Most cost effective system for energy efficient home?

O.K., so we’re designing a new home and I’ve been reading a lot; books, magazines and forums such as this hoping to find the answer to the question… what is the most cost effective system to build an energy efficient home. SIPs, double stud walls, 2×6 wall with rigid foam insulation on the exterior, spray foam, cellulose and so on. So many options, so little time.
I’d also like to avoid as much as I can petrochemical based products and use as many natural and/or recycled products as possible. I understand the argument that using foam insulation in the end saves more oil than is used to produce it but if I can get equal or better results using natural/recycled, all the better.
The concept being discussed here, a vapor open wall system seems a sensible approach allowing the wall to dry to the interior and exterior.
I know that it’s difficult to say what’s best, but any thoughts on what works and what doesn’t would be greatly appreciated.
We’re in the cold climate of New England (RI).
GBA Detail Library
A collection of one thousand construction details organized by climate and house part
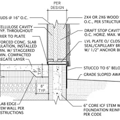
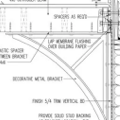
Replies
John,
When it comes to high-R walls, the most cost-effective option in most areas is a double 2x4 wall with a total thickness of about 12 inches, insulated with dense-packed cellulose.
In areas with very high labor costs, some builders claim that it is less expensive to build a 2x6 wall covered on the exterior with 2 or 3 inches of polyisocyanurate foam.
We'll be building a Cape style with the "attic" used for living space, thus a cathedral ceiling. What's the best option for ceiling/roof insulation?
John,
The best option for a cathedral ceiling is different from the most cost-effective. As far as I'm concerned, the best option would be a SIP roof covered with a layer of 2-in.-thick rigid foam above the SIPs, with the top layer of foam lapping over the SIP seams. Then 2x4 sleepers, eaves to ridge, for ventilation. Then another layer of roof sheathing (ideally plywood or boards, not OSB), followed by roof underlayment and the roofing of your choice.
Martin
I'm curious...why the plywood for the second roof sheathing ...why not OSB?
Garth,
Eventually, roof sheathing gets wet. When exposed to moisture, OSB turns to oatmeal much faster than plywood or boards. It's well worth spending the slightly higher cost for plywood in any location where occasional moisture is a possibility.
Martin
OK, I see the reasoning here, but it seems that with a fully back vented sheathing that even OSB would dry before "turning to oatmeal".
Why a "top layer of 2" foam over the SIPs and not just a thicker SIP?
I failed to mention that we'd be using metal roofing like Fabral's Grandrib 3 or standing seam.
How a bout a 12" SIP with 30# felt, sleepers and metal roofing?
John,
If the SIP has an EPS core, then a 12-inch SIP has an R-value of about R-43. That's OK. But if you add 2 inches of EPS on top, you'll get R-50. If you add 2 inches of polyiso on top, you'll get R-56.
In Juneau, Alaska, all of the failures on the SIP roofs occurred at the seams. That's the weak point of SIPs. Roof SIPs are heavy, awkward, and hard to align. Canned spray foam at the seams doesn't stay airtight for long. Interior SIP tape helps, but there is still thermal bridging at the seams.
One more layer of rigid foam on top of the SIP seams solves these problems.
I don't get your assembly, martin - why SIPS at all? If you want a vented roof assembly with foam, why not sheathe the roof, put on as many layers and thicknesses of foam you want, then lay sleepers for ventilation, then sheathe again?
Dan,
That'll work. The thicker the foam, though, the harder the screwing. Once you're up to R-50 or R-60 worth of foam, it's not so easy to find the rafters.
How does that make it any harder? Is the strapping over the extra rigid just fastened to the SIPS? Would that give enough uplift resistance to the final layer of sheathing?
What would be the best non-petrochemical (foam) option?
John H,
You say you want cost effective and you want to avoid petrochemical products.
Have you considered changing the Architecture?
Why not forget about cathedral ceilings and attic living space?
Flat ceilings with a tight air control layer ... and then pile on the not-so-expensive cellulose.
I am building a double stud wall home in Vermont with dense pack cellulose. For the cathedral roof we used 2x12 rafters then gussetted 2x4's to the interior top create an extra 12" cavity. This 23" cavity will then be dense packed like the walls. We chose to go unvented in order to align the air barrier (zip system roof sheathing) with the insulation layer. A vented assembly can be done this way as well. I am not sure if its the best way, just the way we are doing it.
