New build/wall question

Hello all,
I’m trying to build a fairly simple 2k sq ft 3 Bdr rectangular ranch in Southeastern WI, zone 6. My main concern is energy efficiency. I’ve spoken to 7 builders up to this point, and what I’ve been told is:
1) A 2×6 wall meets code and that’s what we do.
2) We will fill it with foam (doesn’t specify open or closed cell) if you want.
3) Have never seen or heard of foam insulation outside the sheathing. Discussing how it’s done, they state it sounds very labor intensive and they either won’t do it or charge a ridiculous amount to try.
If a builder will build the way they normally will (2×6 with fiberglass), I can build this ranch for 250k. If I say in addition I would like Huber zip sheathing, Roxul mineral wool instead of fiberglass between the studs and exterior foam insulation, it’s 450k – 550k for the same ranch. My rough math shows me a material cost difference of about 15k (certainly there would be additional labor costs, particularly for the external foam).
My first question: is this normal (200k difference for those 3 items)?
In trying a third alternative, I’m talking to a builder about doing some of the work myself, and trying to choose products that I’m hoping would reduce the learning curve for them. They will try using Huber Zip for the sheathing, I’ll be happy to do the taping/sealing. As external foam insulation, rain screen, furring strips than siding is completely foreign to everyone I’ve talked to so far, I thought the insofast with the rain screen and studs integrated so the siding could attach directly would make this appear less daunting with a single step; it’s still questionable if I can convince them to use it. That brings me to my second question:
What wall you would choose given the following four choices:
1) 2×6 filled with Roxul bats, Huber zip then siding
2) 2×6 with blown-in fiberglass, Huber zip then siding
3) 2×4 with Roxul bats, Huber zip, insofast 2.5 inch then siding ( R10 for the insofast foam )
4) 2×6 with Roxul bats, Huber zip, insofast 2.5 inch then siding ( R10 falls short of the 11.25 for a 2×6 wall; how much riskier is this )
I greatly appreciate any suggestions regarding a different approach, product, or other feedback. This is really becoming a frustrating process, more so than I would think, but I haven’t built a home before.
Regards,
Michael
GBA Detail Library
A collection of one thousand construction details organized by climate and house part
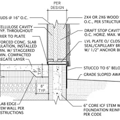
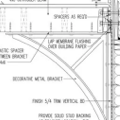
Replies
Michael,
The upcharge of $200,000 for energy efficiency features isn't justified. That said, the price is whatever contractors in your area decide to charge.
You haven't mentioned airtightness targets -- and an airtightness target is probably more important than an R-value target.
You mention Huber Zip sheathing -- but for some reason, you don't mention Zip R sheathing. Zip R sheathing might be more acceptable than exterior rigid foam for builders who are stuck in the 1960s.
To answer your question: Option 3.
I wrestled with exactly the same issues for my 1100 sf addition. I ended up hiring the contractor to build what he normally builds using studs and osb sheathing. I have installed the window buck framing extensions, WRB, and exterior insulation, and will install the strapping, siding and trim. The builder installed the windows in the opening I extended. I'm building a variation of a REMOTE house. So far it has been fairly economical to build. Installation of the WRB and insulation is not difficult. It does depend, obviously, on how much time you have available.
Michael,
Finding knowledgeable builders who are interested in going above code is a common problem. From their perspective you are asking them to gamble on new practices and materials to do a one-off house that may not generate any more revenue than their standard build. You might be able to overcome some of their objections by suggesting a flat pack or modular approach where a lot of the “green” work is done by specialized crews in a factory. Build Smart is one company, but there are others you could consider that might require Work just as well.
I'm in SE WI and I can feel your pain!
I went thru the same thing about 2 years ago.
The hardest part is finding someone who is willing to do the work the way you want.
I know a couple of people in my area that can and will do a better job.
They all have their little comfort zones, the way they like to work.
One I know does 2 x 6 walls with 2" of foam on the outside.
Another will do anything you want.
