Moving forward after finding moisture (and the beginning of mold) in new construction wall cavities

I’m looking for advice (and a little comfort) for the following situation:
We are in the process of building our own home… slowly.
Our exterior wall as designed is as follows:
Wood clapboards
1x strapping
felt paper
2″ foil faced polyisocyanurate insulation (taped joints)
1/2″ plywood sheathing (taped joints) (dedicated air barrier)
2×6 stud walls with Roxul batts
1/2″ gyp bd, painted
We have all of the ductwork in place for an HRV, but it is not yet installed.
We have been cooking in the house but running a dedicated range exhaust when we cook. We do not shower or sleep in the house. Our temperature and humidity ranges between 61 and 70 degrees, and 40%-46% humidity.
Now here’s the problem: We have been slowly picking away at installing the roxul and drywall, and had various stages of completeness throughout. None of it was to the point of paint. We recently went to move a section of the roxul in an open cavity and it was soaking wet and beginning to mold behind it. In the end we removed every piece of drywall and insulation on the entire second floor. Cavities were all a variety of moistness, with the worst have the beginning of mold spots forming. The south side near the wood stove chimney was the best case, the North side on the lower part of the wall was the worst case.
We sprayed and scrubbed the cavities with Borax and plan to leave the cavities open for at least a week. We have upped the temperature to stay nearer to 68-72 and have been exhausting the house to get the humidity down closer to 35%.
SO, (2) questions:
1. Are we approaching the remidiation the right way?
2. Do we have a wall that is destined to fail?
Any input is appreciated,
Heidi
GBA Detail Library
A collection of one thousand construction details organized by climate and house part
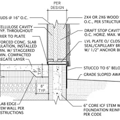
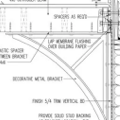
Replies
Heidi,
Your approach seems sound. However, we can't tell you whether your chosen wall assembly is "destined to fail," as you put it, until you tell use your location or climate zone.
Right! I knew I'd miss something...
We are Central Vermont, zone 6
Sounds like another situation of typical new-construction moisture. Did the house get rained on in the framing stage? Do you have concrete basement floor and walls? I would use a dehumidifier periodically to keep humidity under control. I don't know what type of thermo-hygrometer you have but I have seen cheap ones that we off by 10% (i.e. it said RH was 40% and my meter said 50%).
Heidi,
Your rigid foam should be thick enough to keep your wall sheathing warm in your climate zone. The two factors that are contributing to your problem are construction moisture (as David Meiland noted) and the fact that you have probably not been keeping the building warm enough.
So crank up the heat, and keep your ventilation system (or exhaust fans) running for 24 hours a day. Unlike David, I don't think you need a dehumidifier. The temperature in Vermont has been hovering around zero for quite a while lately, so the outdoor air isn't holding much moisture. If you ventilate your house with that nice, dry, outdoor air, you should be able to bring down the indoor RH.
David:
1. We actually framed the house over a year ago and had the cavities open and drying all winter last year, so I think the moisture was pretty low by comparison to new-construction.
2. We are a slab on grade
3. We have a heat pump hot water heater that runs once a day that should do some 'de humidification' right?
4. I would say ours thermo-hygrometer is on the 'cheap' end, so that is a good point that you make.
What I'm hoping is that we have designed a 'safe wall' and that we fell down in not getting the interior air barrier up quickly enough after the insulation. Do you think that is accurate?
I also wonder if we had left things as is would it have eventually dried to the interior during the warmer months?
