Minimum exterior insulation requirements

Martin, recently you published a link to the BC Builder’s Guide for Effective Walls.
In it the guide states that to achieve the minimum requirement of a R22+ wall it should have:
2 x 6 Studs (R-19 Batts) + 1 1/2″ of R-4/inch or R5/inch Ext. Ins.
The guide further states that “This is acceptable across BC and that this level of thermal performance is required by the 2014 Vancouver Building By-Law and the 2012 BC Building Code for climate zones 7B and 8”.
I will be building in climate zone 6 so I figure that this wall assembly must be sufficient there as well. However, in your article “Calculating the Minimum Thickness of Rigid Foam Sheathing” you state that for climate zone 6 you need R 11.25 for exterior sheathing on a 2×6 wall and for zones 7 & 8 you need R 15.
BC seems to require much less exterior insulation than what you advise. Which method is correct? Also, since your article on foam sheathing refers to rigid foam do you need even more insulation if you use exterior mineral wool panels (since mineral wool allows more air to pass through it than a solid piece of foam)?
GBA Detail Library
A collection of one thousand construction details organized by climate and house part
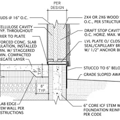
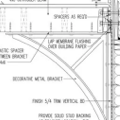
Replies
What really matters is the R value of the exterior foam, not the thickness. The only thing that matters regarding thickness is that you use enough to reach the R value required for your particular wall assembly. The exact type of insulation you use doesn’t really matter either as long as you use enough of it to reach the required R value for the wall.
Martin’s article is based around the idea of keeping the structural sheathing in the wall warm enough to prevent moisture (condensation) issues. This means it’s the ratio of R value of cavity insulation to R value of exterior insulation that is important to ensure that the temperature gradient across the wall keeps the dew point temperature inside the rigid foam layer where it won’t cause problems.
Building codes are absolute minimums. I’ve always liked the “building code gives the minimum passing grade, which is a D-“ analogy. I personally would go with Martin’s recommendation over your local code if Martin is recommending more exterior insulation than your local building code requires. You really don’t want to have moisture issues inside your walls.
Bill
Scott,
Code requirements in Canada are a function of politics, not science. The same can be said for code requirements in the U.S.
There is not necessarily any rhyme or reason to building code requirements. Some requirements are wise, and some are archaic legacies with no known scientific basis. Builders learn to live with building codes, because they are legal requirements. We obey building codes for the same reason that we obey a 30 mile per hour speed limit in a densely populated village.
I think that you misunderstood the recommendations on minimum rigid foam thickness in my article (the one titled "Calculating the Minimum Thickness of Rigid Foam Sheathing.")
That article provides rules for builders who happen to be installing exterior rigid foam. But you don't have to install any exterior rigid foam if you don't want to -- so the recommendations in that article may not apply to you.
For more general recommendations, see another article: "How to Design a Wall."
What I find interesting about the BC guide is that it requires about 1/3 to 1/2 LESS insulation than what Martin's article recommends. An inch and a half of mineral wool would be about an R6 to an R 7.5 - still way below the R11.25 level Martin suggests for zone 6.
Martin, just saw your reply. If adding exterior insulation helps to mitigate problems within the wall cavity (in particular moisture condensing on the inside surface of cold exterior sheathing and causing mold and rot) and the BC Guide says that it is code mandated then why wouldn't the recommendations in your article apply?
It would seem that the focus should be on finding the correct amount of exterior insulation to use, not whether it should or shouldn't be used.
Scott,
It's not true that the B.C. code mandates exterior foam. The code mandates R-22 walls or better, as far as I know, but you don't have to use exterior foam to get there.
The recommendations in my article have nothing to do with minimum R-value requirements for walls. Instead, they have to do with avoiding moisture problems in walls.
It’s possible the code is making some different assumptions (although I’m not sure how), or there was an economic driver to keep costs down. As Martin mentioned, building codes aren’t necessarily based on science in the way you might think, or perhaps hope.
Manufacturers try to get their products written into the code for example. It’s extreamly profitable to have the use of your product legally required in every building! That’s just one example. Some codes are for safety, some are based on best practice learned over the years, some are well intentioned but don’t work out. Some codes are pure head scratching “what were they thinking” codified into the codebook.
