Mineral wool batts for continuous exterior insulation

I’m in Alaska, and it is currently not possible to get any kind of rigid mineral (vapor-open) insulation. It does not seem to even exist in the PNW and my attempts to find a place to freight it have failed. Comfortboard, or really anything from Rockwool, Thermafiber from Corning, etc. and it isn’t even clear if it’s still being made.
I want to build an outbuilding this summer that is insulated and I would really like to have continuous exterior insulation. Is it possible to use mineral wool batts instead? Or maybe some kind of exterior frame like a larsen truss with blown mineral or cellulose insulation? I would like to avoid using foam.
GBA Detail Library
A collection of one thousand construction details organized by climate and house part
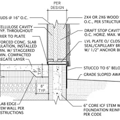
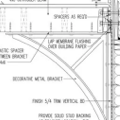
Replies
I can't speak to the advisability of using vapor open exterior insulation in Alaska, or to issues of availability. But it is certainly possible to use mineral wool batts as a continuous exterior insulation. This issue has come up in other recent comments and questions here on the Q&A. So I'd start by encouraging you to search the comments. And then I'll mention that Matt Risinger's Youtube channel has several videos showing how contractors have implemented it with various exterior finishes.
In this case, a vapor-open and fire-resistant exterior insulation is necessary. I'd love to see where Matt Risinger used batt insulation on the exterior. I've watched almost every video he made on cold climate continuous exterior insulation and I feel like I would have remembered that.
Tom, my mistake. Matt used Roxul Comfortboard insulation on exteriors, the fairly dense stuff. It wasn't something like a light, fluffy batt. I misread the original comment.
Here's one of the videos I had in mind.
https://youtu.be/P165RxBHBtU
Have you tried calling a Rockwood rep? They might be ble to point you in the right direction. Ie: they know their clients that they sell to, so if there's any shop in Alaska that they sell their products to, they can tell you who it is.
If we're talking about the same Batts, my personal opinion is it wouldn't work, or would be a horribly cobbled attempt. The batts compress quite a bit. How are you doing to affix them while maintaining the depth? Also, I wouldn't know how you could do an airgap and siding, unless you built an exterior frame, which is essentially a double stud wall. Which you suggested with the Larsen truss.
So, I suggest looking into doing a double stud wall assembly with blown in or batts.
The whole point of exterior insulation is to break up the thermal bridging of the studs/structure. A double stud assembly also does this.
To be fair, I've never done one before. I would like to do it one day. It doesn't look hard to me, just takes a bit of extra planning and design, and cost. But it might outweigh the cost in comfortboard.
I'm sure others on here who've build them can chime in on it.
Jamie
Rigid mineral wool is definitely being made. It's a little more difficult to install as exterior sheathing than it is to install foam or wood fiber panels, but not that much harder. Batts would compress too much to install similarly to those other materials.
What would work for you is a "Swinburne Truss," which involves mounting vertical 2x6 outriggers (or the dimension of your choice) on the outside of a conventionally-built wall, using 3"x3" tabs of plywood pre-screwed into the outriggers and then screwed into the wall studs, creating a thermal break. You can put regular batts between the outriggers.
If I am understanding the Swinburne truss, there is only 3/4" thermal break? That doesn't seem like that would do much as far as thermal breaks go.
Yes, 3/4". When you have 10" to 12" walls, having a large thermal break is less important than on thinner walls. I would also consider doubling the tabs for a 1 1/2" gap. I haven't calculated the whole-wall R-value but I don't think it would make a big difference.
The tabs allow for an offset from the 2x stud they are screwed into. This image is basically what we do. Windows are set in a plywood buck. Also, this construction method allows us to use mostly local wood - non kiln dried.
Thanks, this is a great idea.
I also love this idea and this is the first I’ve seen it.
Quick clarification - For fastening the outer cladding, it looks like there is a lot of load or sheer force on the inner most plywood scrap that is screwed to inner studs. If the load from the exterior cladding is being carried all the way in and not landing into the studs…. Am I understanding that right?
Also, our WRB is an SA version so it looks like we would need that in place of the air barrier shown on the diagram above and then potentially a roll out barrier *again* over the wool insulation (behind the cladding)?
Thanks so much,
Eric
Bob, thanks for weighing in--I had forgotten to mention the offset studs/outriggers which nearly eliminates thermal bridging.
Alaska_Eric, at a former place of employment we did 11 7/8" I-joist outriggers and were often questioned about the loads on them. It's minimal--less than 5 lbs per sq. ft, which is almost nothing by the standards of construction. A single 12-penny nail can support somewhere around 200 lbs. Note that Bob places the windows in a buck supported by the structural framing; that's important, as windows can get heavy, but otherwise there are no structural concerns.
Eric,
It sounds like you already have the SA wrb in hand, but that seems like the wrong product to use as the air barrier. Largely because it's overkill but also potentially because you may need it to provide vapor throttling. Or on secomd thought, perhaps the sheet good provides enough? Interested what others think on that. I assume that's why Bob used intello, though I'm not sure why intello X (UV exposure during construction?)