In that stackup 2" polyiso is a bit marginal for a zone 6 climate, due to the necessary de-rating of polyiso with temperature, and the R23 of the 5.5" Roxul, which would put the mid-winter average temp of the polyiso in mid-winter under 30F. With some manufacturer of polyiso a mid-depth temp of 30F would yield less than R3/inch(!), and none would be more than R5.5/inch, which means there's some risk of moisture accumulation in the plywood. The IRC prescriptive minimum is R11.25 for 2x6 framing, which is expected to be R18-R21 cavity fill, whereas Roxul is R23. If your best-case sceneario on the mid-winter performance of the polyiso is R11, and the worst-case R6-ish, this is potentially a problem. Unfortunately manufacturers don't provide very good derating information but something of a worst-case curve can be found here:
https://www.greenbuildingadvisor.com/sites/default/files/Karagiozis%20-%20thermal%20conductivity%20of%20a%20variety%20of%20insulations%20as%20a%20function%20of%20mean%20temperature.jpg
More information on derating of iso can be found here:
http://www.buildingscience.com/documents/information-sheets/info-502-temperature-dependent-r-value
A range of multiple vendor derating curves (where the warm side of the iso is at room temp, not at your much colder sheathing temp can be found here:
http://www.buildingscience.com/documents/information-sheets/content/info-502-temperature-dependent-r-value/images/bscinfo-502_figure_02r_web.jpg
Note that in a zone 6 climate with 2" of polyiso on the exterior and R23 in the wall cavity the WARM side of the the polyiso will average less than 40F/4C during the winter, which means you're on the left-most edge of those curves, so your polyiso is probably going to be averaging R9 @ 2", but can't be counted on for more than R7 @ 2" if you're being conservative.
If you had added even 3/4" of Type-II EPS to the exterior of the polyiso that would have multiple benefits to the stackup, and add more than the nominal R3.1 labeled value of the EPS to the whole-wall R. By putting that bit of insulation at the coldest edge of the stackup it raises the average temp of the polyiso a few degrees, which could add as much as R2 to the mid-winter performance of the polyiso layer by moving it up the derating curve. And since the performance of the EPS will be more like R3.5 @0.75" when it's average temp is below 25F, it's rising performance at low time offsets the declining of the performance of (that now somewhat-improved) polyiso layer. Assuming the now slightly warmer polyiso would then be performing at least R8.5-9 (a good bet) that R3.5-ish performance of the EPS puts it above the IRC prescriptive minimums, and you're golden.
There isn't a really good model for this, since we don't have derating curves for the polyiso when the warm side is at 40F rather than 70F, but the sheathing can't average much colder than 40F without taking on a signficant moisture burden over the winter, unless you added an interior side vapor retarder, which would have to be "smart" vapor retarder such as Intello Plus or Certainteed MemBrain to not create a moisture trap with the foil facers of the iso on the exterior. More exterior R is always better- R3 EPS is pretty cheap and in this stackup would be adding more than R4 to the true average performance during the months that count.
But since it sounds like the siding is already up, it's not worth ripping it down to add R3 EPS- just add smart vapor retarder as you go while installing the Roxul, detailing the vapor retarder as an air barrier. And don't paint the gypsum until June or later to give the sheathing sufficient drying time during weather the average temp of the sheathing is north of 60F, and releasing it's moisture burden. The smart vapor retarders will be 10perms or higher when there's a large moisture load being released whereas latex paint would be 3-5 perms, slowing the purging of moisture from the assembly. During the winter when the air in the house & wall cavity are under 35% the smart vapor retarder would be less than 1 perm, much tighter than the paint, and slowing next-winter's moisture uptake by an order of magnitude.
Wherever the moisture is coming from, you either ventilate it or remove it with a dehumidifier. If you have a vent fan installed and ducted to the outside (even the range hood) that will work. If you do not, and/or have easy access to a dehu, that will work too. I have one, so I use it, but it's not the only way.
I do think the moisture in the walls will probably go away by itself even if you install the drywall, but I would be doing something to help it along, especially since you are about to add drywall mud, primer, paint and other stuff to the equation.
Martin, warm or cold homes should not have moisture problems. i have camps that winter at 45 degrees set points with no issues, I have camps that have the HVAC off. I have homes set at 65.
There is a problem. Too much moisture in the home is one. 1 layer of exterior rigid foam is not done by my long time contracting locals. Bruce Brownell uses two layers and no between stud insulation. Even with higher than 35% moisture those http://www.aaepassivesolar.com/ homes do not have the problem being discussed.
Best to build proven designs people with the help of someone who knows what they are doing. DIY use of foam in tight homes can be a disaster. Bruce is a detail type and has to be because the tighter one constructs a home the more one opens up possible moisture and air quality issues.
DIY home building is not the same as DIY drain unplugging.
Dana,
Do you have experience with either of the 'smart' membranes you mention above? Seems like a fairly large price difference between the two (Intello being more expensive).
Thanks,
Heidi
AJ,
Thank you for your debate regarding interior air temperature and whether or not that is a factor. We like a cool home, so it would be good to know if that is a factor moving forward or not.