John,
You can have your cathedral ceilings and still avoid petrochemicals (though a flat ceiling is always less expensive and easier to insulate, air seal and vent.
I was the first to respond to your query with a lengthy post, which appeared on the website when I was done, but has mysteriously disappeared (gremlins or other evil-doers or careless editor's fingers?)
I have long been building exactly what you're looking for. Except for foundation and sublsab insulation, for which there is no good and widely accessible alternative to XPS, and a little gun foam around doors and windows, I design and build some of the most cost-effective, energy efficient, healthy, breatheable and low ecological footprint homes.
Even better than the many variations of double stud walls (which I still design for others), I've modified the Larsen Truss to make a 12" thick, nearly thermal bridge free wall, out of locally-sourced rough-sawn (often green) lumber, which uses no more wood than a standard 2x6 house. And all above grade insulation is dry cellulose with borates, the very best of all the commonly available insulation options (short of straw bale and earthen plasters).
My system is described and depicted at http://www.builditsolar.com/Projects/SolarHomes/LarsenTruss/LarsenTruss.htm
Graham,
Air barrier continuity is important, but an unvented and non-breathing roof is not the best partner for cellulose. And, since the primary purpose of the ceiling air barrier is to prevent exfiltration of warm, humid air into the thermal envelope, then the best place for the air barrier is at the inside ceiling plane. That also allows the outside ceiling/roof plane to be both vented and vapor open, which mitigates the several problems of unvented roofs, including non-drying sheathing, lack of escape path for any moisture that finds its way into the thermal envelope, ice dam formation, summer radiant gain, and roofing longevity.
Robert, It wasn't gremlins or evil doers, it's our government's job to keep them under control. Your answer was to the question at the begining of this thread which I had posted on another discussion. What follows is your answer and a few questions from me
...
16. John,
You should have started another thread, as this is a different discussion and likely to elicit many different answers.
I have, however, been building in the way you propose for more than 30 years and have developed what I consider to be the optimum approach using conventional materials (though straw bale with earthen plasters beats them all).
I've modified the Larsen Truss system to optimize it for new construction, and use locally-sourced rough-sawn (often green) lumber for all framing and sometimes for siding and exterior trim as well. Other than subslab or foundation insulation (for which there are no good alternatives to rigid foam board), but which I minimize by using shallow frost-protected grade beams or rubble-trench foundations, I use only cellulose with borates to create a thermally-broken R-45 wall and R-65 ceiling with fully vented roof. I do use some butyl caulk (Tremco) for the air-tight drywall approach and some gun foam around doors and windows and mechanical penetrations, but my use of artificial materials is minimal compared to most approaches.
I'm a firm believer in vapor-open walls, particularly exteriors in a northern clime, and in low-tech ventilation systems (exhaust-only with passive make-up inlets). All my homes are designed for passive solar and typically have woodstoves in addition to possible central radiant heat.
My last such house is described and pictured at http://www.builditsolar.com/Projects/SolarHomes/LarsenTruss/LarsenTruss.htm
I also have designed several modifications of the double-wall system for others to build with KD lumber and plywood sheathing. The only plywood I typically use is for the deep door and window boxes. All other sheathing or decking is rough-sawn boards (makes the most breatheable exterior skin) or simply thick siding over housewrap without redundant sheathing. With board sheathing, I prefer felt to plastic housewrap and I use felt roofing underlayment rather than the new plastic varieties.
Answered by Robert Riversong - Sep 3 10
--------------------------------------------------------------------------------
17. Thanks Robert. I started a new thread in this category as you suggested.
https://www.greenbuildingadvisor.com/community/forum/energy-efficiency-an...
I also looked at the house at the Builditsolar site and it looks great but for me raises some questions.
The design for our home is a cape style using the "attic" space for bedrooms and workspace so there will be a cathedral ceiling. What's the best option to insulate the roof?
Because of the existing topography and a high water table we're going to have a basement under part of the house and a slab floor for the rest. I'm looking into using Thermomass insulation system for the foundation walls. Any suggestions here?
Does a 2x4 24" OC load bearing wall meet code or do building officials consider the truss as a whole?
We're aiming for a nearly maintainance free exterior without using vinyl and are planning on using Hardie Plank clapboard style siding. Would we better off sheathing with plywood/boards with felt paper and a rainscreen like Homesliker? Any thoughts on the Hardie products?
