New construction: exterior walls

Hello, first time builder and avid researcher and want to build my house “right”.
We are building our home in Minneapolis MN and we believe have signed up a trusted builder.
We are planning on using Stucco on the entire house.
Wall construction as follows based on my current plans from the builder.
Stucco
2 layers grade d building paper
1/2″ Plywood Sheathing
2×6 Studs 16″ OC
3″ Spray Foam Insul and Sealer or Fiber Glass Batt.
Continuous Poly Vap Barrier 6 Mil – Seal all seams & Penetrations
1/2 Gyp BD – Taped, Sanded Painted.
I am very worried about the stucco and making sure we do this right so we do not have moisture problems. And also would like to see the wall have a bit higher R rating.
They are planning on using a Flash and Batt system, which I questioned via email and thought I was going to be good because what I read says 3″ and here was the response.
“The flash and batt system uses 1/2″ – 1” of foam so it intentionally does not create a vapor barrier, then the batts go in with the normal poly vapor barrier on top.
If you saw 3″ it was likely referring to the rim joist areas, in those areas to seal the transition between the foundation and the framing we use all spray foam to assure a tight seal as there is no way to get standard insulation to fit tightly into all those tight areas.
What is your opinions on this type of exterior wall? Should I be questioning this?
I am far from a building expert and hate telling others what they should be doing, but I also want to be sure I am doing what is going to be a good long term solution.
Thanks
Also I have attached the plans. I am open to any suggestions. I was first attacking the Exterior Walls but am open to any suggestions. Again no matter the cost I want to do this right the first time.
GBA Detail Library
A collection of one thousand construction details organized by climate and house part
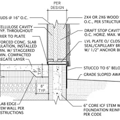
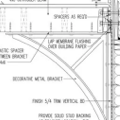
Replies
TechWallEye,
First of all, can you tell us your name? (I'm Martin.)
I'm not a fan of stucco over wood framing. (Stucco works well on stone walls or concrete-block walls.) But if you insist on stucco over wood framing, especially in a cold, moist climate like yours, you absolutely must include an air gap between the stucco and the plywood sheathing.
For more information on this issue, see "To Install Stucco Right, Include an Air Gap."
Hi Martin, name is Tony. Thanks for the response. I am going to be sure that we get an air gap put into the wall.
Hi Tony -
Convince your spray foam installer about the right depth of closed-cell spray foam for flash-and-batt walls in your climate with an information resource from the Spray Polyurethane Foam Alliance: "SPFA-147 Spray Polyurethane Foam for Hybrid Insulation Systems - Part 2: Climate Zones 4-7" - http://www.sprayfoam.org/index.php?option=com_chronoforms&chronoform=techdocs&file=SPFATechDocs2015/SPFA-147%20-%20Aug%202015.pdf.
Peter
Tony,
I inspect stucco for a living. I agree with Martin's post above - I also do not love stucco on wood framed walls, but if you insist on doing it, you must have an air gap. A product like Benjamin Obdyke's Home Slicker Max works well, and there are many similar ones on the market. 2 layers of Grade-D paper is a code minimum, but you will get better performance out of any number of synthetic papers. Also, flashing tapes stick to many of the synthetic papers better than Grade D.
But I have other concerns about your posted wall. It doesn't meet code in most jurisdictions. I don't see the effective code indicated on your plans - you should ask your architect. My jurisdiction is on the IRC/2015 right now, and that requires both cavity and continuous exterior insulation for CZ6. Either R20 cavity + R5 exterior or R13 cavity + R10 exterior is required. Note that the code is wrong here. R20+R5 will not keep the sheathing above the dew point in your climate and it will be soaking wet by the end of winter unless your poly installation is perfectly airtight. I'm also not a big fan of interior poly on any walls except in zone 7 and up. Poly inside and stucco outside is a recipe for disaster, though the air gap moves the odds more in your favor.
Your proposed walls are not even a bare minimum design. There are so many better designs discussed here on GBA - better in terms of insulation level, durability/reliability, "green-ness", or nearly any other criteria. Your architect and builder seem to lack imagination and/or knowledge of advanced building techniques. I'd recommend spending a bit more time in planning before pulling the trigger on construction.
Many posters here seem to have their favorite wall systems, and most of them will work. If nothing else, some simple changes will dramatically improve your performance: Swap the poly for a "smart" vapor retarder. Add 2" of exterior foam or rockwool insulation. Make sure the builder is performing blower door testing for air leakage and carefully detailing joints and gaps - flash and batt systems do not automatically account for air leakage under sills and between stacked framing members, among other things. There's always more you can do.
I was on another forum with someone from Minn and he had a similar wall (minus the stucco).
For some reason, a very cold area has builders that think it is acceptable to build a wall like this. Please fight back against this old school. This person did and could not get exterior foam - neither architect or builder was helpful. So you face an uphill battle.
There is just no financial or environmental reason to build a wall like that in 2019.
You do not need to be an environmental zealot to justify a better wall. It sounds like you know that. The conclusion to higher R value is seemingly always thick wall (double stud) or exterior foam. The R5 of your framing is a terrible hit to the whole wall value.
I am admittedly a zealot and I have a better wall in NC where sub 30 weather is a 15 night a year event. It is 60 today. And A/C thermal wall load is pennies.