New code option for cold floors
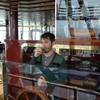
Just read this on PNNL’s site:
“So the best way to construct a warm floor is continuous rigid insulation coupled with an airspace above the cavity insulation (see figure below).”
And that meets 2015 IECC/IRC code. https://basc.pnnl.gov/code-compliance/sealing-and-insulating-existing-floors-above-unconditioned-spaces-code-compliance
This is news to me. In our old house’s fight against cold floors, the typical recommendations have been:
A) condition the basement
B) install radiant flooring
Both options (A) and (B) are expensive. This new code option would be far less expensive for us.
Anyone seen this in action?
GBA Detail Library
A collection of one thousand construction details organized by climate and house part
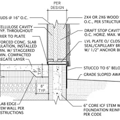
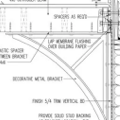
Replies
V,
This is from Martin's recent blog Insulating a Wood-framed Floor Assembly:
Counterintuitive advice on air gaps
Over the years, several GBA readers have posted questions about unusual advice from Joseph Lstiburek, a principal at Building Science Corporation. Surprisingly, Lstiburek recommends that builders insulate floor assemblies with undersized batts, with the batts installed tight to the ceiling below, leaving a deliberate air gap between the top of the batt and the underside of the subfloor. This curious suggestion seems to contradict the advice of many energy-efficiency experts.
As most builders realize, insulated floor assemblies usually suffer from thermal bridging through the joists. (In other words, the joists do a worse job of insulating than the batts.) If you look at a typical insulated floor assembly in winter from indoors with an infrared camera, you’ll see that there is a cold stripe above each joist.
Lstiburek explains that if you leave an air gap above the batts, the air trapped between the top of the batts and the subfloor will be warm in winter, since it’s on the interior side of the insulation. This warm air helps keep the tops of the floor joists warmer than they would otherwise be, thereby reducing the contrast in temperature between the floor joists and the insulated joist bays.
When this topic came up in in a Q&A query, I wrote, “Lstiburek’s approach — leaving an air space between the top of the insulation and the subfloor — is dangerous to follow if you are a builder with average skills, because air leaks in floor assemblies can allow cold exterior air to infiltrate the joist bays. Once that happens, this detail is a disaster. The detail only works if the builder has impeccable air-sealing skills.
“Here’s the bottom line: The insulation that is doing most of the work in this assembly is the continuous layer of rigid foam under the joists. If you want a warmer floor, beef up the thickness of the rigid foam — and do an impeccable job of air sealing at the perimeter of the floor assembly (the rim joist area). Then it hardly matters how much fluffy stuff you put between the floor joists. You can put in a little (the Lstiburek approach) or a lot (my way).”
When I discussed this issue with Lstiburek, he admitted that leaving the air space above the insulation results in greater heat flow (because the batts aren’t as thick as usual) and thus (to a limited degree) the air space results in more energy use. But Lstiburek claims that a floor assembly with his unusual detail will be more comfortable.
If the joist bays are completely filled with insulation, the difference in temperature between the subfloor directly above a joist and the subfloor above the center of a joist bay — a difference in temperature caused by thermal bridging through the joists — will be 1.5 F°, according to Lstiburek. If you leave an air space above the insulation, Lstiburek says, the difference in temperature between the two locations is 0.5 F°, which is less noticeable and therefore more comfortable. (Joe wanted me to emphasize that he is not advocating in favor of less insulation — only for improved comfort.)
That said, if you install a continuous layer of rigid foam insulation across the underside of the joists, you get the best of both worlds — plenty of R-value and no cold spots above the joists due to thermal bridging.
I am with Dr. Joe on this one with this caveat. An insulated floor over an unheated space, a garage for instance, will be comfortable to the touch if there is an airspace between the top of the insulation and the floor if;
* 2 x4 open web trusses are used so any thermal bridging is minimized due to the long path of heat flow in the triangulated floor truss webs.
* The rim joist is air sealed to the highest degree possible, I like 3 layers of 1 1/2"polyiso foam (R-30) with caulking for this task.
* The floor is insulated to a sufficient R-value (R-50 in MSP) with a blown insulation for maximum thermal effectiveness.
A slight settling of the insulation will occur leaving a very slight airspace that if all tasks have been carried out correctly will be right at room temperature. How do I know this? I built an art studio over a double attached garage in The Twin Cities and was visiting the owner on a cold winter day last year. I had two small digital thermometers with me, I put one on a work table about 3 feet off the floor and the other right on the wood floor. After a time both thermometers read 70F.
Now this studio is built with high R-values, R-30 wall, R-65 vaulted ceiling and R-50 floors and very airtight (est. 1 ACH50). Minimal stratification is in play here, thus the even indoor temperature from floor level to work table height. Next time over I will suspend one of the thermometers at a height of about 8' or more above the floor and one again on the floor to see how they compare.
