New 20+ SEER Variable Carrier heat pump w/ Greenspeed Intelligence system creating moisture & performance problems in the crawl

I had to replace 2 -13 SEER HVAC split systems in my house about 2 years ago do to some Sandy storm damage. One split system was a 90% gas furnace with a 3 ton 13 SEER AC and the other was a 2 ton 13 SEER heat pump.
Both the air handlers were originally in the crawlspace, which I hated, and I wanted to come up with a better set up with the new replacement systems. The only option my HVAC contractor could come up with, the way the house was designed, was to combine the 2 systems into one 5 ton 2 zone with damper system and put the air handler at the far side of the house in a storage room off the back of my garage.
The system installed was a top-of-the-line Carrier Infinity Series Hybrid 20+ SEER variable speed Heat Pump with Greenspeed Intelligence and a Infinity ICS Modulating Gas Furnace with 97.2 AFUE. Before the new system was installed I weatherized and enclosed the crawl space area with all new poly vapor barrier and new R19 Batt floor insulation. All the foundation vents and penetrations were sealed. The band and rim joist where sealed and insulated with rigid foam and a Horizon 50 dehumidifier was installed to keep the 2500 sq ft crawlspace humidity in the low 50’s.
I had an early issue with my original HVAC contractors after they installed the new duct system and they improperly wrapped the ducts with reflective bubble wrap with no air gap between the wrap and the metal ducts. It took a while but I got them to eventually come back and remove the bubble wrap and install conventional R8 duct insulation last spring 2014.
I recently started another home renovation project the beginning of this summer and was under the house and noticed that most of the metal trunk line insulation was soaking wet and sagging at the bottom. The closer you got to the furnace side of the house the wetter the metal trunk insulation got. My dehumidifier was doing its job. My moisture meter measured 52% RH in the main crawl. When I got to the end of the duct run closest to the furnace I saw a potential cause to some of the problem where the HVAC contractor had the 8′ wide by 30′ long crawlspace area going to the supply room in the garage totally filled top to bottom with supply and return ducts. I also noticed that the ducts still had the bubble wrap on them with the conventional R8 insulation wrapped around the ducts on top of the bubble wrap.
The RH reading was consistent throughout the main crawl space area although you could tell there was no air circulation getting into the 8′ x 30′ crawl area to the storage room and this also restricted the air flow to the 660 sq. ft. addition attached to the back of the garage.
When I inspected the crawl in the addition the ducts were sweating profusely on the outside and the RH was much higher. What I can’t understand is how the ducts in the main crawl are dry on the outside but soaking wet on the inside with the RH at 52% and the ducts in the addition seem much drier on the inside and sweating on the outside with the RH 10% + higher.
Adding to this mystery there was a section of 12″ return flex in the main crawl connecting to a return plenum, close to the 8′ crawl section going to the furnace, that had over 5 gallons of water inside the flex line. We cut a small hole in it to reduce the strain on the furnace and water poured out from the inside of the flex duct.
So far I have had 3 different HVAC contractors in the crawl to diagnose whats happening and they all seem to be scratching there heads. The one thing that seems obvious to me is that the duct system is definitely not right for my crawlspace. I think there also may be some Carrier performance issues along with some sloppy installation issues.
The install of the new system has created a totally inaccessible problem area along with negating the effectiveness of my dehumidifier reducing the humidity and air flow in the 8′ x 30′ section of the crawl space that feeds the 2 zones from the furnace and it also cuts off air circulation to the 660 sq ft addition crawlspace thats attached to the 8′ x 30′ section.
To make matters worse I have implemented numerous weatherization improvements since installing the new system and have still not seen any benefit in energy savings comparing yearly usage after upgrading from the old 13 SEER systems to the high end 20+ SEER /12HSPF Carrier system.
Some of the suggestions I have gotten are to take out all the metal ducts and install 2″ duct board or foam the metal ducts which would be tough in the crawl., but that does not solve the access and air flow problem. My thoughts are that the system should have been designed to just condition the 3 ton area of the main house and the 2 ton zone to the addition and bedroom over the garage should have had a 2 zone mini split system. This would have reduced the ducts in the 8′ x 30′ crawl space to allow access and air flow.
The problem now in going that way is what can be done with the existing 5 ton split system. I would like to try and salvage what I can from this Carrier system but I can’t seem to find the right course of action to take.
GBA Detail Library
A collection of one thousand construction details organized by climate and house part
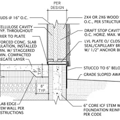
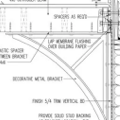
Replies
Bruce ,
where are you in , NJ or NY ? You don't need HVAC contractors a home performance contractor . he can make the proper recommendations contractors and also find any other problems . If you are in nJ , I have the guy for you to contact in Lake Como
One clue--I'm going to guess that the temperature in the main crawl is higher than the temperature in the addition crawl. That would mean that the dew points in the two spaces are more similar than the relative humidities, so you can get dew in either space.
