Mooney floor

I want to put insulation on top of a concrete floor.
A layer of foam + plywood bolted to the concrete has been suggested. (By Dana I think)
While that looks an good option I’ve been exploring more low cost options.
What about a Mooney wall, flooring variation.
Thinking about 2×4 + 2×4, filled with blown in cellulose. Likely GreenFiber or InsulMax.
Is that a good alternative?
GBA Detail Library
A collection of one thousand construction details organized by climate and house part
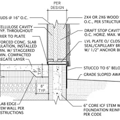
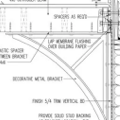
Replies
I suspect you would have a potential moisture issue with cellulose, but let's see what more knowledgeable posters think. In the meantime, you might find this discussion useful:
https://www.greenbuildingadvisor.com/community/forum/general-questions/26528/insulated-floor-top-concrete-slab
Putting the 2x4s in contact with the concrete would be a ground moisture wicking path. Even if you put a capillary break between the 2x4 and concrete the bottom edge of the 2x4 is likely to dwell below the dew point of the summertime air's dew point, taking on moisture to rot-potential levels.
The cool side of the cellulose would have similar issues, even if you managed to make the concrete fully water & water-vapor tight. Using cellulose for insulation anywhere below grade- even walls is fairly risky, since even a minor flood would cause water to wick the full height of the wall, and you'd be forced to gut the place and start over. With fiberglass or rock wool you'd usually be able to cut the wallboard & insulation at a point about a foot or so above the high water mark. On a floor, fuggedaboutdit.
The amount of water-impervious insulation needed for summertime dew point control depends on your deep subsoil temps and your summertime outdoor dew point averages. In most of the US R3-R4 (3/4" - 1" of EPS) would be enough. The amount of R value that makes financial sense depends on your energy costs and deep subsoil temps, but very few places would need the equivalent of 7" of cellulose in a Mooney-floor configuration unless it's a cold/very-cold climate, and the room is heated with a radiant floor.
Tony,
I agree with Steve and Dana. If you ware installing insulation above a concrete slab, you don't want to use an insulation that is vulnerable to moisture like cellulose. The best option (from a "green" perspective) would be EPS, but any rigid foam would work.
For more information, see Choosing Rigid Foam.
"but very few places would need the equivalent of 7"
I'm getting more confused every time I try to learn something :-)
Shouldn't a floor be R-30 according to code? (Zone 5A)
To be honest I was even thinking about a 2x6 + 2x6 floor. The reason is twofold:
a] 11x R-3.2 = R-35 = above code
b] The floor has two levels. Just a 3-3.5" difference but it's irritating enough to get rid of. So part of the floor has 'only' ~R25. Cellulose always fits while foam comes is a limited number of thicknesses.
The only reason I'm going for cellulose is because it's so cheap. The area never had flooding. The river that's nearby swells from a rapid mini river to a serious rafting monster during winter. But even then it's still 3 yards below the lowest point of my foundation.
I've done a rough calculation:
XPS R25 = $ 2225
EPS R22 = $1532
Mooney R35 = $700
Does Roxul mineral wool also suffer from wicking? Is it stable enough without a frame to support the floor that goes on top of it?
R15 $685
R30 $1370
I can say that who wicking horror is a real setback because I'm / was also considering a double stud wall with cellulose. (and ceiling)
R-30 for floor? I've seen a table which states that's for an exposed floor, but I don't believe your cement floor meets that definition. The same table also recommend R 7.5 for sub-slab insulation in CZ5.
Using rigid foam is the way to go. Here's an exerpt from a BSC Article titled "Slab Happy" on foam over concrete approach.
"If you do either approach you might want to install a plastic building wrap under the wood based subfloor. This type of building wrap is “liquid water closed” and “vapor water open.” If you spill stuff of a liquid nature on the floor you want to keep the liquid out of the lower parts of the assembly – but you still want things to dry upwards if stuff happens. What are the odds that someone will spill something sometime?"
http://buildingscience.com/documents/insights/bsi-059-slab-happy
Tony,
Chris is correct. The requirements for insulating slabs are different from the requirements for insulating floors of homes with post foundations (and outdoor air blowing under the floor assembly).
For more information, see Insulating a slab on grade.
Double studwalls and wicking issues aren't a problem above grade, unless you're building on a flood plane with the floor below the record high-water mark (which is a bad place to build a house anyway, though sometimes you have little choice.)
If you don't have an outright inundation of bulk water, the wicking characteristics of cellulose is protective of the structural wood, since it redistributes minor non-chronic bulk-water incursions, limiting just how wet any particular place can be. If you have 2" of standing water on the first floor or attic it's not going to save you, but several tablespoons or even a few ounces of water blown by some defect in the window flashing or something during a random hurricane doesn't become a localized mold/rot problem.
Roxul is rock wool, and like fiberglass it will wick moisture, just not a much. It can't move nearly as much water (or as far vertically) as cellulose will. That makes it less protective in minor wetting incidents.
Even locations well out of flood zones can experience minor flooding of basement slabs, from everything from plumbing leaks to record breaking rainstorms. Some classics are things like water heater failures or washing machine hoses that burst while you're out of town for the weekend. It may not fill the whole basement but it'll sure mess up the floor, but a couple of inches of water doesn't need to mess up the entire wall if you use less-wicking materials for walls.