Doug,
I think the distinction between floors with an air-space and those with full cavity insulation is the temperature of the floor surface itself, not the temperature of the air close to the floor level. Whether the differences the Joe and Jon have cited are large enough to be perceivable is an open question.
Malcom,
In a well insulated floor assembly the air temperature in the air space above the insulation and the floor temperature will be nearly the same. I can say in the case of the studio over the unheated garage I reference, the floor felt very comfortable on my stocking feet on that cold winter day. No scientific analysis here , just perceived human comfort !!
>This is from Martin's recent blog Insulating a Wood-framed Floor Assembly:
Oh I'd his post but didn't think it discussed cold floors. I'll reply there.
P.S. I see now that Martin was unaware of the code change, which was my point in posting.
Seems folks are disagreeing with good ole Joe again :)
Joe is a bit of a trail blazer, and many builders prefer to stick with things they’ve “always done that way”. That can cause some arguments, but it doesn’t mean Joe is wrong.
Other times Joe’s idea is intended to solve one particular issue, but may have other side effects or just not apply in every situation. You need to get the entire system optimized, which means you have to make some trade offs sometimes depending on what you’re goals are.
Bill
Using THERM, I get .3F variation with a gap and 1.0F variation without. Less (but not none) with some foam. And the average floor temp is higher with no gap. I wouldn't bother with a gap - spend more time thinking about your windows and how downward convection creates cold spots on the floor.
Jon,
I'm in the middle of replacing the original 90 year old basement windows -- had to stop because of the sudden cold snap -- and we're in the processing of sealing the inside frames / openings of the new(er) double vinyl windows on the 1st and 2nd floor that the previous owners installed. I've got all the material to air seal & insulate the rim / sill too but had to re-prioritize. Too many projects :)
Should I tackle the rim joists 1st? Especially if cold floors are related to air leaking there. Our basement has 2' field stone foundation walls so the temp down there is a constant 50F, but perhaps the rim joists being closest to the floor joists is a contributing factor to the cold floors on the 1st floor ...
Conditioning the basement seems like it would have a benefit that floor insulation would not. It would assist with moisture/ humidity problems in that space. I assume it would be expensive because you’d have to install ductwork (or hydronic piping, since you mention radiant floors) to the basement, and then Insulate the exterior walls. But I’d find it surprising if the cost difference between the two options were really substantial (all that joist bay insulation etc will add up).
Am I missing something? Because I've learned a lot and trust GBA but there seem to be latent bias about "best" process, like conditioning a basement.
Take a 90 year old house like ours. It seems many folks here and elsewhere assume a so-called "deep energy retrofit" and hefty goals like Passiv or the opposite "po man's" DIY with weatherization and poor (Grade 3) batts are the only options, and one of those options isn't worth it. After reading great GBA articles and comments, I land somewhere in the so-called "Pretty Good House" spectrum. For example, the previous owner's 1980s weatherization project left our house leaky, so we take on projects to fix air leaks, yet I also realize Passiv or deep retrofit will deplete our savings. Everyone's situation is different and I think a spectrum needs to be considered.
Conditioning our 90 year old basement would be a serious undertaking because of what I understand. For example:
excavate the exterior down to footings to install exterior vertical insulation along the foundation wall
or excavate the exterior deep enough to install exterior horizontal insulation along the foundation perimeter
demo the slab to install insulation and water intrusion barrier below the current floor, and install a new slab
insulate & air seal the interior basement walls
increase the heating capacity of the system, and energy needed to heat the basement (ductless multisplit is our primary heating, with backup ducted furnance, and are going solar grid connected next month).
IMHO the above steps are just too much for our Pretty Good House goals. Just take demo'ing the slab step as an example of the extreme: what GBA doesn't talk about is the impact on retrofits, like removing all the critical utilities in a basement, which in our case means the backup gas furnace, the water filtration system, the hot water heater, etc. Basically homeowners have to move out until the project is complete. Even though we have an RV that we could live out of if we chose this path that could lower the "living elsewhere" cost, my Partner and I agreed that it's too much disruption, time, and $$$; especially if our goal is Pretty Good House.
And note one of the goals of a Pretty Good House: go small! I'm going to make an assumption based on what I've seen after years of buying, selling, and looking at houses: once an American conditions a basement, they then add rooms to the basements. It used to be the 1970s home bar, then the 1990s home theater, and now basements have bathrooms, bedrooms, dens -- they're all down there. Americans have a habit of making homes BIGGER by conditioning basements, and IMHO that negates the whole house improvements.
