New home. Zone 6. Looking for wall construction advice

Hello all! Long time reader first time poster.
We are building a new home in western MT.
My first ideas up until recently were:
– LP board and batten siding
– ZIP sheathing on walls and roof
– 2×6 walls
-1″ spray foam
– stabilized cellulose remaining cavity
– 1/2″ drywall.
Recently I have been thinking of adding a 1/2″ polyiso in-between the ZIP and the 2x6s.
I have read about moisture issues with this? Would that be a concern with the spray foam?
My whole reason for wanting to add the polyiso is to reduce thermal bridging from the wall studs this improving the efficiency of the home.
Will be heated and cooled with a ground source heat pump.
We are on a budget as with any build. Adding 1/2″ polyiso only will add about $2200 to the bill. I fear if I go thicker I run into issues of window buck fitment problems, longer fasteners, and needing to fur out possibly? All adding expense.
What do you guys think?
GBA Detail Library
A collection of one thousand construction details organized by climate and house part
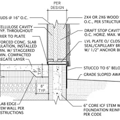
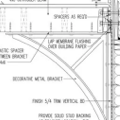
Replies
After some research it seems EPS would be a better choice for exterior insulation in my climate? Would I be better off foregoing the spray foam on the 2x6 cavity and spending that money on exterior insulation?
It seems to me in terms of cost you'd save money and get superior results by going with EPS, outboard of your structural sheathing and foregoing the spray foam in the stud bays. You'll need to balance the EPS to cellulose ratio for your climate. I think you're in zone 6, so that would be about 40% insulation outboard. More is better. IRC 2021 calls for R10 continuous and R13 in the stud bays. Insulfoam makes an EPS that is R-5 per inch. So you could achieve it in 2".
If you go the route of putting your insulation outside your sheathing you need to take some extra steps for your door and window penetrations. GBA has details for that, and there are lots of Q&A comments covering ways to do it.
You can fit R13 insulation in a 2x4 wall. If your home is single story you could frame it with 2x4 at 24" oc and save some money. If it's 2 stories you'll need to go to 16" oc. Put the savings into extra labor on air sealing.
Among foam insulations, closed cell spray foams are among the worst from an environmental perspective.
Here are some interesting wall comparisons:
2x4 framing @ 24" oc. R10 continous exterior insulation, R13 between studs. Whole wall insulation value is R-23.4
2x8 framing @ 24" oc. NO exterior insulation. 7.25" of dense pack cellulose between studs (R3.8 per inch). Whole wall insulation value is R-23.4
Both meet IRC 2021 requirements. You can achieve identical whole wall R values while foregoing the use of petroleum based insulations and avoiding the construction complications of exterior insulation.
What is the benefit of putting the insulation outside the sheathing as opposed to underneath the sheathing?
AKeith,
- It keeps your sheathing warm, preventing it from accumulating moisture.
- A direct connection between the studs and sheathing is much stronger in shear.
Absolutely agree with Malcolm, put the exterior rigid foam (if you end up using any) outside the sheathing and WRB.
Malcolm summarized it well and it's certainly an excellent solution.
The only real drawback is that it can complicate the weather sealing of penetrations. Window and door installations can be a bit more complicated. SOME contractors understand this and have the experience to do it right and not overcharge for it. But it's my experience that a lot of contractors still haven't learned about it yet. So they may not do it right or they may overcharge to cover their perceived risk.
I mentioned the options because I'm trying to find ways to reduce materials that have a higher greenhouse warming potential (GWP) and are more damaging to the environment in their sourcing. Cellulose fits the bill compared to all of the rigid foams. Of the rigid foams EPS remains the least damaging on both counts. So cellulose is my first choice and EPS is next. Unfortunately there aren't practical solutions for using cellulose outboard of the sheathing.
Please see Table 1 on pages 7 and 8 of this Efficiency Vermont study. EPS is not the lowest GWP rigid foam. People say that a lot on this website. I think it’s a common misconception. People also seem to think mineral wool is a low GWP product too.
https://www.efficiencyvermont.com/Media/Default/docs/white-papers/20210122-GHG-RNC-final-report.pdf
Matthew, on that document I see that phenolic foam has lower GWP, but I just talked with a rep from the only company I know of that makes it, Kingspan, at the building conference in VT and they don't have any available and they haven't for the ten years or so that they have been promising it. Polyiso has a bit lower GWP than EPS but shouldn't be used where exposed to soil, and its typical foil facing can be a problem. XPS is an order of magnitude higher than those. What am I missing?