In Zone 5A basement slabs are not required to be insulated, and basement walls can meet code-min performance with R15 continuous air-impermeable insulation (3" of polyiso, with the bottom edge protected from the slab by an air gap or an inch of EPS), or R5 of rigid foam trapped to the foundation with a 2x4 framed wall insulated with fiberglass or rock wool, with no interior side vapor barrier.
Mmmm, I thought I already answered the replies. Maybe something went wrong posting or it's still in the moderation queue. So sorry for a possible double post. Martin you can remove the previous message from your moderation queue if it's still pending.
In reply to the R-7 floor insulation. I may be looking at the wrong table again but R-10 is the closest I can find.
http://www.hbagta.com/local/upload/file/2015%20PRESCRIPTIVE%20COMPLIANCE%20FORM%20N1102%20%28version%202_0%295_2_16.pdf
Footnote 4:
Exterior exposed vertical surfaces shall be protected a minimum of 6" below grade.
The insulation shall extend a minimum of 48 inches below grade
or to the bottom of the slab and then horizontally to to the interior or exterior for a total of 48 inches.
(In Zone 5, insulation shall extend a combined total of 24 inches.) Add R-5 if heated slab.
---> I'm in zone 5
I'm not sure how to understand that code.
Three things are clear:
- The slab edge needs to be insulated.
- Insluation needs to extent 2 feet horizontally or vertically
- The insultion value is R10
It doesn't mention what parts of the insulation are R10 so I assume all parts should be at least R10.
I can interprete the code in several ways:
a]
2ft vertically is all that's needed.
I think this is the most strict reading of the code.
b]
2ft vertically + whole floor area covered.
I think that's reading something into the text that isn't really there, because nowhere anything is stated about the top of the slab.
c]
Slab thickness vertically + 2 feet horizontally to exterior
I hate this option.
d]
Slab thickness vertically + 2 feet horizontally under the slab.
I think this is the most strict reading of the code.
Option d obviously is written with a new construction in mind because there is no way to put inslation under an existing slab.
In my mind the only goal of the code for floor insulation is to stop thermal bridging.
If you inslate the bottom of the slab the heat still leaks out at the edges.
That's why the edge + bottom slab is required. Pure logic in my mind.
But code never discusses inslation on top of the floor.
If that insulation is *suffiently* thick vertical insulation is a total waste of money.
Yeah, vertical insulation keeps the cold from reaching under the slab and because of that the insulation on top of the floor doesn't need to 'work as hard'. So likely can have a lower value.
Why does he keep nagging about that you may ask yourself :-)
The vertial insulation is horror.
1] It needs termite protection.
2] Digging the trench will be a lot of work.
3] How am I going to fasten the insulation to the slab without leaving gaps?
4] I can easily backfill the trench on the exterior side of the foam but not on the interior side. It will be only a few inches but still....
5] It's fragile because the slab is a few inches above grade. While I love WeedEaters the foam likely doesn't :-)
6] Cheap EPS will be fine indoors but below grade the much more expensive XPS is needed.
All things taken into account I think for the extra cost of the slab edge inslation + termite protection I can double the indoor insulation. It's much protected against damage and saves a lot of time.
BTW it will be a 1 story building without a basement. It's just a very simple 6-7" slab with no footers.
Dana/all, the building is way above the flood plane.
So the major, remaining risk is that the wall gets wet due to all sorts of leaks?
I think small quantities will dry out?
For me a double stud wall means all insulation inside the wall. Cheap and still a very good R-value.
That sounded good until I remembered Martin's articles about cold sheating.
An R-30+ wall sure will mean cold sheating. Because of the high R-value the sheating can only kept above dew point with (thick) insulation.
If that conclusion is right then the whole benefit of a double-stud wall vanishes.
Dunno it's of any importance to know but the building will have vertical steel siding (pro-Rib). Full height without any breaks.
The siding isn't flat so I think it has fairly good drying potential. So the cold sheating may not cause any problems?
http://www.domtek.ca/prorib.htm
BTW the sheating will be plywood (not OSB)
Let's see how many tries it takes me this time to beat the chapta's :-)
Tony,
You're right to point out that the code language on slab insulation is confusing.
You have two options:
1. Install vertical insulation at the slab perimeter, from the top of the slab to 24 inches below grade.
2. Install vertical insulation at the slab perimeter, from the top of the slab to an arbitrary stopping point somewhere below grade, as well as with horizontal insulation extending from the bottom of the vertical insulation either toward the building interior or the building exterior. The horizontal insulation shall be wide enough to satisfy this formula:
Depth of vertical insulation + width of horizontal insulation = At least 24 inches.
Tony,
While the code does not discuss the option of installing horizontal insulation above the slab, most code officials would accept that option for insulating an existing slab (that is, a slab that was installed without insulation).
If you choose to install horizontal insulation above your slab, it's a good idea to make sure that your insulated wall is wide enough to prevent heat loss or thermal bridging at the intersection of the horizontal slab insulation and the wall insulation. If you just have 2x4 walls, then vertical insulation at the slab perimeter is still a good idea.