Example: let's say we can heat/cool our house with 33% less energy after a bunch of wise improvements that I gleam off GBA and elsewhere. And then we increase the size of the house by 33%. Now we need to heat/cool that bigger house. Well, that example NEGATES that efficiencies done! The house was 33% more efficient to heat/cool but then made 33% bigger so more space to heat/cool. It's a Net Zero change!! My Partner and I strongly object to this trend in American home upgrades. We are quite happy in 1,000 sq ft. :)
So I'm just not convinced that conditioning a basement meets our goals. This code change sounds like it could meet our Pretty Good Home goals with less intrusive measures. If I'm understanding, I'd be adding 6-8" to the conditioned space (so the depth of the insulating & air sealed floor joists), instead of 7-8' (the height of most basement walls), so the additional heating load would be much less, and the process far less intrusive to a home that's already lived in. Happy to hear experience or studies otherwise for retrofits.
Your points are well taken. For making an existing home more comfortable I would look to the attic first. A very well air sealed and insulated attic has good thermal properties and also you negate to a large degree the stack effect. Next I would head to the basement and seal all air leakage points there, insulate and air seal the rim joists if open. Add rigid insulation to the interior of the basement foundation walls.
By taking these two steps you have decreased heat loss by increasing R-value, have greatly minimized the stack effect and lowered the infiltration heat loss. By sealing air leakage points high and low you have relegated air leakage mainly to the neutral pressure plane area of the house. On days with little or no wind, there will not be much air movement through this area. Leakage points in the neutral pressure plane that show up during the depressurization of a blower door test are not as significant as leakage areas high and low in the building envelope. This does not mean you should neglect obvious leakage areas but start with those in the attic and those in the basement first.
Doug,
Agree, and we're already on that path.
Contractor installed close cell spray foam on the underside of our roof sheathing to get rid of several air sealing and insulating complexities with our knee walls and sloped ceilings.
I'm in the process of air sealing the basement. Hopefully once I'm done with that, the cold floors can go away; but I have my doubts. The basement is a constant 50F, so my bet is the 1st floor hardwood will always feel cool to the touch unless we do something to raise its temp.
Justin
I would 2nd focusing on air sealing first. With my 18" lime stone foundation house with unfinished basement, air sealing the basement (replacing the windows and spray foaming the rim joist) eliminated cold floors.
Insulation is always best on the basement walls(interior is fine), especially anything above grade. 2" of rigid there goes a long way to reduce losses and keep moldy basements at bay. Much cheaper and simpler than insulating the entire underside of the floor. It also keeps the joist open for any work down the road.
Akos,
This is great to hear.
I was in the middle of replacing the original single pane, wood framed basement windows (whose glass and frames had deteriorated into basically open holes) until the early "winter" cold snap hit a few weeks ago. I'm really hoping autumn comes back so I can finish the few remaining basement windows. And I've the materials to start air sealing and insulating the rim joist next.
You spray foamed the sill below the rim joist? or spray foamed the entire cavity at the rim joist between floor joists? And no blocking to put up against rim joist, like rigid foam? Just curious of the process that worked for you. I was hoping to avoid spray foam for this job, so had gotten small backer rod and thin sill seal that I was going to try to stuff in the crack with the top of the foundation, then caulk. I was toying with the idea of creating house wrapped "blocks" filled with several rigid rock wool squares to put up against the rim in the cavity between floor joists, because I already have rigid rock wool and house wrap, but I've never heard/read of anyone doing that. :) It seems most folks a) spray foam the entire rim joist or b) put layers of rigid foam up against the rim and caulk. And then caulk the sill where the foundation wall mates with the joist.
Our house sounds similar: it's 2' thick field stone encased in mortar.
I spray foamed the cavity with one of the 2 part kits. The rigid + canned foam should work as well and would be much cheaper to do. Canned foam doesn't stick too well to old dusty wood and stone, blowing it clean and misting the area with some water really makes a big difference.
I ended up completely removing the old window framing and pouring new sills (some had to be raised) and re-parging the stone/brick.
The headers above the windows as well as the entrance door sills were extremely leaky, those took a while to seal up. Doing work in the winter time is actually not so bad, no need for fancy thermal cameras to find the leaks.
I do get a fair bit of heat from the old black iron heating pipes, even with no insulation on the stone, in the dead of winter here the basement is a bit cool but never cold.
If you don't have any heat source down there, getting R10 to R15 of rigid insulation over the foundation would make a big difference.
Nice technique on misting before spray foaming, so I'll have to try that next time.
Same here on windows: I ripped out the entire wood frame. But we opted to put in glass block. Getting the right dimensions to insert replacement windows was going to be a custom order for us, but the glass block makers already had our dimensions ready to ship, and it was easy DIY job (for me, I'm no tradesman) to install them. I did spray foam the top of the windows where they met the bottom of the rim with low expanding.
