Northwest rambler — Attic and crawl space refurbishing

My wife and I are purchasing a 3750 s.f. 1987 rambler in Duvall, WA, climate zone 4/Marine, 17F design temp. The 2015 data indicates 5,000 Heating Deg Days for Duvall. Electricity is $.10/kW. Heating/cooling is currently with a 36,000 BTU packaged unit heat pump supplemented by electric wall heaters.
This will be our forever home. The attic and crawl space are rodent infested, so all insulation and flex ducting to be removed and replaced. This is an opportunity to optimize those spaces. I have researched this site and BSC’s site for best retrofit practices. Here is what I think needs to be done, but looking for feedback on what I’m missing or over-doing.
My energy calculations using 50F delta T are:
Ceiling – 3877 BTU @R49, 3750sf
Windows – 9040 BTU @ R2.5 existing 1987 alum frame/double pane x 452sf.
Walls – 5158 BTU @ R19, 1924sf
Floor – 6333 BTU @ R30, 3750sf
Leakage -18468 BTU using Vol x 0.6 x dT x .018, 9ft ceilings x 3750
Duct loss- 2440 BTU using 10% of first items above
TOTAL – 45316 BTU
It seems clear that leakage should be minimized!
ATTIC
1. Fix breaches where rodents enter, remove insulation, clean up.
2. Seal all non-IC rated can lights to make airtight, replace with LED retrofit kits.
3. Seal all penetrations per BSC’s extensive guide, including chimney, pipes, electrical, etc.
4. Install blown in fiberglass to R-49, diminishing return if more than that.(?)
5. Seal and insulate attic door.
CRAWL SPACE
6. Rodent breaches fixed, remove insulation and ground cover, clean up.
7. Medium density polyurethane spray foam seal around rim joist
8. 6 Mil polyethylene ground cover, taped seams, sealed to foundation and piers
9. R30 unfaced insulation between floor beams
10. Replace damaged flexible air ducting with metal ductwork, insulate to R11.
Questions:
A. Am I missing anything or do you see any bad choices?
B. New vinyl windows don’t seem cost effective, agree?
C. BSC recommends converting crawl spaces to conditioned spaces (fully insulate perimeter, conditioned air entry, no outside air entry, etc.) and leaving floors un-insulated, except in one article it indicated this may not be appropriate for Zone 4/Marine. The approach is to prevent moist crawl spaces and associated pests, damp/rotting floor beams, etc. when moist air condenses on cold surfaces. At this point I could go either way, cost is appx the same. I want warm floors. Any recommendations or experience you can offer?
D. I wanted to retrofit hydronic floor heating since I really like warm floors, but the high cost will take 22 years to recover compared with getting a larger (properly sized) heat pump. I had hopes of using two Sanden heat pump hot water heaters for this, but cost is high, output currently about 14000 BTU at cold temps, but bigger/better unit is coming next year. Anyway, do you agree this is mainly a comfort decision and not an economic decision? Any experience with hydronic retrofits?
Thanks everyone, I look forward to your comments.
Ron
GBA Detail Library
A collection of one thousand construction details organized by climate and house part
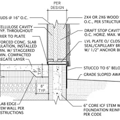
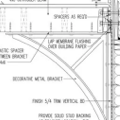
Replies
Your U-factors are all over the place. An R19 2x6 wall with 16" o.c. spacing and typical siding options comes in around U0.070 give or take with hemlock studs, U0.075 with doug-fir studs. Your numbers come up around U0.05, which would a be a "whole-wall-R" of about R19, when your actual would be under R15, R13-ish if the framing timber is douglas fir.
The floor loss estimate is probably overstated, unless the crawlspace is SUPER ventilated (like a pier foundation rather than walls.)
Low-E storm windows over low-performance clear glass double-panes often works out just fine, and is far cheaper than replacement windows.
In your climate a vented crawl space with a ground vapor retarder works. The outdoor dew point averages are below the deep subsoil temps even in summer, and well below the temperature of the bottom edges of the floor joists, unlike summer conditions in the eastern half of the US. Basically, despite being a rainy climate, you don't really have moist enough air for chronic condensation to occur in the crawlspace. A conditioned crawlspace works too, and that may be easier from a reliable air-sealing point of view. If the ducts are in the crawlspace you DEFINTELY want to take a sealed crawlspace approach.
You probably don't have sufficient height clearance to get R49 fiberglass in the attic over all the exterior walls (or any of them, if it's a hipped roof.)
Ronald,
Dana gave you good advice.
If the cost of a sealed, insulated crawl space is the same as ventilated crawl space, then you definitely want to go with the sealed insulated crawl space. To read GBA's recommendations on crawl spaces, see Building an Unvented Crawl Space.
If your house is well insulated and has low levels of air leakage, you won't get any comfort advantage from a hydronic system with in-floor heat. Such a system is expensive, and in a well insulated house, the floor will rarely be warm enough for you to even notice that the system is operating. For more information on this issue, see All About Radiant Floors.
Thank you Dana and Martin.
Dana -
a. I backed off my R-19 wall value to an R-15 whole wall value, more conservative.
b. Turns out the floor has 2x10 joists, so will be using R-38! Seems like overkill but need this to fill the space and avoid the void that could occur next to the subfloor if anything less were to be used.
c. Good tip on the storm windows, thanks!
d. The owner of the company doing the work said insulating the entire crawl space this size would be very expensive and the value questionable in our climate, more or less in agreement with what you said. They use JM Corbond III for spray applications, which they WILL be using around the rim joist and in the attic around the top plate area, can lights, etc.
e. the hipped roof is 4/12 pitch with 4 foot overhangs, so lots of room. Plus they'll be spray foaming around the top plate using R7, then installing baffles to keep the venting open.
Martin-
f. The ductwork does indeed run through the crawl space, but we'll be installing that ourselves and insulating to R11. My Son-in-law works for a major HVAC company and will be assisting.
g. Interesting point about the hydronic floor heat. Seems like it would be the most pleasant to be on when the building is poorly insulated. I'll still keep this in mind for my future shop!