Mini split advice

Climate Zone 5, Oakland County Michigan, building starting in July
2357 sq ft ranch, 2357 sq ft walkout basement.
2×6 walls dense pack cellulose, 3 inches exterior mineral wool
R60 ceiling insulation
Superior wall foundation for backfilled walls
R 7 Windows from Klearwall
Have access to natural gas but prefer to go electric if possible.
Thought I’d try and get your thoughts Dana and others on our Heating and Cooling plan. We just had a Manual J calculation done:
Total heating required including ventilation air: 37,561 Btuh
Total cooling required including ventilation air: 22,639 Btuh
First off, do these numbers seem appropriate? Second, do you think the house is too big to consider using mini splits? We had a local Mitsubishi diamond contractor suggest a plan, and I wanted to see if you thought it was oversized or just right.
Suggested Mechanical setup:
West side of home and main living area. (This unit should be able to give some additional ductwork for basement when completed)
Qty 2 MSZ-FH06 High wall units on exterior wall (Master Bedroom/bath & 2nd Bedroom – Individual control)
Qty 1 MVZ-18 Air handler in basement. (Great Room, Kitchen, mud room, and laundry)
Qty 1 Electric strip heater for air handler for supplemental heat.
Qty 1 MXZ-3C30NAHZ2 unit mounted on west wall near closet area (On a 12“ stand or wall mounted)
East side of home: (This unit will have one more connection to handle the addition of golf room in basement)
Qty 2 MSZ-FH06 High wall units on Exterior wall or close to for drain connections.
Qty 1 MXZ-3C24NAHZ2 unit mounted on east wall on wall bracket under walk around deck.
Possible basement is being completed you may want to utilize an additional condensing unit with MVZ air handler and one additional head to zone that space.
That was what was suggested. I still want to discuss other options with the Mitsubishi contractor, but wanted to see what you thought. We are not opposed to using the air handlers exclusively with no wall mounted units if it’s cheaper or easier. I’m attaching the floorplan below with his notes on it.
GBA Detail Library
A collection of one thousand construction details organized by climate and house part
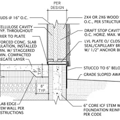
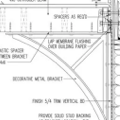
Replies
here is the suggested mechanical layout . . .
Congratulations on finding a contractor that is at least willing to propose a mini-split solution. I live near you and the contractors I talked to wouldn't touch that.
How does the total heating and cooling load break down into the regions associated with each mini-split head? How much of the load is basement? You don't have any heads there.
What are the heat load numbers without the ventilation air?
What is the 99% outside design temp?
On the west side, the individual loads of the bedrooms are probably not big enough for a half ton head each, but would allow you to zone them separately. The minimum modulated output of the -3C30NA @ +47F is 7200 BTU/hr, which is the maximum output of a single FH06, and roughly the minimum output of the MVZ-18 and 20% of the total design load.
Assuming an outside design temp of +5F (Flint is +3F, Detroit is +5F) and an indoor design temp of 68F, that's a 63F delta, so a linear approximation would be 37,500/63F= ~600 BTU/hr per degree below 68F. So a 7200 BTU/hr minimum modulation heat load would occur at 7200/600= 12 F below 68F, or 56F, so it'll probably modulate pretty well with only that system supporting the load.
The min-mod output of the -3C24NAHZ2 is also 7200 BTU/hr so take another +12 off that + and you're at 46F, still not bad, if the compressors are only cycling on/off from the mid-40s and warmer. But the accuracy of those load numbers (particularly the ventilation & infiltration numbers) may be on the high side, which means the compressors could be cycling in the 30s, which is why I'm curious about the ventilation and infiltration load numbers in the Manual-J. If the ventilation + infiltration adds up to a large fraction of the load you may want to back off on the number of compressors, especially if you spring for heat recovery ventilation or ventilate at lower than ASHRAE 62.2 levels (which is usually too drying in winter for comfort in your location.)
On the east side you don't have enough wall-blob capacity to run the -3C24NA compressor efficiently with only a pair of FH06s, which are probably oversized for their room loads anyway. I suspect that unit will spend a lot more time cycling than modulating unless you can give it more load. What are the design loads for those rooms, and what is the total heat load for the basement?
Capacity-wise I think you have more than enough to able to skip the auxilliary strip heat, but without room-by-room load numbers it's hard to say for sure.