Tony,
You wrote, "An R-30+ wall sure will mean cold sheathing. ... If that conclusion is right then the whole benefit of a double-stud wall vanishes."
No it doesn't. It's still an R-30 wall -- in other words, a wall with a higher R-value than most walls.
Here is a link to an article with more information on the issue: How to Design a Wall.
Answering post #10
Under slab is no option. Exterior is a bad option too because if it's just a few inches deep it will likely get damaged. If it's deep then I just as well can dig a bit deeper.
So replacing 2ft or more under the slab with 2ft or more on top of the slab is against strict reading of the code....
Answering post #11
.... but most code officials allow to replace the 2ft or more under slab with 2ft or more on top of the slab.
That combined means 10" at the slab edge + 2ft on top of the floor meets code.
Is that a correct interpretation of your words Martin?
--------------------------------------------
Yeah the intersection of the wall and vertical insulation worried me for a long time. That's one of the reasons I'm for top of the floor insulation only. But that's a code violation so I won't do that.
What about, say, an inch of XPS F150, F250 or F400 between the wall and slab? I doesn't feel good to me but maybe I'm wrong.
I got an additional problem with floor insulation and partly the reason I suggested the very think mooney floor.
The slab has a 3 inch high edge. Adding R10 or about 2" leaves the top of that ledge exposed if not going for a double stud wall. That would be a very big thermal bridge.
Tony,
In most jurisdictions, if this is a retrofit project, you aren't required to meet code requirements. So relax. Call your local building department if you are nervous and ask about local requirements.
If you want to insulate with horizontal rigid foam above the slab, then you need to insulate the entire slab, not just near the perimeter. But there shouldn't be any code requirements for minimum thickness on a retrofit job. Two inches of rigid foam would be good; 3 or 4 inches would be better.
You wrote, "But most code officials allow to replace the 2 ft or more under slab with 2 ft or more on top of the slab." Who told you that? What does that sentence even mean?
Q. "That combined means 10 inches at the slab edge + 2ft on top of the floor meets code. Is that a correct interpretation of your words, Martin?"
A. No. If you want to install 10 inches of vertical rigid foam at the perimeter of the slab, you would need to install the 10 inches of vertical insulation, plus (in your case) 14 inches of horizontal insulation extending from the bottom of the vertical insulation horizontally outward from your building perimeter. The horizontal insulation would be below grade, but would not be under the slab.
Please tell me if this is a bad thought or not......
A foam board extends from the wall downward into the soil. That way the foam can be attached to the framing. The slab edge is insulated and there is no intersection. I want to to wrap that insulation in aluminum insect screen against termite damage.
https://www.amazon.com/GOBAIN-ADFORS-FCS9335-M-Bright-Aluminum/dp/B000CSIBT2/ref=sr_1_5?s=hi&ie=UTF8&qid=1470830511&sr=1-5&keywords=Aluminum+Screen
The possible problems I can see with that are:
a] Moist air can rise into the wall.
b] The wall's insulation is partly bypassed by cold entering from the below grade.
c] The temp difference causes condesation.
All 3 points are extra bad if using cellulose or to a lesser extent Roxul
Extending 2ft at the slab edge without any other form of insulation would meet code. Likely not very comfortable but it would meet code. Right?
Answering post #15
About me writing about 2ft horizontal insulation on top of the floor that was just my understanding from what you wrote, it I never even considered it. If I insulate the floor it will be the full area.
"A. No. If you want to install 10 inches of vertical rigid foam at the perimeter of the slab, you would need to install the 10 inches of vertical insulation, plus (in your case) 14 inches of horizontal insulation extending from the bottom of the vertical insulation horizontally outward from your building perimeter."
Where do those 14 inches come from?
Tony,
Q. "Where do those 14 inches come from?"
A. You have told us that you live in Climate Zone 5, and you included this link to a local code document: 2015 MUEC PRESCRIPTIVE COMPLIANCE APPROACH.
That document notes, "The insulation shall extend a minimum of 48 inches below grade or to the bottom of the slab and then horizontally to to the interior or exterior for a total of 48 inches. (In Zone 5, insulation shall extend a combined total of 24 inches.)"
Since you are in Zone 5, the 24 inch total applies to you.
My calculation was:
10 inches vertical insulation + 14 inches horizontal insulation = 24 inches total.
That's where the 14 inches came from.
It wasn't clear to me until well into the discussion (response #8) that the slab in question was a slab-on-grade foundation and not a basement slab.
Is it a stem wall, or grade-beam construction?
Are the studwall sill plates resting at the slab, or is there a stub of stemwall above the slab on which it rests?
Answering post #12.
Martin I know R30 is good and stays good when a double stud wall.
I've read the article you linked. It was that article I was referring to.
The way I understand that article I should add at least R5 insulation on the exterior side of the sheating.
It was that sheating I was trying to avoid because of the cost.
My very first plan was 2" foam boards and Roxul between the studs.
As a way to cut down costs and increase Rvalue I started considering the double stud wall.
For me, personally, a double stud wall has to be quite thick otherwise the extra cost outweighs the benefit.
I think adding sheating to an already thick wall makes the combined Rvalue a little overkill.
That's why I wrote the benefits vanish.
Yeah, I know an R40 wall saves more energy than a R30 wall but there are diminishing returns.
