Not enough XPS over roof – should I vent?

I am in the Washington DC area – Zone 4. I just had a 1.5/12 single slope roof framed with 2×8’s for a 14×20 new block wall garage. On top of the rafters there is a layer of plywood followed by 2″ XPS rigid foam followed by another layer of plywood and then an ice and water shield across the entire roof. This week there will be a standing seam metal roof installed on top.
I think the foam is R-10 which is below the R-15 recommended for condensation control on the underside of the roof sheathing. I originally was planning not to vent the roof, so I was thinking that perhaps a couple inches of closed cell foam against the underside would be okay to fix the lack of enough foam on top (as i believe i would not be able put anything air-permeable against the underside). Is this a bad idea given the ice and water shield that covers the entire roof assembly since both top and bottom would have vapor barriers? Do i have no choice but to vent from soffit to soffit? Seems like i wasted the XPS if so. Thanks.
GBA Detail Library
A collection of one thousand construction details organized by climate and house part
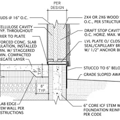
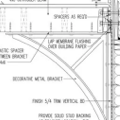
Replies
There are several questions here. The first question is: Do you plan to heat and cool this garage? If you do, the R-value of the roof assembly may matter. But if you aren't going to heat or cool the garage, the R-value really doesn't matter very much.
Assuming that this garage will be conditioned space -- heated in winter and perhaps cooled in the summer -- you want to aim for a roof assembly R-value of at least R-49, with at least R-15 of the total R-value in the form of air-impermeable foam insulation. (For more information on this topic, see Combining Exterior Rigid Foam With Fluffy Insulation.)
Since the rigid foam above the roof sheathing isn't thick enough, your best option at this point is to install R-5 of closed-cell spray foam on the underside of the roof sheathing. Then the rest of the needed insulation (R-34) -- probably in the form of a "fluffy" insulation like cellulose, mineral wool, or fiberglass -- can be installed in the interior side of the cured spray foam. This fluffy insulation needs to be in direct contact with the cured spray foam.
This assembly won't allow the roof sheathing to dry in either direction, but that's not too uncommon. It's your best option at this point. (There will be a little bit of inward drying possible, actually, but the drying rate will be quite slow.) Just make sure that the roof sheathing is dry on the day when the spray foam is installed.
-- Martin Holladay
Thank you very much! Yes, it will eventually be conditioned. I will leave it unvented and spray an inch or two of closed cell and then add mineral wool underneath that.
Most closed cell foam is about 1 perm @1" (give or take 0.2 perms), which is not a severe drying rate issue, but sufficiently low permeance to be protective of the roof deck from interior moisture drives, especially with the R8.4 (the fully depleted R-value of 2" XPS) above the roof deck. At 2" you're looking at a more severe half-perm. Stick with 1".
With R8.4 above the deck and R6 (1" of closed cell) below the roof deck you're already at the R15-ish needed for dew point control at the foam/fiber boundary for as much as R34 of interior fluff. But since you only have 6.25" of space left, that's going to be no more than ~R25 or so of high-density fiberglass (1.8lbs density Spider or Optima, L77 etc.). That's fine- it gives it plenty of dew point margin, and is almost (but not quite) up to code-min performance- close enough that it can be argued on a whole-house performance basis.
The total R at center cavity would only be ~R40, but with the above-deck R8.4 foam thermally breaking the rafters it's whole-assembly performance won't be much higher than the U0.026 code-maximum. Buying that performance back elsewhere (say, slightly better than code windows) would be cheaper and than adding more closed cell foam that would only lower the resilience of the assembly for a miniscule gain in whole-house performance.
Excellent, thank you. I will only have an inch of foam sprayed then.
Interestingly, a spray foam company came by to provide an estimate and told me they would only install 5.5" of open cell, not 1" of closed cell. They thought it was too risky to spray closed cell. Would open cell be an equal or better choice for the underside of my roof? Thanks.
5.5" of open cell foam (~R20) would be too vapor open (10+ perms) if you don't have the sufficient ratio of exterior R to total R.