Keep in mind that although for the BEAM estimator they decided to ignore the embodied carbon categories for transportation and end-of-life, due to wild variations, there are still emissions associated, they are just hard to estimate accurately.
I agree about mineral wool. Basically, mineral wool, EPS and polyiso are all in roughly the same category of carbon emissions, unless you want to parse the differences more finely than most people care to.
The new, low-GWP XPS is much better than the legacy version they used in that document, but it's still roughly twice the emissions of EPS.
Mike,
I was not advocating for phenolic foam, just trying to point out that EPS is not necessarily the lowest GWP product available. jollygreen said "Of the rigid foams EPS remains the least damaging on both counts" so my reply was in response to that. This is for an exterior wall application so I was not considering any exposure to soil limitations here.
Regarding the newer HFO-based blowing agents for XPS, I made this comment in another Q&A (https://www.greenbuildingadvisor.com/question/advice-on-plan-for-exterior-insulation-zone-6#comment-250246) which showed the Owens Corning NGX XPS foam has a GWP of about 9.6 kg CO2e for the standard measured size of 1m^2 @ RSI-1. So even the newest generation of XPS is approximately 4 times worse than polyiso in terms of embodied carbon.
To be clear, I am perfectly fine with anyone using EPS. I just personally prefer the higher R-values of polyiso. I also live in Texas so the foil facer radiant barrier is a net positive for our climate, but I understand it is not always a good option. In the other Q&A I linked to, I mentioned some of the fiberglass-faced polyiso products available that would side step the impermeable foil facer issue.
If this is really a budget build replace the ground source HP with an air source HP this will put 10 or 15K back in your budget.
Yes, the ground source will lower your electric bill a little but not enough to ever recover the high cost of installation.
If you think I am wrong I challenge anyone to build a BEopt model with ground source has a lower cost of ownership.
Walta
Agreed. Montana is cold but that's not enough to justify a GSHP IMO. Need all of these in my opinion: high electricity prices, no solar potential, high heat load, low loan APR and intent to live in the house for many decades.
Isn't every build a budget build? This is my family's home. I need the budget we have to work. Not a lot of extra to throw at it.
I have considered going the heat pump route. But in my area they don't keep up when it's -10 for a week or 2. Yes it will produce heat but very inefficiently. I have looked into the duel fuel. With the rebates that are being offered the ground source made the most sense. No one really take into consideration the saving on heating you hot water either. You don't get that benefit with a duel fuel setup. Ground source is $60k duel fuel is $35k
Not many rebates for duel fuel maybe $2500. I get %30 for the ground source. So that gets me with in $7k of the duel fuel.
That's usually the math, glad it works for you with the credits!
Yea I have been back and forth a 100 times! I was solid on the heat pump route. Then back the GSHP. Then back. Now I'm solid on the GSHP. They are setting lines tomorrow so no going back! Ha
Exterior insulation on the sheathing is a must, as is a rain screen detail. The interior insulation for the 2x6 doesn't matter if it's spray foam or batt or blow-in nearly as much.
If you decide to put polyiso between your sheathing and wall framing, be sure you have adequate wall bracing. Even if not required by code, this is a good use of the IRC: https://codes.iccsafe.org/content/IRC2018/chapter-6-wall-construction#IRC2018_Pt03_Ch06_SecR602.10.
Your situation sounds like potentially a good fit for the Bonfiglioli approach: https://www.finehomebuilding.com/project-guides/insulation/breaking-the-thermal-bridge
Please explain what you mean by adequate bracing? I could read those codes all day long and they wouldn't make a lick of sense to me.
It seems to me that if I glue or staple 1" EPS foam to the back of my ZIP sheathing then I have the exact same product as ZIP -R? Correct? Aside from costing $45 a sheet more that is. Here in MT we are not subject to building inspections. Only inspections are electrical, and septic.
What kind of fasteners does ZIP recommend for there R ?
AKeith,
By spacing the sheathing away from the studs, even by an inch, there just isn't enough strength in the wall anymore. Zip-R tries to paper over this by doubling the number of nails you have to use. But there are more kinds of bracing than sheathing alone. You can use diagonal 2x4s in your walls to add extra strength. Sometimes that's done by cutting out pockets from the edge of the studs in the wall to make space for that bracing.
Zip does more than "paper over" the situation; they went through rigorous testing to get their system approved. But it does boil down to more or less doubling the nailing pattern.
Fair enough. But I do wonder if Zip-R wouldn't work better installed backwards.
There are competitors to Zip-R that essentially flip the system inside-out as you suggest. There are no advantages over simply installing regular sheathing and a separate foam layer.