Many people, including myself, go with even more rigid foam than Martin recommends in his article. Reasons for doing this for many is to increase energy efficiency. In my case, I want to maintain a higher humidity level in the winter without moisture problems in my walls, so I use more rigid insulation to keep the sheathing warmer. I think Martin’s recommendations are a good “best practice” amount of exterior rigid insulation to use on typical walls.
Bill
Martin, if you look farther down in the BC Guide you will see 4 examples of walls that don't meet the minimum code mandate (page 39 of the guide). Two of the walls have interior cavity insulation but no exterior insulation while the other two walls have exterior insulation but no interior cavity insulation.
While it is true that you could simply continue adding more exterior insulation until you achieved the R22+ requirement (and thus avoid using any interior cavity insulation) that would seem to me to be a complicated wall to flash and clad properly due to the needed thickness of the exterior insulation.
Still, if R22 walls are mandated in BC I would assume that the easiest way to achieve that mandate is to include both interior cavity and exterior insulations, so in a round about way the BC code does "mandate" exterior foam (or at least "recommends" it as the simplest method of achieving an effective R22+ wall).
Scott,
I think we're in agreement. The BC code doesn't mandate exterior rigid foam, which is why the guide I reviewed provides information on a variety of code compliance options, including double-stud walls, PERSIST walls, SIP walls, and ICF walls.
Scott,
You wrote: "the BC code does "mandate" exterior foam (or at least "recommends" it as the simplest method of achieving an effective R22+ wall)."
I think the same assumption about simplicity could be made for walls in most of the northern US and the rest of Canada. But that's a very different argument than saying it is mandated by code. Much of southern and coastal BC is n0t required to meet R-22 for walls, and exterior insulation there is rarely used.
Unfortunately the process of building an effective wall tends to turn into a confusing series of articles and guides. Is it mandated, is it required, is it code, why is the exterior insulation actually there (to help achieve R values or prevent moisture problems in the wall cavity) is it right for your zone, etc.
From what I gather, although the BC Guide has some excellent information in it and their recommendations to create an R22+ wall are admirable it remains that 1 1/2" of exterior insulation in zones 7B and 8 (and I assume zone 6) is insufficient to prevent moisture issues within the wall cavity.
> do you need even more insulation if you use exterior mineral wool panels...?
From a moisture standpoint, you need *less* exterior insulation when the exterior is more permeable (ie, permeable sheathing + mineral wool or EPS). If you use foil covered foam (very non-permeable), then even if code allows less, my opinion is that you should use the levels Martin lists (or more).
Jon,
I agree. Walls with a continuous layer of semi-rigid mineral wool dry to the exterior -- and therefore the minimum R-value requirements for continuous exterior insulation don't apply if you're using mineral wool for the exterior layer.
That's why the B.C. guide shows the use of continuous exterior mineral wool in so many of the illustrations.
>"From a moisture standpoint, you need *less* exterior insulation when the exterior is more permeable..."
Parsed in 'merican dialect that's pretty ambiguous. You don't NEED to use less exterior insulation, but you can get away with less when the exterior insulation is vapor permeable. A less ambiguous framing might be:
"From a moisture stand point you don't need as *much* exterior insulation when the exterior is more permeable..."
I am looking to use a wall system as follows:
1/2" Drywall
Poly
2x8 stud wall (structural purposes)
R28 batt
1/2" Plywood
Blueskin VP100 SA
2" Perforated Graphite EPS
Strapping
Metal siding
I am told it will be fine but would appreciate any thoughts....
Follow the expert, not influenced by code politics recommendations here (mostly Sidebar 2 and Table 3):
https://www.buildingscience.com/documents/digests/bsd-106-understanding-vapor-barriers
Summary: it can work depending on climate, interior and exterior perms and AC use.
Always air seal well. And IMO, it's likely that you would be better off with MemBrain replacing the poly.
Thanks Jon,
For example I could use Halo Exterra, per 1 inch is R5. With perforated laminate at 1.5 inch is 1.34 perms. They state it is breathable up to 2".
User-7427373,
First of all, can you tell us your name? (I'm Martin.)