OTOH I must admit cellulose is so cheap a few R extra is practically free.
To wrap this up; I took some notes when reading some articles on this and other sites and my conclusion is summarized as:
"27% of the wall's total R-value should be exterior sheathing with a minimum of R5"
Considering fastening siding gets harder when the insulation is over 2" thick and I likely go for the cheap EPS stuff outer insulation will be R8.3. That's a max of R22.4 for the rest of the wall. A total of R30.7
I guess a little bit of margin is wise. A 2x6 wall is R-25.4 incl framing, plywood, drywall and exterior insulation .
R33 for a 2x8 wall but then the exterior sheating is to thin.
So if even a 2x8 wall is to thick for a 2" foam board double stud quickly becomes 'impossible".
But guess what I must be wrong because R50 walls are built :-)
That what I meant to say with: "the whole benefit of a double-stud wall vanishes."
Tony,
You wrote, "The way I understand that article I should add at least R-5 insulation on the exterior side of the [wall] sheathing."
In your climate zone (Zone 5), that approach would only work if you had 2x4 walls. If you had 2x6 walls or double-stud walls, the R-5 would be woefully inadequate. For more information, see Combining Exterior Rigid Foam With Fluffy Insulation.
27% or R5 whichever is higher. I would go for 2" EPS.
I just found this: https://www.greenbuildingadvisor.com/articles/dept/musings/exterior-rigid-foam-double-stud-walls-no-no
No external insulation at all.
Tony,
Of course it's possible to build walls without any exterior rigid foam. The vast majority of U.S. homes have no exterior rigid foam.
But if you choose to install exterior rigid foam, you have made it almost impossible for the wall to dry to the exterior. That's why walls with exterior rigid foam need to be able to dry to the interior -- and to follow the rules for the minimum ratio of rigid foam R-value to total wall R-value.
In an earlier post, you wrote, "If even a 2x8 wall is too thick for a 2-inch foam board [in Climate Zone 5], then a double-stud wall quickly becomes 'impossible.'"
But as the article you just linked to explains, double-stud walls don't have any exterior rigid foam.
A 2x6 / R20 + R5 wall may hit in the R25 range for a center-cavity R value, but when you factor in the thermal bridging of the R6.5-ish studs it's typically a bit under R20 whole-wall if the studs are 16" on center (yielding a ~25% framing fraction with typical window & door framing), a bit over R20 whole-wall if the studs are 24" o.c..
If the existing studs are 2x4 the whole-wall performance is about R10, but adding 2" of interior side or exterior side continuous polyiso would bring it north of R20.
What is the existing studwall- 2x6?
Is the bottom plate of the studwall resting on the slab, or is it on top of a stemwall, above slab-level ? If above slab level, by how much?
If building a double-studwall, use 2x4s or even finger jointed 2x3s (straighter than milled 2x4s, for better wall flatness) for the non-structural wall, which will reduce the thermal bridging as well. For a good discussion on different high-R wall approaches, see:
http://apps1.eere.energy.gov/buildings/publications/pdfs/building_america/high-r_value_walls_case_study_2011.pdf
Take a close look at Case 10, a double studwall with 9.5" of cavity depth with 2" of ccSPF in a structural 2x4 wall, and 7.5" of cellulose, using a 2x3 interior side stud. The whole-wall R of that assembly is about R32. If it were all cellulose, no ccSPF it would still be north of R30.
In a zone 5A location there's little financial rationale to more than about R30-R35 whole-wall (even with double studwalls), since the lifecycle cost of the additional energy savings beyond that exceed the lifecycle energy cost of rooftop PV solar at today's installed price, when leveraged by any decent heat pump. If you upgrade the other aspects of the house in a comparable fashion you can even hit Net Zero Energy with a PV array that fits on the house.
Tony,
You wrote, "A double stud wall with external sheathing is very much possible in theory."
When you write, "external sheathing," I assume you are talking about exterior rigid foam. (Almost all double-stud walls have exterior sheathing -- usually plywood or OSB -- but none have exterior rigid foam.)
You wrote, "But the sheathing [I assume you mean exterior rigid foam] will get so thick, expensive and hard to fasten it's no real option for (thicker) double stud walls."
Right. And no one -- certainly no one at GBA -- has ever advocated the use of exterior rigid foam on a double-stud wall.
You wrote, "For reasons I still don't fully understand, double stud walls without external sheathing [I assume you mean exterior rigid foam] perform (very) well and without any problems."
Most homes in the U.S. lack exterior rigid foam, and most of these homes have no problems. They work because the sheathing is able to dry to the exterior in April and May.
No offense -- I was just clarifying. It sounds like clarity has been achieved.
At Martin post #22
I know it's a bit contradiction what I wrote. The reason simply is that I stumbled on new info when following links in your answers.
So as a very short summary.
A double stud wall with external ridgid foam is very much possible in theory. But the external ridgid foam will get so thick, expensive and hard to fasten it's no real option for (thicker) double stud walls.
For reasons I still don't fully understand double stud walls without external ridgid foam perform (very) well and without any problems.
I truly hope that's a correct summary...