Why do you use the dry cellulose and not the damp spray?
I've gotten some prices on radiant systems and it seems they are quite expensive considering the minimal heating requirements of a house like this. A warm floor is certainly quite appealing but is there a less expensive way to get there? Perhaps an electric floor "warming" system?
Thanks very much for sharing your expertise and enthusiasm.
Answered by John Holscher - Sep 4 10
Oh, well. That's what happens when someone follows my advice, starts a new thread, and leaves me confused about where my answer went.
"The design for our home is a cape style using the "attic" space for bedrooms and workspace so there will be a cathedral ceiling. What's the best option to insulate the roof?"
The same way you'd insulate the walls. Rather than extending the frame outward with a truss chord, extend the rafters inward with an additional non-structural framing member under each rafter connected by gussets (or webs) to reduce thermal bridging and create a deep enough insulation cavity to still leave room for venting under the roof sheathing, which would require continuous baffles from eave to ridge.
"Because of the existing topography and a high water table we're going to have a basement under part of the house and a slab floor for the rest. I'm looking into using Thermomass insulation system for the foundation walls. Any suggestions here?"
I'm not sure what suggestions you're looking for, but the ThermoMass system is a fine option for a basement. I would recommend the maximum XPS thickness of 4", with two 4" whythes of concrete.
"Does a 2x4 24" OC load bearing wall meet code or do building officials consider the truss as a whole?"
A rough-sawn, full-dimension 2x4 has the strength of a KD 2x6, and if both chords of the wall truss are supported by the foundation, then this makes an exceptionally strong wall. Depending on your code official, you may need an engineer's stamp.
"We're aiming for a nearly maintainance free exterior without using vinyl and are planning on using Hardie Plank clapboard style siding. Would we better off sheathing with plywood/boards with felt paper and a rainscreen like Homesliker? Any thoughts on the Hardie products?"
Vinyl is one of the most environmentally destructive of materials and one of the most common in consumer products. Cement, however, has very high embodied energy and is one of the largest contributors to global warming. If your goal is a "nearly" maintenance-free exterior, then I would suggest wood siding with a solid-color latex stain on all six sides. Never needs scraping, just refinishing every 10 or 15 years, depending on weather exposure.
Homeslicker is not a rainscreen, but merely a drainage plane and capillary break. I don't recommend rainscreens except in the most severe rain/wind zones such as coastal areas. Felt functions better than most plastic housewraps and relies on the time-tested shingling layered approach to drainage rather than tapes, and can diffuse liquid water as well as vapor, unlike housewraps.
"Why do you use the dry cellulose and not the damp spray?"
Because there's no advantage to damp spray and the extra moisture load is unnecessary.
"I've gotten some prices on radiant systems and it seems they are quite expensive considering the minimal heating requirements of a house like this. A warm floor is certainly quite appealing but is there a less expensive way to get there? Perhaps an electric floor "warming" system?"
One of the advantages of a super-insulated house, particularly one that also optimizes solar gain, is that you can often do without central heat, as long as you like feeding a woodstove or are willing to live with the somewhat uneven heat distribution of wall-mounted space heaters.
But, if you're building a home to grow old in, then a reliable central heating system and warm floors will become more desirable with time. A gas boiler will almost always be less expensive to operate and less costly to the environment than electric heat, and if it also produces domestic hot water then it may be worth the investment.
Additionally, a radiant concrete slab can double as solar and thermal mass to help moderate and store excess heat (see my article in the April/May issue of Home Power magazine).
Does anyone other than Robert use roof trusses back east?
Jon, for your cathedral ceilings use a truss thick enough for appropriate venting and insulation (especially above the top plates).
Sure, you can use a roof truss - a high-healed attic truss or a parallel-chord vaulted truss - that's always a quick and easy option to stick framing.
But, like OSB instead of plywood or sawn wood sheathing, it's penny wise and pound foolish. In other words, it's cheaper in both senses of the word.
Unless you have the trusses manufactured with 2x8 bottom and top chords, the roof assembly will always be:
1) more vulnerable to impact damage (such as tree branch falling on roof - 2x4's break easily)
2) more vulnerable to fire damage (firefighters won't do an interior attack or ventilate a roof in a truss house - they collapse too quickly)
3) more difficult to renovate later (try to add a dormer in a truss roof - an engineering nightmare)
4) prone to structural failure in the event of a single truss plate corroding (ammonium sulfate used in some cellulose insulation will corrode steel gang nailers, as will Chinese drywall)
The most cost-effective approach to an efficient home is to build only the space actually required for basic shelter, which is generally no more than half of what the typical American believes they need.
