Need help reducing energy costs

I have a ranch home in climate zone 5a (Northern NJ). It’s a ranch, with a partially finished attic, approximately 1600sqft. Primary heat source is propane via hot water baseboard, with a gas insert fireplace, and electric baseboard in the attic. This is my first year in the house, so I don’t have historical data, but this year we’ve been averaging approximately 300 gallons of propane use per 5-6 weeks, which is quite expensive!. In November I had a high efficiency condensing boiler with indirect hot water heater installed due to the age of the previous system and condition of the chimney liner. We have four heating zones on the main level and keep the thermostats at 59 with the occasional bump up to 62 in the living room in the evenings. I do not use the electric heater or the fireplace.
The house itself was built originally in the mid 40s and is concrete block construction. Additionally, most rooms have bay windows and there are a number of skylights, all of which were added I believe in the early 90s. Attic is, unfortunately, vermiculite insulation so I’m not going to be doing anything much there with the exception of replacing some recessed lights on the knee wall with sealed/IC units. The exterior walls do not have insulation, though I believe that solid foam insulation was installed under the siding when that was redone.
My question is…where do I go from here? My long list of items that I would like to do would include:
-Vermiculite removal so that I can properly air seal and improve attic insulation
-Mini splits for heat/AC (no AC currently) with the gas boiler as backup for the very coldest days
-Improved crawlspace air sealing/insulation
-Insulation of exterior walls via either blown in cellulose or removal of drywall and use of fiberglass batt
-Fireplace seems incredibly drafty…I don’t know anything about gas insert fireplaces, but I’m sure that improvements could be made there
-Possible replacement of some windows, better insulation around them (the window stool area is typically the coldest surface in the house)
Appreciate any suggestions…
GBA Detail Library
A collection of one thousand construction details organized by climate and house part
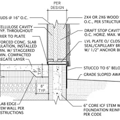
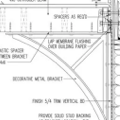
Replies
Eric,
The first step for a homeowner in your situation is to hire an energy auditor, energy rater, or home performance contractor to conduct an energy audit. (You should choose an auditor who has been certified by RESNET or BPI.)
A thorough audit always includes a blower door test and a thorough inspection of your home; in most cases, an auditor will use an infrared camera to determine your building's flaws.
After the results of the audit are analyzed, you will receive a customized list of suggested retrofit measures. This list will be tailor-made for your house, and it should be prioritized, with the biggest-bang-for-the buck measures at the top of the list.
In general, air sealing is almost always at the top, or near the top, of such lists.
You may want to read the following article: Energy Upgrades for Beginners.
Thanks. That's definitely something that I'll be doing in the near future. I've read a lot about the different approaches, but I think it would definitely be helpful to have an outside person come in and do an assessment.
At NJ outdoor temperatures and utility rates heating with a better-class mini-split will cost less than half what it costs to heat with a condensing propane boiler. If there is at least one decent sized zone that's reasonably open enough to heat with a mini-split, it's probably cost effective to install the mini-split even BEFORE the weatherization efforts (or even the audit) is done.
With $4 propane in a 95% efficiency burner you're getting about 21,850 BTU of heating per $.
With a cold-climate mini-split with an HSPF of greater than 10, in a NJ climate same 21,850 BTU can be delivered with about 2.5kwh of electricity use, worst case averages. Even when it's +5F outside it'll take less than 4kwh to deliver 21,850 BTU, and when it's 40F out it'll take less than 2kwh. Average residential retail electricity NJ is about 15 cents/kwh, so that 2.5kwh average means it cost about 38 cents on the dollar to heat with mini-splits instead of condensing propane, a better than 60% reduction in heating cost.
To size it for the zone, do an I=B=R type spreadsheet heat load calc on all of the window/attic/wall areas for the zone you think will be covered by the mini-split, using a 50F or 60F delta-T between indoor & outdoor temps. Windows that are single pane get a U-factor of 1.0 BTU /hr per square foot per degree delta. Uninsulated CMU walls also have a U-factor of about 1, but if there is any siding at all on it with an air gap between the siding & CMU (or 1x furring with wallboard or plaster & lath) it cuts it down to U0.55-U0.6, and if has both back-vented siding AND a trapped air space behind the interior finish wall it could be as low as U0.35. (Tell us what the stackup is and we can estimate a U-factor for you.) If low-E storms can be fitted over the windows it'll lower the window U-factor to about 0.35 for far less cash outlay than a U0.35 replacement window, and it will improve the comfort issue next to windows by quite a bit.
