Moldy wall solution options?

ZONE 5, Chicago area.
One story educational.
Existing construction 8″ CMU with brick exterior, Z-channel horizontal furring on interior with 1.5″ foam, then drywall with no drainage, air, or vapor barriers, except where wallpaper was applied on interior surfaces. And that is where mold growth was found, but also on the back side of drywall.
Given the impracticality of applying an exterior drainage or moisture barrier at this point, would you remove drywall, and apply impervious visqueen over the Z-furring and foam board and install drywall again?
Seal the exterior of the brick?
Both?
Also attached are some photos of an area where drywall and furring was removed for remodeling. We are seeking estimates for exterior waterproofing for the addition, applied to the outside of the CMU before new brick. The currently designed wall detail essentially the same as existing with no barriers specified.
The north exposure of the building primarily, if not exclusively, seems to be the problem area.
Thanks in advance for advice.
GBA Detail Library
A collection of one thousand construction details organized by climate and house part
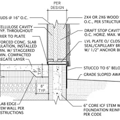
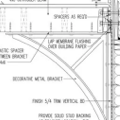
Replies
This shows the details of how to properly insulate load bearing masonry:
https://buildingscience.com/documents/building-science-insights-newsletters/bsi-105-avoiding-mass-failures
Except for the spray foam versions, the walls need to be able to dry towards the interior, so any wallpaper that is impermeable (typical vinyl stuff) will create issues.
My guess the issue in your case is the combination of the missing water barrier behind the insulation increasing the amount of moisture and the wallpaper blocking drying. The water barrier shown in the diagrams is any one of the modern fluid applied WRBs (ie Air-Bloc 17MR or Prosoco R-Guard Cat 5).
Overall, the best solution for these walls is to insulate from the outside, EIFS is pretty common insulation plus exterior finish for block construction. This is not always the options, so if you do insulate from the inside, spray foam is typically the safest option.
If you do put a waterproofing on the exterior of the CMU, make sure it is vapor open as otherwise you create a cold side vapor barrier which is asking for more issues down the road.
Akos, Thanks so much for your time.
So, if we were to add a semi-permiable liquid applied barrier to the inside of the existing CMU and avoid wallpaper, we might be OK, even to stick the rigid foam board back into the cavities between furring, yes? Better would be to apply spray foam though, it seems. (Wall solution 2) What are your thoughts on spraying between furring strips and cutting if flush with them if needed, to try to maintain our mechanicals and avoid losing space in the room. Do you think the weaknesses at the furring would be significant enough to make that a risky solution? My guess is that it would be pretty effective at air sealing and insulating around the "z" furring strips.
The first step in correcting the problem is to decide where the moisture is coming from.
Do you think the moisture is liquid water flowing thru the blocks and making it way to the interior.
Another possibility is that water vapor was condensing on the drywall because the drywall was colder than the dew point of the air in this room. Is it possible the last tenants had a huge moisture source like plants or aquariums? Could the last tenants have chosen not to heat this room allowing the wall to get below the dew point?
You may want to consider building your wall much like basement walls are done.
https://www.greenbuildingadvisor.com/article/three-ways-to-insulate-a-basement-wall
Walta