It's unlikely that the slab is one huge 7" thick tile. If it's completely flat on the top surface all the way out to the edge and it's 7" thick at the edge, it's most likely to be grade-beam construction, and more likely to be 3-4" in the middle:
http://buildipedia.com/images/masterformat/Channels/On_Site/2012.04.10_shallow_footings_part_1/images/Fig1.jpg
Stem walls are are typically 6-8" thick walls resting on a footing, poured separately from the slab built, sometimes (but not aways) with the top of the stemwall an or two above the slab to accomodate thicker flooring and still have sufficient access to the bottom plate of the studwall for fastening the wallboard & kick boards.
Dana,
It's not 100% certain how the slab is exactly contructed. Very likely it's as simple as it can get.
Just a slab without any walls, footers etc. Basically a huge tile. It's very hard to dig with a shovel because the of the many stones in the ground. We will dig a trench with a Bobcat or ditch witch.
Only then I can be sure of the exact construction. I dug a few inches to the bottom of the slab and found plywood. So it looks like the slab was poured on top of plywood.
The slab is 3-5" above grade. About 7" thick.
About 1/3 of the slab is totally flat. 7" thick.
The other 2/3 is 4" thick except at the edge it's the full 7". (a 3" high edge)
"Is the bottom plate of the studwall resting on the slab, or is it on top of a stemwall, above slab-level ? If above slab level, by how much?"
The wall is directly on the slab unless the 3" high edge at part of the slab can be counted as a wall.
I'll call to check the current wall is 2x4 or 2x6. (I'm not living near that buiding). But I'm fairly sure it's 2x4 because that old garage is nothing special at all.
"In a zone 5A location there's little financial rationale to more than about R30-R35 whole-wall (even with double studwalls)"
I fear you are right... as usual :-)
I've done calculations based on what I found. And that was only for cellulose on the top of the ceiling.
Today I found a more detailed factsheet that shows that dense packed walls require *much* more cellulose.
A rough calculation ignoring studs, windows and doors shows it will cost me $135/inch thickness.
Versus $38 I got from the 'ceiling calculation'
Still not bad because excluding the extra studs it will cost me $1300 for R35
http://www.homedepot.com/catalog/pdfImages/14/147163bd-46f1-4833-a0b1-839da92b83f5.pdf
Does dense pack cellulose settle at all?
Martin you are right I mean foam boards like EPS or XPS.
I'm going to edit my post to fix those mistakes.
I'm not claiming anyone at GBA made wrong claims. I'm just asking questions based on what I understood. And that's very little...
The best and latest example is that of adding ridgid foam to avoid cold sheating.
I've read that article about adding exterior ridgid foam and in my mind "a wall is a wall" so I applied the logic of the ridgid sheeting to double stud walls. That seems not to be the case. So if I based on that wrong understanding made wrong claims like "..... said" it was not meant to offend. SORRY!
Dana you asked about the existing wall in a previous post. It's 2x4 wall.
About the slab. Nobody knows anything about what's beneath it. Not about walls. Not about the shape.
The top of the slab is not totally flat. 1/3 is.
The other 2/3 looks exactly like the pictures you linked to. But then upside down. 3" deep
It's garage. In the 2/3 area was used to wash cars in. The 1/3 is flat and once had a workbench in it.
Been narrowing down my to few walls that have a good R-value and reasonable cost.
An R32* and R34* wall. Both with 2" EPS on the outside on top of the sheating.
*= Not including Rvalues for drywall, plywood, steel siding etc. Just framing and insulation.
With an R8 layer of EPS the rest of the wall should be no more than R21.7
The walls exceed that by over 50%.
Simple question: Is this considered a 'dangerous' wall that will start rotting in few years.
Zone 5A.
Tony,
Your description is confusing. I understand what you mean by "2-inch EPS on the outside, on top of the sheathing."
What I don't have a clear image of is the rest of the wall.
1. Is this a wood-framed wall?
2. If so, what type of insulation is there between the studs?
Hi Martin,
There goes my attempt of not being long winded :-)
From outside to inside the R32 wall
Pro-Rib steel siding - 2" EPS (R8) - plywood - 2x8 frame filled with Roxul (R30) - drywall.
From outside to inside the R34 wall
Pro-Rib steel siding - 2" EPS (R8) - plywood - 2x4 frame filled with Roxul (R15) - 2x4 Mooney wall filled with Roxul (R15) - Drywall
Tony,
In your climate zone, if you want to install rigid foam on the exterior side of your wall sheathing, the rigid foam R-value must represent at least 27% of the total R-value of the wall. This is explained in my article on the topic, Combining Exterior Rigid Foam With Fluffy Insulation.
Let's look at your two walls.
Both walls have a total R-value of R-38.
Both walls have exterior rigid foam with an R-value of R-8 (21% of the R-value of the total wall).
Both walls fail.
That's what guessed Martin; but I asked anyway after the confusion with the double stud wall.
It means I have no clue how to design a good wall.
I could lower the R-value of the framed part, but that's obviously not the way to go.
I could double the EPS but then I get problems with the siding. The longest screws with matching color I've found are 3".
Siding - 2x8 wall with Roxul - Plywood - EPS - Drywall
Siding - 2x4 wall with Roxul - Plywood - 2x4 Mooney wall - EPS - Drywall
Both meet the 27% rule but I don't think it's wise to install the Roxul that way.
