New home: wall design help please

Ok, so we probably should have worked out the details on this sooner, but here goes….
We have a new home under construction, the framers are sheeting the roof as we speak. We are in the PNW (zone 4c) and have 2×6 walls. They were designed and engineered with studs on 16 inch centers. I wish we had 24 inch centers, but did not want to go back to engineering. They are sheeted with 7/16 plywood. The current plan is to use Tyvek Drainwrap, an inch of rigid foam, a 3/8 inch rain screen, and either fiber cement board or cedar faced plywood cladding. When looking through the details for wall/windows and flashing on GBA, every one I found shows the foam acting as both sheathing and water resistant barrier. So it got me to wondering: is my wall design fundamentally flawed? Do I need a WRB if I have foam? Will it cause problems to do it this way, or is it just redundant? And finally, where can I find details drawings for the window flashing for MY wall? I am going to do the exterior envelope myself, so any help would be greatly appreciated.
Thanks,
Dave
GBA Detail Library
A collection of one thousand construction details organized by climate and house part
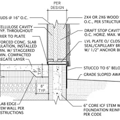
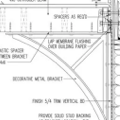
Replies
The way you're proposing is common and works well. The window detail is called an "innie" style window. The counterpart, where the WRB (and window) is at the outermost layer of foam, is called "outie". Searching for those terms should give you lots of info here on GBA and elsewhere on the web. Here's a GBA article to start with: https://www.greenbuildingadvisor.com/blogs/dept/musings/innie-windows-or-outie-windows
Yes, you really do need a WRB, no matter what type of foam you're using. You might get away without it if it's a 1-story with 24" roof overhangs, but even then the ounce prevention is worth more than the pound of cure, for that one gale-force rainstorm per century that drives 10 gallons of water past the siding.
Regarding the foam: Foil faced polyiso has a bit of performance edge over XPS, and is a far greener product due to the difference in blowing agents used. Sealing the facers with FSK tape is as quick as anything. With a foil facers the studwall & sheathing can only dry toward the interior, but with R6+ on the exterior of the sheathing and ~R20 in the cavities you will do just fine from a dew-point/winter moisture-accumulation point of view. (IRC 2012 prescription is R3.75 min for the exterior R for 2x6/R20 construction.)
A 16" o.c. studwall typically has a ~25% framing fraction, and with either the fiber-cement or the cedar-ply siding you'd have a whole-wall R a shade north of R20 in that stackup. If you went with an inch of type-II EPS (R4.2-ish) instead of iso you'd still be above the IRC prescriptive value, but your whole-wall R would be about 10% less. With only an inch of EPS on the exterior the R value of that foam would be about R4.5 at a zone-4c mean January temp, but only ~R4-ish during the mean July temp, but it would also have considerable drying capacity toward the exterior more than 100x that of foil faced iso, and 2-5x that of XPS. So despite slightly higher wintertime moisture accumulation as compared to polyiso due to it's lower R, the additional drying capacity makes up for that. Either makes a fairly resilient assembly.
Damp sprayed or dense-packed cellulose in the stud cavities also adds to the moisture resilience of the assembly.