Dana - I'm not sure what the heat load numbers are without the ventilation air. Please forgive my ignorance here. I'm attaching the Manual J data below that includes the room load numbers. Maybe the answer is in there, and I am just not interpreting it correctly. Thank you for responding so quickly and thoroughly. If this isn't sufficient to help in answering let me know and I can do some digging with the energy auditor who did the Manual J.
Brian,
The breakdown is on page 3: building = 30,472, infiltration = 7,089, ventilation = 0.
I also notice that more than half of the heat loss is attributed to the basement. Your original post indicates that the air handler is located in the basement but serves 1st floor rooms.
Your basement is inside the conditioned space, and based on those numbers is responsible for approximately 40% of your structures heat loss (not including infiltration). Perhaps a small investment in some sub-slab insulation and some thicker insulation on the block walls is warranted? R20 on basement walls and R10 below slab seems reasonable, and will likely help knock that heat load down.
also some quick math on the outdoor capacities;
The 3C24 is rated at 25KBTU @ 5F
The 3C30 is rated at 28.6KBTU @ 5F
Total capacity is 52.6KBTU (4.5ton) @ 5F
Your heat load is calling for a smidge over 3ton.
Thanks for pointing that out Reid. Ryan - for some reason the software the guy used only allowed for a few vague selections in terms of the basement slab and walls. The backfilled walls are the prefabricated R12.5 Superior Walls, and below the slab we specified 2" of EPS foam. Not sure how much the load would decrease due to the inclusion of those details. Also, the Mitsubishi contractor mentioned the total capacity he specified was going to be greater than what the building called for due to the possibility of adding heads in the basement in the future and also because of how the house was zoned. I didn't follow everything he mentioned and probably am leaving out something critical here. But, does any of that sound at least a little reasonable?
I know this is a tangent from your original question, but you may want to check out this thread regarding the R-value of Superior Walls:
https://www.greenbuildingadvisor.com/community/forum/green-products-and-materials/93891/what-would-weighted-average-r-value-be-superior-w
Thanks Reid. I figured the actual R value would be less than reported. Our plan is to either add a few inches of EPS on the outside or spray foam the interior of the walls some time after construction. It's funny because when I brought up this topic with the contact I had at Superior Walls he stood firm that 12.5 was the real number. I didn't argue because going into it I knew what I was getting and that we'd have to compensate. Those therm analysis pics and calcs are really interesting. Thanks again for pointing out the link.
It looks like they're using 1F as an outdoor design temp which is probably a 99.6% temperature bin, and 72F as the indoor design temp, which is 4F above code min. That's a delta-T of 71F, rather than the more likely +4F-out/ 68F-in delta of 64F, or about a 10% to the high side, but lets run with it.
On the 2 ton system, the heat loss of the Season Room at that 71F delta is 2151 BTU/hr, which is barely above the +47F minimum output of the FH06 head that's serving it. The heat load will be roughly 2151/71F = ~30 BTU/hr for every degree below 72F, so with a 1700 BTU/hr minimum modulated output, even if it didn't have a 2 ton compressor behind it that head will be cycling on/off any time the out door temp is 1700 / 30 = 57 F cooler than 72F, which is 16F. It will actually be able to modulate lower at 16F than at 47F, but basically the thing will never modulate, only cycle on/off. The its not clear in the Man-J which is the Office/Bedroom, but it's a smaller room with less window, so it's probably even worse off.
You're looking at a total design load on that compressor of less than 4000 BTU/hr, but a minimum compressor output of 7200 BTU/hr, (which is the max output of a single FH06.) The way the 2 ton unit is probably going to operate most of the time is that one zone will be running at full speed (lowest efficiency) until the temp overshoots (turning the head & compressor off) until the other zone calls for heat, which then runs full blast until it turns off. The average duty cycle on either head will be well under 50% , with very little operational overlap that would allow them to modulate down a bit from the max, and will incur lots of compressor cycling even when it's +5F outside. This is a recipe for pretty lousy average efficiency.
With the 2.5 ton system the FH06s on the Master Bedroom and other bedroom on have a similar issue relative to the room loads, but at least on that compressor whenever the MVZ-18 is running the FH06s can modulate down to minimum speed/highest efficiency, running with much longer (and more likely to overlap) lower-output/higher-efficiency cycles.
