Impermeable over permeable WRB

Hello, I’ve seen other posts on this topic, but I wanted to chime in with a specific instance and hopefully get some feedback.
We are designing a single family home in Philadelphia, PA with Blueskin VP100 over osb and rainscreen siding.
The siding contractor added a synthetic roofing underlayment (Topshield Securegrip) between the blueskin and the rainscreen siding.
My immediate reaction is that this will cause condensation and moisture to collect within the wall which is obviously counter to the purpose of using a vapor permeable weather resistive barrier.
Curious if anyone has any experience with this situation and if there are any remedies short of removing the non-permeable layer and reinstalling the siding (such as adding vents, etc)?
Thanks in advance for any feedback.
GBA Detail Library
A collection of one thousand construction details organized by climate and house part
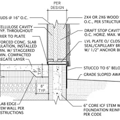
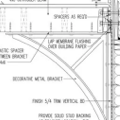
Replies
Hi LPHL.
First, understand that this will not "cause condensation and moisture to collect within the wall." That would be the result of air or vapor getting into the wall assembly and finding a condensing surface at or below the dew point temperature. So, when those mechanisms are controlled (and rain is kept out), you won't have wet wall problems.
The concern with the low-perm WRB is that if the walls do get wet, for any reason, they won't be able to dry to the exterior. If that is problematic, then you need to remove the roofing underlayment.
What type of insulation is in the walls? Is there an interior vapor retarder?
Thanks for the quick response Brian!
The plan was for standard R-22 batt insulation with integral vapor barrier. Assuming a good installation, the blueskin in itself will help to eliminate air leakage and potentially reduce trapped condensation.
Are there any other mitigating steps short of removing the underlayment?
Will this work? Maybe.
Is it a bad idea? YES.
That underlayment is almost a true vapor barrier, cold side vapor barriers are bad idea in any heating dominated climate as it becomes the condensing surface for interior moisture with no way to dry towards the outside eventually causing sheathing rot.
About the only way to have the assembly work is by doing a flash and batt with 2" of closed cell spray foam on inside the wall. I think it is much cheaper to remove the underlayment.
@Akos, We are discussing closed cell insulation as a remedy as the contractor is fairly intent on
not removing /reinstalling the siding/ underlayment.
My concern is that closed cell insulation would keep moisture out of the wall cavity, but then you would have osb in between two vapor barriers (closed cell spray foam and roofing underlayment), which could lead to sheathing rot... Is that avoidable?
I should also note that we were able to catch this issue mid way through the installation so it is isolated to two of the building's four elevations.
It is fairly common to have the roof sheathing between SPF and impermeable underlayment. Provided the sheathing is dry when installed, it works fine.
With a wall, your issues are with bulk water leaks. Any water that makes it behind your WRB will take a very long time to dry out. 2" SPF is still a bit vapor permeable, provided you don't have interior poly, it will allow for a small amount of drying towards the interior during air conditioning season.
So if your window/door flashing details are good, the flash and bat should work fine.
@akso are you suggesting flash and batt vs just spf only because of the slight vapor permeability?
Flash and bat is mostly for cost. The extra bit of drying is a bonus in your case.
The full SPF and SPF+batts have almost the same assembly R value, so you are not really getting anything for your extra SPF dollars.