We can't answer your question until you tell us your climate zone.
You are describing a wall assembly with a total R-value of about R-38. About 26% of the wall's total R-value is in the form of exterior rigid foam. That will work in Climate Zone 5, or anywhere warmer, but it won't work in Climate Zone 6, 7, or 8.
For more information, read this article: "Combining Exterior Rigid Foam With Fluffy Insulation."
Martin,
"Won't work", that is pretty strong words there. I would agree that with a bad warm side air barrier (say T&G wall) you must have the right ratio of exterior insulation.
Building science and experience show that walls with less than ideal ratio still preform well. Not hitting the ideal ratio should not be a reason to skip exterior insulation.
In terms of the question from User-7427373.
Provided the wall is build with a reasonably tight warm side air barrier (ie air tight drywall) with a vapor retarder (6 mil poly, MemBrain or vapor barrier paint) the wall should work.
The VP100 under the foam is not doing all that much, you can save some money by taping the seams of the plywood and using standard building wrap.
Overall some exterior insulation is always better than none, if you are worried about moisture, you can always go with one of the more permeable products (EPS, unfaced/felt faced polyiso or mineral wool).
Akos, building up a mountain I am using the VP100 so I can get the exterior protected quickly and have the 160 days UV stable to finish the outside. (thats the plan anyway:)
I was looking at using Terrafoam Platinum Graphite EPS unfaced. The rep said it is a little fragile in this form and difficult to secure. I would secure it with battens direct to the stud so think it should be fine.
Run of the mill Typar building wrap is 6 months UV stable. Typar Metrowrap is 12 months UV stable.
Assuming that the layer adjacent to the drywall labeled "...Poly..." is 4 mil or 6 mil polyethylene sheeting (a Class-I vapor barrier) it will "work" in almost any climate zone, provided that the layer labeled "...2" Perforated Graphite EPS..." has a vapor permeance significantly higher than the polyethylene.
The resilience of such a stackup against incidental bulk water incursions or big air leaks through the polyethylene layer may not be very good if the EPS layer is low-permeance.
Thanks Martin, I updated my info!
The build is on Mount Washington BC Canada. looking at the map it is climate zone 5 but its at 1200m and temps can get to around 5 below sometimes more.
Paul,
Your wall will be OK.
Thanks Martin.
I am looking at a different EPS (Durospan GPS R10) which is not perforated.
One question regarding a "gap" between WRB and EPS, 1mm will work apparently, but there is not much info out there on how to achieve this, with which products?..
Hey Paul,
Martin is on vacation for a few weeks, so you may not hear back from him soon. If I understand what you asking (this was a pretty involved thread that I'm just coming to now), you want to create a gap between your WRB and exterior rigid foam? If so, that's because you're planning to have some type of an interior vapor barrier and have enough rigid foam on the exterior (or a type of foam) that you are concerned won't allow for outward drying? Do I have it right? If that's the case, you can use a draining housewrap like HydroGap or Tyvek Drainable Homewrap for your WRB.
Let me know if I'm misunderstanding your question.
Thanks Brian, yes you are correct, the only issue is I am using blueskin vp100 which is self adhered. I am trying to think of a solution to create a gap. For example maybe adding a layer of tape (1.5" wide) to sheeting where the EPS/batten is screw to the stud thus creating a gap between two fixing points...if that makes sense.
A staggered 2x4 stud wall 12" oc (24" oc exterior and interior, offset 12") on 2x6 plates, with a 20% framing factor, would have a whole-wall R-value of 21.2. It also has the lowest stick count, lowest labor, and the lack of bridging works acoustically to limit sound transmission. You can make up the balance of the insulation with EP foam, or any other exterior insulating material of your preference. With careful detailing you might be able to squeak by an R22 with a good inspector. FWIW, I alway specify this for common walls between bedrooms, media rooms, etc, along with acoustical drywall or resilient clips, and attach the ceiling drywall the same way leaving a 1/4" gap all around for flexible caulking. I have even used it with OSB on both sides for a shear wall. The inspector had never seen it done before, but couldn't find any structural reason to flag it. Customers love it because the quiet (assuming you use solid core doors and full sweeps) is immediately noticeable.