Thanks
heidi
Certainteed MemBrain has tested well in US climates. The primary problem most people have is finding it in distribution. Intello is imported from Europe, but sold in onesie-twosie roll volumes by 475 Building supply via internet, which makes it availalable to most, but at a more retail/boutique kind of price. I have no long-term experience with either. It would be useful to dissect a building 15-20 years later to see how well it's working, but for now I'd just rely on manufacturer's specs and hope for the best.
I've seen less online data about Intello, but have no doubts about the performance of either of them. With MemBrain there is also at least some amount third party testing info available online to lend some cred, eg:
http://apps1.eere.energy.gov/buildings/publications/pdfs/building_america/smart_vapor_barrier.pdf
http://sweets.construction.com/swts_content_files/151920/591675.pdf
http://www.energy.wsu.edu/documents/AHT_ComparingTheMoisturePerformance%20Of%20Wood%20Framed%20Wall%20Systems.pdf
http://www.bestofbuildingscience.com/pdf/Brainy%20membrane%20HEM_23-4_p37-40.pdf
So if you have a local distributor who has MemBrain in stock, don't hesitate- it'll work.
Getting the interior RH down to 35% or less in winter is important for getting the full benefit of a smart vapor retarder- it may be worth getting better instrumentation to let you know when it's time to bump up the ventilation rates or kick on the dehumidifier.
Heidi, what you built was a mold growing dehumidifier/lousy rehumidifier. Your walls hit the dew point. The foam absorbed no water. The roxul absorbed the dehumidied air's water. Gravity gathered the water and with three to four sides of the roxul trapping and stopping air movement your rehumidifier walls filled with water faster than the rate of evaporation. Mold. Water. Dampness.
Your interior moisture is too high. Your foam is too thin. Your roxul has to go unless you drop the moisture level and your foam is to thin to keep the roxul IMO. And I have no idea how well you built all.
Drop your moisture level a lot. Changes will take time. Your foundation or you or both may be adding too much moisture. Get your moisture load way way down. New homes are well dried out in five years time. Two years for most of the drying if heated for two years. I also build log homes, Large timbers take time to dry.
I have many homes with no moisture problems. I have taken apart homes (I did not build) with just one layer of foam on the exterior that were rotted to the point of the framing being turned into potting soil.
I have not found problems with rigid foam added to the interior (too late for you.) This site says put it on the outside. Outside insulation has to be done right, very right. just a bit wrong and disaster. Inside foam not so.
For now dehumidify,open windows... get your moisture down and figure out where your moisture sources are. Next change something with your 2" foam/roxul assembly to a safer set up. Membrane alone to me is not enough unless you really figure out your moisture sources. You could cut some rigid foam to place between studs to add 2 more inches of foam then roxul then membrane. That's what I would do.
aj
Heidi,
My perspective differs somewhat from AJ's. While I agree that your house probably has high indoor relative humidity (probably due to the construction moisture), I don't think that your wall design is fundamentally flawed.
While it's true that polyisocyanurate insulation has reduced thermal performance at cold temperatures, I don't think that this phenomenon is concerning enough to make your wall assembly particularly risky. Lots of Vermonters have built 2x6 walls with 2 inches of exterior polyiso (including me), and the vast majority of these buildings are performing very well indeed -- better, on average, than most 2x6 walls without exterior foam.
Your first order of business is to reduce the indoor relative humidity (while keeping your interior heated). I think that your house will dry out.
I agree with AJ. Your framing should be dry by now. You must have a steady new source of moisture. Its common for the underside of an uninsulated roof deck and the top end of wall cavities (at the top plate) to get mold during construction through a winter when the house is heated (especially with temporary space, turbo and salamander heaters and not properly vented outdoors during the work phase).
What type of moisture barrier is under and around the sides of the slab?
By the way, dense packed cellulose insulation will not mold or allow insects to thrive after the wall gets wet. It is treated with boric acid. Also, cellulose is "hygroscopic", so it absorbs excess humidity and then releases it back into the building as the humidity levels fall. This is called drying to the inside.
With your assembly, you need to be concerned with this. Your wall assembly cannot dry to the outside so it needs an inside wall treatment that allows drying to the inside. Or more specifically, do not use an interior wall treatment that prevents or inhibits drying to the inside.
