to minimize how much you need below grade.
Michael,
Would you consider polyiso better than ngx in that regard?
There's a hard choice I see in that XPS really has no replacement in terms of compressive strength, permeability, and cost. Mineral wool is heavy, expensive, but well suited to subgrade/above grade, EPS is light, cheap, and OK above grade. PolyISO is light, cheap, and good above grade. In the span of 75 years, will the energy saved by the XPS offset its production? moreso if the production involves fossil fuels?
Kyle, I don't have the specific carbon numbers for NGX vs polyiso handy, but I have seen presentations by the embodied carbon gurus that show they are roughly equivalent in terms of emissions. I'd like to have a more specific answer and will work on that soon.
That said, I have not found a need to specify XPS (or NGX) once in the last ten years, over hundreds of projects. Almost all of my projects have tight budgets and have relatively conventional details compared to more avante-garge designs.
Below grade I typically use EPS; you can specify nearly any density and in the densities equivalent to readily-available XPS it has similar working characteristics. It does require a lead time to get it, but I find that the cost to buy and have it delivered are similar or less than purchasing XPS locally.
Above grade and inside basement foundations (when I can't talk clients out of them) I use polyiso.
I have tried in the past to figure out how to calculate an answer to your question, "will the energy saved by XPS offset its production." Because there are many equivalent alternatives, the answer is no. Using R-20 of XPS will never save energy (or more importantly, carbon emissions) over using R-20 of EPS, and certainly not over R-20 of cellulose or wood fiber.
Thank you both, gentlemen. I’m not used to installing so much insulation on top of a roof decking. This is a 300+ square roof on a full gable, and a very tight budget, so recycled polyiso is attractive, if needed. I’m not familiar with Rockwool and wood fiber insulation prices in NY, but we’ll check them out.
Usually I think of polyiso due to much better continuous insulation R-value/inch, so I don’t have to deal with long attachment issues nor thermal bridging, and on top of that, new formulations make polyiso with much lower GWP. I’m also happy we have 3x6 T&G decking, so no worries with missing framing members.
Mineral wool is a great choice, but pricing puts it out of reach, especially for an R38ci min., since I would need 12”-13”, plus 2xs, plus plywood, and that would take 17” screws min. With 6” thermax, plus 2xs, plus plywood, all I need is 10” screws min.
I would think wood fiver insulation is a good choice on a non-ventilated assembly in NY, but we want a ventilated assembly, and then again it appears to costs a lot more.
Apparently, they have a healthy colony of carpenter bees, so more than likely I’ll use a continuous metal screen at the roof bottom edge and ridge.
Stainless steel screen is good for critter proofing, and you can wrap it around the edge in the field, so you don't need to have something custom made to fit whatever thicknes your insulation ends up being. That way you don't end up with any gaps where critters can sneak in if you try to screen only the vent openings (assuming you put in vent channels, which I agree is probably helpful, even if I can't point to a specific "why").
Be sure to stagger seams. If you are concerned with the "less R in cold weather" issue, use a sheet or two of EPS in the outermost layers, since EPS R value slightly increases when cold, and it will keep the polyiso layers warmer to preserved their R per inch. Remember though that polyiso is usually only derated to around the rated R value of XPS, or EPS on the extreme end, so you while you lose R PER INCH, you don't really end up much, if any, worse off for total R value compared to what you would have had with EPS or XPS.
If you have a heavy roof, I'd run some extra long fasteners in at an upward angle into the roof from the outer sheathing layer or 2x4s if you're running those to create vent channels. Think of this the way a bar joist style truss is put together, trying to keep the fastener in tension instead of shear. This will help to limit the tendency of the assembly to want to "slide off" the roof with all the long fasteners in shear. I would recommend some fasteners like this along the lower edge, driven in so that they are roughly parallel to the ground. I see that as a little extra structural insurance. There are some BSC articles that talk about this too for thick rigid foam, although I think they were talking about walls in their article.
If you want to use reclaimed polyiso, I'd start hunting for that now. Supplies have been much tighter than they once were, which makes sourcing material a lot more difficult, and usually slower too. I have some vendors I've used in the past that have been completely cleaned out of reclaimed and even the "slightly irregular" factory seconds that they usually have, and they've been out of everything for several months now.
Bill
300+ square gable? That's beefy. How many square ft is this building? 25k?
Yes, its a large building with big overhangs, plus a big section with flat roof, but that's my forte.
Deleted