Insulating During Re-Siding Project

Hi All,
This is a great site!
I have a house in Ontario that’s looking to be re-sided. The climate zone is Zone 5 USDA. The windows will be replaced at the same time. Currently, the exterior siding is pine board and the house is about 16 years old. I’m considering two options from two separate contractors.
Option 1.
1. Remove existing pine siding down to OSB.
2. Install 0.5″ poly iso insulation.
3. Install hardie board.
Option 2.
1. Install 0.5″ poly iso insulation.
2. Install Sagiper PVC.
Questions.
A. Because the house has a limited roof overhang, there isn’t space for anything more than 0.5″ of insulation. So in this case would I be better off skipping the insulation altogether?
B. Would you recommend removing the existing siding?
One contractor says that it looks to be in good condition and can be a substrate for the new siding. There is no evidence of damage on the outside or inside of the house. He’ll know more when he installs the new windows.
There is a small drip on the two end windows in horizontal wind-driven rain between the vinyl frame and the jamb extension. No detectible rot on the jambs. Dry wall is nice and clean without staining.
The trim on the windows was removed and looked dry, with the original tuck tape. I also pulled the carpet back from the wall and the OSB subfloor is dry.
GBA Detail Library
A collection of one thousand construction details organized by climate and house part
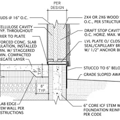
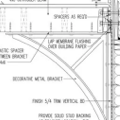
Replies
I’d install 2” of polyiso foam, and definitely a rain screen under the siding.
For such a small area, I'm not sure if rigid makes enough difference to matter. Being a production home, your effort is probably best spent fixing the WRB and flashing details as these tend to be pretty sloppy. About the only extra would be to include rain screen strapping or a textured WRB to improve drying capacity. This will make a big difference on the durability of the siding finish. While the WRB is being fixed, I would also tape the seams of the OSB underneath to help a bit with air sealing.
If you do want to go with foam, 1/2" is not enough. Too little to warm the sheathing enough and also limits the drying potential of the wall. You want about 3/4" of polyiso or ~1 1/4" of EPS/GPS/XPS. Unfaced foam or permeable polyiso is always the better option.
Thank you so much Akos and Bob.
From reading through this site, I was definitely concerned that 0.5" of insulation would limit the drying potential of the wall. I think I'll follow your advice and skip the foam and focus on the WRB.
Do you have any concerns with the contractor's proposal of using the existing pine board as a substrate for the new cladding?
He would remove some of the trim pieces to make it flat. He could then wrap it with a textured WRB. The same contractor is also doing the windows at the same time, so I assume he could integrate the textured WRB into the rough opening of the window. The new windows would be EnergyStar Vinyl windows and would use low expansion foam insulation around the rough opening.
He would then install heavy gage PVC siding (i.e. SAGIPER) over the house wrap.
Is this a good approach?
If the pineboard is in good shape and it is flat, there are no problems keeping it.
Removing the trim is most of the work. Taking the rest off is pretty quick after that. Not sure keeping the siding is worth it.
Once you are down to bare OSB, you can see if there are any issues that need to be dealt with and gives you a chance to tape the seams of your sheathing for a better air seal.
Vinyl siding is self venting, you can skip the drainable WRB and use regular house wrap. Butting the siding up to the brick mold on the window makes for a pretty clean install.
Thanks Akos. Super advice! Glad I found this site :)
Yes, the pine board is in good condition. I've done the following:
1. Check behind the existing window trim. Drywall is in good shape. No mold or moisture.
2. Checked under the baseboard. No moisture.
3. Removed outlet plates. I can see the vapour barrier behind the gang box and can see pink fibreglass insulation.
4. Existing pine board is tight against the house. No crumbling or loose pieces. Pine board is solid.
5. Inspected garage door framing directly under the pine boards. No mold. Drywall in garage is firm.
5. No musty or moldy smells.
Is there anything else I should be looking for? What are the odds there is rotten OSB without any outward signs or symptoms?
In general, I'm trying to be green and re-use the existing siding if possible :)
I would love any tips to identify any problems with the sheathing.
Generally with this type of siding the water damage will be behind the horizontal trim pieces. If you are lucky, the only thing keeping water out is a bead of caulk, lot of times it is just paint.
This is the area I would check especially by the windows. Depending on how well it was detailed and how good the house wrap is, the OSB could have seen some water. Unless it was a lot of water, you won't see it on the inside of the walls.
In your case the pineboard is only there as an extra backer for the new siding. I don't think this counts as reuse, only saves a bit of time removing it.
I would consider adding blown-in cellulose from the outside.
What kind of windows are you going to install and why are they being replaced? Storm windows can be an economical alternative.
It is not clear what you current siding is. Changing siding and/or windows requires that the window opening on the outside and/or inside may need to be reworked if you want to avoid the look of a hack job.
Thanks Jonathan.
The exisiting siding is pine board. The new siding would be either PVC or hardie board.
The new windows would be EnergyStar rated vinyl windows.
The current windows are 16 years old. Over time the vinyl frame has separated from the pine jamb inside. When there is extreme, wind-driven rain, there is a small drip in this gap. I've only seen this once in 12 years during a storm with 90 km/h winds throwing sheets of rain against the house. During normal, heavy rainfall there is no drip.
The same contractor would be replacing the windows and siding at the same time, so it shouldn't be a hack job, since he can prepare the rough opening and ensure the window fits properly.
One contractor says he will install a vinyl window with a brick mold and the PVC siding will lock in behind the brick mould.