We have 15 mil stego wrap vapor barrier under the slab, sealed to the foundation wall at the edges and all pipe penetrations.
We are however 'sort of' living in the house, cooking, laundry, dishwashing, and I guess that has been enough to bump our humidity too high. As I mentioned we use the exhaust when we cook, but clearly that hasn't been enough. We have been watching the humidity and would certainly have run it more frequently if we had known that it was enough to moisture to cause these sort of issues. This all certainly hasn't been for lack of awareness or thought. I'm still a bit surprised that this assembly is as picky as it seems to be.
Nonetheless, since running the kitchen hood exhaust for 16 hours a day over the past couple of days, the RH was down to 16% last night, but bumped up to 34% overnight while it was closed back up. We only heat with wood and do not sleep in the house, so we do turned off the exhaust and shut the windows overnight. The RH was already dropping this morning when we opened it up again.
I'm guessing that as tight as the house is we are going to need to ventilate it constantly during the winter months?
At this point, we are stuck with making the 2" to the exterior work. We are 100% finished on the exterior. We are however open to including a smart vapor barrier, or not. We are open to reusing the roxul, or not. We have the flexibility to wait to paint, or not. We would just like to move forward as conservatively as necessary.
Any additional thoughts or suggestions are much appreciated.
Heidi
If you're confident there is no ground source humidity entering the house, it sounds like you have properly diagnosed its origins: indoor activity, including unvented combustion appliances.
I think your situation is a wakeup call for many of us; showing just how easy it is to load a wall with moisture. Particularly a wall system that is prompted widely by FHB-GBA and Building Science folks.
The question for the analysts here is: Are we seeing (1) wall assembly design issues, (2) possibly construction issues or is it because of (3) insufficient venting, or (4) cavities open in an occupied house under construction? Or a combination?
It reminds me that in heating seasons, exhaust only ventilation (usually bath fans, not kitchen stove exhausts) need to be operated on a steady cycle (X minutes per hour as the air exchange numbers are calculated for your house) and then run on extra duty when there are high moisture event (showers, cooking, etc). Bath fans tend to have lower energy demands. And you need a source of fresh air at well.
Once your walls are finished (so they can breathe to the indoors), you will have to rely on ventilation to resolve and manage the moisture levels. You can permanently install fairly inexpensive and even remote (wireless) moisture monitors and keep an eye on the situation.
The problems are 3) and 4). The presence of the exterior foam is not really an issue, because this same thing happens in houses under construction without exterior foam. Yes, there is a need for adequate mechanical ventilation on a permanent basis. If the house is not complete on the inside then maybe it is worth considering dedicated equipment for ventilation. Without moisture metering of the framing lumber no one here can know whether it is still drying, but unless the house was framed with dry lumber and has been standing a long time, I bet it's not dry, and the slab can still be adding moisture even with Stego under it.
Finish the house. Run the ventilation. It will work out even though slightly more exterior foam would have been safer. My biggest concern with foam sheathed walls is flashing, not vapor from the interior.
Heidi, I'm a DIY-remodeler not a pro like Dana, AJ, Martin, etc. I'm finding the advice a little strange.
One suggestion is that you dump what is undoubtedly thousands of dollars of Roxul to spend thousands on exterior foam board when you already have the exterior siding up? Others are advocating you dump the Roxul for dense packed cellulose? Perhaps less costly but without a WUFI model, I don't know that I'd believe cellulose is going to magically solve all my problems.
Strange advice, given the Roxul isn't causing the problem...
Instead why wouldn't you address your interior vapor load. Personally, I investigated re-insulating my own home with Roxul. I performed my own WUFI modeling using the ORNL version and also asked 475 to review the model. In my case (climate 5b), a smart vapor barrier (Intello) on the interior lowered the expected sheathing MC by a few % critical points. Of course, it is only a model.
Compared to chucking your Roxul, I'd think that cost pre-drywall for a smart vapor barrier would be relatively tolerable in comparison.
I'd think the smart barrier would also offer you the following finesse-the-situation option. 1. Install smart vb in an air sealed fashion (tape, outlet sealants etc). 2. Stall on the drywall. 3. Cut into the vb install (repair with air sealing tape later) 4. Check moisture.
Great comments. Lots to continue considering as we slowly move forward again.
