New home build HVAC

We are in the process of planning a new build, modern style retirement home, on our wooded lake property in Northern Wisconsin (54161 zip, top of zone 6).
Here is a summary of the design:
Fully rigid foam insulated grade beam slab on grade (sandy soil).
Centrally located 8′ x 12′ utility basement.
Attached 25 x 25 garage. (with in floor heat?)
Main level 1750 sq feet with;
North half for 2 bedrooms, 2 baths & laundry/mud room, small loft with clerestory windows and attic spaces above. 1 patio door to East in Master.
High wall, awning windows in the North rooms.
Open concept Southern half with;
Vaulted ceilings and combo awning over fixed window units on South wall plus 1 patio door to East screen porch.
Wall mounted gas fireplace insert in Great room.
Heated bath floors, regardless of heating system selection.
We will install a recovery ventalator for air exchange.
All windows and doors will be Northern climate, higher efficiency to reduce heat gain/loss.
3′ roof overhang all around.
Without to much detail, we will build 2×6 exterior walls with a combo of “Zip wall” foam exterior sheeting, spray foam layer to seal and bat insulation to fill the cavities. Great detail will go into interor and exterior air sealing to prevent leaks.
The roof system is in flux and our achritect will design for the best R value.
We have read plenty of related acticles & blogs (here and elsewhere) and understand the basics and cost/savings aspects for the different HVAC systems available. We have both natural gas and electrical avilable on site.
For the comfort aspect we have been focused on “in slab” hydronic heat supplied by a combo on demand gas unit with domestic hot water.
After all this reseach our question is … what is our best “Green” option for comfort heating and the occasional air conditioning/dehumidifing.
Christine & Pete
GBA Detail Library
A collection of one thousand construction details organized by climate and house part
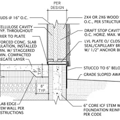
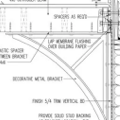
Replies
>" For the comfort aspect we have been focused on “in slab” hydronic heat supplied by a combo on demand gas unit with domestic hot water."
Most combi-heaters don't have sufficient modulation range on the low end to work well with slab radiation in a decently high-R house. Run some preliminary Manual-J load numbers (for both heating and cooling), and update it as the design evolves. DON'T break the heating up into any more zones than absolutely necessary- it's easy to short-cycle a combi boiler into low efficiency and early grave on a house with that description.
Even 199 KBTU/hr combi boilers can be a bit of a pain at your mid-winter incoming water temps if there are any large tubs to fill. Most of those don't modulate much below 19,000 BTU/hr, which is probably more than half your design heat load at -11F (the 99th percentile temperature bin for Marinette) or whatever. That means it won't modulate much with load except during the coldest days/weeks. That isn't a disaster as long as it's not short-cycling, but there are probably better solutions (such as a right-sized modulating condensing boiler + indirect water heater.)
>"After all this reseach our question is … what is our best “Green” option for comfort heating and the occasional air conditioning/dehumidifing."
With out realistic preliminary load numbers it's hard to make appropriate recommendations. A sketch of the floor plan with the room by room load numbers penciled in can be useful here.
Thanks for the insight. I am working on load calcs. as soon as we make a decision on window manufacture.
I have picked up on a lot of comments in blogs here, steering away from in floor heat for high R construction. Any thoughts?
>"I have picked up on a lot of comments in blogs here, steering away from in floor heat for high R construction. Any thoughts?"
The load calcs come first. If the design load works out to be 5 BTU/hr per square foot or something the comfort benefit of slab radiant floor is a bit muted, at 10 BTU/hr+ it can be pretty good.
From a carbon footprint perspective anything that requires burning fossil fuels isn't all that great. Cold climate heat pumps backed up with resistant electric heat cover the shortfall for the hours when it's way colder than -10F (or a wood stove) has a much lower operating carbon footprint. It's possible to spec cold climate heat pumps for design temps in the -10F - -15F range.
I know this isn't your question, but I would strongly consider blown in fiberglass over batts when going over sprayfoam. There will be a lot of surface irregularities that batts will not fill, but a BIBS or equivalent system will.
I am in the trades and have seen that as well. I am of the school that "Dead Air" is the best insulator so between a well sealed exterior and a tight interior moisture barrier I am not too concerned.
OK, now that I have spent a significant amount of time, my first 3 weeks on GBA, I am more confident I didn't know as much as I thought I did.
