New construction wall choice in Zone 6B

I am designing a house in Montana and I am going crazy trying to figure out the best wall type for the money. The biggest problem is that my mother (whom the house is for) is dead set on a stone veneer product from Vennerstone, and even with standard siding and our dry climate I see a lot of wood rot in the area (I used to install internet for people, and I have seen a lot of crawl spaces). We don’t get a lot of rain but do get tons of snow and subzero temperatures in winter, 100+ degrees in summer and high winds (50-60 mph is not unheard of) year-round.
After doing a ton of research I came up with this:
6” stick frame with standard R-19 Batts
DensGlass Sheathing (I like the idea of avoiding OSB and this is cheaper, but I am worried about rigidity of the walls with this)
House Wrap
2x layers of 1” XPS Rigid Foam Board
Some sort of water drain layer
self–furring metal lath with some very strong fasteners to go through 2” of foam
Mortar scratch coat
Stone Veneer
Pros:
High R-value
Cons:
Lots of layers that will drive up costs along with labor and install time
I have read that DensGlass is not as strong as OSB so might not keep the house as rigid, which can be a problem with the high winds we tend to get
Might have trouble getting contractors to do CI. Residential construction around here is stick frame and Tyvek, that’s it.
Might have issues with the stone veneer holding up through 2” of foam, manufacturer documentation says ½” max
After looking at the additional cost and install times of CI and WRBs I am thinking it might be better to go with ICF.
ICF
WRB
self–furring metal lath with standard fasteners
Mortar scratch coat
Stone Veneer
Pros:
Solid and rigid
Much simpler and easier to put up
Nothing to rot
Fire and termite resistant
Cons:
Might have a lower R-value unless we go with the extra foam panels (like Logix D-Rv), increasing cost.
ICF + extra insulation + stone veneer will make for an incredibly thick wall
I could only find a handful of contractors in the state
I am really leaning towards ICF, but I keep coming up with conflicting information regarding R-values, drain layers, average cost, and everything. Any advice would be greatly appreciated.
GBA Detail Library
A collection of one thousand construction details organized by climate and house part
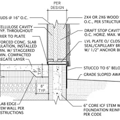
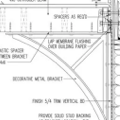
Replies
R19s are practically "genuine imitation insulation" when applied to wall cavities. Installed perfectly they perform no better than R18 when compressed to 5.5" in a 2x6 cavity, and are such low density that any air leaks move air easily through the insulation. R20 mid-density batts are better, R21 fiberglass or R23 rock wool MUCH better.
XPS is the least green insulating material in common use due to it's HFC blowing agents (powerful green house gases). As the blowing agents diffuse out over time performance eventually drops to R4.2/inch (the same as EPS of similar density) even though it's warranteed to "90% of labeled R value". So at 2" the most should be counting on is R9, which is not sufficient for dew point control on R19 fiberglass (or R23 rock wool) in US climate zone 6B, which means it would need an interior side vapor retarder to keep the Densglass or cold side of the batts from accumulating frost/moisture over a winter. For R20 batts the IRC calls out a minimum of R11.25 on the exterior for dew point control using standard latex paint as the interior side vapor retarder.
Using 3" of 1.5lb density (aka "Type II") EPS, blown with much more benign pentane, with stable performance over the decades would deliver R12.6 on the first day, and 50 years from now, which would be enough for dew point control for high density fiberglass or rock wool batts.
Using 3" of reclaimed roofing polyiso (dirt-cheap, when/where it's available) would deliver about R15 performance in that stackup. Using reclaimed 1.25lb density roofing EPS (Type VIII) would deliver R12.5, which is plenty for R21 fiberglass, marginal for R23 rock wool in the colder parts of zone 6B, but fine on the warmer parts.
Of course 3" isn't any better than 2" from the perspective of the stone veneer vendor's 1/2" maximum. Does the vendor give guidance on installing it on ICFs? Most ICFs have 2.25" or more of Type -II EPS on the exterior, so it's the same moment-arm issue on the ties/hangers when hanging heavy siding through the foam.
I read somewhere that polyiso drops its R value when it gets cold so its not so great for colder climates but I will look into it some more, but the hangers are still a problem. The nice thing with ICF is that the web ties that you actually screw into are only about 1/2-1" away from the outside face.
Also any suggestions on where to look for reclaimed roofing polyiso?
Sam,
There is nothing wrong with using any of the fiberglass mat gypsum sheathing products (ie Densglass) in structural application, just have to follow the fastener schedule.
There has been a number of discussions on this forum of low cost high R value walls. If you are paying for labour, pretty much either 2x8 with batts or 2x6 with insulated sheathing (ie ZipR).
As for veneer, the usual problem is the WRB. Lot of installs skimp on this or don't detail the window/door ares well thus the water and rot issues. I see a lot of installs over bare plywood around here, that is asking for trouble.
ICF is a generally a big upcharge over stick built. Might be worth it in tornado areas, otherwise it is an expensive wall that doesn't preform that well energy usage wise (thermal mass is in the wrong spot).
The WRB is what worries me the most, as I need to be very careful to make sure the right stuff goes on or the contractors will throw it on the bare plywood. Any suggestions on WRB products?
The cost of ICF is what leads me to most of the conflicting information I come across. The only price comparisons I can find are ICF vs basic stick framing with no mention of CI, that that is definitely more expensive, but some sources claim that after time labor costs are factored in they come out pretty close with ICF maybe a couple dollars a foot more. After adding in the CI then ICF might be about the same price, but, i admit, this is a guess coming from the information I gathered. Do you have any data or sources breaking down the costs between the two?
Sam,
The insulated sheathing products with built in WRB or densglass with roll on WRB is harder to mess up. If you are going with stone veneer, spec paper backed metal lath for extra insurance.
If ICF was cheap, you would see it in track homes. Forms are expensive, concrete is expensive (also a very high embodied energy building material), people that know how to build with it are harder to find. Also with ICF you need to put drywall on the basement even if you don't intend to finish it (at least around here).
HI Sam -
I assume you have this but in terms of the shear strength of Densglas sheathing: https://www.icc-es.org/wp-content/uploads/report-directory/ESR-3087.pdf.
A key element of any applied masonry cladding is the bond break layer, in addition to the WRB. See Vennerstone installation over wood framing/sheathing: http://www.veneerstone.biz/images/pdf/InstallBrochureTS_BR002v4.pdf.
It's nearly impossible to compare the costs of different building enclosure systems in my opinion, in no small part because labor's familiarity with different systems has such a big impact and making quality of installation equal for different systems is also key to the comparison as well as the outcome.
I would ask to see projects under construction for both local ICF and framing contractors, so you can get a sense of which ones are on top of their crews, and quality control.
Peter