New spray foam contractor is getting conflicted information. I want to do the right thing.

Good Evening. I joined GBA to ask this specific question but I’ll stick around as I believe it’s a good resource.
Climate zone: 6B
TLDR: 3 bidders + myself (last bidder). Owner wants to fully insulate 40x50x18 shop envelope with SPF.
2 installers want to put 3″ closed cell SPF on the underside of a 5/12 pitch roof while 1 wants to put 2″. 2/3 are reputable contractors in our area and say that’s sufficient. – Is it truly?
My background: EIFS and plaster/stucco 8 years with my Pop who is a hard a$$, making me a 5th generation plasterer. I want to do my Pop proud since he loves this trade (mostly to avoid getting lecture of why I’m wrong) so I try hard to retain most of what I pick up. Most of the construction knowledge I have is specific to my trade, so outside of that, I’m am generally inexperienced. Though I am gaining traction on SPF.
My Pop and I have started a new business in the SPF industry (to feed us during the stucco off season) and we found out that a friend of ours was preparing to insulate his 40x50x18 (LxWxH) isolated shop.
Half of that he’s converting into an apartment. Shop on left side, and renting out the apartment which is above its own garage on right.
Before we came along he obtained 3 bids to SPF the envelope.
The focus here is adequate insulation in the roof.
2 bidders say 3″ of CCSPF (r-21 ya?) is enough R factor in the 5/12 pitch rafter bays while 1 bidder says 2″ is enough. That’s it, nothing else for the lid.
My own battle is this:
My accumulated knowledge, plus the manufacturers of our SPF say 7″ of CCSPF = r49. Our regions building codes say all envelope hats must be r49.
My Pops says that 3 other bidders who say 2-3″ is fine, can’t be wrong. (our friend shared the estimates with us to help us out)
These estimators either are just going with what the shop owner wants (he’s got money but also a cheap skate, think Ebenezer Scrooge.) , or seem to have the homeowner convinced he only needs 2-3″ of foam up there. 3 bidders can’t be wrong, right?
I want to give the shop owner what he wants, but I also want to give him what he NEEDS.
Can someone tell me how 2-3″ of CCSPF = R49 or equivalent?
GBA Detail Library
A collection of one thousand construction details organized by climate and house part
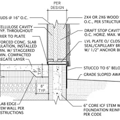
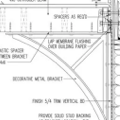
Replies
Can someone tell you how 2-3″ of CCSPF = R49 equivalent? No, nobody can, because it's not. There was just a story about that in one of the blogs here:
https://www.greenbuildingadvisor.com/article/misleading-energy-reports-used-to-sell-spray-foam
Now do you need R49? To meet code, you do. Do you need it to stay warm? If youre local code enforcement is lax, you do have the option to spend a lot of money on heating, both on buying heating equipment and on buying fuel, and use less insulation. But you won't be as comfortable, and you will spend more money overall, over time. So it's a good idea to go with at least the code requirement.
Thanks for the response Charlie, as well as the link.
I feel I should add, just in case I missed or misunderstood something, half of this building will be a living space and the other half will not be. I'm guessing they do but I have to ask, do codes change depending on occupancy?
Joshua,
The energy code applies to all buildings except for certain "low-energy" buildings. Essentially those are buildings that are either in a super-moderate climate, or those that will NEVER be heated or cooled. As soon as you throw in HVAC, you need to insulate and air seal, even for a shop that will only be "occasionally" conditioned.
Oh, this is news to me! I've always assumed with no reason to think otherwise that the building code only applied to liveable spaces.
My workshop is a former horse barn and, as such, doesn't have a lick of insulation. If I were to install a mini-split, it would be foolish of me to not install some insulation, as well... but are we saying here that the addition of a mini-split in my barn would now require the barn to be insulated to code?
Is this a wood framed roof with rafters/trusses? Have you considered flash and batt to up the R?https://www.greenbuildingadvisor.com/article/flash-and-batt-insulation
Joshua,
I think some closed cell would be good for air sealing the living space to protect the occupants from the garage. That would mean also looking at the garage ceiling. (It's a safety and comfort issue.)
Is the shop directly connected to the living space as well?