Tony,
You wrote, "I have no clue how to design a good wall."
We have an article for that! Here is the link: How to Design a Wall.
Tony, you seem concerned about meeting the building code for new buildings. I thought it might put you at ease to know that most places that have adopted the International Residential Code have also adopted the International Existing Building Code, which is specific that even on a large-scale renovation like you're doing, only new or altered portions need to meet the energy code for new buildings. (See the last section here: http://codes.iccsafe.org/app/book/content/2015-I-Codes/2015%20IEBC%20HTML/Chapter%209.html.) So you could say that it meets code to not meet code.
Michael, the altered portion is virtually everything because only the slab will remain.
The reason for my endless list of questions isn't only to meet building code but also to save on heating costs.
I've re-read the articles and come to the same conclusions:
a]
The max total R-value of the wall is R30 when using exterior foam.
Can't use thicker foam because then I can't fasten the siding.
Stone wool exterior is no option.
All that means I have to downgrade my wall if I'm going to use EPS on my sheating.
b]
Double stud wall.
c]
Modified Mooney wall.
Siding - EPS - 2x4 frame filled with Roxul - Plywood - 2x4 frame filled with Roxul - Drywall
-> Can EPS be fastened directly on the 2x4's without the extra support of plywood? And the siding?
Tony,
You wrote, "The max total R-value of the wall is R30 when using exterior foam. I can't use thicker foam because then I can't fasten the siding."
Most builders who install exterior rigid foam also install furring strips on the exterior side of the rigid foam. Once these furring strips are screwed through the rigid foam to the underlying studs, they are fastened securely enough to support the siding -- even if the rigid foam is 4 inches or 6 inches thick.
For more information, see Fastening Furring Strips to a Foam-Sheathed Wall.
Martin,
Very clear article. The 'problem' is that type II or higher EPS is advised. I was planning on type I, so likely that's to soft.
I would like your opinion on 'option c' in post #40
I would also like to use Roxul ComfortBatt (NOT the IS type) instead of EPS but I think that's to soft...
Tony,
You are under a misapprehension. You don't need very dense insulation for furring strips to work.
For more information on this topic, see Installing Mineral Wool Insulation Over Exterior Wall Sheathing.
"FastenMaster’s recommendations work for Type II ESP, Type X XPS, Type 1 polyiso, or for any foam with a density greater than one of these listed foams.
https://www.greenbuildingadvisor.com/blogs/dept/musings/fastening-furring-strips-foam-sheathed-wall#ixzz4HzCSDlnN
EPS type II and up. I was planning on type I.
“We tested a range of higher density Roxul products,” Straube wrote to me in an e-mail. “The 6-pound-per-cubic-foot (pcf) and even the 4 pcf products did amazingly well, but the 8 pcf product was easier to handle for people used to the stiffness of foam and it also worked the best.”
https://www.greenbuildingadvisor.com/blogs/dept/musings/fastening-furring-strips-foam-sheathed-wall
2lbs/ft3
http://www.homedepot.com/catalog/pdfImages/65/6512e647-2e3f-49e0-bb90-c873a8ee904b.pdf
While the article doesn't specifically states anything below 4 pcf is bad it doesn't sound to well.
That's how I (mis)understand it. I only need to know if EPS type I and Roxul <comfortbatt are suitable
Tony: It looks like the plan is for all new construction on top of an existing, uninsulated slab, with no stem wall or footing. Is this right? And you are in zone five?
Tony,
FastenMaster's recommendations are quite conservative. It's true that they only tested a limited number of rigid foam types.
The takeaway, in my opinion, from John Straube's research into furring strips over mineral wool -- tests in which the 4-pound-per-cubic-foot product did amazingly well -- is that furring strips can support siding even when installed over somewhat squishy insulation.
I have never heard of siding failures attributable to furring strip problems associated with foam insulation that was insufficiently dense.
Stephen,
That's entirely correct. I'm building in zone 5A (just a few miles from zone 4)
Martin,
I don't know how squishy Roxul ComfortBatt is. Please note it's just the regular 2pcf comfort batt. Not the IS version. And my only option, financially, is that type of Roxul. Roxul pricing is almost the same for all their products if taking R-value and ft2 per pack into account. $42 a pack but when I buy 15+ packs at HomeDepot it's $21 a pack.
Before there are any misunderstandings I'm not questioning anyone's knowledge. I even bow for all the knowledge displayed here. It's just that I don't feel good with extreme long fasteners. As you probably noticed for my semi-English that it's not my first language. I'm from the Netherlands where 99% of all residential housing is concrete and brick cavity walls. So I have a bit of stressy 'mental' issues with framed buildings :-)
------------------------------------------------------------
Anyway I've learned a lot and have been able to remove a lot of possible wall designs from my list.
A professional crew will do the building, but I want to do as much myself to keep the price down. While not a professional builder I not total without skills. So I would like to do the mooney wall part. So my question/thought.
From outside to inside.
Steel siding - 2x4 frame filled with Roxul - Plywood - 2x4 'mooney frame' filled with Roxul - Drywall
I think this construction keeps the plywood at a (very) good temperature. Right?
I want to add 2"of Type I EPS somewhere.
What would be the best place? Exterior or exterior? I think exterior but perhaps there are reasons like drying it's not the best place.
