Moisture/heat transfer issues in a rigid foam framed over roof?

I have an old house with an uninsulated attic with 2×6 rafters 24inches OC. I am replacing the roof and want to insulate the roof deck with polyiso rigid foam board. My engineer recommends that I beef up the roof framing by adding a 2×8 rafter on top of the roof deck, over and in line with the existing rafters, basically converting a 2×6 into a 2×14. But I am concerned about the implications of having the new wood members embedded in the insulation layer. Here is what I’m thinking of doing: (1) apply peel and stick I&W membrane for air sealing and WRB over the existing roof sheathing; (2) install the 2×8 rafter “extensions”. (3) infill the spaces between the 2x8s with ripped down sections of polyiso rigid foam board (4) finish with a one inch layer of polyiso over the rafters to address thermal bridging and to get an air-tight layer, tape the seams. (5) make a vent channel by applying 1x furring on top of 1 inch foam and in line with the rafters, then OSB decking over the furring, and asphalt shingle roof on top of that.
GBA Detail Library
A collection of one thousand construction details organized by climate and house part
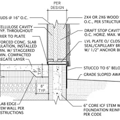
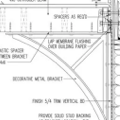
Replies
While I'm sure, as an old house, the rafters are undersized by modern standards, the additional weight per area of a rigid overroof is not that much. Is the engineer really claiming this extra weight is too much?
If you are doing the 2x8s, I would skip the foam, which loses most of its advantage in what would essentially be a cut n cobble operation (read: a huge PITA). Just fill the new rafter bays with batts and leave a vent space. Akos has tips/ideas on this method. You can still seal up the old deck and hit your R value ratios to keep that old sheathing protected.
Thanks. The concern is not so much the added weight as snow load, which can get substantial. Won’t melt and slide so readily on a well insulated asphalt roof. And since this is a one time opportunity to beef things up, it is prudent to do so.
On the disadvantages of “cut and cobble”, my proposed continuous one inch layer over the 2x8s and cobbled foam won’t make enough of a difference to make it worth my while?
And if I do proceed with the foam scenario, should I be worried about moisture issues?
Unless the 2x8s are fastened to the 2x6s with about a zillion screws, structurally it's not like a 2x14, it's equivalent to a 2x10. Specifically, a member sized 1.5"x8.2".
I have done projects similar to what you're proposing using mineral wool instead of polyiso, but it worked out well. We used Intello X as a vapor-open water resistive layer but if you're set on using polyiso, ice and water shield is a good choice. I have used ice and water shield when doing full polyiso roof-overs.
Thanks. Intellio is interesting. Makes sense with the assembly you describe. Would it make sense with mine as an alternative to something like grace ice and water shield? Seems like it would allow a pathway for any moisture that makes its way into my assembly and come into contact with the 2x8s to dry to the interior during the hotter months. Or is that asking too much of it? The primary purpose of this layer is to serve as an air seal. It is a backup water barrier, but hopefully it will never be needed that deep in the assembly.
Cobbling in rigid is a lot more work than using batt, with minimal if any benefit. The 1 inch of thermal break above also doesn't boost total assembly R value to a large degree and definitely reduces outward drying to at least some degree, but with unfaced board and the vent channel above perhaps OK. Definitely do NOT use foil faced rigid though if adding the 1 inch continuous to the top.
Thr advantages to rigid is applying it as continuous sheets. You basically have new rafter bays, which few would ever consider cobbling in with rigid if not painted into a corner.
Michael,
When you say you did something similar but with mineral wool, do you also mean thr part about the 1 inch of foam above it all? I'm guessing not. Did you vent the new rafter bays?
Thanks. The reason for using polyiso is that I have access to material that is cheaper than the equivalent amount of batt insulation, even the cheapest fiberglass stuff, and it gives more r/inch. Yes, a little bit of a hassle to install, but worth the trouble, I think. The question is how to design the assembly to achieve the level of reinforcement that I need while at the same time making it as tight and well insulated as possible. I'm open to alternative ideas! Thanks
You didn't explicitly say this but I have to assume you are converting the attic into a conditioned space, correct?
Yes, converting it into conditioned space (or, rather, insulating what has long been living space, just uninsulated.)