Conditions That Cause Mold

Hi everyone,
I am seeking some information concerning mold and mold formation. Good reading suggestions are also more than welcome.
In my recent job I started to work a lot with mold. Most of the cases are not related to water leaks. Only dangerous combinations of poor insulation, poor ventilation and high relative humidity levels.
However, I find the information concerning mold and mold formation disperse in the literature and sometimes contradictory.
Some folks are still using dewpoint calculation to assess mold formation, which is considered archaic for some experts. Mold formation is a dynamic process, involving dynamic aspects such as the fluctuation of indoor HR and condensation/ drying rates.
I can also find in the literature that is not necessary to have 100% RH to see mold formation. 80% RH is more than enough for some types of mold.
I have also read about hydric capacity. The ability of materials to deal with high RH before starting to develop mold.
So, I am confused with so much information. How do you assess mold formation? How to consider relative Humidity, absolute humidity, condensation/ drying rates, etc.
Is there any type of charts? I found this recently (https://energyhandyman.com/knowledge-library/mold-chart-for-temperature-and-humidity-monitors/) but I only got more confused.
Because I now have to elaborate technical reports, I feel the urgent need to understand the governing factors of mold formation without the presence of liquid water.
Thanks a lot for your help!
Joe
GBA Detail Library
A collection of one thousand construction details organized by climate and house part
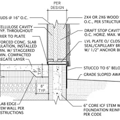
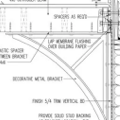
Replies
I don't know much, but I do know most species of wood will not grow mold if the moisture content is below 19%. This can be a problem in a rainy climate when a building is under construction and the framing is open to the rain (Vancouver, for example), and as soon as the roof is on the walls start getting insulated and VB. This, along with heat, will encourage the growth of mold and other organisms that will lead to the decay of wood.
This can also be seen when somebody is too quick to build on a fresh concrete foundation or slab, there is thousands of pounds of water that get released to the atmosphere, you do not want to trap this moisture in.
Same goes for fresh drywall mud, lots of water...
When I have to deal with a mold problem, it is a 2 pronged approach 1) deal with the moisture source, 2) dry the materials and apply a product that will kill the mold and prevent the harmful spores from becoming an environmental health hazard.
Sounds like you know far more than me, care to share some knowledge?
Mold formation is determined by the material, the moisture content and the temperature. If there is condensing humidity mold will grow almost anywhere, I've seen it grow on steel, plastic, concrete, stone and even glass.
In wood, the propensity for mold to grow is determined by moisture content. By convention (as far as I can tell) 16% moisture content is the lower threshold for mold formation and 28% moisture content is saturation, above that point there is liquid water dripping out of the wood. Note that these are not relative humidities like is used for air, it's absolute, the ratio of weight of water in the wood to the weight of the dry wood. Waterlogged wood can have a moisture content of 200%.
Historically the focus in building science has been on keeping wall assemblies below the dew point so that condensation doesn't form. Clearly this is simplistic, and mold can form in wood that is above the dew point -- wood subject to condensation will absorb water until it hits 28% moisture content, and mold starts at 16%.
Wood will reach equilibrium with the moisture in the air over time. What that equilibrium point ends up being is not a simple question, depending on both humidity and temperature. At the same air moisture content (eg absolute humidity) wood will absorb more moisture at lower temperatures and less at higher temperatures. So cold parts of the house are more at risk. However, that is tempered by the fact that mold grows better at warmer temperatures.
DCContrarian,
Thank you for your reply.
That is also a common point of confusion among professional. The difference between Relative Humidity of air, Relative Humidity near the mold surface, and Moisture Content.
Can you please point the source of those values? I would love to read more about it. Also, do you have any information concerning other materials beside wood (e.g. brick, mortar, drywall, etc).
Thank you!
Joe,
It sounds like you have a good grasp of the key concepts, but it's worth doubling down. Mold requires:
1. Food source. Assume everywhere, after all house dust is mostly dead skin.
2. Spores. Again, assume everywhere except say positive-pressurized hospital clean rooms.
3. Proper temperature. Ideal growth range will depend upon mold species but generally assume 60° to 90° F.
4. Elevated humidity. 70% RH and up.
You've asked the loaded questions...