+1 on flash-and-batt. It will have lower heating/cooling costs and can meet code. But other than these issues, 3" will work.
Joshua, as Peter noted above, if the space is heated (and/or cooled) it should meet building code requirements. You could probably call the shop "garage" and get away with less insulation, but the half of the building that is living space should meet residential requirements. If the roof insulation extends all the way over the top plates, you can reduce it to R-38.
Closed cell foam may be R-7/in when brand new (or, technically, carefully aged for six months) but as air displaces the blowing agents in the cells over time, it will get closer to R-5.6/in, the insulating value of dead air. Code enforcement only cares about the tested R-value but as the occupant or installer you should consider the aged value as well.
With that in mind, 2" will eventually be about R-11 and 3" will eventually be about R-17. You would need at least 5.5" to meet code requirements, assuming the insulation extends across the entire top plate, or 7" if it does not. Or as others have mentioned you could use a flash-and-batt system; just make sure at least 50% of R-value (aged) is in the foam.
I have to mention blowing agents--you may or may not be aware of the climate impact of using closed cell foam. The HFC blowing agents in conventional foam are potent, persistent greenhouse gasses, 1000 times worse than CO2. Every manufacturer now offers an HFO-blown foam, which has about 1/4 the total carbon emissions (and therefor the climate impact) of conventional foam. It costs a little more to buy, but from what I've heard it's easier to install so it averages out.
There are/were some spray foam people that claimed that since spray foam typically makes for excellent air sealing, less R value of spray foam would perform the same as more R value of some other type of insulation (like batts or blown insulation). While in a sense there is probably some truth to that, it doesn't meet code: code specifies a minimum required R value, period -- there is no allowance for variations in air sealing.
Basically this means that those contractors are incorrect, if code requires R49, then you have to apply R49 worth of spray foam using whatever R per inch the manufacturer specifies for the particular spray foam product you're using.
Note that you don't necassarily have to use all closed cell though. You can use enough closed cell to ensure good vapor performance for your climate zone, then finish the rest off with cheaper open cell spray foam, or even batts. In that case, the total R value becomes the sum of the rated R values for both types of insulation materials you're using and you can meet code that way.
Bill
My opinion spray foam is not green and large scale use in new construction is a big red flag for lazy planning and that the planner has little or no concern for lowering the cost of the job.
In new construction nothing costs more per square foot for its R value than spray foam.
My wild guess is all the TV shows are getting spray foam at very reduced cost and so they are using a lot of it giving the public the impression that it is the best thing since sliced bread.
If you must have sloped ceiling put sheet foam on the outside and then the roof, it will cost less and work better. Note used foam can be had at an even lower cost.
Walta
Spray foam's "advantage" in normal construction is that it's a bandaid for otherwise sloppy detailing -- spray foam basically ensures good air sealing even with an unskilled crew, and "fixes" otherwise sloppy air sealing. There are better ways to do that though, using regular sealant and other things applied properly and in the right places.
Spray foam, in my view, is a niche product, very good in a few spots where nothing else is really an option (such as stone basement walls and unvented cathedral ceilings). In walls and attic floors, spray foam's real advantages are wasted, and you end up spending more money without really getting a lot of benefit.
I think a lot of the TV shows are essentially marketing for building products. I've seen a lot of bad advice, and sometimes outright code violations, given by the people on those shows too. I see those shows as a good way to see what certain design ideas might look like without spending your own money to try them yourself, but I sure wouldn't trust any construction information I heard on those shows!
Bill
Tyler, Yes. Wood frame with rafter trusses. I have not considered flash and batt.
Steve, Yes, it's directly connected. They share a partition wall.
Michael, good point. I'll suggest the flash and batt to the homeowner.
When I went to bid this, I had the homeowners needs in mind. The shared wall from the apartment to the garage, I suggested to be a sound dampening material (roxul, rockwool, comfortbatt) with a vapor barrier. As well as the ceiling to be loose fill R-49. None of the other contractors considered this and wanted to spray everywhere. 1 guy did suggest flash and batt but nothing about sound dampening.
My only concern is that I want this to meed code requirements and for the client to be happy. But since he's a penny pincher, I don't know if he'll want to pay for it to be done the best way I know how. And hopefully that's the right way.