Mineral Wool in Stud Bays to the Exterior of Continuous Rigid Foam

Hi all. I’m trying to sort out the details for interior basement wall insulation as part of the remodel to finish the basement in our 1920s bungalow. I’ve read through the many helpful articles and posts here on GBA which have answered most of my questions.
What I’m stuck on at the moment is the insulation for the existing 2×4 framed pony wall above the concrete stem wall which it rests upon. We’re planning to do all work on the interior, so won’t be adding any exterior insulation during this project.
Existing wall construction from outside in is shiplap wood siding, felt, horizontal 1″x7″ TG sheathing, then 2×4 framing. As part of the seismic retrofit we’re doing during the remodel 1/2″ CDX sheathing will be nailed to the studs along much of the interior perimeter. Because of the challenge to air seal the interior of that TG sheathing I’m thinking of just running a couple inches of foamed and taped EPS or Polyiso (R-8+) on top of the studs (and over the CDX) creating a continuous layer of rigid foam similar to what will be against the concrete wall below. The benefit being airsealing and a thermal break in one go.
To preserve as much interior space as possible, exceed code min R-Values, and make use of the empty stud bays behind the CDX and rigid foam I’m wondering if it’s worthwhile to stuff those bays with R-15 mineral wool batts?
Is there any reason not to put the mineral wool in those empty bays against the existing and not air sealed TG sheathing? Does it create potential for a moisture problem for the sheathing and/or sill, which has no capillary break as-is? Maybe there’s a better way to insulate/air seal that wall I’m not thinking of that doesn’t involve spray foam?
BTW I’m in climate zone 4C.
Thanks in advance for any thoughts.
GBA Detail Library
A collection of one thousand construction details organized by climate and house part
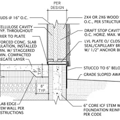
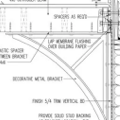
Replies
> sill, which has no capillary break
Your plans (for both upper and lower sections) will reduce drying, which increases risk to the sill. But maybe not enough to be a problem. Can you measure and monitor sill moisture?
> rigid foam ... will be against the concrete wall below
Follow the advice here, ie use semi-permeable (about 1+ perm) foam to promote concrete drying.
maybe I'll grab a moisture meter to see where things are at now, not sure how I'd be able to monitor after everything's closed up.
Seems like the EPS would fit the bill well for 1 perm. We're also planning dimple mat to interior perimeter drain between foam and concrete foundation wall which would further impede drying to the interior. However there will still be an above grade section of the concrete wall on the exterior that should allow for some drying and we're planning to improve the grading outside too. Thanks for the link.
IMO, the dimple mat isn't needed. EPS against concrete doesn't form a watertight seal - so any small amount of water coming through the wall will make it down to the drain. Or if there is substantial water flow, use EPS with drain channels in it. Both allow you to follow Joe L's drying advice.
I like that, save a little space and money too. I've only seen bulk water intrusion in the basement a couple times over the 10 years I've had the house and that was when the gutter clogged and overflowed right next to the foundation and even then it wasn't a great deal of water. Also, the concrete foundation wall is old with nothing close to a smooth surface so I imagine the plain EPS will allow plenty of drainage and
You could consider installing a capillary break under the sill. It seems like a lot of work, but often turns out to be not too bad. Jacking the house in 4'-8' sections and sliding a piece of semi-rigid vinyl under the sills is the most common method. It's not absolutely necessary, but good insurance, especially if the sills are not currently bolted down. Even if they are, you can notch the vinyl around the bolts.
Otherwise, your plan is OK. You have significant drying potential to the exterior with that wall system. If you use foil-faced polyiso on the interior and seal it well, there will be close to zero moisture transport from the interior. The wall may get a bit damp during winter, but probably not enough to cause issues. Stuffing the stud cavities with rock wool or fiberglass will improve its R-value without significantly decreasing its drying potential.
Protect the lower part of the wall from rain splashback and make sure the exterior gets some ventilation for drying.
Adding a capillary break did seem like a lot of work, but I'll give that option more consideration, as the sills are not currently bolted (but will be after the seismic retrofit). We may have jacks down there for work on the posts and beam, so it may make sense to add a capillary break then.
"Stuffing the stud cavities with rock wool or fiberglass will improve its R-value without significantly decreasing its drying potential."
My thought was that the additional risk of slower drying of the sheathing/sill was worth the added R-value from the added mineral wool. It sounds like you think so too.
We have decent overhangs and will be doing some work to clear vegetation and regrade around the perimeter which should help with the external drying potential.
I have been putting mineral wool in my exterior walls as I gradually renovate my own home. I put a smart vapor retarder (MemBrain, although that has gotten difficult to find lately) on the interior under the drywall. I haven't had any problems. I have 1/2" foil faced polyiso under the exterior siding though, which isn't really enough for my climate zone, but I haven't gotten to my reside project yet where I'll be adding a lot more exterior rigid foam.
1/32" HDPE sheet makes a great retrofit capillary break. HDPE is relatively stiff and slippery, which makes it easy to slide into a small gap. HDPE is also cheap. I try to use black HDPE for these kinds of projects -- it's harder to see and also more UV resistant if it's exposed to sunlight anywhere.
Good to hear the mineral wool's been working in your home and thanks for the tip about the HDPE, I'll look into it. I guess if/when we ever replace the old siding I may want to add exterior insulation, in which case adding a capillary break now makes even more sense.
If you have the ability to do so, add the capillary break now -- it's cheap insurance. You only need to jack the house up maybe 1/8" if even that much, then slip in the HDPE sheet. Get the HDPE sheet sheared into strips 4 or 8 feet long (4 foot strips are easier to handle), and if possible have the supplier form a lip on one edge so that the top part (before the lip) is the same depth as the width of your foundation wall. This way you can slide the strips in from one side, use the lip as a stop, and do the entire operation blind knowing each time when you have the strip positioned properly in the wall. Overlap the strips an inch or two on the ends and you're good to go. It goes faster than you'd expect.
Bill