Regardless of materials and methods chosen, this uses far fewer resources and reduces both operating and maintenance costs (and even daily cleaning effort), as well as ultimate disposal costs. A half-sized house can have half the R-value and still be energy-efficient.
The most cost-effective building system for a temperate climate? Structural straw bale with earthen plaster, cordwood masonry with earthen floor, or scribed log construction, with no interior plumbing or wiring, a simple woodstove or Rumford fireplace, a shallow well with windlass bucket or gravity-fed spring and a rain barrel, and a pleasant composting outhouse.
Robert's answer concerning home size is an excellent one and far too seldom made. The very first concern for an aspiring green builder should be to build no larger than necessary. Sadly most of the featured 'green homes' we see, including even the plans featured on Sarah Susanka's 'not so big' web site set expectations of well over 2,000 s.f. for a modest three-bedroom home. Oddly, as a result of poor planning and fussy detailing many of these oversized homes feel anything but spacious.
I came across a study, "Building America Special Research Project: High-R Walls
Case Study Analysis"
Research Report - 0903 March 11, 2009 (rev. 8/7/09) John Straube and Jonathan Smegal
http://www.buildingscience.com/documents/reports/rr-1003-building-america-high-r-foundations-case-study-analysis
In this study the follwoing different wall construction options were tested.
1a 2x6 AF, 24"oc, R19FG + OSB
1aii 2x6, 16"oc, R19FG + OSB
1b 2x4 AF, 24"oc, R13FG + OSB
1bii 2x4, 16"oc, R13FG + OSB
2a 2x6 AF, 24"oc R19FG + 1" R5 XPS
2b 2x6 AF, 24"oc R19FG + 4" R20 XPS
3 2x6 AF, 24"oc, 2x3 R19+R8 FG
4 Double stud wall 9.5" R34 cellulose
5 Truss wall 12" R43 cellulose
6a SIPs (3.5" EPS)
6b SIPs (11.25" EPS)
7a ICF - 8" foam ICF (4" EPS)
7b ICF - 15" foam ICF (5" EPS)
7c ICF - 14" cement woodfiber ICF with Rockwool
8a 2x6 AF, 24" o.c., 5" 2 pcf R29 SPF, OSB
8b 2x6 AF, 24" o.c., 5.5" R21 0.5 pcf SPF, OSB
9 2x6 AF, 24"oc, 2" SPF and 3.5" cellulose
10 Double stud with 2" 2.0 pcf foam, 7.5" cell.
11 Offset frame wall with ext. spray foam
12 2x6 AF, 24"oc, EIFS - 4" EPS
*AF - Advanced Framing
They were evaluated in 5 categories; Thermal Control, Durability (wetting/drying), Buildability, Cost and Material Use and then given a Total score.
The study gave the highest marks to Cases 2, 8 and 12 and the lowest scores to Cases 4 & 5.
Speaking in favor of the use of exterior insulation as in cases 2 & 12, the study noted that "Two dimensional heat flow modeling has shown that exterior insulation is very effective at minimizing the thermal bridging losses of wall framing, and hygrothermal modeling showed reduced condensation potential in the wall from vapor diffusion and air leakage, as well as increased drying potential to the interior with reasonable interior relative humidities."
The study's critique of the double stud and truss walls was that "The main issue with most of the wood framed walls without exterior insulation is the probability of wintertime air leakage condensation depending on the quality of workmanship and the attention to detail." and "Hygrothermal modeling showed that traditional double stud walls, truss walls and interior strapped walls, are at a greater risk of air leakage condensation because of the air permeable insulation, and cold exterior surface."
Can anyone speak to the results of this study? It seems to run contrary to most of the comments made in this thread.
John H.,
The thing that I thought was not-so-fair about the study was that most of the non-outsulation assemblies included a vapor barrier.
John Holscher,
A double-stud wall filled with cellulose can perform very well, as long as:
1. You address concerns over moisture accumulation in the exterior sheathing by using plywood or boards, not OSB, and by including a rainscreen between the sheathing and the siding, and
2. You pay close attention to air sealing on the interior (by following the Airtight Drywall Approach).
As long as you follow these details, you're all set. And it should be the least expensive wall.