But the R15 is based on R49 total- the ratio is about 30% exterior, 70% interior. If you're stopping at R20 with the open cell foam you'll be fine. The fully depleted R of the XPS is R8.4, for a total of R28.4, and a ratio of R8.4/R28.4= ~30%. (For the first decade or more it'll be a bit higher than 30%).
If you want to go higher than R20 on the interior right away, you need an inch or two of closed cell on the under side of the roof deck. It's not very risky- at 2" most 2lb polyurethane is still in the mid to upper range of class-II vapor retardency, not a true vapor barrier, but at 1" it's usually about 1-perm, give or take, which is just about right.
I suspect the real issue with the foam contractor is that 1" of closed cell runs about a buck a square foot, and 5.5" of open cell is roughly twice as much, and it takes about the same amount of time to install, and only slightly more polymer. They have to pay time for the crew & truck no matter what, and it's easier for them to make a living with the 5.5" of open cell than 1" of closed cell. Proposing 2" of closed cell might seem less risky to them. ;-)
Thanks for the quick response. I will see how the prices compare, but good to know that i can do 5.5" of open cell if i don't add any more insulation underneath.
After some more research and reflection, I have decided to avoid spray foam because i can't risk getting a bad installation. So i am going to cut and cobble 1.5" of EPS or XPS against the underside of the roof deck. i am leaning towards EPS for the better drying potential, but the thought of doing XPS is intriguing because i can use tape to help with gaps/seams which seems easier than foam/caulk.
I don't recommend the cut-and-cobble approach for unvented cathedral ceilings, because there have been several reports of failures (moisture accumulation and sheathing rot) in roof assemblies where this approach was attempted.
To learn more about those failures, see this article: Cut-and-Cobble Insulation.
-- Martin Holladay
Seriouisly, cut'n' cobbled foam is a waste of high $/R foam, and a risk to the roof deck. Venting the roof deck with an ample channel above a cavity-fill of fluff and CONTINOUS foam thermally breaking the rafters under the gypsum uses less foam, is higher performance at a lower cost, and has much lower moisture risk.
For low-pitch roofs a ~2" vent channel is more appropriate than the code-min 1", so R23 rock wool ( 5.5" nominal loft) with 2" of continuous polyiso on the interior (seams taped) would yield R35-ish at center cavity (discounting the exterior XPS to zero, even though it's actually doing some good), and would deliver an R12 thermal break over the rafters. With credit for the air films in the cavity and even half-credit the R value of the exterior foam it'll hit code performance on a U-factor basis, despite the vent channel being a thermal bypass.
I ended up having open-cell spray foam installed in the rafter bays and small knee-walls at the top of the block walls. I will eventually be framing a free-standing room (both walls and ceiling) to be covered with drywall. That will create a very small unvented attic space. I am planning to condition the room with a minisplit that heats and cools, but i have been reading about the importance of conditioning the attic space given the open-cell. Should i just get a dehumidifier to address the attic space? Otherwise since i will be using a minisplit with one indoor unit, it sounds like i would need to add vents in the drywall ceiling to exchange air with the attic. That doesn't seem ideal to me, especially because i thought it was not good to add heat to the underside of the roof in the winter due to ice dams. Thanks.
Not all open-cell foamed attics end up with moisture cycling issues. Monitor the humidity in the space, and remediate only if it's necessary. A room dehumidifier can handle the job just fine, and it's likely to be at most a springtime-only problem if treated that way.
Another approach would be small 20-30cfm fan that runs only during the cooling season. ( A Panasonic WhisperGreen at it's lowest ~3 watt setting would do it.) During the winter, don't run the fan, since that's when conditioned space air would have a dew point higher than the average roof deck temp, causing moisture to accumulate.
As long as there isn't a true vapor barrier between the conditioned space and the attic, the mini-split will provide some amount of vapor diffusion drying through latex paint on gypsum during the cooling season.
Thanks! I have a portable dehumidifier that I will use if needed.