New roof – critique wanted
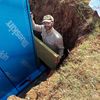
Hi All,
Apologies for the long-winded post! I am going to be placing a new roof on my parents house, and I’d like a double check on a few items, while I still have plenty of influence on the design. This will likely be the last roof either of them see before the home is passed to myself or sibling, or sold. Cost is a concern, but quality install and materials can take precedence, as there will be no labor costs associated with the project, other than my/others time.
The gable roof is 4:12, sheathed with 1″x12″ boards during construction in 1982. The current roof (2nd) is in its final stages, with some leaks in long straight lines developing somewhat uniformly over the whole house. The roof has vented soffits, with vents on the gable ends instead of ridge. The state of the insulation is unknown, with no direct access to the attic space – this is a 2nd story addition to a previously ranch floor plan. The house is in climate zone 4, but very close to the border of zone 5.
Plan for the roof:
1. Strip roof to original planks
2. Install a new layer of 7/16″ OSB sheathing (a)
3. Seal the seams with 3M 90 adhesive and ZIP tape
4. Two strips of 36″ Grace Select I&W Shield from the eaves and rake
5. New drip edge on the perimeter, new flashing around chimney
6. GAF Feltbuster synthetic underlayment (b)
7. GAF Starter shingle course
8. GAF Timberline HDZ arch. shingles (c)
9. GAF Cobra ridge vent
10. GAF Timbertex ridge cap
Plan for the attic:
1. Remove any water damaged insulation (d)
2. Install rafter vents, if not present
3. Air seal around fixtures and other obvious leaks
4. Install a bathroom ventilation fan with insulated ducting to roof
5. Add blow-in insulation to achieve something around R50
6. Block existing gable vents
Questions:
(a) I’m assuming the existing planks have shrunk in their width, creating gaps that allow the long straight leak lines to develop. Combined with the multitude of existing nail holes, I’ve planned to create a new, flat, sealed surface with the OSB. Is this a reasonable design goal? Also, should a 3″ fastener be used, or is a regular 2-1/2″ ring shank sufficient?
(b) The roof isn’t considered low slope, but is on the edge. Is a standard overlap sufficient, or should I follow the low slope advice and perform a half overlap on the underlayment for extra protection? Should I cap nail only to the new layer of OSB sheathing?
(c) Should I strive to nail through both layers of sheathing material? If so, that would require a 1-1/2″ nail. Otherwise, will a 1″ or 1-1/4″ nail be sufficient? Will bounce be a concern between the layers of dissimilar material?
(d) Being that the type, condition, and quantity of insulation is unknown, should I be prepared to remove all of the insulation if necessary, and start from scratch? Any other gotchas on houses from this era?
Thanks,
Kyle
Attached: supporting pictures
GBA Detail Library
A collection of one thousand construction details organized by climate and house part
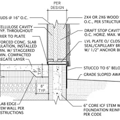
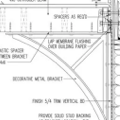
Replies
Kyle,
4:12 for new asphalt is standard, not low slope, and I sure wouldn't sweat any fancy underlayment details. Flashing details, though, are critical.
Unless they're badly water damaged, adding a layer of OSB over the existing planks seems like a waste of money in a vented attic. In any case, the ZIP tape is not necessary. This is not a place you need to establish an air barrier, and if you're concerned about the gaps or previous nail holes, you have the option of simply using a few more nails. Air sealing the ceiling after removing insulation--now that's the winner here.
It's hard to tell from your pics where the water damage is. A main area of concern is the top of your exterior wall plates--that constricted area where the truss "heel" or the rafter bird's mouth is--and you haven't mentioned improving that. Since you're stripping the roof, it might be super convenient to pull off the 1x12's in this location and get all the air sealing details from above, then put it back together and ensure good vent flow from the soffit while maximizing insulation.
Andy,
You raise a good point. 4:12 isn't low, but the roof sees a considerable amount of snow, that was my initial reasoning for the double band if I&W. My main concern about the original sheathing is having a course of shingles who's nail line just perfectly straddles a gap between two boards, being forced to either nail above the nail line (warranty issues), or shifting the course around, and throwing off the look. I wish I knew for certain. As a backup, I've used a 4% tangential shrinkage factor for the boards in case they weren't fully cured when installed, and even butted tight that leaves a possibility for a 1/2" gap between adjacent boards. I'll admit, I've helped on a lot of roofs, but only on new construction where everything's in ideal shape, and plywood or OSB is used. Is there a maximum recommended gap between planks for shingles in general? If it's a non-issue then less worry for me.
Do you think the synthetic underlayment is overkill? I can understand the thoughts on the ZIP tape not being needed - I was hoping for an extra layer of security on water tightness than for the air sealing. The damage, as you suspected, is near the wall top plates in most instances. Many of the water marks are 2-3 ft in from them, those are smaller, and generally in the same place as identifiable missing shingles. I do like the idea of pulling up the boards for ease of access near that area, it sure would make it easier to work around in there!
Kyle,
If you typically have lots of snow, the BEST thing you can do to keep snowmelt out of your house is to prevent warmth from squeezing out through the ceiling into the attic, particularly at the exterior wall top plates. A strip or two of peel&stick is fine for eaves and valleys for those times when outside conditions generate ice dams, but you've got this golden opportunity now to address the envelope deficiency. First air seal, then insulate.
As for the OSB, save your money. Yup, you'll encounter a row now and then where all your nails go into a gap. Don't shift the shingles, just nail an inch higher on that row. Unless you're in Miami-Dade County, this is not a problem. Any underlayment is fine under asphalt shingles; the manufacturer wants something there.
Andy,
Extremely grateful for your input!
Kyle