That wall is about R32.
I can see two (possible) weak area's
There is no plywood to support/fasten the steel siding.
While the plywood will be at the right temp the framing itself is protected by just R8. That's just on the border of 27% is calculated from 4.3 (studs) + 15 (Roxul) = R19.3
Tony,
In my opinion, you can create a framed wall with exterior Type I EPS if you want. Of course, the R-value of the EPS has to represent at least 27% of the R-value of the entire wall. It seems that you understand that.
I don't think you'll have any problems if you install furring strips to the exterior side of the EPS. The siding will then be attached to the furring strips.
This type of wall is quite common, as noted in my article, How to Design a Wall.
Your approach is a little unusual: For example, you seem to have chosen what type of EPS to buy, and what type of mineral wool to buy, before your wall was designed. Is that because you have a stack of leftover (or inexpensive) materials lying around that you want to use up?
That's exactly it Martin. Those are the most inexpensive materials. If I would find cheap XPS I would use that. If I would find cheap mineral wool of any type or any brand I would use that.
To compare: I can get a 4'x8' 2" Type I EPS board for about $11. But the cheapest XPS I can find is around $30.
I haven't found any other type of EPS at any price.
So my approach was reading about wall designs and especially about a good R-value. After that I started searching for materials that give me that R-value at the lowest price possible.
"... at the lowest price possible"
In my area there are multiple vendors of used roofing EPS / XPS / polyiso sheeting at a fraction of that price. One of my local vendors has multiple depots around the country, and if you know what & how much you want it can be shipped to your site (for a fee, based on distance from the depot.)
http://www.nationwidefoam.com/
Order at least 10-15% more than you need- there's bound to be some damaged in most lots, but the pricing of reclaimed foam from most vendors is typically 20-35% of the price of virgin-stock goods, and sometimes quite a bit less. In recent years I've paid as little as $12/sheet for 4' x 8' x 4" roofing polyiso to as much as $20/sheet for 3", but never more than that. Reclaimed EPS is usually cheaper than that, and it's almost always Type-II or denser, since it's hard to strip Type-I off a roof and get it to the ground and have it still in one piece (unless it has facers.) Most roofing EPS is Type-II, simply for it's easier handling characteristics, but also for having a "walkable" membrane roof that doesn't leave permanent footprints in the foam. The compressive strength of Type-I EPS is fine if there is wooden subfloor or something above it, not so much for having a 250lb roofer carrying materials walking directly on it.
Finally I'm really ready to start building. (done end October) Talked to the contractor. Good honest guy but it looks like he learned something 30 years ago and that's it.
I don't have much options. At least not at $37.50/h for a crew.
So I'm looking at simple alternatives.
IDEA
From exterior to interior
Steel siding - 2x12 frame filled with Roxul mineral wool - plywood - drywall
The reason I've put plywood on the inside is the condensation factor (if I understood that right)
I only use drywall on top of the plywood because I think it has to be to meet fire code.
R-value wise it's good wall. I'm not so sure about the Roxul being only protected by the siding. (no plywood, no wrap, etc)
Is such a wall ok?
What is your sheathing material? Are you using 2 X12 dimensional lumber, which seems expensive, or a double wall? Why do you think plywood is needed on the interior?
I would think that blown-in cellulose would be cheaper and safer (from a moisture management perspective). That pricing on the framing crew sounds more like a per-worker cost. You might want to see if the contractor will give you a fixed cost since time and materials can get expensive.
Plywood sheating unless advised otherwise.
Pro-Rib steel siding
Yeah, 2x12 is expensive but I'm trying to find a last minute compromise.
Yeah, I was thinking of a double stud wall with blownin cellulose but I feel not at ease letting them so it.
He does by the hour or fixed cost. Whatever I want.
"Why do you think plywood is needed on the interior?"
The only reason is that when put on the exterior it may start to rot because of condensation.
At least that's what I understood from previous answers. If I'm wrong I'll put it on the exterior side (I even prefer that.
Tony. I think you would be better off with ZIP R-7.5 and a 2 x 6 wall with air permeable insulation or open cell foam and air-sealed drywall. If your guy has been building for 30 years, there shouldn't be anything about this assembly that he will find puzzling.
Alternatively, you could use something like this: steel siding, house wrap, plywood (or OSB) with taped seams, 2X12, closed cell foam, air-permeable insulation, and air-sealed drywall. I'm not sure how much closed cell foam would be recommended for this type of wall or whether you would want a vapor retarder under the drywall. Perhaps someone else will comment.
A long shot, but perhaps the steel siding provides enough resistance to racking that plywood isn't needed. Even if not, diagonal steel strapping is a lower cost, non moisture susceptible option.
Tony,
2x12 studs are expensive, and the thermal bridging through 2x12s is worse than it would be through a double-stud wall. You've chosen an expensive wall.
If you haven't read it yet, check out this article: How to Design a Wall.
It's not impossible to install your plywood sheathing on the interior side of the wall -- but it's unusual, and most builders won't like it. It complicates attachment of siding.
In short, don't reinvent the wheel. Choose a wall type that is well-known and tried & true. Steve Knapp's suggestion is a good one; even a double-stud wall should be easier than the stack-up you have come up with.