Or, if you have vapor throttling (as required per code) on the inside, you would be fine with the SA wrb assuming it's vapor open.
The more I think on it, without sheathing on the exterior, I imagine the inboard sheathing may be enough vapor throttling.
Eric,
In a normal insulation design, your vertical battens are screwed into place through maybe six inches of insulation into the studs. The insulation itself provides no support at all, only more load, so you essentially have the entire weight of the outboard wall hanging on long steel pins. They can handle that just fine, but the forces in this assembly are much less extreme already, and I would expect it to do fine even if you only had attachment points at the top and bottom. If you wanted to be really extra you could use steel Z-girts, but why?
While this thread is still going, I am curious if anyone has any recommendations for insect and rodent-proofing and top and bottom details on this assembly.
TomK,
As the WRB is right behind the outer vertical furring, the framing behind that could have any type of solid material under it. The 3/4" cavity behind the cladding can use any of the typical screening to keep out pests. I prefer perforated flashing.
If you don't want to vent the top of the rain-screen, the top can simply terminate at the soffits. The outer framing would have to have fire blocking (a top plate) between it and the roof space.
Tom_K,
Akos has done this. He strapped the sheathing and used 1 1/2" mineral world batts in between. The advantages he cited were that it was much cheaper, and alleviated concerns about planing the strapping the way you have to when it is fastened through mineral wool boards.
Thanks for all the responses! I did read through other comments first as well as contact a Rockwool rep and subsequently the local distributor before posting, and confirmed that it would be "very difficult to find" and my best bet would be to try to have it freighted from Seattle at a cost of tens of dollars per wsf. But, Lowe's carries basically unlimited amounts of the mineral batt insulation.
I suspect using a T-stud (https://www.tstud.com/) vs the 2x6 on edge would resolve the thermal break issue. They are apparently 2.50/foot but I suspect you could go with 24" centres (assuming framing was also at 24") with that extra nailing surface. They are doing 2x6 and 2x8 versions.
Comfortboard definitely exists in the PNW. I'm using it on a project in Bellingham, ordered through my local lumberyard. I'm sure at least one supplier in Alaska would be able to special order it. In terms of shipping though it would likely be pricey.
Tom,
I was going to send you a DM. I have been working on this EXACT issue (also in Alaska) for a while now and would love to chat with you about what I’ve found.
Eric
Deleted
Tom et al,
First of all thank you for all the excellent replies. Planning for exterior insulation in Alaska has proven to be a challenge because of the need to dry to the outside & the lack of vapor open (mineral wool board) insulation.
Just to reiterate my question above - Assuming the exterior cladding has a weight similar to cedar plank lap siding, it appears that when using the Swinburne truss as shown above, the cladding is going to only be fastened to the outer 2x6, which is fastened to the interior studs via the offset plywood (4"x4"). Am I misunderstanding? It appears that I am putting a great deal of pure lateral shear force onto those plywood squares as the load is transferred over to the fasteners going into the inner studs because there is NO direct fastener from the outside to the inside. Is that right?
@maine_tyler - Yes, I already have the WRB in hand. VaproShield PanelShield - selected because of its highly vapor open perm rating and 12 month UV exposure. Is there an assembly that would make sense given that I already have the WRB and the walls are already built & sheathed in ply? Adding the 2x6 outriggers on top of peel & stick WRB, followed by 5'5" of rockwool, followed by either another vapor open (roll out) WRB? Does the rock wool need to be "protected" in order to maintain R value and longevity? This is the great option of the ComfortBoard - it's made for exterior abuse.
@Tom - I am considering "Cor A Vent" (https://www.cor-a-vent.com) for terminating the bottom edge to provide a drain and bug screen.
Eric,
That cedar lap siding weighs about four pounds per wall square foot, but consider that the amount each plywood section is carrying is 24" x 16" of siding plus, say, 16" of 2x6, plus the insulation and incidentals, no more than fourteen pounds. Your intuition will tell you this is fine, and a quick napkin calculation suggests it's over 100x stronger than it needs to be.
Mineral wool batts are about 2.5 lbs/ft³; at 16" o.c. and 6" thick, that's 1.7 lbs per linear foot of outrigger.
Red cedar is about 21 lbs/ft³; depending on your details, the siding is probably around 3.5 lbs per linear foot of outrigger.
Hemlock for the outrigger is about 4.1 lbs/ft³, or about 0.7 lbs per linear foot of outrigger.
In total, that's less than 6 pounds per linear foot of outrigger. If the fastening tabs are 3' on center, that's less than 20 lbs per fastener.
As I wrote in comment 17, a typical 12-penny nail can hold about 200 lbs. The heavy-duty screws used for this application can hold even more. I'm pretty comfortable with a factor of safety of 10.
There are other Stone Wool manufacturers in the market, such as Owens Corning Thermafiber insulation... Feel free to contact me in case you want to know where to source it