That said, foam-sheathed walls perform very, very well -- and they do a better job of addressing thermal bridging at rim joists. I love walls with thick exterior foam sheathing. Their two major drawbacks are:
1. They usually cost more than double-stud walls, and
2. There are increasing environmental concerns about rigid foam products (questionable fire retardant chemicals and a very long payback for some blowing agents in terms of global-warming potential).
John Holscher,
You linked to the Basement Wall study. The High-R Wall comparison is http://www.buildingscience.com/documents/reports/rr-0903-building-america-special-research-project-high-r-walls and the report is replete with suppositions, assumptions and bias. And this was a theoretical analysis using WUFI software, not a field evaluation. But there are a number of findings which support a vapor open and hygroscopic wall assembly.
Much of the problematic nature of certain wall systems was due to the use of poly, an archaic technique for moisture management that should be eliminated:
"Often times, the 6-mil polyethylene vapor barrier is also used as the air barrier. This is very difficult to detail correctly, and because it may not be air tight, there is a considerable risk to air leakage condensation on the sheathing should interior air leak into the enclosure."
And these results show the benefits of hygroscopic assemblies:
Inward vapor drives of Cases 3, 4, and 5(Figure 20) show there is very little performance difference between the test walls, and none of the walls experience any moisture related durability issues caused by inward vapor drives. Case 4, double stud construction, and Case 5, truss wall, experience slightly lower relative humidities because of the moisture buffering effect of the cellulose insulation.
A double stud wall with 2” of high density foam (Case 10) with and without an interior vapor barrier was compared to Case 4, a double stud wall filled with cellulose in Figure 21. There was an improvement in performance when two inches of foam were used on the exterior and an interior vapor barrier was installed. The foam restricted the inward vapor drive, and the poly controlled vapor from the interior environment. Although this wall showed lower relative humidities with respect to summer inward vapor drives, it is never recommended to have a high level of vapor control on both sides of the wall system. This substantially increases the risk of moisture related durability issues, should any water get into the wall cavity.
[Figure 21 shows that a double-stud flash & fill wall without poly has consistently higher RH than the same wall with a double vapor barrier or the double-stud wall with just cellulose.]
Inward vapor drive: Both Case 8 [int spray foam] and Case 11 [exterior spray foam] perform very similarly, with slightly higher relative humidities than Case 4 [double-stud/cellulose]
Comparing the double stud wall with cellulose insulation (Case 4) with the double stud wall with spray foam and cellulose (Case 10), Case 4 dried more quickly than Case 10 both with and without a interior polyethylene vapor barrier. With 12” of moisture buffering cellulose insulation in Case 4, it appears that the wall is able to quickly buffer and redistribute the moisture of a single wetting event and then release it slowly, mostly to the exterior of the OSB. Neither wall would suffer moisture related durability issues following a single wetting event but repeated wetting events to the OSB will increase the risk of moisture related durability issues.
The offset wall enclosure with exterior spray foam dried very slowly compared to the truss wall of Case 5 with cellulose insulation. The wall system with exterior high density spray foam is unable to dry to the exterior due to the vapor control of the spray foam. The interior relative humidity is elevated in the spring and summer months which would also affect the vapor pressure gradient and drying potential.
Martin,
The old varieties of double-stud walls (several of which I built in the 80's) had thermal bridging problems at floor and ceiling platforms, which interrupted the thermal barrier just as in a standard framed house. They also suffered from ambiguous load path issues and excessive framing materials (with structural headers in both walls, for instance).
But there are versions of the double-stud wall that overcome all three of these issues. I have one being built right now in Tinmouth VT and a few others that I've designed for other builders to erect. Though the Riversong Truss wall is more resource efficient and (I believe) much easier to build, I've found more acceptance for double framing when designed for conventional materials and methods, including KD lumber and plywood sheathing.
But, as my current builder has already noted, building a double-stud wall frame is like building two houses, whereas my Riversong Truss is like building one with some advanced framing techniques and than adding a site-fabricated exterior half truss, which is far easier and quicker and also gets the house under roof much sooner.
With either system, however, there is a completely uninterrupted thermal barrier surrounding the rim joists. Care needs to be taken, though, to create an uninterrupted interior air barrier with the ADA system. That is really the only advantage of exterior rigid foam - the continuous air barrier - but I assert that, for cold climates, it's on the wrong side.
Robert,
Do you have any details posted for the double stud wall that you mentioned?