If you can afford enough Roxul Mineral Wool to fill a 2x12 stud cavity, why not do something like this instead?
From outside to inside:
- Steel siding
- 1x4 furring strips
- 2" Mineral Wool (or any other insulation)
- Air/water barrier
- Plywood
- 2x6 wall with cellulose
- Gypsum board
The plywood + air/water barrier can be accomplished in a variety of ways. You can use the regular zip sheathing and tape the seams, you can use regular plywood with a fluid-applied or fully-adhered membrane air/water barrier, you could even probably do some combo of taping the plywood seams for air sealing then putting tyvek over the plywood for the water barrier if that ended up being cheaper.
While the R-value might not be quite as high with a wall like this, it's a very high quality, durable wall, and by having the air barrier at the plywood sheathing, you end up with a really high quality air barrier because it has far fewer penetrations that your interior drywall (another common place to locate the air barrier).
If you want more R, just add more mineral wool to the exterior.
This article has some information about mineral wool exterior to your sheathing, as well as above-slab mineral wool insulation: https://buildingscience.com/documents/building-science-insights/bsi-096-hot-and-wet-dry
@Brendan
I can only get 3.5" mineral wool at an affordable price. Regular Roxul Comfort Batt. Not the IS type often used on the exterior side of the wall.
The regular batts are far less dense than the IS version.
@Steve
Can you please give me a link to a page on Home Depot, Menards or Lowes with those zip panels. I can't find then. At least nothing that insulates. http://www.huberwood.com/zipsystem/products/zip-system-rsheathing
Any idea what a panel costs? Am I understanding correctly the zip sheating is insulation+barrier+plywood/OSB all in one?
While I often don't get the details right and have an R-value in mind I really do see the advantage of a quality wall. What's the use of a high R wall that's starting to get issues after a few years and as the issues increase the R-value decreases. I'm really "I hate any form of maintenance" kinda guy.
@Martin
"2x12 studs are expensive"
Very true but it saves a lot on labor.
"Choose a wall type that is well-known and tried & true."
That's why I'm here again. My builder doesn't even understand why I want to insulate a wall because "we don't live in Alaska."
His type of wall is ZIP + 2x4 frame filled with pink stuff and drywall.
The contractor suggested zip sheating. So he knows that stuff. It's suggested by Steve.Maybe I can combine it with the wall Brendan Suggested.
So I try to find a good compromise of cost, quality, R-value and what the contractor knows/likes.
Yeah, I know the contractor has to do what I want him to do, but I just happen to think that stuff he knows will be done much faster and better.
@Tony
You should be able to basically attach some exterior insulation to the wall your contractor likes and be pretty successful. Have you checked out that link Dana Dorset posted ( http://www.nationwidefoam.com/ ) regarding sourcing Type II EPS affordably?
- Steel siding
- 1x4 furring strips
- 2" EPS (or 3" or 4")
- ZIP Sheathing
- 2x4 (or 2x6) wall with "pink stuff" ;)
- Gypsum board
Another EPS thought for you:
The R-Tech foam Home Depot sells (Type I) has a compressive strength of 13 PSI, which is really close to the 15 PSI recommended by https://basc.pnnl.gov/code-compliance/continuous-insulation-%E2%80%93-claddingfurring-attachment-code-compliance-brief for exterior foam insulation (it's hidden in a footnote).
Depending on thickness of foam, weight of cladding, amount of furring, etc., you might be able to make it work, but you'd probably want to do some further research to confirm.
Like Steve said regarding sourcing ZIP-R, the more specialized foams (like type II EPS) probably come from dealers, not straight off the shelves at Home Depot. You or your contractor should be able to reach out to the manufacturer of whatever Type II EPS you are interested in to find out how to source it locally.
EDIT: In addition, based on the fact that mineral wool with compressive strength in the 5 PSI neighborhood works as exterior insulation, it really seems like your standard 13 PSI EPS from Home Depot ought to work: http://www.homedepot.com/p/R-Tech-2-in-x-4-ft-x-8-ft-R-7-7-Rigid-Foam-Insulation-310891/202532856 Also, Martin said he thinks exterior Type I EPS will work for you in an earlier response, so that seems like a really good solution!
It seems like you've been running in circles a little bit on the wall, as you started off with EPS on the outside of a frame wall, but got thrown off by there not being enough EPS because your interior wall was so thick (2x8). You just need a little more on the outside and a little less on the inside and you're good.
4" EPS, ZIP sheathing, 2x6 stud wall with batt insulation (or cellulose) is a very standard, high performance, high R-value wall that seems to meet the majority of your requirements.
Tony. It's likely you'll have to buy ZIP-R through an authorized distributor. You can search for the closed source by going here: http://www.huberwood.com/locations. Be aware that there may be lead time on receiving the R product if it's not standard for your region.
Your best protection against ongoing maintenance is a good installation.
If you search your local Craigslist for the terms:
rigid insulation
rigid foam
foam insulation
... you are likely to find a few small-time foam reclaimers or others with new or surplus foam at much lower price points than box stores, usually cheaper than box store pricing on fiberglass batts for R value & square feet of coverage.
Nationwide Foam is one of a good half-dozen or more foam reclaimers within 90 minutes drive of my house. YMMV.