If I had to do this again I'd "TRY" and find an architect that is up on energy efficient home building.
And I would work with him by giving him targets of what your looking for.
After I got prints then shop them around for pricing.
Where are you in SE WI, I can maybe give you some contractors both good and one to stay far away from.
Hire an architect who designs efficient buildings. Have the builder build to the drawings. If a builder can't install exterior foam, he's incompetent. If he won't, he's useless. It's not rocket science.
I assume you're like most people. This will be, by far, the most expensive undertaking of your life. Don't settle for some crappy house just because a builder won't build what you want.
Michael,
Stephen offers some pretty sound advice.
Even if you aren't building to passive house standards, PAssive House educated builders are a good start - even if they aren't interested in your build they may have contacts who are. I took the PH Builders Training and have found that my fellow students are a great contact list for various high(er) performance homes. A quick look through the list at PHIUS Find a Builder (http://www.phius.org/find-a-professional/find-a-phius-certified-builder#W) led me to TDS in Madison https://tdscustomconstruction.com/specialties/high-performance-homes/ and Tony Lyons in Milwaukee.
Perhaps ask you local building inspector about any energy efficient projects built recently, and if they know who the contractors were.
To add to Stephen's comments about hiring an architect. The details are important; an architect/designer (of efficient homes) will provide all the details necessary. Following them even more important. This is where you will need to self educate. Unless you find a builder that knows how to build energy efficient homes and understands the importance of sticking to the plan, you will be the one guiding every detail and NEED to be the go to guy to ensure details are being followed according to the plans. You will need to know and understand all the plan details like it is second nature. Constant quality assurance is a must. There was no way that I could depend on sub-trades to ensure my house plans were followed. People in general tend to make decisions based on the information they have at the time they are working and tend to do things the way they always do them. Often times bad decisions result because the builder doesn't see the whole picture, hasn't reviewed all the details, doesn't understand how one step ties to the next...so they make a decision that sets off a butterfly effect that has to be somehow compensated for later down the road during construction.
For example, my framers had to frame in a staircase on an exterior wall. When the first storey walls went up, the rim joist ran continiously around the house. to support the second story wall, they put another rim around the inside of the top plate of the wall where the staircase was to be installed. There was an empty space between the two rims about 4" wide and 9" deep. if the 2nd level subfloor was installed, that would have been left as an empty cavity. There was no way to air seal the detail. When I asked about what the plan was, they said I should just drill holes in the interior rim joist and fill the cavity with spray foam. This would have lead to major headaches. First of all, there was no way to determine if the spray foam expanded uniformly and there was no way to determine if the spray foam was actually sealing all the gaps. I had to ask them to remove the detail and I came up with an alternative method (which I won't get into here) that worked like a charm.
Like Ethan, I also did the PHIUS builders course. It was a small cost and a huge investment. I figured that it is pointless to build a an "energy efficient" house and miss the mark! The plans, their details, understanding and their implementation is the key. Otherwise you end up with an "energy efficient" house that cost you more than a code build house and it performs like a code build house...that would be a horrible situation to be in.
Like I mentioned I've been thru this.
I hired a builder that hung his hat on energy efficient homes.
He had an architect that worked for him so you think that the architect would be on top of it.
Wrong.
You'd think the builder would guide the architect so the job would be done right.
Wrong.
You'd think that his crew would be dialed in on how to build an energy efficient home. That they would be watching the details, The details after all are key in an energy efficient home.
Wrong.
You'd think at the very least the builder would be on the job keeping an eye on the subs and his crew.
Wrong.
Time is going to have to be spent searching for qualified builder and architect. Just because they have experience or claim to be all about green building means nothing. They still can be a bunch of PEA brained incompetents.
The best route is finding a competent well informed architect that is on the same page as you.
Once you have good plans that spell out all the details then at least you can go to builders and they can see what and how its done. It's the best way to get a realistic price and you can shop around. Thats half the battle. Making sure the builder does what hes supposed to is the rest of the battle.