(designed for more conventional materials&methods)
John B,
Here is a sampling of the double-frame walls I've designed and/or built:
http://www.flickr.com/photos/riversong-housewright/sets/72157624253116215/
Please use these drawings only with attribution (copyleft).
I noticed Mr. Riversong's comments on Rainscreen / Water Penetration issues, one consideration today is ventilation behind absorptive claddings - you may want to review these You Tube video animations:
Rainscreen Stucco:
https://www.youtube.com/watch?v=lgCbk76f3-E
Manufactured Stone Veneer:
https://www.youtube.com/watch?v=O3TTRmk-2Uo
Reservoir claddings, such as brick and stucco, always require a drainage space behind them. This has been traditional with brick facings (though the space may get filled with mortar droppings with sloppy fabrication, and weep holes may get clogged), and the standard for stucco is a double layer of grade D building paper to create a drainage plane.
Wood sidings should be back- and end-grain-sealed, but should not require a drainage plane unless they're installed over something as low-quality as OSB sheathing. But what is the comparative cost of using CDX over OSB with a vented rainscreen?
Mr. Riversong, fisrt let me say this thread has some good info although conflicting at times. You seam to have some different ideas than Mr. Holladay and the building science case study referanced above.
"the report is replete with suppositions, assumptions and bias. And this was a theoretical analysis using WUFI software, not a field evaluation. But there are a number of findings which support a vapor open and hygroscopic wall assembly."
I have read the case study previously and took it to be science "proven fact" and I have been leaning toward wall #2 based on the case study However enviro concerns associated with rigid are making me think twice. One of the reasons I do like wall #2 is the fact that it is not different than what builders is CT are acustom to. The truss a bit of a harder sell, as it appears you may have experianced. How do you get past the code requirement for a vapor "barrier" (retarder)? I don't think I can get away with a vapor open wall in CT. Your thought on vapor control are interesting but way out of the box from conventional thinking. I would love to read more debate on this topic between you and Mr. Holladay. Thank you. *sorry for poor spelling. I am on a moble device with no spellcheck.
"The most cost-effective approach to an efficient home is to build only the space actually required for basic shelter, which is generally no more than half of what the typical American believes they need."
Answered by Robert Riversong - Sep 5 10
----------------------------
Can anyone suggest good web resources for designing efficient, effective, inexpensive, DIY, non-claustrophobic small houses for cold climates?
Thanks
To John Hess:
"Can anyone suggest good web resources for designing efficient, effective, inexpensive, DIY, non-claustrophobic small houses for cold climates?"
Find an experienced LOCAL designer, architect or design-builder to work with whose portfolio is compatible with your vision. Good design is not generic, and not just climate-specific but also site-specific and culture-specific.
Riversong,
I may have misunderstood your comment above. "I'm a firm believer in vapor-open walls, particularly exteriors in a northern climate..."Do your wall assemblies have any vapor barriers/retarders (latex paint or otherwise) or are they completly "vapor-open"?
Cory,
The only reason that some of my approaches appear "outside the box" is that the box we have boxed ourselves into is very constrictive and violates some basic principles of physics and ecology. My "outside-the-box" materials and methods are, in fact, very similar to what has been done to create shelter for tens of thousands of years. It is only quite recently, in the scale of human evolution, that designers and builders have shifted to creating suffocating and anti-ecological boxes for human habitation.
Firstly, there is no such thing as "science proven fact". Facts are what was in the news yesterday, and even that different people can't agree upon. Science can do no more than suggest hypotheses and test them for reproducibility. Once tests (experiments) show agreement between the physical world and the hypothesis is becomes a theory. With enough positive experimental evidence, a theory becomes widely accepted as valid, until further evidence shows that it's not. Science can disprove a theory but can never prove one.
Second, terms like "vapor-open" are always scalable - that is, they have meaning only along a continuum. For this reason, building scientists and building codes not use the terms vapor-impermeable (class 1 vapor barrier), vapor semi-impermeable (class 2), vapor semi-permeable (class 3) and vapor permeable (class 4). These, like any categories, are arbitrary divisions of an undivided continuum and merely conventional.
When I refer to vapor-open cold-climate walls, I mean those with no more than the code-required 1 perm inner surface and at least 5 perm outer surface, with no vapor barrier material within the thermal envelope and with only hygroscopic framing, sheathing and insulating materials.
This is allowed anywhere by code and it is the most ecological and healthy way to build shelters for human habitation. It's also often the most cost-effective, durable and efficient way to build.
