Nail Laminated Slab on Grade?

The conversation around slabless slabs has been very fun to watch progress.
By my estimation a constructed on site 2×4 NLT floor would cost about 5 to 6 dollars a SQFT. This could serve as both the subfloor and finished floor. Seems on par with concrete but better for (C02) and better in comfort especially if treated as a slab on grade over ridged insulation. If used as a finished floor it does very well on the affordability front.
Has anyone seen anyone do this yet?
With appropriately sized frost wings and site drainage my understanding is there is no need for a turned down slab?
GBA Detail Library
A collection of one thousand construction details organized by climate and house part
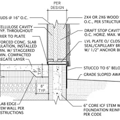
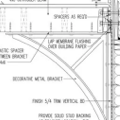
Replies
Hammel,
Laminated slabs are typically glued and screwed. You would have hard time getting the sheets tight and level using nails. I think you are pushing it trying to use the plywood as the finished floor. You would need to use something like baltic birch as the upper layer, and you are facing the problem of exposed fasteners on the finished surface, and that wood or wood based flooring needs periodical re-finishing, which isn't possible with plywood.
You wouldn't need a turned down slab, but you still need a way to take up your structural loads, which is usually concrete stem-walls and pads for point loads.
Thanks for the reply Malcolm, I think it wasn't specific enough.
I'm thinking of 2x4's on edge nail laminated together. I suppose it falls under the mass timber designation.
Deleted
Hammel,
I could see using manufactured CLT floors, but site nailed lumber would need to somehow deal with the huge initial and season movement you would get. Unlike hardwood floors, which are kept back 3/4" from walls, the nail laminated floor would extend under demising walls and span uninterrupted over the whole area of the house. I'm not sure how you would detail that.
I'm sorry if both my answers sound discouraging, I'm just not sure either are good ideas.
That's a very fair point. The first thing that comes to mind would be framing the NLT slab inside of a built up plywood "footer" on the same plane as the NLT.
This doesn't address the Demising walls. But I would question how much expansion and contraction would occur in the slab under a 2x4 wall plate? I could be way off base on that though.
Hammel,
The hardwood flooring that gets an expansion gap starts as kiln dried material acclimatized to the house's eventual indoor humidity. You aren't getting that with nail laminated 2"x4"s. The shrinkage will occur both over the entire floor, and between the individual pieces. Wood used that way in applications that want a similar smooth surface - like butcher block counters - has to be glued.
Any movement of the slab will do one of two things at the demising walls. They will either move with the wood slab, meaning somewhere the walls will need to separate from each other, and become slightly out of plumb. Or they will stay where they are and the slab will move below them, meaning they aren't anchored to anything.
I'm also still having trouble understanding how interior load-bearing walls or point loads get transferred to the footings below.
I know this is a bit of a reactionary sentiment - and if everyone followed this advice we would never have any innovation, but if you don't see something being done, there is probably a good reason for that. If I was going to pursue this idea, I'd first try it out on a small outbuilding where you could find out the downsides and figure out how to deal with them - and decide whether the approach makes sense or not.
Solid points again thanks Malcolm!
Perhaps the best application for this would be on second floors with exposed ceilings on the first floor. The expansion and contraction could be better contained in smaller sections.
I agree there probably is a reason we don't see this in residential construction. It does exist in commercial buildings but it's not common.
On interior load bearing walls. The NLT would be laying on insulation overtop of gravel like a concrete slab. I would think a wall plate perpendicular to the 2x4's on edge would provide more than enough support? For slab movement under the wall plate perhaps the plate could be carriage bolted to the NLT slab with a larger oval hole in the slab to allow movement and large washers on the bolt? Hopefully over time the wood moisture would find equilibrium and the potential for loud noises between with wall plate and moving slab would diminish.
Overall you are right, this needs to be done in a small outbuilding first!
In the 1970's a popular look for modern/rustic houses was to use 2x6 tongue and groove for the floor on the second floor and the ceiling of the first. It's also popular if you want the underside of roof sheathing to be the finished ceiling.