Fernando discussed them here: https://www.greenbuildingadvisor.com/article/alternatives-to-zip-system-sheathing
AKeith,
See table #1 on page 5. http://cdnassets.hw.net/03/89/8e0a710f4b269e5cf2a50d490f1b/zip-r-sheathing-installation-guide.pdf
AKeith, there are some similarities between Zip-R and conventional OSB with a separate layer of EPS, but structurally they are not the same. Zip has polyiso adhered to the OSB. I'm not sure what compressive rating the polyiso is but at minimum the EPS would need to match. But it still wouldn't be the same as having the foam fully adhered to the OSB; using separate pieces introduces a "slip layer" and puts additional stress on each fastener.
I understand that MT does not have inspections, but as I wrote, the IRC is still a good guide for safe building techniques. You should read the Zip-R literature to learn about the details.
Zip is also widely regarded to use a higher grade of OSB than that generally available for regular construction too.
Bill
Where exactly are you? I’m in Kalispell and we’re are in a seismic zone in this area of the state. This is a very important detail. Yes there is no building code enforcement, but do you want your house to fall apart during an earthquake?
Ok, so how does this sound to everyone?
LP siding, 1" polyiso, ZIP, 2x6 studs, stabilized cellulose, drywall. ??
Does that sound like a wall that will preform well in zone 6 MT?
any issues? Does the ZIP count as a vapor barrier? Do I need one?
Still looking for a little information. Not sure if the 1" is sufficient? I'm actually in zone 5b. Will the above wall assembly preform well in my area?
I have also read that the condensation concern hasn't been observed in real world as much as people lead on? Idk I'm just trying to get my house to preform well with our having to deal with all the construction woes of furring and window and door details that go along with 2"+ ci.
The alternative is spray foam and I want to avoid that.
Thanks
Alex
Alex,
See my post #13 in your other thread where I answered that question. https://www.greenbuildingadvisor.com/question/exterior-rigid-foam-insulation-with-vinyl-and-tyvek
The short answer is:
- You are always safe if you go with the recommended amount of exterior foam for your climate zone, which is more than one inch whether you are in 6 or 5.
- The assembly can be fairly safe if you follow the recommendations in the second link in my post.
Ok I have read all the articles.
It seems to me if I go with:
-LP siding
- 1" foam
- ZIP sheathing
- 5.5" dense pack cellulose
- 2x6 framing
- membrain smart vapor retarder
- 1/2" drywall
Then I will have a wall that is proven and efficient?
My question with this wall is, do I need to use the ZIP if I tape and seal the foam? Seems I would have 2 air barriers? If I do use the ZIP do I need to tape and seal the foam?
Thanks
Alex
I had to change my screen name after I got prime
Foam tends to shrink over time so the tape might not hold up.
Also when you have less rigid than required for full condensation control, it doesn't hurt to provide a bit of drying capacity to the outside. This means not taping the rigid to allow for a bit of diffusion drying, even better also use crinkled house wrap.
You can read more about this and the beer screen near the end here:
https://buildingscience.com/documents/building-science-insights-newsletters/bsi-026-they-all-laughed
That wall should perform well for you, though I would add a drainage layer behind the siding. You can have as many air barriers as you want; in fact, the more the better. It's vapor control layers that you need to be careful about. Like Akos says, foam shrinks. If you choose to use tape, I recommend using one that can stretch a bit.
Tape and Seal the ZIP. Important.
Don't tape the foam. Not needed.
– LP board and batten siding
– ZIP sheathing on walls and roof
– 2×6 walls
-1″ spray foam
– stabilized cellulose remaining cavity
– 1/2″ drywall.
>>>> Better:
– LP board and batten siding
- Rainscreen 1x4's. (Not optional* Many builders still don't do this, but it needs to be done.)
- Exterior insulation (1" foam or more depending on budget or ZIP R)
– ZIP sheathing on walls and roof (Zip is fine)
– 2×6 walls (Advanced framing)
- Cellulose fill or Rockwool. (Not a fan of spray foam)
- Membrain smart vapor retarder (Optional if you can afford it, do it.)
– 1/2″ drywall. (5/8" is optional, but better)
- Alpen High Performance Products Windows :D
Why is the rain screen so important?
Also, I have access to polyiso local to me that is paper faced? Is that acceptable for exterior insulation? The distributor says it won't work and will swell ?