Riversong,
I was taking the term "vapor-open" too literal. Thank you for defining it for me. I fully understand what you are saying and your ideas make a lot of sense to me. I also understand and agree with you on fact vs. theory. What I should have stated was that I took the information in the case study to be "a widely accepted, valid theory”. I am happy to have been introduced to your thoughts and expertise. Thank you for your assistance.
Riversong,
Please disregard my request for a wall section. I just reviewed the one in the Flickr link above. Thank you.
To most of the posters, I skipped most of the minutae of the wall assemblies debated.
Specifically:
@ Graham Mink - I am not a fan of ZIP roof sheathing and suggest you avoid it. Tar paper is not that expensive.
To the OP I toyed briefly with double stud walls on several houses. The costs always came back very high relative to the performance. Rather than make walls thicker, I made them better. I use salvaged polyiso foam board bought by the tractor trailer load. I insulate everything on the outside now. And the interior trims look fairly normal.
-Rob
Robert Susz,
You're defining "performance" much too narrowly. A vapor-open double-wall or a truss wall filled with cellulose, with sawn lumber sheathing and wood siding will outperform any foam-insulated house in terms of the entire spectrum of embodied energy, embodied CO2, operating energy, durability, moisture management, comfort, healthy indoor environment, and small ecological footprint.
And there are relatively simple, effective, and low-cost methods for building double-wall homes.
post 3 from Martin intrigues me. I like the thought of a 12" SIP covered (lapped over joints) with 2" polyiso and vented. My question is.........are the SIPs in lieu of trusses/rafters in any/all situations? It seems a while back when looking over timber-frame companies, that SIPs might be engineered to handle roof load, and that would seem to save 2 or three steps and possibly less of a $$ outlay. Any thoughts/direction appreciated. in zone 5 and shooting for R-40 walls and R-60 roof.....
This may be slightly off-topic, but if you're comparing a wall assembly insulated entirely with plastic foam vs. a double wall or truss wall with deep cellulose, one of the differences is acoustics. Styrofoam is pretty much useless acoustically, so I would guess a wall with R-40 of rigid foam would have relatively poor soundproofing compared to a wall with equal R-value in cellulose. That alone could impact quality of life for the occupants in some locations.
Another difference is the combustibility and toxicity of plastic foam when burned.
Robert Riversong,
I have tried to build 3 homes with double walls here since 1999. Including my recently "substantially completed" 1500 sf addition. I am a believer, and have wanted to do it. But finding trades people, even after 11 years in this field, is very difficult. I was thrilled just to get my framer to help with the foam board on this addition.
I think if we were to debate " my wall vs your wall" we would lose the rest of the audience. And on many of your items, the differences would be decimal places. I'm not saying your wall is bad, I've just gone a direction I find easier.
Though I did notice you mentioned sawn lumber sheathing. That's a bit out there. I had never considered that. I am not a detractor from your wall assembly, but you have to admit it's a good bit away from conventional construction.
What I've found with my clients is that they will not make the move from junk construction to "bomb-proof" in one step. They need to take baby steps. Even the most enthusiastic greenie customer has gotten strung out with the details of trying to implement double walls and they just just give up. I've seen it happen.
So my approach is to get people from a bicycle to a fighter jet in more than one step. My wall (Lstibureks wall actually) looks like a "regular" wall with 4" or so of foam on the outside. Double walls, larsen trusses, and 12" of cellulose looks very different and very costly - unless you've been doing it a long time and have gotten effective at it, as you apparently have.
Much the way a SIP home would also be difficult to get built.
Also, I suspect that the cost of 12" D.P. cellulose could be better spent. In 2008 I would have charged $1 psf for wall spray cellulose and $3.20 psf to densepack 12" of cellulose. So the cellulose package will be VERY expensive. A $3k upgrade even for our smaller homes.
One item you didn't mention is sound. My outsilation doesn't stop sound as well as R-21 of cellulose would have. But thankfully I am 500 feet off the road. And a country road at that.
Regarding your items listed though. Did you notice I mentioned *salvaged* foam board?
As for operating Energy. I just added on 1500 sf with external foam. My gas bill went up $50 a month in the heating season. My total cost for the foam outsilation was about $3k. There is no cavity insulation. The foam was put over a 2x4 conventionally framed wall. It went very fast and was semi painless.