In the meantime, I'm wondering if anyone has suggestions for moisture monitoring instrumentation? Looking on-line it looks like dozens of the same 'cheap' version that we already have, and I would rather purchase on recommendation not just looking for one that costs more than the rest.
Any suggestions?
DM has a good point on the slab. It will emit vapor until it dries and will absorb and release vapor if it is allowed to get damp or wet again. You can check if the slab is gassing off water vapor quite easily:
Try the polyurethane sheet test (ASTM D4263) – it's simple and bullet proof.
http://www.nrmca.org/aboutconcrete/cips/28p.pdf
As for the framing lumber; you have been heating for a year and assumably you used commercial kiln dried lumber. Your moisture levels should be equalized in 2" dimensional lumber by now. Larger dimensional lumber, posts and timbers take longer
http://www.conradlumberco.com/pdfs/ch12_Drying_Control_of_Moisture.pdf
DM... how is flashing an issue with the taped seams? I can see how that could be a problem on the weather side if the flashing details were weak at the seams and openings/envelope penetrations, leading to bulk water entering.
Is there any correspondence of water with these locations? Check these things and let us know.
Heidi,
I agree with Keith that your Roxul batts are not the problem, and there is no reason to throw out the Roxul.
Here's an important point to remember about vapor retarders: the reason we get one or two questions a year like yours on the GBA website -- "It's winter, I'm working on my house, and I haven't put up my drywall yet but now I'm scared because I found moisture between the insulation and the wall sheathing" -- is due to two facts: (a) homes under construction have construction moisture, and (b) walls without drywall usually don't have an interior vapor retarder or an interior air barrier.
Once your drywall is up and covered with latex paint, you'll have (a) an interior air barrier and (b) a fairly effective vapor retarder (because even ordinary latex paint slows down vapor diffusion).
So you may not need an expensive smart retarder. You just may need to lower your indoor humidity, wait for spring, and finish installing your drywall and paint.
An update and a follow-up question:
We have been using the outside air to dry the house out for the past week. This was working well until 2 days ago when the outside air got moist again. Now that the interior humidity has crept back up to 40% (it was as low as 16%, then steady in the 20's, then steady in the 30's), we will jump over to using a dehumidifier.
Which leads me to my question: When we begin living like normal people and occupying a finished house, what will our target humidity be during the cold months? Eg: If it is zero outside, we're shooting for 70° and 25% humidity right? If it is 30° outside we're shooting for 70° and what rh inside? I'm imagining there will be some difficulty in achieving the 25% when it's humid outside (like today). Will we forever be tethered to a dehumidifier? I guess the same question goes for the swing seasons where it's 50° outside and we're not likely to be heating (yet or still).
I guess I'm looking for a playbook so that there isn't the worry that we're doing something wrong (again).
Your input is appreciated,
Heidi
You haven't actually determiend the source of the moisture, yet: slab, frame, bulk water and or life style, or all the above. And it appears you are still under construction (insulation, drywall, etc) so building performance is a moving target. Are you moitoring the moisture in the wall cavities or only in the living space.
No way to answer your question about when this might be over. But what you are aiming for is definable and addressed by science and by law:
http://www.epa.gov/region7/citizens/pdf/EPA_HomeHelps.pdf
https://www.energycodes.gov/sites/default/files/documents/BECP_Buidling%20Energy%20Code%20Resource%20Guide%20Air%20Leakage%20Guide_Sept2011_v00_lores.pdf
Fitch:
Agreed, we are still in the 'diagnostic' phase. We are measuring our living space humidity only currently.
Our mid-construction blower door test placed us at 0.5 ach.
I guess I'm already mentally fast forwarding to getting beyond this short term moisture issue (believing strongly that is residual new construction and already partial occupying the building without ventilation), and looking more for guidelines for next winter for example. The links that you attached were helpful, particularly in detailing our interior air barrier, but I wasn't seeing the sort of climatic guidelines I was looking for, unless I missed something and looked too quickly?
Thanks,
Heidi
The healthy-comfortable range for humans is 30-50% RH according to health professionals, 25-65% according to ASHRAE (but what do THEY know, eh? ;-) ) The healthy range for your house in mid winter is "as low as possible".