The polyiso that I have available is the GAF brand.
https://www.gaf.com/en-us/products/energyguard-polyiso-insulation
Axel,
I think this product would work fine. It is a “glass fiber-reinforced cellulosic felt facer” with
“Excellent dimensional stability, high moisture resistance and low water permeability” according to their data sheet. It’s <1.5 perms.
You should reach out to GAF and see if this is an approved use of the product to be safe.
I have used something similar a number of times on walls. Works great, building inspector had no issues with it.
I like to put the WRB over the foam and mount the windows as outies over small window bucks. This is a very quick and simple install of window flashing details and window trim although at 1" it might not matter much.
So with the ZIP under the foam, do I need another WRB?
So, my plan has changed to 1.5" because this GAF product is so reasonable, it's the same or less than the 1" I have been considering.
Yes we plan on holding the foam back the width of the window flange and ripping 2x material to build up flush with the foam.
You have a couple of options.
ZIP with innie windows. Simple install/flashing, more complicated trim with thick foam.
Zip with outie windows. Fair bit of flashing tape origami, simple window trim.
CDX/OSB with taped seams and exterior WRB. Simple flashing, simple window trim.
Of course you can also go with ZIP and exterior WRB but that seems a bit redundant.
So I also could use EPS. Suppliers around here can get non faced for a reasonable price. Is there a reason to use foil faces foam as opposed to just straight foam?
So question on this, if I replace the cellulose with fiberglass? What are the advantages and disadvantages?
Thanks!
Blown-in dense pack fiberglass (not the kraft-paper batts) is an excellent choice, very comparable to cellulose. It has a higher GWP than cellulose but it also has a slightly higher R-value. I would go with whichever option is cheaper.
Ok good to hear! My insulation guy says for a 5.5" wall I will get an r value of 23? Johns Mansfield site said the same thing. So with 1.5" of xps on the exterior and 5.5" of fiberglass in the wall I'm looking at around r-30 for my walls?
About R-4.3 per inch for BIBS is what my notes say. So yes, I think they quoted you correctly.
Why XPS? Previously in this thread we tried to steer you towards polyiso or EPS as better alternatives. XPS loses R-value over time and ends up being R-4.5 per inch or lower in the long run. It’s also terrible for the environment, even the new HFO-based blowing agents like Owen Corning’s NGX product is roughly 4 times the GWP as polyiso.
Mainly because the polyiso I mentioned earlier in this thread isn't meant for wall assemblys. The only thing available to me local is EPS and xps. I would go with EPS, they call it beadboard at my local lumbar yard. Is that the correct stuff?? When I ask for prices on it they act like it's the worst thing ever and tell me I don't want it. It is just EPS and no facer.
I would have no concerns whatsoever using roofing polyiso on my walls in a non-load bearing setting. Was it GAF who told you not to use it for walls or was it the same salesman who said EPS is a bad choice?
“Beadboard” in my neck of the woods is a type of wood paneling for the interior of walls, but EPS is made up of little polystyrene “beads” so I could see how they might call it that. It’s the same material that disposable insulated coffee cups are made from.
Yes I called GAF and they said it wasn't approved for wall assemblies. They used to make a wall approved polyiso but no longer make that. So you think unfaced EPS will be just fine then?
Yes it will be just fine. EPS regularly goes under slabs and can be exposed to moisture without concerns. Remember, it is used to hold coffee! Add a rain screen in front of it and it will last a long time.
I need to get this foam ordered, and I value your input. I live in a fairly cold climate. Zone 6b. But we trend on the warmer aide as our elevation in lower than most of MT. Regardless, I have everything set up at the moment with walls standing for 1.5" of foam. So I need to decide between the XPS, unfaced EPS, or the poly iso from GAF. I can also get foil faces EPS but it is much more expensive.
If I did switch to EPS what would my total r value be with r23 in blown in fiberglass in the wall cavity?
EPS is R-4 per inch. You don't need a facer, the unfaced product is probably preferable actually. You have Zip as your WRB, correct? Your clear-wall R-value would be about R-29. My personal choice would be polyiso, but given that the manufacturer does not recommend its use on the wall it is technically a building code violation to install a product different from the manufacturer's guidelines. You might be able to find other sources of polyiso at the big box stores, brands like R-Max are available readily near me in Texas. They would allow for wall installation.
I would need a lot more information to calculate your effective whole-wall R-value like your framing factor (16" vs 24" o.c.) window and door U-values and area of the wall taken up by both of those. But I think you were just asking for a center-of-cavity R-value.
Yea you nailed it!
Yes the ZIP is installed currently
I can get 1.5" EPS for $18 bucks a sheet at my local lumbar yard. They have to order it but it a week out is all.