New outbuilding, mold, crawl space encapsulation/ventilation plan

I’m building a 190sf art studio/office in Zone 5B (Central Oregon, drier/sunnier eastern side of Cascade range, sandy/volcanic ash soil, 24″ frost line, ground freezes here). It has a one-year-old vented crawl space that developed mold beneath the plywood subfloor and I-joists. It sat with no roof and no ground moisture barrier through last year’s snowy winter. Last Spring, I scrubbed the mold off with diluted bleach and spread 6mil poly over the ground, but did not attach the poly to the stem wall or seal up the vents.
A year later, it’s closed in, unoccupied, un-insulated, no drywall, foundation still vented. Mold has re-appeared in the crawl space, and also seeing some on the above floor studs, interior OSB wall sheathing, and a little above on the TJI rafters. I assume my moisture problem is due to the ground, the stem walls themselves, and the four foundation vents. No rain leaks as I can still see all the framing. Crawl space currently averages 35° with 65% RH. Outside, it’s 45° and 30% RH. Moisture meter reads 15-18%.
Interior plans:
Walls – R21 faced fg batts.
Cathedral ceiling – R30 unfaced fg batts with air-sealed site-built 2″ ventilation channel (have bird block vents and full ridge vent).
Floor – Was to be fg batts in the joists but, if I’m on the right track, I should change that to XPS/EPS on the interior foundation stem wall and also cut and cobbled into the rim joist.
Drywall – Airtight method.
HVAC – No plans for furnace/AC or HRV/ERV.
As this isn’t a house, I’m less concerned with R-value efficiency/human comfort as I am with affordably solving the moisture issues. Ideally I’ll be able to leave this building unattended, without constant conditioning, only heating with a space heater as needed when in-use. Rarely hot enough here to warrant AC, and it has plenty of operable windows. To exhaust oil painting art studio odors when I can’t open a window, I’ve planned a wall bath fan that exhausts directly out the 2×6 exterior wall (70 cfm, 0.1″ static pressure, DC motor rated for continuous use).
—
1) Seeing as this is not a dwelling, is it still recommended to encapsulate/condition the crawl space?
2) For crawl space ventilation without HVAC, would the sensible choice be a floor-mounted air register along with an exhaust fan positioned over one existing foundation vent? Would it have to run constantly even when the building is not in-use? Is this necessary?
3) Will the crawl space exhaust fan conflict with the painting odor bath exhaust fan?
4) How thick does the foundation interior foam need to be? R15? Same R-value in the rim joist, or bump up closer to walls/R20?
5) In cathedral ceiling, is it wise to add a vapor barrier (such as MemBrain) between drywall and unfaced batts?
—
After research over the last few months leading me here, I acknowledge my naivety and mistakes (went on a local builder friend’s old-fashioned advice of “houses need to breathe”). Building science is fascinating, thank you all for this great resource.
Thanks!
Kevin
GBA Detail Library
A collection of one thousand construction details organized by climate and house part
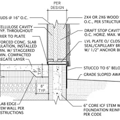
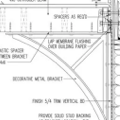
Replies
For the batts in the ceiling, rock wool or HD fiberglass is preferred for the higher air-retardency.
R30 is still below IECC 2015 minimums for commercial buildings (unless it's continuous insulation above the roof deck). If an HD38 aka "R38C" (C for cathedralized ceiling) fits in your rafters, use them. With 2x12 milled rafters an HD38 has an inch left over for ventilation gap, which is enough.
As long as the ceiling gypsum is reasonably air tight there is no need for a vapor retarder tighter than standard latex ceiling paint in your climate, even with just a code-min inch of roof deck venting.
Unless it's going to be covered with an ignition barrier, use Dow Thermax rather than polystryene for the stemwall insulation. Tape the cut bottom edge with foil tape, and lap the ground vapor retarder up the stemwall, between the foam & foundation.
R15 would be needed for code on the stemwall if it were residential, but it only needs to be half that to meet IECC for commercial buildings. See Table C402.1.3:
https://codes.iccsafe.org/public/document/IECC2015/chapter-4-ce-commercial-energy-efficiency
1.5" of polyiso runs about R10 which makes it with margin but you'd need 2" of EPS to hit IECC 2015 code min on the foundation walls.
Thanks, Dana. Do I need to be hitting commercial building code requirements? This is an outbuilding on rural residential property, small enough to not require a permit in my county. I am unclear of code requirements for such a building.
If I stay with R30 unfaced fg (already purchased) in the ceiling, am I risking moisture/condensation issues? Or will the building just not be as efficient?
Roof already finished with OSB sheathing, 15# felt, Ice/Water shield at eaves, composition asphalt shingles. I have 12" TJI rafters. I do have concerns with the two gable end rafter bays venting, as there are 2x4 lookouts up tight to the OSB, holding the rake overhangs. I was planning to detail the ventilation channels to swoop under these, either trimming away or just compressing the batts where those 2x4s are. At this point, I think this is my only option.
I read conflicting info on the ignition barrier somewhere saying it wasn't needed in a crawl space if under 36", which is about where mine is. What are my options here if I can't source the Dow Thermax?
Kevin
An outbuilding isn't like a residence, and the internal moisture sources & quantities will vary by use. If you're growing commercial weed you'll have a different moisture profile and energy use than if it's usually-unoccupied office, etc.
What you "need" is up to local code officials, and it sounds like that's fairly moot in your situation. The moisture risk to the roof deck doesn't change much with R-values over R25, but tends to be riskier with higher R (due to lower roof deck temps). But without internal moisture sources like 25 sweaty Bikram Yoga students the risk is pretty low.
Batts don't tend to fit I-joist rafters, since the widths are designed for 1.5" framing, not 0.5" I-joist webbing. You may need to do a fair amount of cutting & sculpting with a batt knife to get a decent fit.
If not Thermax, foil faced polyiso is still slower to ignite than polystyrene, and chars in place rather than melting into a puddle o' flamin' polymer. Requirements for ignition barriers are often amended in local codes (usually toward leniency- not sure what OR code says). But unless there's an ignition source down there the risk is small.
(edited for length) Thanks again for the help.
Locally, I can get Rmax Thermasheath-3. https://www.rmax.com/thermasheath-3/
Is this comparable to Dow Thermax?
Shouldn't the rim joist insulation be permeable enough to allow drying to the inside? (Do I need the ignition barrier there?)
Any feedback on my original exhaust fan questions above (2 and 3)? If code doesn't apply, is this still recommended?
Kevin,
To keep your crawl space dry, the first step is to pay close attention to exterior grading. Make sure that the soil around your building slopes away from the foundation on all four sides.
If you have any reason to believe that the roof water is contributing to crawl space moisture, install gutters at the eaves, along with conductor pipes to convey the roof water far from the foundation.
The next step is to seal the crawl space vents and do a good job with the air sealing and insulation details to create a conditioned crawl space. Here is a link to an article that tells you what to do: Building an Unvented Crawl Space.
Codes require (a) Thermax or (b) an ignition barrier to protect the rigid foam on the crawl space walls. Code interpretation varies widely. In your kind of building, in your rural area, you may choose to ignore this requirement. That said, if your family has any reason to be concerned with fire safety issues, find some Thermax or protect the foam with 1/2-inch drywall.
Codes also require that this type of crawl space have conditioned air or ventilation, but if I were you, I would just monitor the crawl space and see how it works before installing any fans. In a pinch, a portable dehumidifier, operated for just a few months to get things stable, might be all you need.
Good luck.