Natural Gas Leak Discovered During Blower Door Testing

I am the un-proud owner of a new home constructed 1 year ago. I have terrible problems with air leakage particularly from the attic where blown cellulose is used. Due to this problem and after reading your columns, I called a BPI certified Energy Audit Company to perform a blower door test.
Prior to testing the company came and turned off all the furnaces and hotwater heater. The gas dryer and stove were not running.
During the blower door test run at 50 Pa, I began smelling natural gas. The test was immediately stopped and the smell dissipated. The natural gas hand-held detectors were unsuccessful in detecting a leak with the blower door turned off. The operators then turned the blower door back to 25 Pa, and behind one of the walls the detectors isolated the area of the leak. The problem however is that there are no gas lines located behind this particular wall where the leak was detected.
The plumber who originally installed the gas lines later came out and without the aid of the blower door, said confidently he couldn’t detect any leak with his detector.
What do I do now? It seems like the natural gas leak is only detectable with the blower door in place and operating. I am concerned since based on the results of the audit I believe I am going to spray foam the attic and turn it into a conditioned space. I don’t want to create a closed envelope with combustion hazard.
GBA Detail Library
A collection of one thousand construction details organized by climate and house part
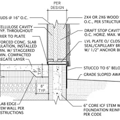
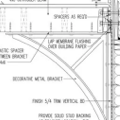
Replies
Kevin,
There are many possibilities. The only way to solve this mystery is more diagnostic testing.
Many things can smell like natural gas, including a decomposing dead animal. Perhaps there is a dead animal in your wall or floor, and the blower door depressurization pulls air past the corpse.
I would do two tests on the gas piping. One, disconnect all of the appliance connectors from the piping, install caps in their place. Disconnect the meter and install a test cap with a pressure gauge. Pressurize the piping with compressed air and see how the gauge behaves. It should be possible for the piping to hold pressure with no drop for a long period. Two, reconnect the entire system and fill it with gas. Attach a manometer to one of the appliance shutoff valves using the side tap. Watch for pressure drop. A qualified gas plumber should do both of these tests.
Also, your builder and plumber should be doing these tests/repairs at their cost.
As a builder, a leaky attic is a quality issue, but a leaky gas line is a serious safety/liability issue.
I would double check with a gas sniffer before going to the pressure test. Especially the stove, water heater, and dryer. Have someone take the time and go around all exposed gas fittings throughout the house. A good sniffer will be able to pick up a leak.
I don't see the point of sniffing any more. A possible gas leak needs to be ruled out using pressure. A sniffer (I have one...) is a useful tool for finding leaks, but it isn't the same thing as pressurizing and making sure that pressure is held. Without doing that you are not going to be sure.
With all the appliances connected, it would be simple to run a low pressure test, assuming someone thought to install a ported shutoff valve somewhere. In most cases it just doesn't take that long to set up a high pressure test.
As a follow-up and for clarification -- with the blower door set at 25 Pa, a handheld natural gas leak detector unit (the one's which beep and light up) -- detected a natural gas leak (Sorry I don't know the brand of the units however they were the one's the energy audit company used). Not only did it small like natural gas, two handheld detectors reported positive findings. The detectors looked something like this one pictured here: http://www.trutechtools.com/Bacharach-Informant-2--Combustible-Refrigerant-Leak-Detector-DELUXE-kit_p_1261.html
As far as pressure gas line test, I assume this should be done by the builder/plumber? Both the plumber/builder at this point have been very resistant to doing any further testing.
Side comment: As far as the leaky attic and the massive airleaks detected via use of the blower door/thermal imaging, the builder states he followed all local code rules and the code inspector passed his work. The cost for me to remove the blown-in insulation and spray foam the underneath side of the roof deck is estimated to cost me anywhere from $25K to $40K depending on company, type of foam (open/closed), amount of drywall that needs to be removed to access certain areas of the attic, etc. The builder has informed me that if I choose to go this route, I'm responsible for all the costs associated with this intervention.
Re the air leakage, it would be interesting to know what code was in force at the time in your jurisdiction, and whether it was really met. Locally, the last round of energy code had non-specific language about sealing of air leaks, but no standard was set. I've inspected a couple of houses with large leakage where I do not think even the most basic air sealing was done and that the owners would have a very good shot at proving that the intent of the code was not met, even though there weren't specific work items listed in the code.
Anyway. it's sad that your builder won't chase down a gas leak, ridiculous actually. The plumber is a little less suspect, because his work probably was pressure-tested during construction, and someone could have shot a nail into a pipe after he was done and gone. Someone competent should test anyway.
If you have an attic, air leaks can be fixed for a lot less than $25K. Cathedral ceilings with drywall are more problematic.
Kevin,
For information on code requirements for air sealing, see New Air Sealing Requirements in the International Residential Code.
My bet is while you are depressurizing the house sewer gas is entering the house through the basement floor drain. Check to make sure all your plumbing drains have appropriate traps and make sure they are filled with water.
measure the depth of the cellulose in the attic. this will give you the R-value. Cross reference it with the code. The conservation tact would be to just move sections of the cellulose and airseal. Then replace the cellulose. It shouldn't have to be disposed of, seeing as how it is practically brand new.
I think J. Chestnut has it. Drive to the grocery store with an empty coffee can in your car. Buy four little bottles of peppermint extract from the bakery section. Place them un-opened in the coffee can and rest it between the truck motor and the hood so they get nice and warm as you drive home. With out entering the house climb up on the roof and pour all that peppermint down the sewer vent. You will now smell like a Christmas cookie so have someone else sniff around inside the house for peppermint smell, run blower door or range hood as required. Replace wax gasket at base of toilet that smells like Christmas. Been there, done this, it's why my hair is this impressive shade of gray and so thin on top where I pull on it.
Had a situation a few years ago where the client's house started to stink shortly after they had the septic tank pumped. Removing the solid layer on top of the tank allowed sewer gas to enter the house through an uncapped pipe left by a hack owner/builder in the wall. With the solid layer the gas was not strong or plentiful enough to be noticeable, but without it... look out! The smell was not what I would consider a gas-leak smell, but it's a possibility worth checking. We ended up using a salvaged bath fan to push smoke-bomb smoke down a vent on the roof, and then found it coming out of a wall. There was a test tee on the sewer in the crawl space, so capping it was easy.