New build in Zone 6a – What’s my best affordable insulation solution?

I’m planning on building a 2200sqft 2 story (+ basement) in Atlantic Canada. Assuming I can’t afford a full ICF build, what are my next best options? From what I gather, it would be a traditionally framed house, with R11 foam and Tyvek on the exterior and batts in the 2×6 cavities (with a vapour barrier?).
Beyond that, do I have any other affordable options?
GBA Detail Library
A collection of one thousand construction details organized by climate and house part
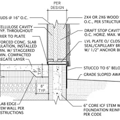
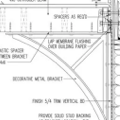
Replies
Hi Zach,
Your plan would work. It would likely get you to minimum R-values for your area, though I don't know what R-values your building inspector will require. Do you?
If by writing "batts" you are talking about fiberglass batts, then this may also be your most affordable route. Keep in mind that they are tricky to install well. Read this article to make sure that you, or your contractor, are installing them right: https://www.greenbuildingadvisor.com/article/installing-fiberglass-right
If lowest upfront costs are the goal, your options are limited. If you open up the budget a bit, you have lots more options including spray foam or dense packed cellulose for the cavities, mineral wool exterior insulation or ZIP R Sheathing, among many other options, which you can easily find on this site.
One more thing. Since you are working on an insulation plan, I assume that you have your air barrier strategy dialed in. If not, make that a priority. Insulation is secondary to air sealing in terms of efficiency and air-sealing doesn't have to cost much at all. Here's a good article on air barriers: https://www.greenbuildingadvisor.com/article/questions-and-answers-about-air-barriers
Hi Brain,
Thanks for the reply. The lowest cost is not the goal, but I am looking for a combination of the best bang-for-your-buck, while still being able to find contractors who can supply the materials and do the work.
Would 2" XPS on the exterior, plus a flash and batt in the cavity be another alternative?
Using rock wool instead of medium density fiberglass for the batts is "worth it" on a number of levels. Using cellulose is slightly lower R, but somewhat greener than rock wool or high density fiberglass due to the fact that it's more than 80% recycled material, and it is sequestering carbon.
Flash & batt is perhaps the MOST expensive way to air seal a wall, and wastes the high R/inch of foam by installing it where it is thermally bridged by the framing. Save the high R/inch foam budget for continuous layers on the exterior side. Seal the framing bays to the framing with a bead of polyurethane caulk or purpose-made sealants around the perimeter of each stud bay, and seal any penetrations of the sheathing with can foam. Seal the seams of the sheathing with purpose-made tapes. Seal the seams of any double-up framing (jack studs, top plates etc) and between the subfloor and bottom plate with polyurethane foam, and any electrical or plumbing penetrations of the framing with can-foam.
Using XPS on the exterior is the opposite of "green", due to the extremely high global warming potential of the HFC blowing agents used (well over 1000x CO2 @ 100 years). As the HFCs diffuse out over a few decades it's performance drops toward that of EPS of similar density & thickness. EPS is blown with variants of pentane, at about 7x CO2 @100 years, most of which leaves the foam and is recaptured at the factory, often burned as process heat fuel. Graphite loaded EPS performs at similar levels to fresh XPS, but doesn't lose that performance over time.
Both EPS and XPS are made of polystyrene, which melts while burning and has a greater environmental impact than polyurethane or polyisocyanurate. Rigid polyisocycanurate board is also blown with low-impact hydrocarbons such as pentane, and has a comparable or slightly higher performance at a given thickness than graphite loaded EPS, at a comparable financial cost per performance level as plain (non-graphite loaded) EPS.
ICF isn't really a less-green way to build the entire house, primarily due to the very high embodied energy/carbon emissions of the concrete, but also the comparatively high environmental impact of 100% EPS insulation. There is a reasonable rationale for using it to build the foundation walls, but only in extreme hurricane zones where only concrete construction would survive for a half-century or more is there much of a rationale for building the entire wall out of concrete.
Dana, I am trying to decide between mineral wool and fiberglass batt insulation for my house. I would love to hear your opinion on the matter! I think I calculated it would cost me about 3-4K more for mineral wool.
What R/RSI value for the fiberglass vs. that of the rock wool?
Low density fiberglass is dirt cheap, but is not worth much. Make sure you're comparing apples to apples when looking at the comparative cost.
Mid to high density fiberglass can approach the performance of rock wool at R20-R21, and R21 fiberglass is about as air retardent as R23 rock wool. An "R19" low density batt in a 2x6 wall really only performs at R18 (RSI 3.2) when compressed to the 5.5" nominal cavity depth, so at a given temperature difference it's conducting 28% more heat than R23 rock wool even if perfectly fitted and perfectly air tight. An R19 batt is barely more than an air filter in terms of it's ability to mitigate air infiltration flows, or even convection currents within the batt. To have "reasonable" air redardency in a 2x6 framed wall with either fiberglass or rock wool look for a minimum of R20 (RSI 3.5). R23 (RSI 4.1) rock wool is
At house fire temperatures fiberglass melts, rock wool doesn't. A small intense fire next to a rock wool insulated wall doesn't burn through to the other side (until the framing does) whereas with fiberglass once the fire reaches the melting temp of the glass it's a matter of seconds before fire has completely penetrated the wall. That's worth something, but what it's worth to you is your call. In Europe almost nobody insulates wall cavities with fiberglass- rock wool is the generic standard, but dense packed cellulose isn't rare.
The polyiso vs. polystyrene flammability issue isn't quite as stark. The kindling temperatures of the two polymers aren't dramatically different, but the fact that polyiso chars in place while polystyrene drips into pools of burning liquid means that fire can spread downward (aided by gravity) much more quickly with polystyrene than with polyiso.
Best bang for the buck for foam is going to be reclaimed or 2nds for the exterior. Polyiso is preffered, but EPS and XPS are good. XPS being the least green by far if buying new, as in don't buy new XPS. XPS uses a blowing agent that has high global warming potential. Check craigslist for the resellers of this stuff in your area.
Have a comprehensive and detailed plan for making everything airtight. Taped and sealed sheathing has generally worked better and is more cost effective than flash and batt. Include in that as much "advanced framing" methods as possible. If you can make it work, frame on 24" instead of 16". Air seal the ceiling. Plan a blower door test to verify air tightness of the shell before insulating the inside.
For the attic, use a raised heal truss or similar and R60 of blown cellulose in the attic. Dense pack cellulose for the walls is a pretty good upgrade from batts if you have decent options for installers. If you end up with batts, check the upcharge to go to rockwool R23 in the walls.
You might want to take a look at this !
https://www.youtube.com/watch?v=mxDSulcLpAE&t=8s
It's a way to boost the R-value of walls without increasing the thickness.
Only you can decide if it's worth the price.
On the house of my son we have almost the same assembly except we added a 2'' insulation on the inside wall stuck between horizontal 2x2. So from inside : sheetrock, 2'' rock insulation, vapor barrier, 6'' rock insulation, 3/8'' plywood, 1 1/2'' styrofoam, air barrier, forenz, cedar shingles. Note that the vapor barrier in not right at the inside but behind the 2'' insulation. In that way , all the electricity passes in the 2'' cavity and a lot easier to do a good job in sealing the vapor barrier.