New low slope roof -> A Canadian told me to double strap, radiant barrier, vent and used exposed fastener.

What do you guys think about this? Zone 5, northern utah with two large shed roofs that face south. They are both 1.5:12 pitch and have HT underlayment on them now.
I’ve been planning on mechanical standing seam right on the deck, but wonder if this Canadian has a couple good points.
1. Why not run furring strips like a rainscreen to raise the metal off the osb deck? This air space would reduce ice damming, and dry out any water entry.
2. It would meet the requirement for using a radiant barrier, placed directly on the underlayment before the strapping is attached.
3. It would allow for the use of exposed fastener roofing which is way less expensive compared to mechanical standing seam.
4. It would let me use a dark roof color to help melt off the snow without having the heat enter the house as much.
GBA Detail Library
A collection of one thousand construction details organized by climate and house part
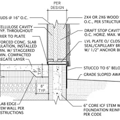
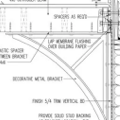
Replies
In most situations, a radiant barrier doesn't do anything that can't be accomplished with more insulation, so that alone isn't compelling. I'm not sure what your whole assembly in proposed to be in the two alternatives--it might help to say a little more.
Charlie,
It's TJI's with 3" of closed cell spray foam and will be filled with rock wool.
The main perk I see of keeping that space open is because I have more than enough R under the deck and foil alone would seem to keep an airspace to ensure any future leaks dry, but as Malcom pointed out maybe that is not optimum.
Mike,
I prefer metal roofing attached directly to the sheathing for a few reasons.
- Strapping solves a problem that it caused. The air-space accumulates moist air, which can condense. If you didn't have the air-space there would be no moist air to deal with.
- You have to provide intakes and outlets for the vent space, which complicates the detailing at the eaves and peak.
- It makes the roofing panels load-bearing, where before that function was done by the sheathing below - making them more susceptible to damage from walking on them and from debris.
I'm curious as to why having strapping influences whether you can use an exposed fastener roof or not?
The strapping might make sense if the roof below was un-vented, but not with an impermeable roofing underlayment.
Thanks Malcom. Excellent points, and I didn't think abut the load bearing or the cavity making moisture. On a Facebook metal roofing group they are adamant that exposed fasteners into osb is the worst possible option. Because the movement of the panel loosens the screw more so than when its into metal or wood. The problem I see with exposed fasteners that do not have strapping is that any leak in the fastener, which is inevitable would result in water being placed directly at the hole the screw made through the underlayment. Where if it's on a horizontal strap and leaks through you have a relatively sealed deck below to allow water to leave or dry.
This seemed informative on some of the benefits ..
https://www.youtube.com/watch?v=S2MvVmQLX7s
Careful installation of exposed screws and careful inspection every few years should be enough to ensure that screw-down roofing stays watertight.
If you get little enough precipitation that a screw-down roof is ok at a 1.5:12 pitch, you might consider using snap-lock roofing. It's only a little more challenging to install than screw-down but looks almost like traditional standing seam.
Mike,
I see your point about gasketed fasteners into sheathing. Given any choice at all I use snap-lock over exposed fasteners. It means the whole roof has the same long lifespan, as opposed to looking at periodic maintenance or replacement of screws every few years.
A bit of a sore point for me as several years ago I replaced over 3000 screws on our community hall roof, but I've admitted defeat and as we speak that roof is coming off and is being replaced by snap-lock panels.
Oof, that must have hurt! At my former place of employment we had a decent-sized shop in an older metal building, with a lot of nice new woodworking equipment inside. We discovered that there were many leaks in the roof but there wasn't money to do anything but inspect or replace every screw. Fortunately I didn't have to do the work.
Mike,
The usual advice is to up-size the screw diameter a bit when replacing them, but I found scores that had leaked long enough the strapping was rotten and wouldn't hold any fasteners.
Having a new roof will be a huge relief for me. The crew are all surfers from a nearby community. They stopped for an hour this morning so as not to disturb a yoga class, but rather than stand around they went and joined in. I'm having a good time watching rather than doing for a change.
Deleted
UtahMike,
Malcom is right about strapping. Even the double level version shown, which at least allows for downslope relief of condensation merely solves the problem air gapping creates. Plus with your very low slope, the magic air arrows Martin talks about won't help you any for venting purposes.
I strongly agree with the group opinions about OSB and face screwed panels, especially in your environment. I am in a similar location to you. Higher elevation, strong sunlight, dry, hot-cold extremes with daily temperature swings in the 30+ degree range. Metal panels expand and contract more than you might think in width and length. This movement works the screws in a small oscillation that over time works the screws loose. A combination of compression and heat seems to be what makes the OSB holes get loose over time. The heat and UV degrades the rubber washers which allows water to leak downward.
Like Michael, I would suggest going with snap lock IF you can get someone to warrant its use on your low pitch. The clips used to hold panels to the roof are protected from bulk water and more important the panels can move without dragging the clips around. It may be possible to source snap-lock style preformed panels with butyl seals in the rib gutter to further enhance resistance to ice dam back ups forcing water higher than the seam height. Even then the manufacturer may not warrant installation on a low pitch roof. Another advantage over locked seam roof panels is that snap-locks can be un snapped if you ever need to fix the roof. I have not heard of a method for un-seaming a mechanically locked roof.
Having lived in snow country for over a decade now, I disagree with many ideas posited about metal roof behavior. I will try to get some pics later now that we are under a major snow storm watch. A few more details about how you are handling over hangs would be helpful in advising about ice build up potential. I will note that the foam between TJI still leaves a path for heat loss to the roof that could have been better handled with exterior insulation. But that ship has sailed.
I have un-locked double-lock standing seams a few times. It's not easy and it's hard to impossible to do without causing some damage. Maybe pros have special tools to do it; I just have a little more than the average carpenter's amount of metalworking hand tools.
An upward-facing radiant barrier in a vented air space would likely be covered in dust before long, greatly reducing its effectiveness.
Metal roof fasteners will hold better in solid lumber, but I've put the strapping below the sheathing for more insulation space: rafters, 2x4 strapping, roof sheathing, underlayment, metal.
Unless you install exposed fastener roof, it would get a good washing every snow…
Exposed fastener roofing is industrial roofing. Keeps the rain out but who cares if there is a drip here or there? Well, your insulation and sheet rock might.
On a low pitch?
No thanks.
Some of this comes down to your local snow load. If you are in snow country with above 60lb, top venting is needed to limit snow melt especially on a low slope roof.
I'm not a roofer but I've installed both snaplock and exposed fastener metal roofs. If I look at purely at labor costs, the snaplock is much faster. Exposed fastener will be cheaper but also a slower install. Never mind the strapping underneath you are proposing. I know you can get snaplock for 2:12, there might be something out there for lower slope.
If you must have exposed fastener, I would use metal Z grits instead of wood. These would allow the panels to expand without putting as much load on the fasteners. The Z grits can be ordered perforated or slotted to allow for airflow.