IRC code prescriptive R values for using exterior insulation as dew point control at the sheathing presumes interior air with a dew point of 38-40F, which corresponds to about 30-35% RH @ 70F. So that's really your mid-winter range to shoot for, though it's not usually a disaster to hit 40%RH as long as it's not a sustained 40% through all of the coldest weeks of winter. Ventilation operated under dehumidistat control set to 30-33% will get you there, or you can play around with duty cycle settings to make it happen.
When it warms up into the mid-40s and into the 50s it's likely that even the outdoor dewpoint will be above 40F, so the dehumidistat won't bring the RH down any more, but when it's getting that warm the sheathing is drying, not accumulating moisture.
Agree that you should shoot for 30-35% at 68F. It should be easily do-able with a decent bath fan (capable of moving 50CFM or more) and a timer control or possibly a humidistat.
You're probably a candidate for a good hygrometer. Spending $150-200 should get you a nice tool, maybe a Testo, Fluke, Protimeter, Extech, something in that range. You can sell it on eBay when you're satisfied that you've got a stable situation and no longer need it. I have a number of them and can tell you that if I set them side by side in a stable environment, they never give identical readings, but they're pretty close. Having a "datalogging" (recording) function is nice. You could spend about $80 and buy UEI THL2 datalogger if you don't need a display on it (have to plug it into a USB port and download the data).
After a period of time monitoring the temperature and RH numbers, you'll have a good handle on how much ventilation you need to control humidity.
For future home builders;
Some facts;
1 This home would have had less issues if it had two 2" layers of external foam.
2 This home desperately needs the interior barrier of well sealed drywall or variable perm barrier
3 A home with more exterior foam layers and no in wall insulation would not have this moisture problem.
4 A home with more exterior foam layers would also be able to have nice higher humidity levels which we humans appreciate. Examples of such I have been in... http://www.aaepassivesolar.com/ designed by Bruce Brownell.
Heidi, the last few posts others have given you should help. As the weather warms you will not have condensation in your walls so once you get all dry, get your walls assembled. Tight homes cost more to build, take less to heat, cost more to vent, need humidistats and homeowners that vent moisture loads like pasta boiling, showers, fifty plants in a wonderful indoor atrium... pools... jacuzzis...and... NEW HOME MOISTURE.
Once you are done building... and you use just a bit of venting, fans... all should be fine.
Lastly if that were my build, I would price out adding a layer of foam to the inside of the walls on top of the exterior foam, using some can foam to seal it. Then add roxul back in and drywall walls at the time the roxul is installed. Airtight methods for drywall install.
To Ms. Davis - As a possible test for how much moisture is or is not hiding in the Roxul, you might wish to take a batt out of one of the offending bays when it is coolest, then place it into a clear plastic bag. Something like a mattress or new sheet set comes in that does not have the little safety holes. Place the bagged Roxul in a warm place and see how much moisture collects on the bag walls. This is much like the test for "hidden" moisture in your slab and will reveal water that can't be felt or squeezed out and may be missed by meters that can't cope with the materials characteristics. Random samples of the Roxul might be necessary if there is doubt about walls on the north or south being main offenders.
Installing your HRV will go a long way in mitigating your moisture issues. The jury is still out on whether 2" polyiso will work long term as a general practice, but Mem-brain or an interior permeable air barrier would help keep moisture out of the assembly provided you seal the outlets and other penatrations. Maine Green Buidlng in Portland (or online) carries air barriers and like products.
A follow-up observation and (2) questions:
1. New observation: We pulled all of the first floor walls apart this weekend.(Previously just the second floor had been 'undone'.) There was minimal moisture on the plywood, but signs (yuck) that it had been wet for a while. There was zero sign of moisture now or ever on the south wall which is behind the wood stove.
Can we conclude that a.) getting the humidity down to 30% + ('slightly') warmer daytime outside temperatures combined to stop the wetting at the plywood?
Can we conclude that b) near the wood stove the air was drier and warmer and therefor not a problem?
2. Other questions:
-We have not yet begun to put the second floor back together, but are getting ready to do so. We are hesitating on the Membrain type product. Not because of cost, but because we won't be installing it exactly as the installation manual requires/recommends. ie: our ceilings are already up, the rim joist is inaccessible, and the roof has already been insulated without a similar vb product. We've got the willies that perhaps having this strong difference in vapor permeability during the winter months between the walls and ceiling or some joint that we're not going to be able to get to, is going to have an intensifying effect on the more vulnerable areas ie: you've to 2 cups of water that wants to get out, there's all this area with the smart v.b. that is basically impermeable, then you've got other areas and locations where it can go - and all in one place. Are we over thinking this? Is sticking with installing the drywall air tight and painting OK like we all thought originally?