Knee wall attic spaces can be notoriously difficult to air seal, and it may be reasonably cost effective to insulate at the roof deck, but it gets complicated.
Thanks, I really appreciate the detailed response.
Fortunately I've only been paying $3 for the 21,850 BTU but that is still a 2:1 difference which is a bit of an eye opener. We do have essentially an open plan that I think would be well served with a single unit. I actually had someone out to give me an estimate for that installation as well as the boiler replacement and his first cut guess was a 12k unit for that space.
I am not certain about the exact wall composition, so I'll have to have a closer look. On most of the exterior walls we have two layers of drywall and then the CMU wall with a normal I guess 3.5" of uninsulated space in between. The exterior is vinyl siding and I think that there are something like 1/2" polystyrene sheets underneath (based on what I found with the spare siding material). I will try to confirm this as well. So if I'm reading you correctly, it sounds like 1x furring with wallboard and associated air gap. I'm not sure about back-vented siding...haven't heard this term previously. Here's a picture from this winter for whatever inferences may be drawn from the visual:
http://farm6.staticflickr.com/5493/12509549445_ce6c466672_b.jpg
Do you have a link to an I=B=R spreadsheet? I would definitely like to give it a try.
Thanks again.
Icicles over your bay windows and on the back corner, along with obvious details indicating no roof thickness over the bays means no R value there. It’s hard to tell with the fresh snow fall but if you have ice buildup in your gutters, you have a roof melt usually stemming from insufficient insulation and air-sealing. Are you knocking off icicles often this winter?
Close the barn door, the cows are getting out.
I have no doubt that everything that you're saying is true. There are definite air leaks and insufficient insulation in many of the areas that I'm sure aren't helping with any ice dam issues. Especially in the bay windows...I don't know anything about how those are built/insulated or how they're supposed to be. Anything that I can do with those? However, none of the issues showed up after a few days of snow on the roof, it was really just after the two to three incredibly severe freezing rain storms that we've experienced here that the ice dams/icicles started showing up. Since we had a bit of a thaw the last weekend things have been largely ok.
NJ Home Performance with Energy Star is one of the most generous rebate programs in the country. The funding for customers without either central cooling or natural gas is a little sporadic, and currently depleted. However, it would be worth keeping an eye on to see if the program picks up any more funding propane customers. The vermiculite insulation would also pose a problem. Not certain, but suspect that were you to install a ducted heat pump you would gain program eligibility, and doing so in a conditioned crawlspace might be a reasonable alternative to mini-splits.
Not sure on contractors in your area, but were you to go with an HVAC specialist I'd recommend you limit the shell work to program minimums (air sealing and health/safety).
http://www.njcleanenergy.com/residential/programs/home-performance-energy-star/benefits-and-incentives
Thanks, yes I attempted to take advantage of the NJ rebates when I put in the new boiler/hot water setup back in November, but didn't get anything back so it's not really looking promising at this point. The company I'm considering going with for the audit/possible work has a lot of information regarding the various incentives so I'll see what they have to say.
What is the rationale for limiting the shell work to program minimums? Just straight ROI?
Appreciate all of the responses. I find all of this fascinating, although being in the midst of spending close to $1k a month to heat a fairly small house takes a lot of the fun out of the learning process! :)
An I=B=R spreadsheet is something you build yourself using a standard tool like Excel or thethe freebie found Open Software Foundation suite of office tools. To set it up you need to measure up the square feet of each type of exterior surface type in each room, establish what a reasonable delta-T is for your location (70F minus the 99% outside design temp works, but 10F lower than that would still reasonable for sizing a mini-split.) Then it's a matter of muliplying the square feet x U-factor x delta-T to come up with the heat load. Breaking it up room -by-room or zone-by-zone is more useful than a single whole-house version.