It went out of fashion for several reasons. It's not bad as a ceiling, but as a floor it had a tendency to cup and warp and squeak, and the cracks would open up in the winter. But most important, that space between ceiling and floor is useful, often essential. Without it you're struggling to find a way to run wiring and plumbing.
I grew up in a timber frame house my dad built. 2x6 T and G.
You're right on the the ceiling cavity being valuably space. He did solve for that by doing drywalling between the beams on the first floor ceiling under the second floor bathroom. The bathrooms were stacked so it didn't feel odd to only have a certain area of the ceiling dropped because it was already a unique space.
Some noise on the floors but not any cupping or warping issues with the TandG but it was a pretty stable temperature SIPS house.
The wood moisture doesn't find equilibrium unless the inside air moisture finds equilibrium.
It's common for houses to be 60% RH in the summer and 40% RH in the winter, even though the temperature is relatively constant. Depending on the species wood can change width across the grain by as much as a quarter inch per foot with that humidity change. Did you know your house is actually taller in the summer than in the winter?
Framing lumber just isn't going to make a very good floor. It's soft, it has knots, you're going to have trouble getting it to lay flat. You're going to have to sand it extensively, and it won't take finish well and will constantly be producing splinters.
Half inch CDX is $25/sheet right now, two layers of that is $1.56 per square foot, then finish with a regular flooring. For the same money you'll get a much better result.
DC, you're probably very very right in this assessment of using CDX as the slab and regular flooring on top. To be honest it's the way to go.
I would disagree with framing lumber as the finished floor being untenable though. NLT floors are already in use in commercial buildings. I understand running over it with a drum sander would be needed, but (and this is purely subjective) I think 2x4's on edge have a beautiful grain pattern! I don't mind dents in my floors and there is plenty of depth to accept the dents.
I'm always up for innovation, and I think this could be a viable idea. I would break the NLT into sections of say 18" to 24" wide, with a plywood spline where the sections join, and cork set into the joint once the wood has reached its lowest wood moisture content (i.e., has shrunk as much as it's going to.)
I would still expect some cupping, warping, splitting, etc.. It won't be a picture-perfect floor. But it would have character.
We had a project manager involved with the Kendeda Center on our BS+Beer Show a while back. They used NLT: https://youtu.be/Ksjd7G2Ba3c?si=SNlcIOuU5uDq20j4. NLT discussion starts about 19 minutes in.
Very good idea on a cork filler. The BS and Beer video was very interesting as well. It makes me wonder about the expansion and contraction as they mentioned "screwing down the panels". Perhaps sealing the whole panel in a urethane coating or something else I'm not aware of greatly reduces expansion?
Sealing wood slows its movement with changes in humidity, but I don't know of any finishes that totally prevent moisture absorption/loss. Maybe an epoxy like West System would, but it would be very expensive. It's a lesson I have learned the hard way too many times: wood moves with changes in moisture, period, so plan for it.
If you know the species, moisture content and typical humidity ranges for your area, there are formulas that can predict movement fairly precisely.
I have seen this used in old commercial buildings. Essentially post and beam construction with 2x6 NLT floor.
The top surface is always some kind of flooring though, some of the flooring is 100year old so must have been original. My guess the 2x6 would not hold up well to traffic.
They do creak a fair bit, I guess all those nails plus wood shrinkage over time. Maybe if you glue them as well but then it won't move as freely which might create other issues. The radial shrinkage over time is not insignificant, so Michel's suggestions of smaller section is probably a good one.
All the new commercial stuff uses fancy lumber for even height and look, I don't think this is something you can pull off with framing lumber without a lot of culling.
If you want solid, two layers of 7/8" OSB and you can drive a car over it.
Thanks Akos, good to know on the creaky-ness. What sort of commercial buildings were these? I'm picturing manufacturing?
Yes I do think two layers of sheet goods would be a very strong way to go. I'm very interested in a value engineered solution to the slab on grade with the slab as the finished floor.
Sheet goods just don't cut it as a finished floor. But perhaps inexpensive engineered hardwood flooring really doesn't add too much expense.