Nominal R-value on plans

Hello,
On my draft plans they say “NOMINAL R-21 INSULATION AT WALLS”. This is not correct and needs to be updated to reflect R-23 cavity with R-10 exterior, rigid, XPS. Should I ask it to read…
Option 1 – “NOMINAL R-33 INSTULATION AT WALLS”
Option 2 – “NOMINAL R-23 CAVITY INSULATION AT WALLS AND R-10 RIGID AT EXTERIOR WALL”
Option 3 – ??
I’m working with a drafting company so, they need guidance.
thanks.
GBA Detail Library
A collection of one thousand construction details organized by climate and house part
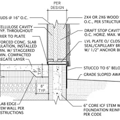
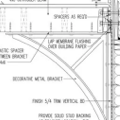
Replies
Option 1 is vague, if you want something specific you better specify it. But please don't use XPS, there are much greener options that will work equally well.
thanks ..._page. I definitely leaning toward specificity.
idahobuild,
The more specific you are, the less ambiguity or misunderstanding you will encounter later. The note, which forms part of your Outline Specifications, should call out the materials, their R-value, and where they are to be located.
Malcolm, so if I have the info. regarding the r-values in the detail drawing (see atch'd), then I should just delete the line or specify as in option 2? I am torn - one part of my brain likes to have the info in both places, but the other part says "that's just another place to correct/look".
idahobuild,
There is a hierarchy of which legally have primacy that generally goes:
- Specifications
- Details
- Other more general drawings.
If you don't have separate Outline Specifications, then yes the details govern, and I wouldn't call it out in more general terms elsewhere.
The standard AIA contract language is (paraphrasing here) "where a conflict exists between the drawings and the written specifications, the written specifications shall prevail". This just means the contract document (the written spec) takes priority over the drawings in case of a conflict. I have seen many a change order arise from this particular issue...
Anyway, I like your detail, but I'd probably put in callout on there referencing a page in the written spec that would read something like "R10 of exterior rigid insulation consisting of 2" thick XPS plus R23 mineral wool batts in all stud bays for a total nominal R value of R33 for the wall assembly". Being an engineer, I would also specify manufacturer's part numbers for the insulating materials I want used in the assembly. The more specific you are, the less chance someone deviates from your specified design. I would try to modify that detail so that as you read from the top down, you are working from the inside to the outside of the assembly on each side (or vice versa). If you skip around, so that each line doesn't represent each respective layer in sequence, it's too easy for people to read things incorrectly by mistake and build the assembly out of order.
I would also be sure to do a plan review with your contractors and your GC prior to building if you are planning to do anything outside of the norms for the trades in your area. Make sure everyone is on the same page, literally, for anything you need done a particular way.
BTW, make sure the revision numbers are prominently listed on every page of your drawings. I can't count how many times I've seen problems because one contractor on a project is working off of an older revision of a design.
One last note: in my work in critical facility design, we put a --==**LOT**==-- of effort (can't overemphasize this enough) into minimizing the chances for human error causing problems. In our case, those problems are usually "downtime", which means someone made a mistake that broke something so that some system stopped working. This is a Bad Thing (think "I called 911, but it just rings and rings and no one answers", etc.). When you are putting your designs together and making your drawings, try to make everything very clear and simple. Use space on the page, use extra pages, don't use fancy and confusing language. Make it EASY to understand WITHOUT the need to really think about it. This will help to avoid any errors that may well be honest mistakes on the part of your contractors. Clear drawings and clear descriptions go a long way to ensuring your project gets built the way you want without a lot of problems along the way.
Bill
Thanks. I think I'll pull those lines out.
The general rule of thumb is to only put information in 1 place in a set of drawings. If information is in 2 places, you risk that information becoming out of sync if you have to change it (and things always change).
Like every rule about drawing, there are many reasons that you may choose to break this rule, but it's a good place to start.
A common way to do it (and the way I do it), is that on your plans you tag your walls with wall types, e.g. "WT1", "WT2", "WT3", etc., then you have an assemblies sheet that has a section view of each wall type and labels every layer. This way you can be extremely detailed about how the wall is constructed, but you only have to draw/write that information once.