When the A/C first turns on, the moisture in the air in the insulation can condense on the duct, but that should be a small amount--drops not gallons. In order to get substantial condensation, new air has to be flowing into the insulation. The wrap on it is supposed to prevent that. If there are tears here and there and poorly sealed ends, that would explain some of it. But 5 gallons sounds like there must be air flowing through the insulation pretty intensively. Perhaps there is a pressure difference between the two spaces, maybe driven by duct leakage, and with the opening mostly blocked, the air flow goes through the duct insulation.
If Richard's recommendation of a home performance expert works out that could be your best bet. If he can measure duct leakage, pressure differences, etc., and if he understands how moisture in air works, he can probably figure it out and recommend a solution.
Bruce,
We have to go back to first principles when analyzing a situation like this.
To have condensation, you must have humid air that is contacting cold surfaces.
If this type of condensation is happening on a duct, there are basically two possibilities.
If you are talking about a return duct, the duct seams may be poorly sealed. That means that the leaky seams are pulling humid air through the poorly sealed insulation jacket, and the humid air is contacting cold duct surfaces.
If you are talking about a supply duct, then duct insulation jacket must be poorly sealed, allowing humid air to penetrate the fiberglass duct insulation and contact cold surfaces.
Note to GBA readers: this case is a textbook example of why you want to install ductless minisplits instead of a conventional forced-air system. A high SEER rating doesn't mean much if the duct system has flaws.
Hey Martin, I just took my moisture meter into the main crawlspace and the rear addition crawl to measure temperature and RH. The outside temperature is 80 deg with an RH of 79%. The temperature in the main crawl where the Horizon 50 dehumidifier is working was 74deg with an average of 62%RH. On the front side with the airflow direction of the Horizon it was mid 50sRH on the back side was mid to upper 60s with the humid air coming in from the open access door. On normal days with lower humidity the average RH is in the lower 50s. The addition readings were much higher due to no airflow from the horizon. The temp was 77 deg with the RH at 80.5%. The duct insulation in the addition was beading up with sweat on the outside which is to be expected with the dew point in the low 70s. The dew point in the main crawl was in the low 60s and there was no moisture on the outside of the insulation but the metal trunk lines located on the airflow side of the dehumidifier and closer to the furnace, where the RH is in the 50s, are soaked on the bottom of the ducts and sagging with accumulated moisture. The ac conditioned temperature coming out of the ducts now is 60deg with a 73%RH. The large flex return coming off the return plenum in the main crawl in space zone 1 had 5 gallons of water which had accumulated on the inside of the duct, restricting airflow back to the furnace. That's why we cut a hole in the duct to drain it. I am a home performance contractor and I am in the process of implementing an action plan to upgrade the vapor barrier in both crawls by taping all seams and running barrier further up the block walls. I need to crank up the setting on the horizon to further lower the humidity during the summer season. The Horizon is rated for being able to dehumidify a crawlspace up to 3500 sq.ft.. My crawl space including the addition is 2500Sq ft.. The poorly designed duct system has created issues with proper air circulation so I might be putting in another Horizon dehumidifier in the addition along with ducting the humidifier in the main crawl. I also may end up foaming the foundation walls. I just had a certified Carrier dealer look at my system and he thinks there very well could be a problem with my downflow furnace leaking from a cracked pan, missing factory plugs or the fan blowing condensation into my duct system. That is what I have thought all along. The ducts in the addition were sweating on the foil outside of the insulation on the all the ducts including the flex runs but the inside of the insulation was dry. The ducts in the main crawl were sopping wet on the bottom of the metal ducts but not sweating on the outside and the insulation on the top of the ducts seemed dry. We will be running more tests on the system after the weekend. I'll keep you posted on what we find. I do agree with all your comments. If I had known that the duct systems for the 5 ton was going to cause access and airflow problems I would have put in the mini split for my 2 ton zone and downsized the main system. Thanks for all your feedback
The fact that your humidity and temperature in the addition crawl are so close to outside likely means that it's just in equilibrium with outside air, rather than being driven by moisture coming in through the block walls. It can only help to improve the vapor barrier, but I'd focus on the air sealing aspect more than the vapor barrier aspect, even though you might be doing same taping of seams for either purpose.
Can you squeeze some smaller uninsulated ducts between the big ones blocking the opening, and put a small fan in one to circulate air between the two crawls, so that one duhumidifier serves both?
The return being soggy in the space that is dehumidified well is a little weird--the return air shouldn't be below the dew point of the dehumidified basement. So the theories that the Carrier dealer has sound like they right direction to pursue, although without seeing the system layout it's a little hard to follow.