You're not the 1st to recommend at least insulating the foundation walls even from the inside. We're just against excavating and insulating from the exterior because of time and money (if contracted). Good to hear that it will make a difference.
Justin
I wish production builders would use this approach being that the they more often than not build out living space above the garage. Cheapskates !
I have a house from 1930 and have experience getting rid of cold floors caused by an uninsulated basement (in our case, there is only access to the basement from the outside).*
Applying 2" of closed cell to the top of the ceiling did work quite well. We couldn't have added much more without burying electric wires, gas lines, etc. In our case our floor was supported by 2x8 lumber.
I did recognize that the insulation layer was below code, and we would get bridging through the floor joists, etc. So we ended up filling the remaining space in the joists with rock wool and covering everything with a sheet of poly, taking care to caulk the gap between double joists, which we had a lot of. I am pretty sure this improved the floor temperature some more and if people are really interested I could stick a thermometer between the 2 layers of insulation to see if the spray foam is now at least partially on the "warm side" of the building envelope.
But the thermal bridging is not the biggest concern if the wall is not well sealed which is our case. The floor above the basement still has cold spots on the outside edges of the flooring. What is happening is leakage of air where the wall framing meets the sill, and into the walls directly above it.
I suspect that without exterior sheathing, an old school, heavy layer of siding on the house is the only thing preventing air from getting into the walls. While the walls are blown with insulation and generally fine, I suspect that over the years mice have traveled under the siding and created air gaps. Plus some of the bottom wall plate was rotted out some cellulose fell out when I replaced the rear sill.
With a repaired and insulated sill, the mice can no longer access the basement, but any gaps above the still still allow the cold Massachusetts air to get to the edge of layers of wood flooring. The oak flooring layers run east-west so it seems that more air can travel into the floors on the east and the west side of our home.
My point is, in an older home insulating the basement ceiling may be fine, but to prevent cold floors it may also be necessary to strip the siding, at least the bottom layers, and install something like rock wool boards that completely cover the sill and at least the first couple feet of the wall. In our case I am thinking we might do this on top of the original wood/pressboard siding product, but that we should remove a foot or two of the product all around the house to inspect the bottom of the wall, address any rot, and re insulate the bottom of the wall, probably with rock wool batts or some product that would allow moisture coming from the foundation to escape.
Any thoughts?
*my old thread can be accessed here:
https://www.greenbuildingadvisor.com/question/basement-insulation-for-a-1930-house-retrofit-wall-and-slab
I don't have an answer to your direct question Rich, but ...
>I suspect that over the years mice have traveled under the siding and created air gaps.
I've been battling mice -- the joys of country living -- and one last suspect is the lack of a rodent / pest screen between my siding and foundation. I've no night vision proof but my guess is the mice crawl up the foundation wall into holes that I've not found on the underside of siding. But it looks like products only exist to block birds, termites, etc. nothing for larger pests crawling up foundation walls ?
We use this at the bott0m of our rain-screens to stop insects and rodents:
https://www.menzies-metal.com/metal-flashings/perforated-j-channel-rain-screen-low-back-5-lengths/
Ah, J channel screen. Great, ty Malcom.
That drawing is exactly how we did it in the late 70's 80's and 90's in the Twin Cities, MN.
I thought it worked extremely well. We built a lot of tuck under garages.
Random question: what does blown in cellulose, in a wall, look like after 60 years? Especially in a wall where there is some air movement... There should be good data on this by now.
Some sources say it will "not rot or decompose" and others say the lifespan is only 30 years. I suspect there is some compaction in all my stud bays in addition to the gaps caused by rodents before we bought the house.
MassSave (the state energy efficiency program) once put a camera on my walls, it would be a good idea for the state programs to do a baseline test and store the results to compare to future audits with different homeowners, 10 or 20 years later.
>"...others say the lifespan is only 30 years..."
I've personally seen cellulose in walls in a house in Worcester MA that were gutted roughly 30 years after installation that looked as if it had been installed within the last month. I suppose in side-by-side observation with fresh material some amount of oxidation may have been evident, but on the bigger flakes of newsprint the printing still looked pretty crisp. Had the house not been undergoing a full gut rehab and deep energy retrofit I'm confident it would not have looked much different after another 30 years.
I've read that there are balloon framed houses in Saskatchewan with cellulose insulation in the walls installed in the 1920s that are still standing, and still look pretty good in IR imaging.
The quality of the installation matters- I helped a friend remediate a balloon framed circa 1900 house where the wall cellulose had settled 3-4 FEET in only a dozen years. MassSave now inspects and audits most blown insulation installations to some degree, and insulation contractors under the program now seem (on average) to doing a lot better job of it than what was typical in the 1990s.