"How do you assess mold formation? How to consider relative Humidity, absolute humidity, condensation/ drying rates, etc."
I've only scratched the surface of this myself as it relates to building assemblies using WUFI Pro. What you get are 'isopleth' graphs that show the likelihood of growth under given conditions for a given assembly. There are no absolute answers because, as you noted, it's a dynamic process and conditions are always flux, but as far as I know it's the best tool to try and predict results in absence of a tested assembly for a given climate.
The mold isopleth simulations are certainly not a guarantee. When in doubt go with good sense and a tried & true assembly. Design and build things that can dry.
Jason,
Thanks for your reply.
The thing with WUFI is that is more labor intensive. And requires you to know the dynamic boundary conditions.
In most cases, there is no data on the boundary conditions, especially indoor environments of non-heated and dehumidified buildings.
Joe
Actually that's the easy part, at least from the user standpoint. WUFI just has you import climate data (easy) and then pick the assumed temp and humidity set points for the interior -- it defaults to 35% interior winter RH. When in doubt we bump that to 50% to be conservative. Building the wall or roof assembly is the more time-consuming part, digging up material permeability data, translating perms to perm-inches and adding air gap layers with/without moisture storage capacity to simulate driving rain and rainscreens and such and such.. Important, and dramatically changes the results, but time-consuming.
Unheated and unhumidified is also easy. You tell the program both sides are effectively 'exterior' with or without rain exposure.
I would disagree with point 4.
Mold needs available moisture. On an impervious surface like glass it needs liquid water which means the surface has to be at the dew point. On a porous surface mold can grow in the absence of liquid water. For example, an oft-quoted number is that wood will support mold with a moisture content of 16% or higher. If you look at this chart: https://www.woodworkerssource.com/wood-moisture-content.html *
you see that you really have to have 80% RH to get up to 16% equilibrium moisture content. And if you look at the chart below it seems the only US cities that routinely hit 16% equilibrium moisture content are Juneau and Seattle. But mold happens all over. How? Generally in a house absolute moisture levels are fairly constant, but temperatures aren't. So you get pockets of high relative humidity and even condensation. So really the trigger isn't a particular level of humidity, it's a combination of conditions that lead to areas of local 80% RH or higher.
Of course liquid water infiltration is also a big contributor. Often in situations where things are humid anyway and drying is limited a small leak becomes a big problem.
*(I can't vouch for the accuracy of the chart it was the first one that popped up in a Google search).
DC,
My note #4 was intentionally overgeneralized, but perhaps you're right that "available moisture" is more accurate than saying "elevated humidity" or a specific RH threshold, those being atmospheric or proximity measurements with potentially big deviation from surface or adsorbed moisture measurements.
With regard for the other factors you noted, I will say it's easy to be guilty of error by omission when there are countless materials and at least six figures worth of mold species in existence. The growth surface of interest, its porosity, moisture storage capacity, prefentiality to the mold as food, and the water phase at the source all play a role.
I grew a lot of fungi, on rice, on other substrates, etc. Here is an interesting article with basics, https://www.researchgate.net/profile/Lina-Nunes/publication/269152614_Fungal_degradation_of_wood_in_buildings/links/559bec9808ae0035df233c1b/Fungal-degradation-of-wood-in-buildings.pdf?origin=publication_detail
I have a lichen garden too, fascinating organisms. It took a while to find the right location for the lichen to thrive. Gives some insights as to where “mold” might grow. There’s a Netflix show or elsewhere on internet called Amazing Fungi (or something like that).
From article: “There is no precise moisture level at which fungi will attack timber, since the moisture threshold for decay can vary depending on the timber type and fungal species. There are, nevertheless, three points that should be considered when dealing with fungal decay and timber (8): Decay only occurs in damp timbers; Fungal decay is possible for measured moisture contents above 22% but rapid decay is likely only at 26% and above; For practical purposes, a safety margin of 2% should be given to account for possible inaccuracies in readings and inaccessibility of some wood components. Therefore, timber is considered safe from fungal decay if the measured moisture content is 20% or below.”
Cellulase anyone? Worked with those too, so much cellulose in our world (carbon cycles).
https://pubs.acs.org/doi/10.1021/cr500351c