You are probably better off designing duct system for the MVZ-18 to include the Season Room and Office rather than installing the woefully under-loaded 2 tonner to zone them separately, or bumping up to a MXZ-4C36NAHZ, or MXZ-5C42NAHZ and using a KD09 mini duct cassette to combine the Master Bedroom and the adjacent bedroom into a single zone, assuming you don't run into refrigerant line length issues.
https://meus.mylinkdrive.com/files/MXZ-4C36NAHZ_Submittal.pdf
https://meus.mylinkdrive.com/files/MXZ-5C42NAHZ_Submittal.pdf
Dana - again thank you for your response. I'm forwarding your suggestions to my Mitsubishi contact tonight. I think I'm starting to grasp more and more each time I read through your posts, but admittedly I still have a ways to go before I'm comfortable with all the detail. So I have a few more questions: the multi zone units you suggested - based on the setup of my house, how many zones do you think are appropriate , and could we get away with one multizone outdoor unit with the length of refrigerant lines that would be required? What's the advantage of their new air handler - are a few ducted cassettes better or cheaper? Also, do you have a feel for the ballpark costs - just to have a comparative reference when I get figures here locally? Thanks again for your time and expertise.
Some newbie comments from me. I am seriously thinking of replacing my AC setup with the Mitsu MVZ/MXZ in zone 5. In your case, perhaps the MXZ-8C48NAHZ might work better since it can take upto 8 heads including upto 2 MVZs and the big MXZ can also modulate down to 7200BTU which when distributed over smaller heads might lessen the possibility of cycling? One thing not clear to me with regard to the MVZ air handler is that while it has an ECM blower, it can only operate at 3 speeds? Does this not limit the modulation ability?
Brian,
According to the below, the total piping length for the MXZ 36, 42, 48 models is 492 ft.
https://meus.mylinkdrive.com/files/MXZ-4C36-5C42-8C48NAHZ_PAC-MKA30-50BC_TechService_OCH573_08-14.pdf
Brian,
You asked about the advantage of the MVZ over the mini-ducts. I have seen it described in:
https://www.greenbuildingadvisor.com/articles/dept/musings/how-buy-ductless-minisplit
Thanks for the response Venkat. Since I've posted this question I've had some pricing done and I'm getting somewhere around $26,000 installed. Wow was that a shock. Geothermal quote was $22,000 and that's before the 30% tax credit. It looks like it's either that or traditional gas furnace. Bums me out because I really wanted to get on board with mini splits. I liked the minimal equipment and quick response aspect of the temp controls, and the fact I wouldn't be burning fossil fuel.
I tend to think of geomethermal as the first-class solution and mini-splits as a cheap alternative that's almost as good. So I think you should be delighted that you can get a geothermal system that cheap. No shoveling snow around the outdoor unit, and higher COP. It's all upside.
Brian,
Are both the Geothermal Heat pump and the water pump going to be inverter driven and will modulate?
If the Geothermal would be all ducted, then I would do a comparison with the MVZ ducted Mitsubishi in terms of cost vs COP. What I have seen from other articles on this site and elsewhere is that Ground source would do well if sized and installed "correctly", whereas ASHP COPs are good/respectable and are harder to screw-up. I would want to see what the particular installer's/tech's installations have achieved in terms of COP.
venkat
You got a little further than me down the mini-split route by finding a contractor that would do a quote. However, it appears that they don't really want the business. They probably included a large contingency for rework and call-backs based on their own lack of familiarity. If they thought there was a future in the mini-split business, they would be willing to invest their own money in climbing the learning curve. They apparently don't expect enough future business to justify that.
The majority of post on this site indicate that mini-splits are far cheaper than ground source, so your quotes are surprising. Our region may be different. I suspect the difference is not due to climate, but rather is due to the expertise of the contractor base. With the tax credit, your GSHP quote is very competitive with what I ended up spending for a conventional forced air system with a natural gas furnace and central AC.
@Brian. Your geothermal quote is surprisingly affordable. My community has a sweetheart deal with Bosch and requires its systems in most new construction. I have heard that these installs are typically running $40K with a vertical ground loop. Maybe that is an exaggeration, but I would give your quote a careful review before moving forward. Of course, we are in a warm/humid climate and need AC and heat.
FYI. For my fairly efficient 3200-square-foot house, I was able to use a conventional heat pump system that cost about $11K. It was a no-brainer.
If you can get a GSHP system installed by a compentent contractor/designer for $22K before subsidy you should be ELATED, rather than bummed!
It's almost too good to be true, so vet that contractor carefully- get references, (and check them!)