Regarding moisture buffering. I blew all interior walls and floors with cellulose for sound. So i got those benefits.
There will be no other moisture issues with these walls. They already went through a rainy fall and a heating season with no drywall. I looked for problems and didn't find them.
-Rob
Robert,
I just read the link you provided. I'm jealous and envious at the construction you were showing. Fantastic, top notch. I longingly read every detail as I am a big fan of cellulose. And of meticulous construction.
But that also still looks like a lot of work, and I think the cost/benefit stuff could be debated or applied differently.
Clearly, your customers value the many "intangible" portions of their homes that are simply not included when you say "larsen truss" or "cost/benefit."
-Rob
Steven Bumpus,
SIPs can be engineered to handle normal roof loads, as long as they aren't too long. Long spans require structural purlins. If you prefer to provide all of the the roof framing yourself, you can also order roof SIPs without the structural details.
Contact your SIP supplier for more information.
Martin Holliday,
What happens at the first condensing surface in the wall you describe below if you are using plywood sheathing?
Robert,
Some moisture can accumulate in the plywood sheathing over the winter. How much depends on:
- Outdoor temperatures during the winter,
- The indoor RH during the winter,
- The airtightness of the drywall installation, and
- The type of interior vapor retarder, if any.
During the spring and summer, the plywood should be able to dry to the exterior -- especially if there is a ventilated rainscreen gap between the sheathing and the siding.
Martin Holladay,
Eugene, Oregon, in zone 4, has a marine climate with cool wet winters(40F-50F) with wind driven rain, summers warm and dry(75F-85F) with cool nights(50F-60F).
Would the following wall work well in Eugene or would you suggest something else?
Siding, 1/2" rain screen, house wrap, 1/2" plywood sheathing, 2x4 stud wall on 2x4 plate, 5" gap, 2x4 stud wall on 2x4 plate, 5/8 X board with ADA. Wall filled with dense pack cellulose. HRV will be used in the winter.
Would there be enough time for this wall to dry out? What type of interior vapor retarder would be best, if any?
Robert,
I think your wall will be fine. Your best choices for an interior vapor retarder are either vapor-retarder paint or MemBrain.
Enough time from when to when? And what moisture are you concerned about - the 19% MC of the KD lumber, or are you planning to install 12" of moist cellulose? If the latter, that would be highly foolish and completely unnecessary. A wall that thick should be blown dry. In that case, the cellulose will help redistribute the moisture from the KD lumber (a typical house will release 600 gallons of water from the drying of KD lumber to equilibrium in the first year).
Dear John,
As longtime design/build home builder in Tucson, AZ, I have devoted the past two years to researching what it takes to answer your question of what is the most cost effective system for an energy efficient new home. I am nearing completion on a prototype 1935 sq.ft home. I have done extensive research and analysis and believe I have arrived at a real answer. The key is designing and building a home like an ice chest - a total super insulated above ground thermal envelope AND a thermally isolated and insulated concrete slab (5") with hydronic radiant heating and cooling. With the complete integrity of the thermal envelope above ground and below, I can efectively and completely control the temperature of the home with out and forced air system. I have evaluated this to be a cost effective zero energy use home that is extremely comfortable, quiet and healthy.
The use of polyurethane foam core SIPs for the walls AND the roof coupled with an insulated and thermally isolated concrete floor is my answer to your question. It is garnering some DOE & BAP attention and will be monitored post construction for effectiveness by The Davis Energy Group, a Team Member of the BAP (Build America Program). You can check out The S.E.E.D. Home at http://www.lamiradahomes.net.
Michael,
I know you think you are breaking new ground, but people have been building SIP homes over insulated slabs for decades.
And I'm still a skeptic when it comes to hydronic in-floor cooling. It only works if you can keep the indoor humidity very low. Even in Tucson, there will be days when you need supplemental dehumidification. And in most of the rest of the country, you'd get lots of condensation on your floor.
Michael,
Two years is hardly "extensive". I've been not only researching, but actually building such homes for 30 years and teaching the principles of truly efficient, effective, affordable and healthy homes for five years.
An "ice chest" is for storage of dead things or for keeping people in suspended animation. A shelter for living things (such as people, plants and animals) requires a breatheable structure composed of natural, non-toxic materials.
Not only are petrochemical foam "ice chests" very expensive to build, they are even more expensive to the environment and to human health. I can assure you that you are going down a literal dead end (as is much of the so-called "green" building movement).