New house with basement vapor barrier

We purchased a spec built home in zone 5A last spring (2018). The basement is unfinished. In our area its required in basements to build exterior studded walls, insulate, and install a vapor barrier. The installation is a mineral wool insulation and the vapor barrier is polyethylene sheeting. We’re wanting to finish the basement, but that polyethylene sheet seems wrong from a building science perspective. I’ve talked to a couple builders around here and they just blindly accept it as the way its done around here.
I’m not too excited about ripping it all out and installing XPS, or even spray foaming. Should I just rip down the PE sheet and drywall? Should I use something like Certainteed’s Membrain product? …or should I truly go through the time, expense, and hassle of starting completely over? (That would be major scope creep!)
GBA Detail Library
A collection of one thousand construction details organized by climate and house part
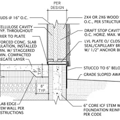
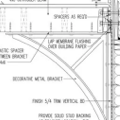
Replies
Hamm,
You're in a tough situation. The right approach is described in this article: "How to Insulate a Basement Wall."
In my opinion, it doesn't make sense to invest in finishes like drywall and flooring, with the idea that you will use your basement as finished space, without fixing the problems you describe. Doing it right costs money, but if you are finishing your basement, you're about to spend a lot of money no matter what you do.
If this were my house, I would put the polyethylene in a dumpster, and I would remove the mineral wool batts and offer them for sale, cheap, on Craigs List.
Your next step would be to either (a) insulate the stud bays with closed-cell spray foam, or (b) disassemble the stud wall, insulate the concrete with rigid foam, and re-assemble the stud wall, re-using as many of the same studs as possible.
If you aren't in a hurry, you could monitor a few different options for a year.
The IRC prescribes minimum R20 for basement studwalls in zone 5, or R15 minimum continuous insulation. Are your studs in fact 2x6 with R23 rock wool? If it's 2x4/R15 it doesn't even meet IRC code min!
3" reclaimed roofing polyiso runs about R17, usually costs less than a buck a square foot, and can be secured in place with 1x4 furring through-screwed to the foundation with 4.5"-5" masonry screws, hanging the wallboard on the furring. Tape the seams with housewrap tape, seal the top & bottom with can-foam (or 2lb spray polyurethane.) That takes up less interior space than a code-min 2x6 studwall, and only 1/4 " deeper than an underperforming 2x4 studwall. Leave the polyethylend or strip it- it doesn't really matter. Fiber faced sheet polyiso is a Class-II vapor retarder- it won't let in enough ground moisture in to interfere with latex paint or create mold conditions on paper-faced wallboard.
HI Hamm -
When you say, "it's required," do you mean by local code, local building code official, or "the local industry?" That can make a difference in your approach.
Do you know how your foundation was built? Exterior waterproofing vs dampproofing; perimeter footing drain system to daylight or sump; capillary break at footing/below-grade cold joint?
It's important to know how moisture managed your foundation is before you finish it, blocking access to changing moisture management.
How expensive it will be to correctly moisture manage your finished basement from the interior depends on how well they managed on the outside. Your builder took an approach on the exterior that was your only opportunity to get it right on the "easy" side and that affects your only opportunity to get it "right" on the inside.
Peter
I spoke to the inspector. He said its code per IECC to have a vapor barrier. Not sure if this is something they enforce locally or what.
Regarding how my foundation was constructed, I can only assume they built it per the prints I have. The print states:
Exterior:
-water proofing
-4" exterior drain tile (below 12" aggregate)
Interior:
-4" drain tile at inside perimeter take to sump basket
-2x4 furring @ 16" OC fill cavities w/R19 batt insulation
-1/2" Gyp Bd over 6mil vapor barrier
From what I can see, they deviated in two places.
1) There is no gypsum board.
2) Studs are 24" OC, not 16".