Martin mentioned in his first post about shooting for an air tightness instead of an R value.
In theory I'd agree with him, in reality its much harder to do. You'll have hard enough time getting what is specified on prints for insulation thickness especially in areas that the installation of the insulation determines the R value (spray foam and cellulose). The R value can be seen as the building progresses. Fact is the vast majority of builders never test for air infiltration. Your going to try and hold them to something that they have no experience, something they can't see and something that is going to cost them money to check for. Best method is hire a independent 3rd party to watch over builder that will keep an eye on and work with builder to achieve desired goal. Even then the builder will excessively tack on to the price because your pushing him out of his comfort zone. Best solution might be a time and mat'l charge for certain work. It is the fairest way for all. But you'll have to agree on hourly rates and watch and document time yourself.
All this green building stuff is great in theory but making it happen in the real world with PEA brained general contractors who spend more time on vacations then they do on the jobsite, subs that do things the way they want "cause that's the way we always do it" attitude and don't even bother with looking at the prints, workers who don't care cutting corners as much as possible to make their jobs easier all the while making the next guys job harder and architects who will leave details out of plans cause its easier to and then let the General figure it out. These and more are what your up against.
Been there done that.
I wish you luck Michael.
The best I can do for you is tell who stay away from in SE Wisconsin.
In Zone 6 a 2x6 wall needs at least R11.25 on the exterior for dew point control when air & water-vapor permeable cavity fill is used. Standard 2x6 16" o.c. framing with R20 in the stud bays delivers only ~R13-R14 "whole wall", when the thermal bridging of the studs, and the R-values of the wallboard, sheathing, siding etc are all factored in, so adding that R11.25 is a substantial performance improvement.
If using ZIP-R instead of exterior foam it would have to be the 2.5" version, which comes in at R12.6:
http://www.huberwood.com/assets/user/library/ZIP_System_R-Sheathing_-_Product_Data_Sheet_(R3-12)_v1.pdf
Fastener spacing & types will be important to achieve adequate structural capacity when the OSB layer is on the exterior of 2" of foam, and it may require let-in bracing when going with ZIP-R that thick, but the general instructions shouldn't be too challenging even for newbies:
http://www.ebsbuild.com/wp-content/uploads/pdf/plywood/Zip-SystemR_Sheathing_Installation_Guide.pdf
With an R12.6 ZIP-R approach the whole-wall R will be in the ~R25 range, well above code-min. With an R25 wall, code minimum windows would undercut the whole HOUSE performance by quite a bit, and it's rationale (financially and performance-wise) in your climate to go with U0.20-U0.25 double panes with a SHGC greater than 0.4 which is usually achievable with double low-E glass, with low E coatings on surfaces #2 and #4 (eg. Cardianal's LoE180 + i89.) It's an upcharge from a single low-E U0.28-U0.32 type window, but WAY cheaper than a triple-pane. On the coldest nights when it's well into negative double-digits there may be condensation of room air on the interior surface (#4), which undercuts performance due to the high emissivity of liquid water, but those conditions are the exception rather than the rule in SW WI. Even if you end up building a code-min wall this type of glazing will be both noticeably more comfortable, and measurable in the heating bill.
Thanks to everyone for your feedback.
Martin, while I didn't explicitly mention air tightness, that's the main reason I wanted to use the Zip sheathing. The amount of blogs and posts of great blower door tests using the Zip system have me convinced it's the most cost effective way for me to air seal. As for the R-sheathing, I thought when I priced it out it would be more expensive then the standard Zip + the insofast. I also prefer the EPS of the insofast to the polyiso on the Zip-R, but I'm prepared to compromise however I have to.
Michael
Dirk,
Thank you very much for your warning regarding a builder to stay away from. They were the only ones in this area that claim to specialize in an energy efficient home, and they said all the right things. While I have been leaning towards the builder that I can do some of the work myself, I was on the fence as to whether to go with the "green" builder as they looked to be on target with what I wanted to accomplish. After reflecting on your post, I'm going to sign a contract with the builder that I can control the subs and do some work myself. If I'm taping the zip sheathing, installing the mineral wool, water proofing and insulating the foundation, I'm going to feel comfortable that those items were done correctly.