-Second question: Any masochists out there that are living in a home with a similar wall section that have done some selective demolition to see what you've got going on in your walls? Or do you all favor sleep more than I do?
Thanks again,
Heidi
You pulled what apart on your walls?
Post pictures.
Give us more details.
Heidi.
YOUR FOAM IS TOO THIN FOR YOUR CURRENT ASSEMBLY AND MOISTURE. IT IS THAT SIMPLE.
The walls your took apart... were just batts of roxul no drywall? No vapor barrier?
Details
Pictures
Post humidity levels
Test your slab for moisture
You are there and if you read up on this site, you should know what is what by now.
There are pros you could get to do a site inspection and help you.
How many pros or others of any experience have you had go look at your situation????
Not trying to get your goat... but by now you have mine.
Good news... Spring warmer weather is only a weekend away.... yippee...
I would and others for a fee would travel to your home to help you if this just gets to going nowhere... via web chatting.
If I was close I would definitely stop in for nuttin.
aj
Heidi,
If some areas of your house (for example, your south-facing walls) have plywood sheathing that doesn't look as bad as others (for example, your north-facing walls) it's probably because the south-facing walls are, on average, warmer than north-facing walls. If the plywood stays warm, there's less chance of condensation or moisture accumulation in the plywood.
If you address just your walls but not your ceiling, you won't be increasing the risk of ceiling problems. The physics doesn't work the way you propose ("you've to 2 cups of water that wants to get out, there's all this area with the smart vapor barrier that is basically impermeable, then you've got other areas and locations where it can go - and all in one place").
Fortunately, the 2 cups of water that you are worried about don't sit down to a strategy meeting, and then all rush for the same hole in your ceiling.
Martin: Thank you for the humor and the gentle explanation. Do you think that air tight drywall would be acceptable too?
AJ: To answer your questions:
- The walls that were mentioned above were insulated with roxul and drywalled. No tape, mud, paint. No vapor barrier.
- We are going on three weeks of RH in the low 30's through exhaust only ventilation with our rangehood
- The slab was poured 2 1/2 years ago. We tested the slab for moisture and there was none.
- As for the professional: I am a professional in the design industry. I work in a firm that designs high performance homes and buildings. I chose this wall assembly 3 years ago for reasons of constructibility, affordability, and wide acceptance in the industry. While our firm typically designs exterior insulation assemblies these days, the assembly listed above is on our 'acceptable wall design' list for our climate, and is used. This wall and many others were run by our wufi consultant and approved.
Three years of refining some of those pesky exterior insulation details plus our own current build-it-slow formula, yes, I would choose a different route. Hindsight.
My goals are to:
a.) Come up with a solution for a homestead that we've worked tirelessly towards and on for last 4 years and hope to spend the next 40
b.) Learn from this in the most productive way
In the meantime, apologies if I'm really that tiresome, see a.) and b.) above.
Heidi,
Q. "Do you think that air tight drywall would be acceptable?"
A. If your stud bays are filled with air-permeable insulation -- and they are -- then the airtight drywall approach is certainly helpful. For more on the topic, see Airtight Drywall.
On a more positive follow-up:
We have one section of exterior wall that has a layer of plywood instead of drywall. (It is going to receive some clapboard as a wall finish that's why the plywood).
We insulated the bays back in October, and got around to hanging the plywood around middle of December. There was an unfinished one foot gap at the bottom, and also at the top.
We cut a hole in the plywood last week in a bay and location that we thought was 'worst possible case' based on what we've seen in every other bay we've pulled apart. The cavity was dry.
So what this tells me (if you all agree) is that the plywood as an air barrier worked in keeping moisture and damage out of the wall. Just as our air tight painted drywall will for the rest of the walls. And this was with a couple of months of being loaded with moisture and cold temps, too high humidity, and also not completed finish at top and bottom.
Seemed like good news to me and maybe a help to others out there who have a similar wall and might be wondering.