For example, say you have a 18 x 15' living room on the corner of the house, with two 6x8' single pane picture windows, no exterior doors. Assume also that you have 4" of vermiculite on the attic floor of a vented attic, with half-inch ceiling gypsum and 3/4" plywood roof deck with composite shingles. The U-factor of that stackup is about 0.1 BTU/hr per square foot per degree-F difference. Say you lived in Patterson, where the 99% outside design temp is +10F (http://www.energystar.gov/ia/partners/bldrs_lenders_raters/downloads/Outdoor_Design_Conditions_508.pdf), and you keep it at 70F indoors, for a delta-T of 60F. The ceiling area of an 18' x 15' room is 270 square feet, and the ceiling losses are then:
U0.1 x 270' x 60F= 1620 BTU/hr
The U-factor of the windows are about 1.0 BTU/degree-ft-hr, so a pair of 6x8's would be 96 square feet for window losses of:
U1.0 x 48' x 60F= 2880 BTU/hr
The wall stackup as described with 1" of gypsum mounted to 1x furring (?) on 6" CMU and continuous half-inch of EPS foam under vinyl siding runs about U0.2. Assuming 9' wall height and 18' + 15' = 33' of exterior wall you're looking at 330' of gross wall area, less the 96' of window means you have 234' of wall, for wall losses totaling:
U0.2 x 234' x 60F= 2808 BTU/hr
Add it up, the estimated heat load for that room is ~7300 BTU/hr
Doing it using a spreadsheet tool that you can keep editing allows you to pay "what if" and "before/after" upgrade kinds of assessments by just changing the U-factor of the component that is being upgraded. Adding up the "after" picture heat load of the collection of continguous rooms that could be point-source heated with a mini-split would give you an idea of what size to be considering.
The +10F output of a pretty-good 1 ton like the Fujitsu 12RLS2-H or Mitsubishi MSZ-FE12NA (or the new MSZ -FH12NA, which has substantially higher efficiency) is a bit over 13,000-17,000 BTU/hr, (and these particular units still have a known rated output at -13F.) The output @ +10F of the 3/4 ton versions of those series is about 10,000-11,000 BTU/hr, etc. In my neighborhood a full turn-key installation of a cold-climate 1-ton mini-split would run between $3.5-4K, and a mostly-DIY installation could come in at around half that, if you're up for it. If you're burning through 1000 gallons of $3/gallon propane a year (sounds like you probably will) and can cut that by more than half with a mini-split (likely) that costs only half as much to run, it means you'd be saving more than $750/year, and the thing would essentially be self-financing in 5 years or less at the full-turnkey installed price, under 3 as a mostly DIY.
That 20%+ internal rate of return is better than you'll get out of most building envelope upgrades, though they are still well worth doing, but for the immediate bang/buck the mini-split is probably the right place to start. It helps to have the building upgrade plan sketched out first, so you can better assess what the "after" picture heat loads are going to be, but if you're burning through $500-700/month in propane you don't want to spend TOO much time nailing down the load numbers to the last 200 BTU/hr. Even if you over or undersized it by one size within a series it'll still work pretty well, and take a big bite out of the propane bill.
If you can, install the exterior unit in a location protected by the rake of the roof under a gable end, to avoid roof-avalanche burial or icicle/ice-dam fall. It's also better to mount it so that it's above the historical peak snowpack depths in your neighborhood. If adding more isn't likely , bracket mounting on the wall under a gable overhang would be best, but you think it's remotely possible that you'd be adding a couple inches of exterior foam you may want to install that foam behind your bracket mounts as part of the initial installation. It doesn't look like you have sufficient overhang to fully protect the unit from the elements, so if you install it under eaves rather than the rake it's a good idea to build a little shed-roof/awning to protect it from whatever slides of the roof.
Eric - I'm pretty certain that you'd be eligible for the program if you installed a ducted air-source heat pump. Not a bad way to go for someone with a crawlspace under a ranch. Although without potentially $15,000 in rebate and loan money the mini-splits are probably a better choice.
My comments aren't based on ROI. I do a lot of work in the NJ program in southern and central NJ. It's much more difficult to retrofit buildings than most people realize.
Dana, thanks. Simple enough! I put together a spreadsheet this morning with approximate values and I'll do some measuring/investigating tonight to get the actual sizes and approximate insulation values. There are a few things that are going to be challenging to account for but, like you said, it should be close enough for these purposes. It looks like a mini-split is in my future, especially since I don't currently have AC. I'm doing some research into installation now. It looks feasible especially with some help.
Jesse, thanks for the response. That makes sense...focus on the biggest bang for the buck and do any shell work when it makes sense to based on other potential renovation/repair work.