I think it will be a lot of fun too, certainly easier then when I did much of the same on my 70's ranch I just sold. As my wife reminds me, I have a day job so I'm limited to evenings and weekends.
If I can get contact information for the contractors you mentioned that will do external foam (perhaps the walls and sheathing also), I'd be very grateful. In my ideal scenario I'd do two layers of overlapping mineral wool board instead of foam outside the sheathing, but I can't find anyone who's done it or willing to try, so I'm letting the mineral wool externally go and settling for the foam; as I mentioned the insofast is probably my best bet, but I will revisit the Zip R Sheathing to check on pricing. I liked the Thermalstar One because it was EPS, but you need a special nail gun and still furring strips/rain screen, so I figured that would be too much to ask for around here.
Oh, as far as area of SE Wisconsin, I'm in New Berlin and my lot is about 5 minutes from here.
Thanks again,
Michael
Dana,
Thanks for the information regarding the Zip-R and particularly the windows, I will definitely look into this.
I know there was a post here on the forums regarding Wasco 1400 windows that are local to me, that by choosing a slightly smaller size you could save significantly and they were available with the Cardinal 180 glass you mentioned.
While I'm not replying directly to everyone who posted, I'd like to say again I appreciate everyone's responses.
Hello all,
So I ended up agreeing on Option 4, which is a 2x6 with Roxul and the 2.5 inch of insofast at R10. How concerned do I need to be falling slightly short of the outside R value in terms of condensation? Will a smart vapor membrane like MemBrain be good insurance to lower risk of any issues?
Thanks for any replies,
Michael
Michael,
For a thorough discussion of your question, see this article: Rethinking the Rules on Minimum Foam Thickness.
Regarding Wasco's glass choices:
I see the LoE 180 listed...
http://www.wascowindows.com/wp-content/uploads/2014/10/WASCO-1400_4500-Series-Glass-Options.pdf
... but not the LoE 180 (surface #2) + i89 (surface #4).
It's the second low E-coating, the i89 on surface #4, that gives the additional comfort and performance boost without significantly impeding SHGC.
Regarding the 2.5" exterior foam:
Most Type-II EPS (1.5lbs per cubic foot nominal density) would run R4.5/inch or a bit higher at a mean temp of 40F, and thus would have an R-value greater than 11.25 during weather that matters in your stackup, so you really ARE there. Since the average temp at the sheathing will be about ~40F through the colder part of the winter, the mean temp through the EPS will be lower, and it's performance higher. When the mean temp through the foam is +25F (on a really cold night) the performance of the foam is about R12. I didn't see R values at other temperatures for Insofast, but take a peek at the Type-II column in this vendor's spec, which is a fairly typical R4.17/inch @ 75F mean temp (the FTC labeled R value) , R4.55/inch @ 40F, R4.76/inch @ 25F mean temp through the foam:
https://www.insulfoam.com/wp-content/uploads/2014/04/Insulfoam-EPS-Physical-Properties.pdf
In exterior sheathing/dew-point control applications it's totally legitimate from a design point of view to use the 40F tested R-value rather than the 75F labeled value.
With the drain channels InSoFast is probably going to come in about R0.25 shy of a flat-faced panel would be, so assuming R4.55 /inch @ 40F you'd be at R11.375, less R0.25 = R11.125, just shy of would still meet code-prescriptives at the cold edge of zone 6, and you're at the warm edge of zone 6- it's enough. Just across the border in IL R10 would still meet the code prescriptive. While it doesn't hurt to install MemBrain or Intello Plus, it's definitely not a must.
If you can get documentation on the density of InSoFast or better yet, ASTM C518 tested performance at a mean temp of 40F it would be easy to make this call.