I am working toward calculating my heat load (Dana D comment #5) and am looking at exterior wall construction.
With a better understanding of the current "Air seal / Insulation" theories and a desire to build an affordable comfortable and efficient home I am reconsidering a layer of spray foam, then batts (T Carlson #2)
I am an Electrical contractor and will do the work myself, with close attention to envelope penetrations and limit horizontal wiring through the insulated cavities. All of the plumbing will be in slab and will not penetrate the outer walls.
I plan to oversee the entire project and will insure strict compliance from all of the subs.
What I am looking for now is a "wall R value calculator" to help me select my method of construction. The only reference I found here was from 2016 and the link is no longer active.
Any Help? Thanks
This calculator is pretty good for total wall R-value:
https://ekotrope.com/r-value-calculator/
For new construction, the best path seems to be using the sheathing as the airtight layer. Plan the construction so you can test the air tightness prior to any insulation or drywall going on the walls. The ceiling is usually the tricky item to plan for in this approach. This approach gives you a simplest surface to address any leaks that are found in testing.
If you can secure a large supply of reclaimed or seconds polyiso, that is by far the most cost effective way to go. Then batts work well on the inside, particularly with a bit of advanced framing.
Thanks Matt
I found another calculator on line at Applied Building Technologies and without consideration of the siding and air gap, I get an R29.412 with 2.5" polyiso, housewrap, OSB, 5.5" fiberglass batt @R19 & 1/2" drywall. Using "Ekotrope" with vinyl siding & gap, I get 35.348.
I would like to get to the 10-20-40-60 envelope.
Also I have picked up on the "recaimed polyiso" in other articles and will certainly look into availability.
>"...5.5" fiberglass batt @R19..."
R19 fiberglass batts are one of the CRUMMIEST materials currently being sold as insulation, and only performs at R18 when compressed to 5.5" in a 2x6 bay (it's tested for labeling at ~6.25" of loft):
https://s3.amazonaws.com/greenbuildingadvisor.s3.tauntoncloud.com/app/uploads/2018/08/08074629/Compressing%20fiberglass_0-700x310.jpg
R20s are now being manufactured in volume (since the IRC started including R20 in the prescriptives), and actually performs at R20 in 2x6 walls.
>"Also I have picked up on the "recaimed polyiso" in other articles and will certainly look into availability.
Run this search every week or two to see if a reclaimer closer than Reedsburg WI shows up:
https://greenbay.craigslist.org/search/sss?query=rigid+insulation
You also might be able to get a shipping estimate from that outfit in Reedsburg once you know how much of what insulation you'd be looking for:
https://madison.craigslist.org/mad/d/madison-discount-insulation-foam-board/7073907121.html
(Note their phone #: 608-616-0594 )
TOTAL RESET ish
We have spent a great deal of time reading many topics here on GBA and now have a re-set of our construction plan.
Based on what I see in "5 Rules for Wall Design" and with Advanced Framing Techniques we are now going to shoot for the 10/20/30/60 insulating goals.
The walls will be siding, rain screen gap, Polyiso R11+ thermal break, WRB, OSB, 2x6 - 24" on center, interior vapor screen, blown fiberglass and painted drywall interior.
The roof will be a similar process as most of the ceilings will be at the underside of the roof.
The air seal barrier will be outside the sheathing level and and I wonder if a painted on material with extensive caulking and taping would be best. Followed by a blower door test and fine tuning of course.
I understand that concrete has a significant carbon cost and looked at alternative methods, but since we are on very sandy glacier formed sand, we will stay with the insulated concrete slab on grade to avoid moisture and vermin exposure from below and may include in ground ISO gutters beyond the foundation.
Budget will ultimately drive our decision on double vs triple pane windows. I will consider fiberglass for the high awning windows on the North wall and garage and spend more on the 2 triple wide awning over fixed assemblies on the South wall in the great room. Roof overhangs are to be 3 feet and fairly low to the ground.
I am still wrestling with the heating though. We do not have the time for payback or the resources now to go with Geothermal, so Air source heat pump(s) will provide our heating and cooling needs. If we have a separate HW heater, it may be a heat pump as well, unless I can combine with Hydro floor heat in the bath rooms and garage floor (wish) and an HRV system for balanced ventilation. The kitchen will have a separate passive air makeup for the range hood.
Now where do we go?